Подготовка деталей под сварку
Федеральное агентство Российской Федерации по образованию
Государственное образовательное учреждение высшего профессионального образования
Санкт-Петербургский государственный горный институт
имени Г.В. Плеханова (технический университет)
Кафедра конструирования горных машин
и технологии машиностроения
ТЕХНОЛОГИЯ
КОНСТРУКЦИОННЫХ
МАТЕРИАЛОВ
Изготовление неразъемных соединений методами сварки и пайки
Методические указания к лабораторным работам
для студентов машиностроительных и технологических специальностей всех форм обучения
Санкт-Петербург
2006
УДК 621.7/09.612.9(0.75.83)
ТЕХНОЛОГИЯ КОНСТРУКЦИОННЫХ МАТЕРИАЛОВ. Изготовление неразъемных соединение методами пайки и сварки: Методические указания к лабораторным работам / Санкт-Петербургский горный институт (технический университет). Сост.: Ю.П. Бойцов, В.И. Болобов, С.Л. Иванов, Э.А. Кремчеев, С.Ю. Кувшинкин. СПб, 2006, 32 с.
Приведены рекомендации и пояснения по выполнению лабораторных работ. Содержатся сведения, необходимые как для выполнения лабораторных работ, так и для самостоятельных работ по дисциплине.
Методические указания предназначены для студентов машиностроительных и технологических специальностей всех форм обучения.
Ил. 15. Библиогр.: 9 назв.
Научный редактор проф. И.П.Тимофеев
|
|
© Санкт-Петербургский горный
институт им. Г.В. Плеханова, 2006 г.
Лабораторная работа №1
«Сварочное производство. Изготовление деталей ручной электродуговой сваркой»
Введение
Сварка — это процесс получения неразъемных соединений посредством установления межатомных связей между свариваемыми частями при их местном или общем нагреве, пластическом деформировании или совместном действии того и другого.
Ручная дуговая сварка применяется главным образом в изделиях, имеющих короткие и прерывистые швы, а также швы сложной конфигурации, т.е. там, где трудно или невыгодно применять автоматические методы сварки. Положительной стороной ручной сварки является возможность производить сварку в любом пространственном положении, что особенно важно для сварки в монтажных условиях. Ручной дуговой сваркой можно сваривать стали, чугуны, алюминий и его сплавы, медь и медные сплавы, с применением для каждого металла соответствующих электродов.
К недостаткам ручной дуговой сварки относят: трудности сварки тонкого материала (менее 1...2 мм), высокие требования к квалификации сварщика, малая производительность.
Цель работы — изучение основ технологии сварочного производства. Разработка технологического процесса неразъемного соединения металлических конструкций с использованием ручной электродуговой сварки плавящимся электродом, как наиболее распространенной в условиях ремонтно-механических цехов горных предприятий.
|
|
Основные типы сварных соединений
К основным типам сварных соединений для ручной дуговой сварки относят: стыковые, угловые, тавровые и нахлесточные.
Соединение стыковое без разделки кромок (рис. 1.1, а) рекомендуется для толщин металла S ≤ 3 мм. Наличие зазора обеспечивает полное проплавление. При S = 1...2 мм величина зазора a ≤ 1 мм, при 2 < S ≤ 3 мм a ≤ 1,5 мм.
Рис. 1.1. Рекомендуемые типы соединений для ручной дуговой сварки
При стыковом соединении изделий большей толщины (3 < S ≤ 20 мм) с целью предотвращения непровара рекомендуется производить V-образную разделку кромок с притуплением (рис. 1.1, б), которое необходимо для того, чтобы при сварке кромки не проплавлялись и расплавленный металл не протекал внутрь конструкции. Величина притупления принимается равной 2...3мм для толщин изделий до 20мм и 4...5 мм для больших значений S.
Стыковое соединение с Х-образной разделкой кромок (рис. 1.1, в) применяют при 20 < S ≤ 30 мм. При этом соединение сваривается с двух сторон.
|
|
Угловое соединение вида рис. 1.1, г рекомендуется для толщин до 8мм,
- вида рис. 1.1, д — для толщин от 8 до 26 мм,
- вида рис. 1.1, е — для толщин более 26 мм.
Тавровое соединение вида рис. 1.1, ж рекомендуется для толщин до 6 мм; при больших толщинах свариваемых материалов - соединение вида рис. 1, з.
Нахлесточное соединение (рис. 1.1, и) применяется при S = 2...6 мм при величине зазора а от 0 до 4 мм. При этом величина нахлеста одного листа на другой должна быть ≥ 3S. В сравнении со стыковым нахлесточное соединение отличается более легкой сборкой сварных узлов, однако из-за несоосности соединяемых деталей в них при работе возникает изгибающий момент, снижающий прочность соединения. При применении нахлесточного соединения, так же как таврового и углового, имеющих повышенную жесткость, больше вероятность образования трещин при сварке
Подготовка деталей под сварку
Разделку кромок под сварку можно производить различными способами. Самым грубым и малопроизводительным из них является срубание кромок ручным или пневматическим зубилом. При этом способе края кромок получаются неровными. Наиболее ровные и чистые кромки получаются при изготовлении их на специальных кромкострогальных или фрезерных станках. Применение кислородной резки, ручной или механизированной, для скоса кромок является самым экономичным. Шлаки и окалина, остающиеся после кислородной резки, должны быть удалены с помощью зубила и стальной щетки или шлифовальных машин.
|
|
Следует уделять большое внимание чистоте кромок, так как загрязненная поверхность кромок металла приводит к плохому провару и образованию в сварном шве неметаллических включений. Поэтому перед сваркой кромки стыка, а также соседние с каждой кромкой участки на ширину 20...30 мм должны очищаться до металлического блеска от окалины, ржавчины, масла, краски и других загрязнений. Очистка от окалины, краски и масла может осуществляться пламенем сварочной горелки. При этом окалина отстает от металла, а масло и краска сгорают. После нагрева пламенем поверхность зачищается стальной щеткой.
При сборке деталей под сварку нужно следить за тем, чтобы кромки правильно располагались одна относительно другой, чтобы выдерживались установленные зазоры, не было перекосов и т. д.
Для того чтобы в процессе сварки установленные зазоры и положение деталей не изменялись, перед сваркой делают предварительную прихватку деталей, т. е. свариваемые детали соединяют друг с другом в нескольких местах короткими швами. Длину прихваток и расстояние между ними выбирают в зависимости от толщины свариваемого металла и длины шва. При сварке тонкого металла и коротких швах длина прихваток - не более 5 мм. При сварке толстого металла и значительных длинах швов длина прихваток 20...30 мм при расстоянии между ними 300...500 мм. В случае сварки деталей значительной толщины прихватка может заполнять разделку примерно на 2 / 3 ее глубины.
Порядок постановки прихваток перед сваркой длинных швов показан на рис. 1.2, а, б. Прихватки должны располагаться от края изделия на расстоянии не менее 10 мм.
Рис. 1.2. Порядок простановки прихваток: а — от центра листа; б — от краев листа
Для сварки изделий из листового металла толщиной до 1 мм в месте сварки листов делают их отбортовку, после чего сложенные вместе листы сваривают. Более толстые листы сваривают без отбортовки.
Зазор между листами должен быть одинаковым по всей длине шва и соответствовать свариваемой толщине металла (см. п. 1.1). Для того чтобы при постановке прихваток зазор не уменьшался за счет усадки металла прихваток, в зазор между листами устанавливают прокладки (обрезки листа, проволоку). После прихватки прокладки могут быть удалены.
Для выравнивания кромок листов при прихватке и сварке пользуются клиновыми прокладками, изображенными на рис. 1.3, а.
Прокладка 1 представляет собой пластину, вставляемую в зазор между соединяемыми листами. С одной стороны листов в круглые отверстия прокладки закладывают цилиндрический стержень 2, с другой — коническую оправку 3. При вбивании последней кромки листов оказываются зажатыми, чем предупреждается их смещение.
Рис. 1.3. Способ выравнивания (а) и стягивания (б) кромок листовых конструкций
Для стягивания кромок листовых конструкций может применяться болтовое стяжное устройство, показанное на рис. 1.3, б.
Описанные приемы сварки изделий из листового металла могут применяться как при изготовлении плоских конструкций, так и обечаек цилиндрических сосудов. При соединении днища с обечайкой перед сваркой ставят прихватки в порядке, указанном на рис. 1.4.
Рис. 1.4. Порядок простановки прихваток при соединении днища с обечайкой
Такой порядок постановки прихваток уменьшает коробление изделия, так как оно нагревается более равномерно. Таким же образом соединяют между собой обечайки. Продольные швы обечаек не должны располагаться на одной линии.
При изготовлении коробчатых изделий (рис. 1.5) вначале сваривают угловые швы 1, 2 и 3 боковых стенок.
Рис. 1.5. Порядок сварки коробчатого изделия
Затем стенки приваривают к днищу швами 4, 5, 6 и 7. Изготовление ящика заканчивают сваркой вертикального шва 8. При указанном порядке сварки достигается наименьшее коробление изделия.
Трубы соединяют между собой чаще всего в стык (рис. 1.6, а), так как стыковое соединение требует простой подготовки кромок и наименьшей затраты времени.
Рис. 1.6. Типы сварных соединений труб: а — стыковое; б — с вкладышем; в — враструб; г — стыковое с вкладками
Иногда для удобства сварки внутрь труб вставляют кольца (рис. 1.6, б), облегчающие сборку и сварку труб. Постановка кольца нежелательна из-за того, что оно уменьшает внутреннее сечение трубы в месте соединения труб и тем самым создает излишнее сопротивление движению газа или жидкости. (При сборке магистральных газо- и нефтепроводов постановка колец запрещена и сварка производится только встык). Для того чтобы не уменьшать внутреннего сечения трубы, применяют соединение враструб (рис. 1.6, в), но оно требует специальной подготовки одного конца трубы. Иногда для усиления стыкового шва ставят муфты либо отдельные накладки (рис. 1.6, г ).
Трубы соединяют с помощью прихваток длиной 30...50 мм. При диаметре труб до 300 мм ставят три-четыре прихватки, при большем диаметре число прихваток увеличивают. Порядок постановки их такой же, как и при сварке днищ. Первая прихватка обычно ставится внизу.
Дата добавления: 2018-04-05; просмотров: 790; Мы поможем в написании вашей работы! |
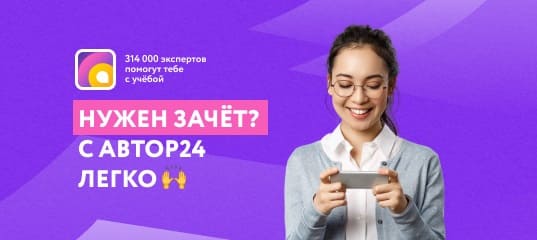
Мы поможем в написании ваших работ!