Материалы подшипников качения
Назначаются с учётом высоких требований к твёрдости и износостойкости колец и тел качения.
Здесь используются шарикоподшипниковые высокоуглеродистые хромистые стали ШХ15 и ШХ15СГ, а также цементируемые легированные стали 18ХГТ и 20Х2Н4А.
Твёрдость колец и роликов обычно HRC 60 ¸ 65, а у шариков немного больше – HRC 62 ¸ 66, поскольку площадка контактного давления у шарика меньше.
Сепараторы изготавливают из мягких углеродистых сталей либо из антифрикционных бронз для высокоскоростных подшипников. Широко внедряются сепараторы из дюралюминия, металлокерамики, текстолита, пластмасс.
Смазка подшипников качения
Смазка подшипников качения необходима для:
· снижения сил трения, возникающих между их телами качения, кольцами и сепаратором;
· усиления местного теплоотвода от рабочих поверхностей и общего теплоотвода от подшипника в целом;
· снижения динамичности приложения нагрузки к деталям подшипника и уровня его шума;
· предотвращения коррозии элементов подшипника.
Для смазывания подшипников качения применяют жидкие масла и пластичные смазочные материалы.
Жидкие смазки применяются при более высоких температурах, когда твердые смазки плавятся и вытекают. Обеспечивают минимальные потери на трение.
Применяются следующие способы смазки:
· масляная ванна для подшипников горизонтальных валов при n ≤ 10000об/мин, для подшипников малых размеров допускается и при большей частоте вращения. Уровень масла при
|
|
n ≤ 2000об/мин должен быть не выше центра нижнего шарика или ролика, при большей частоте вращения уровень масла лишь касается шарика или ролика;
· смазка масляным туманом для высокоскоростных малонагруженных подшипников; смазка проникает в подшипники, омывает и охлаждает их;
· смазка разбрызгиванием для подшипников, не изолированных от общей системы смазки (например, редукторы), при n = 2000... 3000об/мин; при большей частоте вращения следует предусматривать устройства, ограничивающие поступление масла в подшипник;
· циркуляционная смазка самотеком или под давлением через форсунки. Последний способ применяется для подшипников, работающих в тяжелых условиях, когда необходим интенсивный отвод теплоты;
· фитильная смазка назначается в широких пределах скоростей для подшипниковых узлов горизонтальных и вертикальных валов.
Достоинства применения жидких смазочных материалов: возможность централизованного смазывания с автоматизацией процесса подачи смазочного материала. Применение жидкого смазочного материала допускает полную его смену без разборки узла, хорошо отводит тепло. Периодичность замены масла — 3—6 месяцев, пополнение — 1—2 раза в месяц.
|
|
Пластичные смазки представляют собой загущенные специальными загустителями жидкие масла с включением различных присадок. Обычно используют минеральные масла ИГ-А32, ИГ-А68, составляющие 75…90% общего объема. В качестве загустителей применяют кальциевые, натриевые и литиевые мыла, а также углеводороды (парафин, церезин). В качестве присадок обычно используют дисульфид молибдена, графит.
Основными пластичными смазочными материалами, применяемыми в подшипниковых узлах редукторов общего назначения, в настоящее время являются Литол–24 ТУ 21150-75 (для работы в температурном интервале – 40…+130°С) и ЦИАТИМ–201 ГОСТ 6267-74 (–60…+90°С).
Пластичные смазочные материалы по сравнению с жидкими имеют следующие преимущества:
не вытекают из узлов при нормальных условиях работы; лучше защищают подшипники от коррозии; могут работать в узле без пополнения в течение продолжительного времени (до одного года) и без особого надзора; требуют менее сложных конструкций уплотнительных устройств.
Их недостаток в том, что в конструкции требуется предусматривать специальные полости. Эту полость первоначально заполняют на 2/3 объёма при n £ 1500 об/мин или на 1/2 объёма при n > 1500 об/мин. В дальнейшем обычно через каждые три месяца через специальные устройства (пресс-маслёнки) добавляют свежую смазку, а через год её меняют с предварительной разборкой и промывкой узла.
|
|
При специфических условиях эксплуатации, например, при низких или высоких температурах, в вакууме или при повышенных требованиях к чистоте смазочных материалов, применяются твердые смазки. Наиболее популярными материалами из данной категории можно назвать графит и дисульфид молибдена. Твердые смазки характеризуются высокими антифрикционными свойствами, что объясняется их пластинчатой структурой. Малое трение обеспечивает высокую стойкость к износу, но чтобы обеспечить длительную работу пленки твердой смазки используются связующие с высокими показателями адгезии. Оптимальная толщина данного слоя должна быть в диапазоне 5-25 мк.
Контрольные вопросы
1. Расшифровать маркировку подшипника
Дата добавления: 2018-05-13; просмотров: 119; Мы поможем в написании вашей работы! |
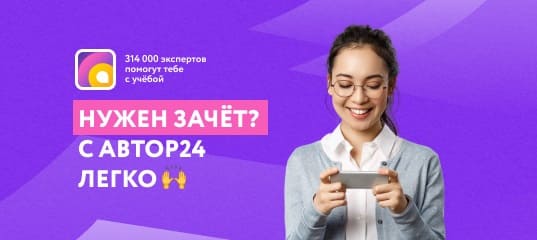
Мы поможем в написании ваших работ!