Валковые (валково-дисковые) грохоты
Валковые грохоты (рис. 1.10) состоят из ряда параллельных валков, установленных на наклонной раме и вращаемых в направлении движения материала. На валки насажены или отлиты вместе с ними диски различной конфигурации. Валки с дисками образуют просеивающую поверхность с отверстиями, форма и размеры которых определяются расстояниями между валками и формой дисков.
Рис. 1.10. Схема работы и конструкция валкового
(валково-дискового) грохота
Число валков для разных конструкций грохотов составляет от 5 до 13, а для грохочения мелкого материала и больше. Размеры отверстий валковых грохотов – от 5 до 175 мм. Рама грохота устанавливается под углом 12–15о.
Производительность валковых грохотов по исходному материалу принимается около 1 м3/ч на 1 м2 и 1 мм ширины отверстия. Например, при размере отверстия 75мм – 75 м3/(м2ч).
Достоинствами валковых грохотов являются самоочищаемость вращающихся поверхностей, возможность рыхления исходного материала, не боятся перегрузки, бесшумность работы; недостатками – большая металлоемкость и сложность привода.
Барабанные грохоты
Барабанные грохоты (рис. 1.11) имеют цилиндрическую или коническую просеивающую поверхность из перфорированных стальных листов или сетки. Ось цилиндрического барабана наклонена к горизонту под углом 4–14о, ось конического – горизонтальна. Исходный материал крупностью до 300–500 мм подается внутрь вращающегося барабана.
|
|
Рис. 1.11. Схема работы (а) и конструкция трехсекционного цилиндрического
барабанного грохота (б): d 3 > d 2 > d 1.
Движение материала в барабанном грохоте схематически показано на рис. 1.11. а. Материал под действием силы трения увлекается внутренней поверхностью вращающегося барабана и затем под действием силы тяжести скатывается вниз. Вследствие наклона оси барабана α скатывание материала происходит под некоторым углом к плоскости вращения. Поэтому материал несколько продвигается вниз вдоль оси барабана со средней скоростью V ср. Далее цикл повторяется и материал движется по зигзагообразной линии.
Если материал необходимо рассеять на несколько классов крупности, барабан по длине собирается из ряда секций с разными отверстиями, увеличивающимися к разгрузочному концу. Сита могут собираться с концентрическими просеивающими поверхностями: внутренние – с наибольшими, а наружные – с наименьшими отверстиями. Применяют также комбинированные конструкции, в которых на барабане, состоящем из нескольких секций сит с отверстиями, увеличивающимися в размерах, устанавливается концентрически еще одно или несколько сит с мелкой сеткой.
|
|
Диаметр барабана колеблется от 500 до 3000 мм, длина от 2000 до 900 мм; длина отдельной секции барабана – от 800 до 1500 мм. По практическим данным, средняя производительность барабанного грохота на 1 м2 площади сита и на 1 мм размера отверстий составляет 0,25–0,30 т/ч при сухом грохочении, при мокром – около 0,45 т/ч.
Частота вращения барабана ограничивается определенным пределом, так как при больших частотах возникающая центробежная сила прижимает материал к рабочей поверхности и грохочение становится невозможным. Частота вращения, при которой слой материала, прилегающий к поверхности барабана, начинает вращаться вместе с барабаном, называется критической. Критическая частота вращения барабанного грохота
(1.12)
где R – радиус барабана, м.
Барабанные грохоты находят применение для грохочения и промывки различных материалов, россыпных руд, для сортировки флотационного концентрата.
Достоинствами барабанных грохотов являются: простота конструкции, бесшумная работа, простота обслуживания и надежность в работе, а также возможность мокрого грохочения сильно-глинистых материалов. К недостаткам следует отнести низкую удельную производительность и относительно невысокую эффективность грохочения.
Дата добавления: 2015-12-19; просмотров: 17; Мы поможем в написании вашей работы! |
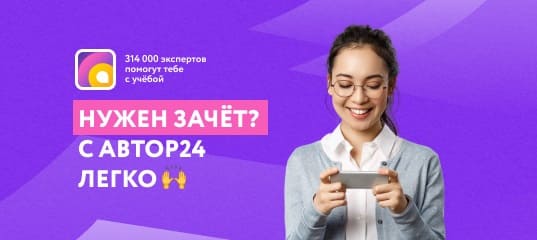
Мы поможем в написании ваших работ!