Методы подготовки управляющих программ
Подготовка управляющих программ вручную
Этапы подготовки:
1. Разработка чертежа заготовки и операционного чертежа.
2. Техническая проработка операции (состояние операционной карты).
3. Разработка схемы наладки.
4. Построение циклограммы (схемы перемещения инструмента).
5. Определение координат опорных точек (составление операционной расчетно-технологической карты)
6. Составление операционной карты кодирования (буквенно-цифровая запись программы).
7. Запись программы.
8. Проверка программы.
Автоматизация подготовки управляющих программ
Направление автоматизации, качество, продолжительность и стоимость подготовки управляющей программы во многом определяет эффективность применения станков с ЧПУ. Автоматизация подготовки УП значительно сокращает сроки и трудоемкость этого процесса при одновременном повышении качества УП.
Основная идея системы автоматизированного программирования (САП) создать такое програмно-математическое обеспечение для ПК, чтобы имея запас необходимых сведений в своей памяти: об особенностях станка УЧПУ, инструментах, системе координат и т.д., ПК осуществил не только расчет координат опорных точек обрабатываемого профиля, параметры эквидистанты, выполнил аппроксимацию, но и решил технологические задачи с их оптимизацией. Кроме того, ПК должен провести кодирование информации, формирование УП, ее контроль и корректировку, разработать сопроводительную документацию.
|
|
САП классифицируется: по назначению, области использования, параметрам используемых ПК. По назначению различают:
- универсальные САП – предназначенные для станков определенных групп при изготовлении разных по форме деталей;
- специализированные – для автоматизированных участков для деталей отдельных классов;
- комплексные – для подготовки УП к станкам различных групп, они объединяют возможности универсальных и специализированных САП.
По области использования в зависимости от типа деталей и оборудования различают САП:
- для обработки плоскостей параллельных осям координат (фрезерные станки);
- для обработки сложно-контурных поверхностей на фрезерных станках;
- сложно-профильных деталей на токарных станках;
- для сверлильных станков с позиционной системой управления;
- для комплексной обработки корпусных деталей на многоцелевых станках.
Методики и способы подготовки управляющих программ для станков,
Оснащенных устройствами ЧПУ типа CNC
1. Использование подпрограмм различного типа: стандартных на типовые детали и составленных в процессе программирования для каждой конкретной детали.
|
|
2. Программирование с сокращенным описанием контура. Принцип основан на том, что с помощью УЧПУ определяются недостающие данные по заданным вводимым параметрам и при необходимости формируются дополнительные кадры УП.
3. Параметрическое программирование широко используется для задания технологической информации с учетом специфики станка. Например: параметры программно-математического обеспечения для данной модели станка, параметры, с помощью которых могут записываться различные подпрограммы и параметры, используемые как переменные в УП для обработки конкретной детали.
4. Оперативное программирование. Программа предварительно не составляется, а координаты опорных точек, циклограмма перемещения инструмента, режимы резания вводятся с пульта управления устройством ЧПУ с оперативного эскиза. Для станков с УЧПУ оперативного программирования характерно: упрощенная схема ввода программы, использование большого количества постоянных циклов ориентированных, на данный станок, простая схема редактирования и ввода коррекции программы.
5. Символьно-графическое программирование. Программирование ведется в системе диалога с выводом буквенной и графической информации на монитор. Процесс программирования ведется в режиме диалога, оператору предлагается набор отдельных решений по каждому конкретному циклу обработки, выбирается нужное, и дается следующий запрос; затем выбранный вариант программы вызывается на экран.
|
|
Программирование обработки символьно-графическим способом включает следующие этапы:
- формирование геометрических параметров заготовки и детали;
- конкретизация технических требований;
- выбор схемы обработки и инструмента;
- определение режимов обработки;
- разработка схемы наладки;
- наладка;
- динамическое моделирование с вызовом на графику изображения рабочего процесса при обработке данной детали.
В настоящее время находят широкое применение различные системы автоматизированного программирования (Delcam, Гемма и др).
Дата добавления: 2019-02-13; просмотров: 944; Мы поможем в написании вашей работы! |
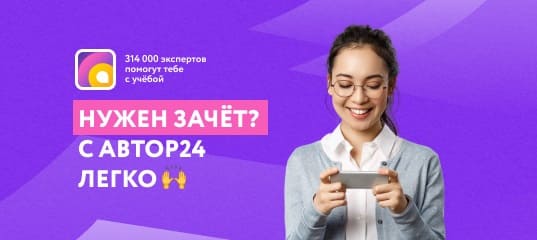
Мы поможем в написании ваших работ!