Component parts of a casing string
A casing string consists of individual joints of steel joints which are connected together by threaded connections. The joints of casing in a string generally have the same diameter and approximately 40ft. long. A bull-nose shaped device, known as a guide shoe (casing shoe), is attached to the bottom of the casing string. A casing hanger allowing the casing to be suspended from the wellhead, is attached to the top of the casing.
Conductor casing (30”O.D.) – is the first casing string to be run and consequently has the largest diameter. It is generally set at approximately 100ft, below the round level. Its function is to seal off unconsolidated formations shallow depths. The conductor casing is needed to circulate the drilling fluid to the shale shaker without eroding the surface sediments below the rig and rig foundations when drilling is initiated. It also protects the subsequent casing strings from corrosion and may be used to support structurally some of the wellhead load.
Surface casing ( 20” O.D.) - is run after the conductor and is generally set at approximate4ly 1000-1500ft. below the ground level. The main functions: prevents cave-in of unconsolidated, weaker, near-surface sediments and protects the shallow fresh water sands from contamination; supports and protects from corrosion any subsequent casing strings run in the well; supports the wellhead and BOP equipment (in case of kick, surface casing generally allows the flow to be contained by closing the BOPs ).
Intermediate casing (13 3\8” O/D.) are used to isolate troublesome formations between the surface casing depth and the production casing setting depth. Unstable shales, lost circulation zones, abnormally pressured zones and squeezing salts. When abnormal formation pore pressures are present in the deeper portions of a well, intermediate casing is needed to protect formations below the surface casing from the pressures created by the required high-drilling-fluid density. When normal pore pressures are found below sections having abnormal pore pressure, an additional intermediate casing permits lowering the mud density to drill deeper formations economically.
Production casing (95\8”O.D.) is either run through the pay zone or set just above the pay zone. The main function of this casing is to isolate the production interval from other formations. It also provides protection for the environment in the event of failure of the tubing string during production operations and permits the production tubing to be replaced or repaired later in the life of the well.
|
|
Liner (7” O. D.) – is a short casing string which is suspended from the inside of the previous casing string by a device known as a liner hanger. The liner hanger is attached to the top joint of the casing in the string. The liner hanger consists of a collar which ahs hydraulically or mechanically set slips. These slips support the weight of the liner. The overlap with the previous casing (liner lap) is usually 200ft. – 400ft. Liners may be used as an intermediate string or as a production string.
casing string | колонна обсадных труб |
anticipated load | ожидаемая нагрузка |
guide shoe (casing shoe) | башмак обсадных труб ( деталь из твердой стали, прикрепляемая к нижней трубе обсадной колонны и снабжена острым краем для срезания грунта) |
casing hanger | клиновой захват для спуска обсадных труб |
surface string | комплект противовыбросовых превенторов |
conductor | направляющая труба (первая колонна обсадных труб, спускаемая в буровую скважину на сравнительно небольшую глубину для придания скважине правильного направления и перекрытия и пород, склонных к осыпанию) |
setting | установка; спуск и посадка обсадных труб |
setting depth | глубина установки |
surface casing | колонна обсадных труб после кондуктора (кондуктор) |
intermediate casing | промежуточная обсадная колонна (техническая) |
production casing | эксплуатационная колонна |
pay zone | зона с промышленной нефтегазоносностью |
conduit | трубопровод |
liner | хвостовик |
|
|
Сements and Cementing
Well cementing is the process of mixing and displacing cement slurry down the casing and up the annular space behind the pipe where it is allowed to set, thus bonding the pipe to the formation. No other operation in the drilling or completion process plays an important role in the producing life of the well as does a successful primary cementing job.
The first verified use of Portland cement in an oil well, for shutting off water that could not be held with a casing shoe, was in 1903. After placing the cement, the operator normally waited 28 days before drilling the cement and testing. Improvements in cements and the use of admixtures have reduced WOC time a few hours under present-day practices.
Cementing procedures may be classified into primary and secondary phases. Primary cementing is performed immediately after the casing is run in the hole. Its objective is to obtain an effective zonal separation and help protect the pipe itself. Cementing also helps in:
- bonding the pipe to the formation;
- protecting producing strata;
- minimizing the danger of blowouts from high pressure zones;
- sealing off “lost-circulating zones” or other troublesome formations as a prelude to deeper drilling.
Secondary cementing (squeeze cementing) can be described as process of forcing cement slurry into holes in the casing and cavities behind the casing. These operations are usually performed for repairing or altering a well at some later date or it may be
|

used during the initial drilling process. Squeeze cementing is necessary for many reasons, but probably the most important use is to segregate hydrocarbon producing zones from those formations producing other fluids. The key factor on a squeeze cementing job is that of placing the cement at the desired point or points necessary to accomplish the purpose. Squeeze cementing is also employed to:
1. supplement or repair a faulty primary cementing job;
2. reduce the gas-oil, water-oil or water-gas ratio;
3. repair defective casing or improperly placed perforations;
|
|
4. minimize the danger of lost circulation in open hole while drilling deeper;
5. abandon permanently a non-productive or depleted zone;
6. isolate a zone prior to perforating for production or to fracture.
Fig. Conventional placement technique used for cementing casing
Дата добавления: 2019-01-14; просмотров: 362; Мы поможем в написании вашей работы! |
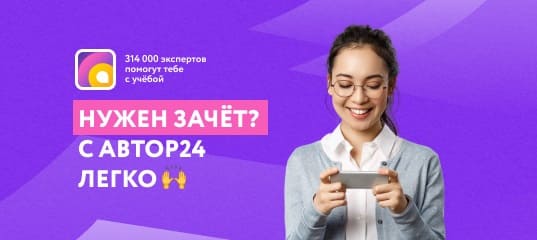
Мы поможем в написании ваших работ!