Элементы режимов резания при фрезеровании
Министерство образования и науки Российской Федерации
Федеральное государственное бюджетное образовательное учреждение
высшего образования
«Магнитогорский государственный технический университет
им. Г.И. Носова»
(ФГБОУ ВО «МГТУ им. Г.И. Носова»)
Кафедра машины и технологии обработки давлением и машиностроения
ИНСТИТУТ МЕТАЛЛУРГИИ, МАШИНОСТРОЕНИЯ И МАТЕРИАЛООБРАБОТКИ
Лабораторная работа №1
по дисциплине «Научные основы размерной формообразующей обработки»
Выполнил: студент группы МКТм-17 Никитченко Р.В.
Проверил: Огарков Н.Н. д.т.н., профессор каф. МиТОДиМ
Фрезерование деталей на универсально-фрезерном станке
Цель работы: изучение назначения и устройства универсально-фрезерного станка, органов его управления. Проведение наладки и настройки станка на заданный режим фрезерования.
Используемое оборудование: универсально-фрезерный станок 6Н81Г.
Назначение и краткая характеристика станка
Фрезерование является одним из наиболее распространённых и производительных видов обработки плоскостей, пазов, винтовых канавок, фасонных поверхностей.
Фреза – многозубый вращаемый инструмент, режущие зубья которого последовательно, один за другим вступают в работу.
Универсально-фрезерный станок 6Н81Г предназначен для различных фрезерных работ:
1. Фрезерование плоскостей цилиндрическими фрезами (рис. 1.1,1.2а).
|
|
2. Фрезерование уступов, пазов, канавок (рис. 1.2в.).
3. Фрезерование фасонных поверхностей фасонными фрезами (рис. 1.2ж,и.).
4. Отрезка заготовки отрезными фрезами (рис. 1.2г.).
Наличие поворотного стола на ставке делает его универсальным, позволяет при помощи делительной головки изготавливать косозубые шестерни, винтовые канавки.
Техническая характеристика станка:
Рабочая поверхность стола:
200×800 мм.
Наибольшее перемещение стола, в мм:
продольные – 650;
поперечное – 200;
вертикальное – 400.
Расстояние от оси шпинделя до стола, в мм:
наибольшее – 400;
наименьшее – 60.
Мощность главного электродвигателя, в кВт: 2,8;
Пределы угла поворота стола, в градусах: 45º.
Числа оборотов шпинделя, мин-1: 50, 71, 100, 140, 200, 280, 400, 560, 800, 1120, 1600, 2240.
Величина подачи, мм/мин: 22,4, 31,5, 45, 63, 90, 125, 180, 250, 300, 355, 710, 1000.
Скорость ускоренного перемещения стола, мм/мин:
вертикальное – 500;
поперечное – 500;
продольное – 1000.
Рисунок 1.1 – Схема фрезерования плоскостей цилиндрическими фрезами
Рисунок 1.2 – Схемы обработки фрезами различных поверхностей
Устройство станка
На основании (фундаментной плите) установлена пустотелая литая станина, на которой крепятся и по вертикальным направляющим которой перемещаются остальные узлы станка. Внутри станины размещена коробка скоростей, с помощью которой, движение от электродвигателя передается к шпинделю и осуществляется ступенчатое регулирование частоты вращения шпинделя в пределах от 65 до 1800 об/мин. Шпиндель - пустотелый выходной вал коробки скоростей служит для установки в нем оправки для крепления фрезы.
По вертикальным направляющим станины перемещается консоль, несущая на себе поперечные салазки, перемещающиеся по направляющим консоли, в продольных направляющих которой перемещайся стол, служащий для установки приспособлений для закрепления обрабатываемой детали. Внутри консоли размещается коробка подач, которая служит для передачи движения от отдельного электродвигателя к механизмам продольного и поперечного перемещения стола и механизму вертикального перемещения консоли. С помощью коробки подач можно изменять величину продольной, поперечной и вертикальной подачи. Следует иметь в виду, что подача устанавливается с помощью рукояток коробки скоростей в мм/мин, т.е. это минутная подача SM. По горизонтальным направляющим станины перемещается хобот, который с помощью серьги создает дополнительную опору для оправки с установленной на ней фрезой.
|
|
|
|
Движения в станке
В зависимости от вида фрезерования на станке включают определённые движения его узлов.
Движение резания (главное) – вращение фрезы, закреплённой на оправке или в патроне.
Движение подач:
1) вертикальная подача – перемещение консоли в вертикальном направлении;
2) поперечная подача – перемещение консоли в поперечном направлении (параллельно оси фрезы);
3) продольная подача – горизонтальное перемещение продольных салазок перпендикулярно оси фрезы. Вспомогательные движения – ручные и быстрые механические перемещения в направлении подач.
Принцип работы станка
Заготовку закрепляем непосредственно на столе или в тисках, или в патроне делительной головки.
Инструмент – различные фрезы, устанавливают и закрепляют на оправке. Скорость вращения фрезы регулируется коробкой скоростей, представляющей набор зубчатых передач. Для увеличения количества ступеней скоростей на станке применён зубчатый перебор, позволяющий уменьшить число оборотов фрезы в 8 раз при том же положении рукоятки коробки скоростей. Для установления величины подач применяют коробку подач, состоящую так же, как и коробка скоростей, из нескольких зубчатых передач.
|
|
Органы управления станком
Для настройки станка на заданный режим, т.е. для включения необходимой скорости резания V, подачи S и глубины резания t на станке установлены рукоятки, управляющие определёнными узлами станка. На общем виде станка (рис. 1.3) указаны следующие органы управления: 1 - рукоятка закрепления стола от продольного перемещения; 2- маховик ручной продольной подачи стола; 3- рукоятка включения продольной механической подачи; 4- рукоятка включения поперечной механической подачи; 5- рукоятка включения вертикальной механической подачи; 6- рукоятка переключения перебора механизма подачи; 7- рукоятка вертикальной подачи стола вручную; 8- маховик поперечной подави стола вручную; 9- рукоятка включения ускоренной подачи во всех направлениях; 10- рукоятка привода ручного насоса смазки стола.
Рисунок 1.3 – Общий вид универсально-фрезерного станка 6Н81Г
Элементы режимов резания при фрезеровании
Элементами режима резания при фрезеровании являются скорость резания V (м/мин), подача S (мм/мин), глубина резания t (мм).
1. Скорость резания V– окружная скорость вращения фрезы, величину которой определяем по формуле, м/мин.
V = ,
где Dфр – диаметр фрезы (мм); nфр – число оборотов фрезы (об/мин).
2. Подача S – величина перемещения заготовки в единицу времени в направлении подачи. При фрезеровании различают следующие подачи:
Sz – подача на один зуб (подача за время поворота фрезы на 1 зуб, мм/зуб);
S – подача на один оборот фрезы, мм/об;
Sm – минутная подача, мм/мин:
Sm = S∙nфр = Sz∙Zфр∙nфр
где Zфр – число зубьев фрезы.
3. Глубина резания t – толщина слоя металла, срезанного за один рабочий ход фрезы, измеряемый в миллиметрах.
4. Ширина фрезерования B определяется шириной зуба фрезы при обработке пазов дисковыми и отрезными фрезами, а также при обработке прямозубыми цилиндрическими фрезами, если поверхность обрабатываем на всю ширину зуба.
5. Машинное время T – время, необходимое для снятия стружки за один рабочий ход, величину которого определяем по формуле, мин:
T0= , (мин),
где Y = - длина врезания,
L – длина обработки,
l – величина перебега 1…10 миллиметров.
Порядок выполнения работы
1. Ознакомиться с общим устройством универсально-фрезерного станка и его основными механизмами, и его органами управления.
2. Получить индивидуальное задание у преподавателя.
3. В зависимости от применяемой фрезы и заданных элементах режима резания определить число оборотов фрезы в минуту nфр, машинное время T0, а также величины подач Sмин, S и Sz.
4. Закрепить заготовку и фрезу.
5. Провести настройку станка на заданный режим резания, т.е. при помощи рукояток установить необходимое число оборотов фрезы nфр, величину подачи заготовки Sm и глубину резания t.
6. Произвести обработку детали в присутствии учебного мастера.
7. Составить отчёт.
Содержание отчёта
1. Цель работы.
2. Назначение и краткая характеристика универсально-фрезерного станка, инструментов и видов фрезерования, производимых на станке.
3. Эскиз обработки заданной детали (индивидуальное задание по таблице 1.1) с указанием способа крепления заготовки, инструмента и обозначением элементов режима резания.
Таблица 1.1 – Индивидуальное задание
№ варианта | Вид операции | Режим резания | Примечание | ||||
6 | Обработка плоской поверхности цилиндрической фрезой | Глубина резания t, мм | Подача S,мм/мин | Скорость резания V, м/мин | Длина обработки Y, мм | Ширина фрезерования Y, мм |
|
5 | 63 | 60 | 100 | 50 |
Рисунок 1.4 – Цилиндрическая косозубая фреза, закреплённая на оправке
Параметры фрезы по ГОСТ 29092 – 91:
Материал фрезы по ГОСТ 19265 – Р6М5
Диаметр фрезы – 80 мм;
Длина фрезы – 75 мм;
Длина зуба – 79,7 мм;
Число зубьев – 18 шт.
1. Зная заданную скорость резания и определённый диаметр фрезы, рассчитаем число оборотов фрезы:
nфр =
Так как коробка скоростей станка не может выдать полученное значение оборотов, берём ближайшее наименьшее значение 200 об/мин.
2. Зная обороты фрезы, можем подсчитать фактическую окружную скорость фрезы:
Vфр =
3.Рассчитаем подачу на зуб:
Sz =
4. Рассчитаем подачу на оборот фрезы:
S = 0,014∙18 = 0.252 мм/об
5. Рассчитаем минутную подачу:
Sm = 0,252∙200 = 50.4 мм/мин
6. Рассчитаем длину врезания и машинное время:
Y = = 75.16 мм
T0 = = 3.6 мин
Таблица 1.2 – Величины элементов режима резания
№ варианта | Вид операции | Диаметр фрезы Dфр, мм | Число зубьев фрезы Zфр, шт | Ширина фрезерования B, мм | Глубина резания t, мм | Подача Sm, мм/мин | Подача на один зуб Sz, мм/зуб | Число оборотов фрезы nфр, об/мин | Скорость фрезерования V, м/мин | Длина обработки L, мм | Машинное время T, мин |
6 | Обработка плоской поверхности цилиндрической фрезой | 80 | 18 | 50 | 5 | 50.4 | 0.014 | 200 | 50.26 | 100 | 3.6 |
Вывод:ознакомились с общим устройством универсально-фрезерного станка и его основными механизмами и органами управления. Получили индивидуальное задание у преподавателя. В зависимости от задания подобрали фрезу, изобразили её рисунок, определили её параметры и рассчитали элементы режима резания, такие как: число оборотов фрезы в минуту nфр, машинное время T0, а также величины подач Sмин, S и Sz. Закрепили заготовку и фрезу. Провели настройку станка на заданный режим резания, т.е. при помощи рукояток установили необходимое число оборотов фрезы nфр, величину подачи заготовки Sm и глубину резания t. Произвели обработку детали в присутствии учебного мастера. Все полученные данные свели в отчётную таблицу 1.2.
Дата добавления: 2018-08-06; просмотров: 81; Мы поможем в написании вашей работы! |
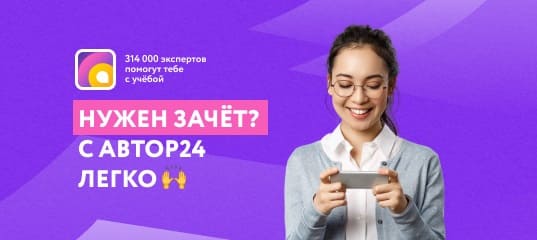
Мы поможем в написании ваших работ!