Дефекты и неполадки при экструзии и последующей фиксации формы изделия охлаждением
Заключительной стадией формования изделий из экструзионной заготовки является его деформирование в калибраторе либо (при отсутствии последнего) промежуточное или окончательное охлаждение до твердого состояния. Процессы, происходящие на этой стадии, в значительной степени влияют на качество изделий и образование скрытых и явных дефектов.
При получении рукавных, тонких плоских пленок, объемных изделий методом выдува в замкнутой форме этап калибрования отсутствует.
При получении рукавных пленок экструзионная заготовка деформируется вдоль и поперек движения экструдата в потоке воздуха из обдувочного кольца. Даже если после формующей щели была получена качественная заготовка, готовая пленка может иметь разнотолщинность из-за неравномерности обдува, а несбалансированность в соотношении степени выдува и вытяжки приводит к разрывам, разнотолщинности, повышенной термоусадке, пониженному блеску и т.п. Поэтому процессы окончательного формования пленки после стадии экструзии значительно влияют на дефектность изделий.
Таблица 3
Виды дефектов полимерных пленок, получаемых экструзией с раздувом
Дефект | Причины дефекта | Способ устранения |
Гели (вкрапления, цвета пленки, создающие оптические искажения) | Неоднородность полимера по молекулярной массе | Замена партии ПМ |
Перегрев или недогрев зоны головки цилиндра | Изменение температурного режима | |
Плохая гомогенизация расплава | Увеличить давление | |
Пробивка сеток | Замена сеток | |
Загрязнение головки экструдера | Очистка головки экструдера | |
«Апельсиновая корка» | Перегрев расплава около витков шнека | - Увеличение интенсивности охлаждения шнека; - Уменьшение частоты вращения шнека; |
Полосы на пленке | Наросты на поверхности головки | Очистка регулирующего зазора и поверхности головки |
Наплывы, сминание рукава после приемных валков | Перегрев ПМ | - Снижение температуру цилиндра и головки; - Уменьшение скорость экструзии; - Увеличение интенсивности охлаждения рукава; |
Ассиметричностьраздутого рукава, утолщения на рулоне | Неравномерный выход расплава из зазора | Калибровка формовочного зазора фильеры |
Сквозняки в цехе | Устранение | |
Неравномерный обдув | Устранение | |
Нестабильность расплава | Пульсация из-за «козла» в воронке | Очистка загрузочной зоны |
Высокая температура в первой зоне цилиндра | Регулировка температуры | |
Неравномерность подачи воздуха в рукав | Устранение неравномерности подачи | |
Пузырьки наповерхности рукава | ПМ имеет повышенную влажность | Высушивание ПМ |
Обрыв рукава | Нарушение условий формирования пленки | Увеличение ширины рукава или толщину пленки |
Перегрев расплава, высокая «линия кристаллизации» | Снижение температуры или скорости экструзии, увеличение интенсивности охлаждения рукава | |
Низкие физико-механические показатели | ПМ не соответствует ГОСТу | Замена материала |
Нарушение режимов формования | Регулировка режимя | |
Низкая степень ориентации | Регулировка валиков, устранение перекоса | |
Складки на пленке | Большая разнотолщинность | Регулировка толщины формующей щели |
Перекос приемных и намоточных устройств | Регулировка валиков, устранение перекоса | |
Горячие складки на пленке | Центр зазора приемных валков не соответствует диаметру рукава | Регулировка положения приемных валков |
Угол зазора щек не соответствует диаметру рукава | Установить соответствие диаметров | |
Слишком высокая температура расплава | Уменьшение температуры экструзии, увеличение температуры охлаждения | |
Большая термическая усадка готовой пленки | Большая степень ориентации вдоль и/или поперек пленки | Уменьшение деформации раздува и/или вытяжки; увеличение время охлаждения до «линии кристаллизации» |
|
|
|
|
Таблица 4
Виды дефектов плоской экструзионной пленки
|
|
Дефект | Причины дефекта | Способ устранения |
Гели | Низкая температура экструзии (непроплавы) | Увеличение температуры цилиндра и головки |
Плохая гомогенизация расплава | Уменьшение частоты вращения шнека | |
Забивка фильтрующих сеток | Замена сеток, увеличение количества сеток | |
Некачественный ПМ | Замена ПМ | |
Неоднородная, местами матовая поверхность | Периодическое прилипание-отлипание пленки к охлаждающему приемному барабану | Уменьшение температуры барабана |
Проскальзывание пленки по поверхности барабана | Проверка работы электроприжима пленки | |
Разнотолщинность | Не отрегулирован щелевой зазор экструзионной головки | Добиться постоянного зазора по ширине |
Неравномерная скорость экструзии | Устранение пульсации расплава | |
Хрупкость | Перегрев расплава | Уменьшение температуры экструзии |
Кристаллизация на барабане | Уменьшение температуры барабана | |
Сквозные отверстия в пленке | Повышенная влажность ПМ | Высушивание ПМ |
Задиры, царапины | Негладкая поверхность охлаждающего барабана | Очистка и полировка поверхность |
Повреждена поверхность валов агрегата для вытяжки пленки по длине | Очистка и полировка поверхности |
|
|
Вывод:
Для переработчиков и конечных потребителей полимерных пленок важны такие показатели качества, как прочность, жесткость, способность противостоять проколу и раздиру, прозрачность, плоскостность, блеск, равномерность окраса, свариваемость. Кроме того, переработчики контролируют и качество рулонов пленки, оцениваемое по геометрическим характеристикам рулона и плотности намотки. Повышенное качество рулонов и собственно пленки позволяет при ее переработке в упаковку использовать производительное, имеющее рабочие скорости до 500 м/мин оборудование для нанесения печати и ламинирования, получать прочные и равномерные сварные швы на скоростных пакетосварочных машинах, облегчать упаковывание продукции в стретч- и термоусадочную пленки, применять скоростное групповое упаковывание.
Перечисленные контролируемые параметры говорят о том, что без эффективной системы контроля качества, охватывающей весь процесс переработки исходного сырья в конечную продукцию, невозможно представить эффективный пленочный бизнес.
Для оценки качества проводятся лабораторные и производственные испытания исходного сырья и образцов конечной продукции. В некоторых случаях проводятся математическая обработка и анализ собранных данных, что позволяет подобрать необходимые модифицирующие добавки, провести коррекцию режимов переработки, определить источники проблем и найти способы снижения затрат.
Одним из важнейших показателей, определяющих пригодность полимерной пленки к использованию по назначению, является ее толщина, от которой зависят многие другие эксплуатационные свойства пленки. В процессе производства толщина пленки всегда имеет некоторые отклонения от номинала (разнотолщинность). Ее допустимое значение, согласно все еще действующему в России ГОСТ 10354-82, составляет 20 %, а допуск на толщину – соответственно ± 20 %.
За тридцать лет, прошедших с момента появления ГОСТа, накоплен большой новый опыт производства и переработки пленок. Появились принципиально новые виды пленок и пленкообразующих видов полимеров. Требования потребителей и переработчиков к стабильности толщины полимерных пленок стали гораздо жестче условий, определенных ГОСТом. Более того, практика показывает, что простого нормирования минимального и максимального значений сегодня уже недостаточно.
Если толщина пленки становится меньше допустимой, то возрастает вероятность разрыва пленочного полотна в процессе его получения, что связано с дополнительными затратами на остановку процесса и потерями ПМ. Однако значительно худшие последствия влечет за собой несвоевременное обнаружение недопустимых отклонений толщины. Чтобы избежать потери репутации как поставщика стабильно качественной продукции, производители пленки зачастую завышают ее номинальную толщину, что позволяет решить вопрос обеспечения прочности упаковки. Однако при этом возрастает расход ПМ и соответственно повышается себестоимость полимерной пленки.
Вместе с тем увеличение средней толщины не всегда способно решить проблему качества пленки. Ключевую роль для стабильной работы оборудования часто играет разнотолщинность пленки. Так, пленка с повышенным разбросом толщины становится непригодной для ламинирования, а также для получения качественных сварных швов. Для переработки пленки на скоростных флексографских машинах допуск по толщине составляет ± 3-4 %. Допуск по толщине термоусадочных пленок составляет ± 4-6 %, а, например, пищевики потребляют пленку с разнотолщинностью ± 5-6 %. Особенно высокие требования предъявляются к пленкам для ламинирования, разброс толщин у которых должен приближаться к ± 2 %.
С точки зрения экономии сырья разницы между продольной и поперечной разнотолщинностью нет. Однако на скорость и качество таких процессов как, нанесение рисунка, сварка и ламинирование, обычно сильнее влияет поперечная разнотолщинность пленочного полотна.
В среднем увеличение расхода ПМ на разнотолщинность может составлять 20 %. Но на производство «лишних» микрометров толщины пленки тратится не только сырье, но и другие ресурсы предприятия, связанные с перерасходом сырья и электроэнергии, с дополнительными расходами на заработную плату и амортизацию оборудования.
При оформлении технического регламента технологического процесса в соответствующем разделе данные по наиболее типичным и часто встречающимся видам дефектов, причинам и способам их устранения, накопленные в процессе отработки стабильного технологического процесса производства изделий, оформляются в виде таблицы. При этом, чем меньше порядковый номер дефекта, тем чаще он может встречаться при производстве изделий. И наоборот: чем больше порядковый номер дефекта, тем менее вероятно его появление.
Следует отметить, что при отработанном устойчивом процессе производства такие показатели свойств, как механические или химические, либо занимают последние строки таблицы, либо вообще отсутствуют в виде дефекта. Это связано с тем, что при отрегулированном процессе при хорошем качестве исходного полимерного материала, эти свойства изделия соответствуют требованиям ТУ, согласованных с заказчиком данного изделия. В этом случае на первый план выходят такие дефекты, как недостатки внешнего вида, посторонние включения и т.п.
Приведенные в табл. 1, 2, 3 и 4 данные о возможных причинах дефектов и способах их устранения являются необходимой составной частью системы мероприятий по обеспечению качества продукции на современном производстве. Прогрессивные системы регулирования технологических процессов позволяют не просто фиксировать появление дефектов (пассивный контроль качества), а выявлять тенденции их возможного возникновения и своевременно предупреждать появление брака (активный контроль качества).
Список литературы:
1) М. Бихлер. Дефекты литьевых деталей и способы их устранения. Полимерные материалы №10 (101) октябрь 2007, стр.42-45
2) С.В. Власов, Е.А. Щербакова. Виды дефектов литьевых изделий из термопластов, причины их возникновения и способы устранения. Полимерные материалы №9 (112) сентябрь 2008, стр.26-29
3) Устраняем дефекты при литье полистирол. Пластикс №7 (113) 2012, стр. 22-25
4) С.В. Власов, Е.А. Щербакова. Виды дефектов экструзионных изделий из термопластов, причины и способы устранения. Полимерные материалы №4-5 (131-132) апрель-май 2010, стр.47-54
5) А.Р. Смышляев, Б.В. Бердышев. Коррекция толщины полимерных пленок в процессе их изготовления. Полимерные материалы №11 (102) ноябрь 2007, стр.6-11
6) М.Бихлер. Детали из пластмасс - отливать без дефектов. - Швайг, 1999, 95 стр.
Дата добавления: 2015-12-21; просмотров: 29; Мы поможем в написании вашей работы! |
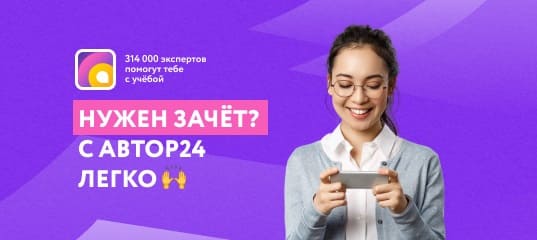
Мы поможем в написании ваших работ!