Система технического обслуживания и ремонта оборудования
Различают три формы организации ремонта: централизованную, децентрализованную и смешанную. При централизованной форме все виды ремонта и технического обслуживания производит ремонтно-механический цех предприятия. При децентрализованной форме ремонт и техническое обслуживание оборудования производится силами цеховых ремонтных баз. Здесь же изготавливают новые и восстанавливают изношенные детали и узлы. При смешанной форме организации ремонта трудоемкие работы, такие, как капитальный ремонт и модернизация оборудования, изготовление запасных частей и восстановление изношенных деталей и узлов, производятся в ремонтно-механическом цехе предприятия, а техническое обслуживание и текущий ремонт оборудования осуществляется в цеховых ремонтных базах. Такой ремонт и обслуживание обычно выполняется комплексными бригадами слесарей, закрепленных за отдельными участками. В практике работы предприятий чаще всего применяются три метода организации ремонта. 1. Ремонт по потребности, т. е. по мере остановки станка. Это может вызвать срыв выполнения планового задания, брак продукции и т. д. Увеличиваются время и затраты на ремонт оборудования в связи с износом сопряженных деталей. При этом методе работу ремонтно-механического цеха невозможно планировать. 2. Метод по дефектным ведомостям, выполняется осмотр оборудования и составляется дефектная ведомость, в которой отражается, что и когда надо ремонтировать. Заранее служба главного механика здесь также не может планировать ремонтные работы. 3. Третий метод организации ремонтного хозяйства базируется на системах планово-предупредительного ремонта (ППР) и технического обслуживания и ремонта (ТОР). Они представляют собой совокупность организационно-технических мероприятий по уходу, надзору, обслуживанию и ремонту оборудования, по заранее составленному плану. В основе этих систем лежат принципы плановости и профилактики. Цель этого метода — предупредить остановку оборудования из-за возможных отказов и аварий. Эти системы включают в себя:
|
|
Г) уход за оборудованием основными рабочими в начале и в конце смены, что повышает их ответственность за состояние оборудования. Кроме того, за состоянием оборудования повседневно наблюдают дежурные слесари, электрики, смазчики, устраняющие возникшие мелкие неисправности; 2) техническое обслуживание, включающее комплекс операций по поддержанию работоспособности оборудования: осмотры выполняются
дежурными слесарями 1 -2 раза в месяц, промывки, проверки на точность, последние производятся наладчиком или слесарем совместно с представителем отдела технического контроля; 3) ремонты. Система ППР включает три вида ремонта: малый (М), средний (С) и капитальный (К). В основном она применяется для устаревшего оборудования. Для нового, дорогостоящего оборудования рекомендуется система ТОР, включающая два вида ремонта: текущий (Т) и капитальный (К). Основной же упор в ней сделан на техническое обслуживание оборудования.
|
|
Нормативы и планирование ремонта
1. Оценку сложности ремонта присвоение категории производят путем сопоставления трудоемкости ремонта данного оборудования и трудоемкости ремонта оборудования, принятого за единицу сравнения: машина-эталон. В качестве эталона выбран токарно-винторезный станок 1К62, которому присвоена 11 категория сложности ремонта.
2. Ремонтная еденица-условный показатель, характеризующий нормативные затраты времени на ремонт оборудования первой категории сложностию. За единицу сложности ремонта механической части оборудования принята ремонтная сложность условного оборудования, трудоемкость которого в условиях среднего ремонтного цеха составляет 50 часов. Единица ремонтной сложности экономической части 12,5 часа.
3. Таким образом общая трудоемкость ремонтных работ в плановом периоде может быть определена по следующей формуле:
|
|
где: - соответственно число капитальных, средних и текущих ремонтов и технического обслуживания.
- категория сложности ремонта i-го оборудования
- соответственно нормы трудоемкости капитального, среднего и текущего ремонта, а также технического обслуживания на одну ремонтную единицу. Трудоемкость определяется раздельно по механической и электрической части оборудования.
4. 4. Ремонтный цикл — это промежуток времени от ввода оборудования в эксплуатацию до капитального ремонта или между двумя капитальными ремонтами. Он измеряется оперативным временем работы оборудования. Время простоя в ремонте в цикл не включается. Ремонтный цикл Т ц определяется по формуле
А- исходная нормативная продолжительность ремнтного цикла, 16800 ч
- коэффициент, учитывающий обрабатываемый материал.
- коэффициент, учитывающий применяемый инструмент
- коэффициент, учитывающий точность обработки
- коэффициент, учитывающий возраст оборудования.
- коэффициент, учитывающий долговечность оборудования.
- коэффициент, учитывающий категорию массы оборудования.
5. Межремонтный период Гм — это время (в месяцах) между двумя очередными ремонтами, определяемое по формуле
|
|
Межремонтным периодам- называют промежуток времени работы оборудования м/у двумя очередными видами плановых ремонтов:
6. Длительность межосмотрового периода - это промежуток времени м/у ремонтом и техническим обслуживанием:
где: - число средних и текущих ремонтов, а также технологического обслуживания в ремонтном цикле.
7. Число обслуживающего персонала для проведения технического обслуживания определяют по следующей формуле:
число типоразмеров оборудования
N - число однотипного оборудования.
- коэффициент смежности работы оборудования.
- норма обслуживания на одного рабочего в единицах сложности ремонта.
Дата добавления: 2015-12-21; просмотров: 24; Мы поможем в написании вашей работы! |
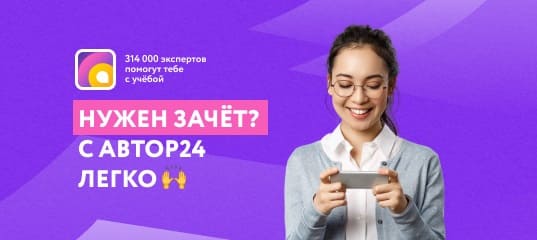
Мы поможем в написании ваших работ!