Реакторы идеального вытеснения: определение времени реакции и объема трубчатого реактора для условий идеального вытеснения (реакции первого и второго порядков)
Федеральное агентство по образованию
Нижнекамский химико-технологический институт (филиал)
Государственное образовательное учреждение
высшего профессионального образования
«Казанский государственный технологический университет»
Кафедра: Машин и аппаратов химических производств и предприятий строительных материалов
КОНТРОЛЬНАЯ РАБОТА
По дисциплине: Машины и аппараты химических производств
Вариант:17
Выполнил: студент группы
механического факультета
Проверил:
Нижнекамск 2009г
Содержание:
1. Вопрос 42.
Фильтры для жидкостей. Классификация фильтров. Емкостные фильтры, конструкции, порядок расчета. Рамные и камерные фильтры, простые и автоматизированные.
2. Вопрос 9
Реакторы идеального вытеснения: определение времени реакции и объема трубчатого реактора для условий идеального вытеснения (реакции первого и второго порядков)
3. Вопрос 16
Роль теплообменной аппаратуры в химической , нефтехимической и нефтеперерабатывающей промышленности. Факторы, влияющие на выбор конструкции теплообменников. Классификация теплообменной аппаратуры.
4. Вопрос 19
Кожухотрубчатые теплообменные аппараты: теплообменник с плавающей головкой (типа П), устройство, характеристика, основные параметры и размеры.
5. Задача А4
6. Задача Б17
Литература
Вопрос 42
|
|
Фильтры для жидкостей. Классификация фильтров. Емкостные фильтры, конструкции, порядок расчета. Рамные и камерные фильтры, простые и автоматизированные.
В фильтрах проводят процесс разделения неоднородных систем с помощью пористых перегородок, пропускающих одну из фаз системы и задерживающих другую. Разделяемость суспензии в значительной мере зависит от размеров и концентрации твердых частиц, а также от вязкости и плотности сплошной фазы. В зависимости от среднего размера частиц различают грубые (более 100 мкм) и тонкие суспензии (0,5—100 мкм), мути (0,1 — 0,5 мкм) и коллоидные растворы (от 0,1 мкм до размеров молекул). Все суспензии, кроме коллоидных растворов, в спокойном состоянии способны отстаиваться под действием силы тяжести, образуя осадок на дне сосуда.
В качестве фильтровальных пористых перегородок в фильтрах используют различные ткани, прополочные и полимерные сетки, бумагу, металлические, стеклянные, керамические плоские пористые пластины и полые, цилиндры и др. Довольно широко используют также слои зернистого материала — песка, гравия, угля, древесных опилок, диатомита. Зернистый материал используют в насыпных фильтрах и фильтрах с намывным слоем зернистого фильтрующего материала.
|
|
Размеры пор перегородки зависят от размеров взвешенных твердых частиц, которые не должны проходить через фильтр для получения по возможности чистого фильтрата. Задерживаемые перегородкой твердые частицы обычно образуют на ней слой осадка. В связи с этим сплошная фаза (жидкость или газ) проходит через два слоя: осадок и перегородку. С течением времени толщина осадка увеличивается, возрастает гидравлическое сопротивление и уменьшается скорость процесса.
При заданной производительности размеры фильтра зависят от величины и закона изменения во времени скорости прохождения жидкости через осадок и пористую перегородку, т. е. от скорости фильтрации. Движущей силой фильтрации является создаваемая тем или иным способом разность давлений над осадком и под пористой перегородкой.
В зависимости от величины и способа создания движущей силы различают: вакуум-фильтры; фильтры, работающие при повышенном давлении (фильтр-прессы); фильтры, работающие под наливом (под действием гидростатического давления слоя суспензии). Существуют также фильтры, в которых используют одновременно повышенное давление перед фильтровальной перегородкой и вакуум' за ней.
|
|
Фильтры периодического действия работают преимущественно В подавляющем большинстве случаев фильтры непрерывного действия работают под вакуумом. К ним относятся вакуум-фильтры барабанные, дисковые, тарельчатые, карусельные и ленточные.
Рамные и камерные фильтр-прессы. Фильтры периодического действия рамного типа широко используют в промышленности благодаря сравнительно простому устройству и возможности проводить процесс при повышенном давлении (обычно 0,3— 0,5 МПа). Типовой конструкцией является плиточно-рамный фильтр-пресс (рис. 3.1).
Рис. 3.1. Плиточно-рамный фильтр-пресс
Фильтровальными перегородками в нем служат прямоугольные отрезки ткани, зажатые между чередующимися рамами 2 и плитами 3. Плиты и рамы (обычно чугунные) расположены вертикально и закреплены на опорной конструкции, состоящей из стоек, опорной 1 и прижимной 5 плит, двух опорных брусьев 4 круглого сечения и гидравлического или электромеханического зажима 6. В малых фильтр-прессах используют ручной винтовой зажим. Для подвода суспензии, промывной жидкости и сжатого воздуха опорная плита 1 снабжена штуцерами (бобышками) 7 и 8. Плиты фильтров с раздельным отводом фильтрата снабжены кранами 9.
|
|
Рама (рис. 3.2) имеет сквозную полость в и гладко обработанные края 2. В плите выполнены две
впадины д, разделенные стенкой 4; ребра 3 немного не доходят до нижнего края впадин и служат опорой для фильтровальной ткани. Плиты и рамы опираются приливами (ручками) 1 на опорные брусья. В краях плит и рам имеются отверстия гиг, образующие при сжатии плит каналы для подачи суспензии, сжатого воздуха и промывной жидкости, а также канал для отвода фильтрата. Отверстия г для суспензии радиальными отверстиями сообщаются с полостями в рам, а отверстия е для сбора фильтрата — со впадинами д плит.
Рис. 3.2. Рама (а) и плита (б) фильтр-пресса
Используют также фильтр-прессы с раздельным отводом фильтрата из каждой плиты. В этом случае сквозные отверстия е отсут ствуют, а впадины каждой плиты соединены с отводным отверстием а ее нижней части, снабженным краном. Вытекающий из кранов фильтрат собирается в специальный желоб, откуда отводится по назначению. Таким образом, можно отключить закрытием кранов те. плиты, из которых выходит загрязненный фильтрат (например, из-за повреждения фильтровальной ткани).
После окончания фильтрации осадок промывается жидкостью. По окончании промывки происходит осушка осадка сжатым воздухом, подаваемым по каналу для суспензии или промывной 'жидкости Затем освобождают зажим, плиты и рамы поочередно отодвигают по опорным брусьям в сторону зажима и из полостей рам вручную скребком или лопаткой удаляют осадок, падающий в расположенное под фильтром корыто. После выгрузки осадка плиты и рамы вновь собирают, зажимают и никл работы фильтра повторяется.
Основные преимущества рамных фильтр-прессов — большая удельная поверхность фильтрации, отнесенная к единице массы аппарата, отсутствие движущихся частей, возможность отключать отдельные плиты (при раздельном отводе фильтрата). Благодаря значительной движущей силе фильтр обладает высокой производительностью единицы фильтрующей поверхности.
Сложность и трудоемкость разгрузки фильтра от осадка ограничивает его применимость в основном малоконцентрирован-ными суспензиями. Недопустимо использовать рамный фильтр-пресс, если жидкая фаза суспензии или промывная жидкость являются легколетучими, ядовитыми или пожароопасными веществами, так как фильтр не герметичен.
Камерный фильтр-пресс по устройству аналогичен плиточно-рамному. Основное отличие состоит в том, что
Рис. 3.3. Камерный фильтр-пресс
чередующиеся плиты и рамы заменены плитами 1 (рис. 3.3), по конструкции несколько отличающимися от плит рамного фильтр-пресса. Глад кая поверхность по краям каждой плиты приподнята над краями ребер 2 во впадинах (над дренирующей поверхностью), образуя борт. Между соседними плитами зажаты ,два листа фильтровальной ткани (две салфетки) 3 и 4. При сжатии плит вследствие деформации фильтровальной ткани в каждой паре плит образуется пространство (камера) а для осадка. Эти камеры играют ту же роль, что и полости рам рамного фильтр-пресса. Суспензия перетекает из
камеры в камеру через отверстие в бобышке плиты. Каждая фильтровальная перегородка (салфетка) имеет отверстие, края которого прижаты к плоскости бобышки уплотнительными втулками 5 или 6. Промывная жидкость и сжатый воздух подаются тем же путем, что и суспензия. Фильтрат отводится так же, как в рамном фильтр-прессе; возможен как общий, так и раздельный отвод фильтрата из плит.
Благодаря отсутствию рам камерный фильтр-пресс имеет меньшие размеры, чем рамный с той же поверхностью фильтрации. Малый объем пространства для осадка и значительное допускаемое давление объясняют большее удобство камерных фильтр-прессов по сравнению с рамными при обработке малоконцентрированных труднофильтруемых суспензий.
Автоматизированные камерные фильтр-прессы. Существенный недостаток, затрудняющий использование обычных плиточно-рамных и камерных фильтр-прессов — длительность и трудоемкость выгрузки осадка, проводимой обычно вручную. В связи с этим, несмотря на простоту конструкции, компактность и низкую удельную металлоемкость, их заменяют фильтр-прессами с механической выгрузкой осадка.
Примером может служить автоматизированный камерный фильтр-пресс ФПАКМ (рис. 3.4).
Рис 3.4. Схема автоматизированного фильтр-пресса ФПАКМ
Фильтр состоит из пакета горизонтальных фильтровальных плит 2, закрепленных на раме с возможностью вертикального перемещения. Рама состоит из нижней опорной 6 и верхней упорной / плит, соединенных четырьмя вертикальными плоскими стяжками 5, которые служат одновременно направляющими для фильтровальных плит. Для поднятия и опускания плит предназначены электромеханический зажим 4 и нажимная плита 3. В поднятом состоянии плиты 2 прижаты одна к другой и зажаты между нажимной 3 и упорной 1 Плитами. При опускании плит между ними образуется зазор 45 мм. Время закрытия или раскрытия фильтр-пресса 50—70 с. Фильтровальная ткань 9 в виде непрерывной замкнутой ленты натянута на ряд направляющих валиков (роликов) 10 и протянута между фильтровальными плитами. В стадии фильтрования ткань зажата между сомкнутыми плитами и на ней образуется осадок. При выгрузке осадка плиты раздвигаются, ткань освобождается и приводится в движение приводным валиком 5. Огибая направляющие валики 10, ткань освобождается ножами (скребками) 11 от осадка, который ссыпается в бункеры или на конвейеры. Фильтр снабжен специальной камерой 7 регенерации ткани; проходя камеру, ткань омывается водой и очищается скребками или щетками.
К фильтровальным плитам приварены патрубки, снабженные уплотнителями, которые при сжатии плит образуют с одной стороны коллектор для подачи суспензии, промывной жидкости и воздуха, а с другой — коллектор для отвода основного и промывного фильтратов. Трубчатый коллектор, отводы которого соединены резинотканевыми шлангами с соответствующими патрубками плит, служит для привода отжимных диафрагм водой, подаваемой под давлением в специальные полости плит.
Устройство плит схематически показано на рис. 3.5. Каждая плита (кроме верхней и нижней) состоит из двух частей 1 я 2, между которыми зажата по краям резиновая отжимная диафрагма 4.
Рис. 3.5. Схема устройства плит фильтр-пресса ФПАКМ
Верхняя часть плиты имеет впадину б, закрытую сверху перфорированным листом 3, снабжена патрубками 8 и 9 и служит для сбора фильтрата. На ней имеются также патрубок 7 и отверстия для подачи воды в пространство б между дном верхней части плиты и диафрагмой. Нижняя часть плиты представляет собой раму с полостью а и патрубками 5 и 6 и служит для подачи в нее суспензии и накопления осадка. По периметру плиты снизу выполнена канавка, в которую вставлен резиновый шнур 11, уплотняющий зазор между плитой и фильтровальной тканью 10.
В стадии фильтрования при сомкнутых плитах через приемный коллектор, образуемый патрубками 6, и патрубки 5 в нижние части плит подается суспензия. Проходя через фильтровальную ткань, она разделяется на осадок, остающийся на ткани, и фильтрат, отводимый из верхних полостей б нижерасположенных плит через патрубки 8 в патрубки 9, образующие отводной коллектор. После накопления осадка определенной толщины он подвергается осушке сжатым воздухом, подаваемым также через приемный коллектор. Воздух вытесняет жидкость из полостей а и пор осадка. При этом осадок дополнительно отжимается упругими диафрагмами 4, давящими на осадок. Частицы осадка сближаются, и из его пор вытесняется жидкость. К диафрагмам из специального коллектора через патрубки 7 в полости в подается под давлением вода. По окончании отжима давление в водяном коллекторе уменьшается и диафрагмы выпрямляются. При необходимости таким же образом (через приемный коллектор) осадок промывается и повторно подвергается осушке. По окончании осушки плиты, опускаясь, раздвигаются, включается соответствующий механизм и фильтровальная ткань перемещается. При этом происходит снятие осадка с ткани и ее очистка в камере регенерации.
Основные преимущества фильтра — возможность фильтрации и отжима осадка при давлении до 1,5 МПа и полная автоматизация процесса, позволяющая одному рабочему обслуживать до десяти фильтров. Горизонтальное расположение плит обеспечивает равномерность толщины слоя осадка и эффективную его промывку. Фильтр обладает развитой фильтрующей поверхностью при сравнительно небольшой занимаемой площади. Так, фильтр с поверхностью фильтрации 25 м2 занимает 8,6 м2 производственного помещения.
Разработаны и используются в промышленности автоматизированные камерные фильтр-прессы с вертикальным расположением плит. Примером является серия разработанных в СССР фильтров ФПАВ с поверхностями фильтрации от 50 до 600 м2, предназначенных для установок очистки сточных вод (для обезвоживания шлама отстойников).
Вопрос 9
Реакторы идеального вытеснения: определение времени реакции и объема трубчатого реактора для условий идеального вытеснения (реакции первого и второго порядков)
Трубчатые проточные реакторы, в отличие от кубовых, не имеют перемешивающих устройств, в них перемешивание среды в направлении ее течения сведено к минимуму. Приближенной теоретической моделью такого аппарата является реактор идеального вытеснения, в котором среда движется с постоянной скоростью подобно поршню. Вследствие отсутствия перемешивания и поступательного (поршневого) течения время пребывания различных частиц или элементарных объемов реакционной смеси в таком аппарате одинаково. Частицы, одновременно вошедшие в реактор, в любой момент времени находятся в каком-либо одном его попе речном сечении и, следовательно, одновременно его покинут. В отличие от кубового реактора концентрации веществ, участвующих в реакции, плавно меняются по длине аппарата. Ввиду отсутствия перемешивания среды в продольном направлении это изменение обусловлено только течением реакции. В таком аппарате не происходит разбавления поступающих в него исходных веществ продуктами реакции. Поэтому при одинаковых начальных и колеч-ных концентрациях средние значения концентраций реагирующих вещеотв и скорости реакции в таком реакторе больше, а время реакции и необходимый объем реактора меньше, чем в условиях идеального смешения.
Рис.2.1 Схема трубчатого реактора
Пусть на вход реактора идеального вытеснения, схема подается с объемной скоростью W раствор, содержащий два реагирующие между собой вещества и
. По-прежнему будем считать реакцию протекающей без изменения объема, а условия в аппарате - изотермическими. На расстоянии X от входа выделим элемент реактора бесконечно малой длины
. Пусть
- объем выделенного элемента,
и
-концентрации веществ
и
в сечении с координатой X ,
- изменение (прирост) концентрации
, a
-время нахождения реакционной смеси на рассматриваемом участке реактора. В пределах бесконечно малого объема d.V скорость реакции можно считать постоянной. Применив уравнение, справедливое при постоянной скорости реакции, к участку dX , получим время, в течение которого концентрация
уменьшивается на величину
(1)
Числитель правой части уравнения (1) представляет собой изменение концентрации вещества , а знаменатель - скорость реакции на участке dX .
Время реакции, соответствующее конечному изменению концентрации вещества , можно определить от
до
,можно определить интегрированием уравнения (1) :
(2)
Для решения задачи по уравнению (2) необходимо знать численные значения величин К, р и q, , а также перейти от двух независимых переменных к одной, использовав связывающее стихеометрическое уравнение реакции.
Реакция 1-го порядка. Приняв в уравнении (2) р=1 получим:
(3)
Модуль реакции:
(4)
Степень превращения, достигаемая в реакторе заданного объема, может быть найдена по уравнению (4), решенному относительно :
(5)
Реакция 2-го порядка, 1-го типа.Здесь р=2,q=0
(5)
Модуль реакции 2-го порядка, согласно уравнению (5), равен
(6)
Решив уравнение (6) относительно , получим
(7)
Сравнивая уравнение (1) с ранее приведенным уравнением, соответствующим периодическому процессу, нетрудно установить , что они по существу совпадают. Таким образом, течение реакции в аппарате периодического действия и в проточном реакторе идеального вытеснения описывается одним и тем же дифференциальным уравнением. Вследствие этого время реакции в аппарате периодического действия определяется так же, как в реакторе идеального вытеснения, т.е. по уравнению (2). Производительность обоих аппаратов при равных объемах и одинаковых степенях пре -вращения в них в случае мгновенной загрузки и выгрузки была бы одинакова, В действительности периодический реактор имеет несколько меньшую производительность, так как загрузка и выгрузка (вместе с разогревом аппарата и последующим охлаждением продуктов реакции) занимают определенную часть цикле его работа. Уравнения (3-7) также справедливы для периодического реактора.
Вопрос 16.
Роль теплообменной аппаратуры в химической , нефтехимической и нефтеперерабатывающей промышленности. Факторы, влияющие на выбор конструкции теплообменников. Классификация теплообменной аппаратуры.
Факторы, определяющие выбор теплообменников
Теплообменники характеризуются рядом показателей: особенностями конструкции, габаритами, массой, удобством обслуживания, условиями теплообмена, к. п. д., гидродинамическим совершенством, долговечностью, эстетикой, тепловой производительностью, температурными условиями процесса, физико-химическими свойствами теплоносителей, стабильностью процесса и др.
Конструктивные показатели
Выбор оптимальной конструкции теплообменника является задачей, разрешаемой технико-экономическим сравнением нескольких типоразмеров аппаратов применительно к заданным условиям или на основании критерия оптимизации.
На поверхность теплообмена и на относящуюся к ней долю капитальных затрат, а также на стоимость эксплуатации влияет недорекуперация теплоты. Чем меньше величина недорекуперации теплоты, т.е. чем меньше разность температур греющего теплоносителя на входе и нагреваемого теплоносителя на выходе при противотоке, тем больше поверхность теплообмена, тем выше стоимость аппарата, но тем меньше эксплуатационные расходы. Конечно, должен быть определенный оптимум увеличения капитальных и снижения эксплуатационных расходов, который можно определить графически. Известно также, что с увеличением числа и длины труб в пучке и уменьшением диаметра труб снижается относительная стоимость одного квадратного метра поверхности кожухотрубчатого теплообменника, так как при этом снижается общая затрата металла на аппарат в расчете на единицу поверхности теплообмена. Зависимость относительной стоимости теплообменника (на 1 м2) от общей поверхности теплообмена, диаметра и длины труб показана на рисунке:
Зависимость относительной стоимости теплообменника от общей поверхности, диаметра и длины труб. К – относительная стоимость 1 м2 поверхности нагрева; F, d, l – соответственно поверхность, диаметр и длина труб.
Следует иметь в виду, что с увеличением числа труб увеличивается вероятность нарушения плотности их крепления в трубной решетке, а с применением труб малого диаметра увеличивается их засоряемость и усложняется чистка.
При выборе типа теплообменника можно руководствоваться следующими рекомендациями.
1. При обмене теплотой двух жидкостей или двух газов целесообразно выбрать секционные (элементные) теплообменники; если из-за большой поверхности теплообменника конструкция получается громоздкой, можно принять к установке многоходовой кожухотрубчатый теплообменник.
2. При подогреве жидкости паром рекомендуются многоходовые по трубному пространству кожухотрубчатые аппараты с подачей пара в межтрубное пространство.
3. Для химически агрессивных сред и при небольших тепловых производительностях экономически целесообразны рубашечные, оросительные и погружные теплообменники.
4. Если условия теплообмена по обе стороны теплопередающей поверхности резко различны (газ и жидкость), должны быть рекомендованы трубчатые ребристые или плавниковые теплообменники.
5. Для передвижных и транспортных тепловых установок, авиационных двигателей и криогенных систем, где при высокой эффективности процесса необходимы компактность и малая масса, находят широкое применение пластинчатые ребристые и штампованные теплообменники.
6. Во всех случаях необходимо стремиться выбирать наиболее простые по конструкции и наиболее дешевые по материалам теплообменники. К усложненным аппаратам (с плавающей камерой, с сильфонным компенсатором, спиральным), а также с латунными или медными трубами следует прибегать лишь в случае обоснованной необходимости.
Теплообменные аппараты предназначены для проведения процессов теплообмена при необходимости нагревания или охлаждения технологической среды с целью ее обработки или утилизации теплоты.
Теплообменная аппаратура составляет весьма значительную часть технологического оборудования в химической и смежных отраслях промышленности. Удельный вес на предприятиях химической промышленности теплообменного оборудования составляет в среднем 15–18 %, в нефтехимической и нефтеперерабатывающей промышленностях 50 %. Значительный объем теплообменного оборудования на химических предприятиях объясняется тем, что почти все основные процессы химической технологии (выпаривание, ректификация, сушка и др.) связаны с необходимостью подвода или отвода теплоты.
Теплообменные аппараты можно классифицировать по следующим признакам:
по конструкции — аппараты, изготовленные из труб (кожухо-трубчатые, «труба в трубе», оросительные, погружные змеевико-вые, воздушного охлаждения); аппараты, поверхностность теплообмена которых изготовлена из листового материала (пластинчатые, спиральные, сотовые); аппараты с поверхностью теплообмена, изготовленной из неметаллических материалов (графита, пластмасс, стекла и др.);
по назначению — холодильники, подогреватели, испарители, конденсаторы;
по направлению движения теплоносителей — прямоточные, противоточные, перекрестного тока и др.
В общем выпуске теплообменных аппаратов для химической и смежных отраслей промышленности в России около 80 % занимают кожухотрубчатые теплообменники. Эти теплообменники достаточно просты в изготовлении и надежны в эксплуатации и в то же время достаточно универсальны, т. е. могут быть использованы для осуществления теплообмена между газами, парами, жидкостями в любом сочетании теплоносителей и в широком диапазоне их давлений и температур.
Теплообменники типа «труба в трубе» и змеевиковые стальные в общем объеме теплообменной аппаратуры составляют около 8 %, а оросительные из чугуна — около 2 %.
Доля спиральных и пластинчатых теплообменников и аппаратов воздушного охлаждения пока невелика, но на вновь строящихся технологических линиях аппараты этого типа занимают все большее место.
Условия проведения процессов теплообмена в промышленных аппаратах чрезвычайно разнообразны. Эти аппараты применяют для рабочих сред с различным агрегатным состоянием и структурой (газ, пар, капельная жидкость, эмульсия и др.) в широком диапазоне температур, давлений и физико-химических свойств. Из-за разнообразия предъявляемых к теплообменным аппаратам требований, связанных с условиями их эксплуатации, применяют аппараты самых различных конструкций и типов, причем для аппарата каждого типа разработан широкий размерный ряд поверхности теплообмена (от нескольких до нескольких тысяч квадратных метров в одном аппарате). В размерном ряду теплообменники различаются по допускаемым давлениям и температурам рабочей среды, а также по материалам, из которых изготовлен аппарат.
Широкая номенклатура теплообменников по типам, размерам, параметрам и материалам позволяет выбрать для конкретных условий теплообмена аппарат, оптимальный по размерам и материалам. Выбор конструкции аппарата для определенных условий теплообменного процесса зависит в основном от эрудиции и интуиции конструктора. Однако существуют рекомендации общего характера, которыми можно руководствоваться при выборе конструкции теплообменника и схемы движения в нем теплоносителей:
при высоком давлении теплоносителей предпочтительнее трубчатые теплообменники; в этом случае в трубное пространство желательно направить теплоноситель с более высоким давлением, поскольку из-за малого диаметра трубы могут выдержать большее давление, чем корпус;
коррозионный теплоноситель в трубчатых теплообменниках целесообразно направлять по трубам, так как в этом случае при коррозионном изнашивании не требуется замена корпуса теплообменника;
при использовании коррозионных теплоносителей предпочтительнее теплообменные аппараты из полимерных материалов, например фторопласта и его сополимеров, обладающих уникальной коррозионной стойкостью;
если один из теплоносителей загрязнен или дает отложения, то целесообразно направлять его с той стороны теплообмена, которая более доступна для очистки (в змеевиковых теплообменниках — это наружная поверхность труб, в кожухотрубчатых — внутренняя);
для улучшения теплообмена не всегда требуется увеличение скорости теплоносителя (так, например, при конденсации паров для улучшения теплообмена необходимо обеспечить хороший отвод конденсата с теплообменной поверхности, для чего следует подобрать аппарат соответствующей конструкции).
Вопрос 19
Дата добавления: 2018-02-28; просмотров: 654; Мы поможем в написании вашей работы! |
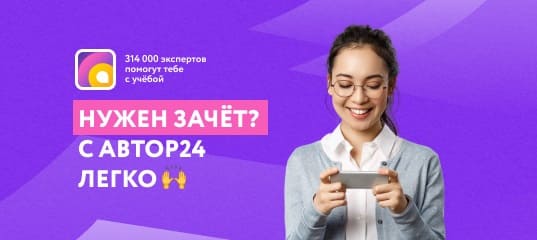
Мы поможем в написании ваших работ!