ОПЕРАЦИОННЫХ ТОКАРНЫХ СТАНКАХ
Министерство промышленности и торговли Тверской области
Государственное Бюджетное профессиональное
Образовательное учреждение
«БЕЖЕЦКИЙ ПРОМЫШЛЕННО-ЭКОНОМИЧЕСКИЙ колледж»
РАСЧЕТ НОРМ ВРЕМЕНИ ПРИ ТОКАРНОЙ ОБРАБОТКЕ
Методические указания
по выполнению расчета норм времени при токарной обработке
по предмету ОПД 09 «Технология машиностроения»
для специальности 15.02.08 «Технология машиностроения»
Бежецк 2022
Рассмотрены и утверждены
На заседании методической комиссии
специальностей технического профиля
Протокол № _____ от «____» ______________ 2022 г.
Председатель комиссии _______________Н.В. Абрамова
Составлено в соответствии с рабочей программой по дисциплине: «Технология машиностроения»
по специальности: 15.02.08 «Технология машиностроения»
____________________А.Ю. Судариков
Практическая работа № 8
Цель: 1. Закрепление теоретических знаний структуры основного и вспомогательного времени.
2. Формирование умения расчета норм времени на токарную обработку.
Характер занятия: частично – поисковый.
Форма организации занятия: индивидуальная.
Обеспечение занятия: справочная литература, ручка шариковая, карандаш, линейка, бумага формата А4.
Требования к знаниям и умениям
Перед выполнением практического занятия студент должен
|
|
знать:
- структуру оперативного времени,
- элементы основного и вспомогательного времени при точении,
- порядок расчета норм времени при точении;
после выполнения практического занятия студент должен
уметь:
- определить основное и вспомогательное время для заданных условий обработки,
- выбирать табличные значения элементов режима резания по справочным данным.
Задание
Последняя цифра варианта | Рассчитываемая поверхность | ||||||||
Номер вари анта | Размеры детали, мм | ||||||||
D1 | D2 | d1 | d2 | L | L1 | L2 | Номер | шерохо ватость Ra | |
1 | 100 | 70 | 80 | 40 | 150 | 80 | 70 | 1, 2 | 5 |
2 | 130 | 90 | 105 | 50 | 180 | 130 | 100 | 4, 6 | 5 |
3 | 150 | 100 | 120 | 60 | 200 | 150 | 120 | 1, 3 | 10 |
4 | 150 | 120 | 120 | 90 | 150 | 110 | 60 | 5, 6 | 10 |
5 | 80 | 50 | 60 | 30 | 200 | 150 | 120 | 1, 2 | 2,5 |
6 | 200 | 140 | 160 | 100 | 200 | 150 | 120 | 4, 6 | 2,5 |
7 | 200 | 120 | 150 | 70 | 160 | 100 | 70 | 1.3 | 5 |
8 | 130 | 80 | 100 | 50 | 160 | 100 | 70 | 5, 6 | 5 |
9 | 130 | 80 | 100 | 50 | 200 | 150 | 120 | 4, 6 | 5 |
10 | 90 | 70 | 80 | 40 | 200 | 150 | 70 | 1, 2 | 5 |
Первая цифра варианта | Предел прочности при растяжении, Н/мм2 | ||||||
Номер вариан та | Заготовка | ||||||
Метод получения | Марка материала | Припуски | |||||
Диаметр | Длина | ||||||
1 | Штам
повка | Сталь 45 | 10 | 5 | 610 | ||
2 | Сталь 40Х | 15 | 6 | 1000 | |||
3 | Сталь 20 | 10 | 4 | 420 | |||
4 | Ст20Х | 15 | 5 | 800 | |||
5 | Сталь 35Х | 20 | 6 | 930 | |||
6 | отливка | 45Л | 15 | 10 | 540 | ||
7 | 25Л | 20 | 8 | 440 | |||
8 | СЧ15 | 20 | 12 | 150 | |||
9 | СЧ25 | 25 | 8 | 250 | |||
10 | АЛ9 | 10 | 10 | 200 |
Последовательность обработки втулки:
Установ 1. Подрезка торца 1. Точить наружный диаметр 2 на проход. Расточить отверстие 3 на глубину L2. | Установ 2. Подрезать торец 6. Точить наружный диаметр 4, выдержав размер L1. Расточить отверстие 5 на глубину (L-L1) |
Станок - токарно-винторезный мод. 16К20.
Приспособление - самоцентрирующий трёхкулачковый патрон.
Размер партии n = 100 штук.
Припуски на обработку:
для поверхности 1 - 10 мм;
для поверхности 2 и 3 - 10 мм.
Точность обработки D1- h8; D2-h9; d1- H8; d2-H8;линейные размеры по IT11/2.
Количество переходов:
- подрезание торца 1 - заданную шероховатость можно достичь черновым и чистовым подрезанием.
- обработка наружной поверхности 2 - заданную поверхность можно достичь черновым и чистовым точением.
- расточка отверстия 3 - заданную поверхность можно достичь черновым и чистовым растачиванием.
Содержание операции:
- Установка 1. Установить и снять деталь.
- Переход 1. Подрезать торец начерно и начисто.
|
|
- Переход 2. Точить наружную поверхность 2 начерно и начисто.
- Переход 3. Расточить отверстие 3 в упор начерно и начисто.
- Установка 2. Переустановить деталь.
- Переход 4. Подрезать торец 6 начерно и начисто.
- Переход 5. Точить наружную поверхность 4 начерно и начисто.
- Переход 6. Расточить отверстие 5 на проход начерно и начисто.
1. Выбрать режущий инструмент для токарной обработки.
2. Рассчитать режим резания точения
3. Определить машинное время точения.
4. Определить основное и вспомогательное время.
5. Определить штучное время для заданных условий обработки.
Номер задачи и варианта – по указанию преподавателя.
Порядок выбора режима резания
ОДНОИНСТРУМЕНТНАЯ ОБРАБОТКА НА
ОПЕРАЦИОННЫХ ТОКАРНЫХ СТАНКАХ
№ этапа | Последовательность определения режима резания | Расчетная формула и нормативы | Исходные данные | ||
1 | Определить тип инструмента резания по назначению для заданного вида токарной обработки, выбрать марку твердого сплава, геометрические параметры (углы заточки) и размеры резца | Вид обрабатываемого материала; Размер резцедержателя станка; Конструкция детали; Вид обработки (черновая, получистовая, чистовая) | |||
2 | Определить глубину резания | ![]() | D – диаметр заготовки, мм; d – диаметр обработанной поверхности, мм | ||
3 | Расчет длины рабочего хода суппорта Lp х. в мм | ![]() | 1. Длинна резания Lpез. 2. Подвод, врезание и перебег y 3. Дополнительная длина хода, вызванная в отдельных случаях особенностями наладки и конфигурацией дета- лей Lдоп. | ||
4 | Назначение подачи суппорта на оборот шпинделя S0 в мм/об: а) определение рекомендуемой подачи по нормативам; б) уточнение подачи по паспорту станка | См. таб. 2,3,4 | 1.Обрабатываемый металл; 2.Вид инструмента; 3. Глубина (ширина)-резания t (b); 4. Жесткость системы; 5.Точность обработки; 6. Чистота поверхности; | ||
5 | Определение стойкости инструмента по Нормативам Т р в мин | См. таб.5 | Коэффициент времени резания λ
![]() ![]() | ||
6
| Расчет скорости резания v в м/мин и числа оборотов шпинделя n в минуту: | 1. Вид инструмента и инструментальный материал; 2. Обрабатываемый металл и его твердость 3. Глубина резания t 4. Подача s0; 5. Угол в плане (в рабочем положении инструмента) φ 6. Принятая стойкость инструмента Тр; | |||
а) определение рекомендуемой скорости резания по нормативам; | См. таб. 6,7,8,9,10,11, 12,13 | ||||
б) расчет рекомендуемого числа оборотов шпинделя станка; | ![]() | ||||
в) уточнение числа оборотов шпинделя по паспорту станка; | |||||
г) уточнение скорости резания по принятому числу оборотов шпинделя | ![]() | ||||
7 | Расчет основного машинного времени обработки tм в мин (при работе с различными подачами машинное время суммируется по участкам | ![]() | 1. Длина рабочего хода суппорта Lp х 2. Принятые подача Sо и число оборотов шпинделя n | ||
8 | Расчет силы резания Рz | См. таб. | 1. Глубина резания t 2. Подача s0; 3. Инструментальный материал; 4. Обрабатываемый металл | ||
9 | Расчет мощности резания N | ![]() | 1. Сила резания Рz; 2. Скорость резания V | ||
10 | Проверяем мощность резания по паспорту станка |
Таблица 1
Таблица 2
Рекомендуемые подачи на оборот шпинделя s0
Точение стальных и чугунных деталей
Обрабатываемый металл | s0 суппорта в мм/об при суммарной глубине , | ||||
До 3 | 5 | 10 | 20 | 40 | |
Сталь ........ Чугун........ | 0,6 0,8 | 0,4 0,6 | 0,3 0,45 | 0,25 0,35 | 0,2 0,25 |
Примечания: 1. В случае жесткой системы станок—деталь- приспособление— инструмент подачи можно увеличивать до 1,5 раза, а при нежесткой системе (например, валиков небольшого диаметра и большой длины, при расточке на тонких скалках и др.) можно уменьшать.
2. При обработке жестких деталей на одношпиндельных станках при простых наладках и небольшом припуске можно назначать подачи до 1,0 —1,5 мм/об, применяя резцы с дополнительной режущей кромкой (φ1 = 0°).
3. Обточку конусов и фасонных поверхностей по копиру с дополнительных суппортов производить с подачами 0,3 —0,4 мм/об при глубине резания до 2 мм и подачами 0,2 —0,3 мм/об при больших глубинах резания.
4. При высокой точности деталей, обрабатываемых на многорезцовых станках, подачу принимать равной 0,2 —0,3 мм/об.
5. При повышенных требованиях к чистоте обработанной поверхности не рекомендуется превышать указанные ниже значения подач:
Обрабаты ваемый металл | Скорость резания v в м/мин | Шероховатость Ra | ||||||
6.3 | 3.2 | 1.6 | ||||||
s0 в мм/об при радиусе при вершине резца г в мм | ||||||||
1,5—2 | 0,5 | 1 | 2 | 1 | 2 | |||
Сталь | 30-50 50 — 80 80 — 100 Более 100 | 0,45 0,55 0,6 0,65 | 0,15 0,3 0,35 0,4 | 0,2 0,35 0,4 0,45 | 0,25 0,4 0,45 0,5 | 0,12 0,15 0,2 | 0,15 0,2 0,25 | |
Чугун | Весь диапазон | 0,5 - 0,7 | - | 0,35 | 0,45 | 0,15 | 0,25 | |
В таблице указаны подачи при обработке сталей с σв = 70-90 кг/мм2. Если σв = 50-70 кг/мм2, то табличные значения следует умножать на 0,75, а при σв = 90-110 кг/мм2 на 1,25.
Для прорезных, широких (лопаточных), фасонных резцов и расточных головок с плавающими ножами подачи принимать по таблице 2:
таблица 3
Резец |
| Расточная головка с плавающими ножами | ||||||||
прорезной | фасонный * | широкий * |
| |||||||
Обрабатываемый металл | Канавки шириной до 20 мм |
| Цилиндрические и конические поверхности | Отверстия | ||||||
неглубокие | глубокие и точные | сложный | простой | |||||||
Сталь ..... | 0,2 | 0,08 | 0,08 | 0,15 | 0,12 | 0,4-0,5 | ||||
Чугун........ | 0,3 | 0,15 | 0,12 | 0,25 | 0,20 | 0,6-0,9 | ||||
* В конце рабочего хода подачу рекомендуется уменьшать до 0,02 -0,03 мм/об и пять-шесть оборотов производить зачистку профиля за без подачи. | ||||||||||
Точение деталей из алюминиевых сплавов
Таблица 4
Обрабатываемый материал | Черновая обработка | Чистовая обработка | |||
Обточка | Расточка | Обточка | Расточка | φ1 = 0° | |
Силумин . . . Дюралюминий | 0,7-1,0 | 0,6 —0,8 | 0,2 —0,3 0,15 — 0,25 | 0,1-0,2 0,1— 0,15 | 0,5—0,8 0,6 —1,0 |
Примечания: 1. При прорезке точных канавок подачу принимать равной 0,05—0,08 мм/об.
2. При чистовом точении силумина скорости резания принимать не ниже 100 м/мин, дюралюминия закаленного — 60 м/мин.
Определение стойкости инструмента
Таблица 5
No по пор. | Рекомендуемые значения Тм при числе инструментов в наладке | |||||||||
Группа наладки | Характеристика | 1 | 3 | 5 | 8 | 10 | 15 | 20 | более 20 | |
I | Наладки с равномерной загрузкой инструментов | Диаметры обтачиваемых поверхностей отличаются не более чем в 1,2 раза; количество фасочных и подрезных резцов не более 20% от общего количества инструментов наладки | 50 | 150 | 200 | 300 | 350 | 400 | ||
II | Среднее наладки по равномерности загрузки инструментов | Все наладки, не относящиеся к I и III группам | 100 | 140 | 200 | 230 | 260 | 300 | 350 | |
III | Наладки с большой разницей в загрузке инструментов | Диаметры обтачиваемых поверхностей отличаются более чем в 2 раза; количество фасочных и других мало- нагруженных инструментов свыше 50% от общего количества инструментов наладки | 70 | 90 | 110 | 130 | 150 | 170 | 180 |
Скорость резания.
V == VтабК1К2К3 м/мин,
где К1 — коэффициент, зависящий от обрабатываемого материала; К2 — от стойкости и марки твердого сплава; К3 — от вида обработки.
Vтаб. определяют по таблице 6
СКОРОСТЬ РЕЗАНИЯ Vта6л
Точение проходными, подрезными и расточными резцами
Таблица 6
| s0 в мм/об
| Обрабатываемый материал | ||||||||||||||||||||||||||||||||||||||
Сталь | Чугун серый | Чугун ковкий и прочный | Алюминиевые сплавы | |||||||||||||||||||||||||||||||||||||
t | Материал инструмента | |||||||||||||||||||||||||||||||||||||||
в мм | Быстрорежущая сталь |
|
|
|
|
|
|
| ||||||||||||||||||||||||||||||||
|
|
|
| Твердый сплав | Быстрорежущая сталь |
| ||||||||||||||||||||||||||||||||||
|
|
|
|
|
|
|
| |||||||||||||||||||||||||||||||||
Vтабл в м!мин при угле в плане φ в град | ||||||||||||||||||||||||||||||||||||||||
45 | 60 | 90 | 45 | 60 | 90 | 45 | 60 | 90 | 45 . | 60 | 90 | 45-90 | 45-90 | |||||||||||||||||||||||||||
До 0,2 | 57 | 57 | 57 | 160 | 160 | 160 | 105 | 105 | 105 | 120 | 120 | 120 | 530 | 225 | ||||||||||||||||||||||||||
0,3. | 48 | 48 | 48 | 150 | 150 | 150 | 100 | 100 | 100 | 115 | 115 | 115 | 460 | 190 | ||||||||||||||||||||||||||
0,4 | 42 | 42 | 42 | 135 | 135 | 135 | 93 | 93 | 93 | 110 | 110 | 110 | 400 | 170 | ||||||||||||||||||||||||||
До 1 | 0,5 | 40 | 40 | 40 | 130 | 130 | 130 | 88 | 88 | 88 | 105 | 105 | 105 | 360 | 155 | |||||||||||||||||||||||||
0,6 | 37 | 37 | 37 | 125 | 125 | 125 | 84 | 84 | 84 | 97 | 97 | 97 | 330 | 140 | ||||||||||||||||||||||||||
0,8 | 33 | 33 | 33 | 120 | 120 | 120 | 80 | 80 | 80 | 93 | 93 | 93 | 290 | 125 | ||||||||||||||||||||||||||
До 0,2 | 50 | 46 | 44 | 150 | 150 | 140 | 100 | 96 | 92 | 120 | 110 | 110 | 460 | 190 | ||||||||||||||||||||||||||
0,3 | 42 | 37 | 35 | 135 | 125 | 120 | 88 | 84 | 80 | 105 | 98 | 94 | 380 | 160 | ||||||||||||||||||||||||||
2,5 | 0,4 | 35 | 32 | 30 | 125 | 120 | 115 | 80 | 77 | 74 | 95 | 89 | 87 | 335 | 145 | |||||||||||||||||||||||||
0,5 | 32 | 28 | 27 | 115 | 110 | 105 | 75 | 72 | 70 | 89 | 84 | 82 | 300 | 130 | ||||||||||||||||||||||||||
0,6 | 30 | 26 | 25 | 110 | 105 | 100 | 72 | 68 | 65 | 85 | 79 | 77 | 270 | 115 | ||||||||||||||||||||||||||
0,8 | 26 | 23 | 22 | 100 | 95 | 93\ | 66 | 62 | 60 | 78 | 72 | 70 | 240 | 105 | ||||||||||||||||||||||||||
|
|
|
|
|
|
|
|
|
|
|
|
|
| |||||||||||||||||||||||||||
До 0,2 | 50 | 44 | 34 | 150 | 140 | 125 | 100 | 92 | 80 | 115 | 108 | 93 | 410 | 170 | ||||||||||||||||||||||||||
5 | 0,3 | 40 | 34 | 27 | 130 | 125 | 105 | 85 | 77 | 70 | 100 | 95 | 80 | 340 | 145 | |||||||||||||||||||||||||
| 0,4 | 33 | 30 | 24 | 120 | 115 | 95 | 77 | 70 | 63 | 90 | 85 | 74 | 305 | 125 | |||||||||||||||||||||||||
0,5 | 30 | 26 | 22 | 110 | 100 | 90 | 70 | 65 | 58 | 84 | 79 | 68 | 270 | 110 | ||||||||||||||||||||||||||
0,6 | 26 | 23 | 20 | 100 | 95 | 85 | 65 | 60 | 54 | 78 | 73 | 64 | 245 | 100 | ||||||||||||||||||||||||||
0,8 | 23 | 20 | 17 | 90 | 85 | 75 | 60 | 56 | 48 | 69 | 66 | 57 | 215 | 90 | ||||||||||||||||||||||||||
Точение твердосплавными резцами с дополнительной режущей кромкой (φ1 =00)
Таблица 7
s0 в мм/об | Обрабатываемый материал | |||||||||||||||
Сталь | Чугун серый | Чугун ковкий и прочный | Алюминиевые сплавы | |||||||||||||
Vтабл в м/мин | ||||||||||||||||
0,5 | 1 | 1,5 | 2 | 0,5 | 1 | 1,5 | 2 | 0,5 | 1 | 1,5 | 2 | 0,5 | 1 | 1,5 | 2 | |
1 | 136 | 113 | 110 | 100 | 84 | 74 | 68 | 65 | 105 | 90 | 84 | 77 | 315 | 260 | 240 | 225 |
1,5 | 120 | 103 | 94 | 86 | 77 | 67 | 57 | 54 | 93 | 80 | 72 | 67 | 260 | 220 | 195 | 185 |
2 | 113 | 94 | 86 | 80 | 74 | 62 | 56 | 52 | 90 | 73 | 67 | 62 | 230 | 195 | 175 | 160 |
Точение фасонными, прорезными, отрезными и широкими резцами
Таблица 8
Обрабатываемый материал | Резец | Vтабл в м/мин при s0 в мм/об | |||||||||||
Тип | Материал | 0,03 | 0,04 | 0,06 | 0,08 | 0,1 | 0,15 | 0,2 | 0,3 | 0,4 | 0,5 | ||
Сталь | фасонный | Быстрорежущая сталь | 53 | 50 | 42 | 35 | 32 | 27 | - | - | - | - | |
прорезной, отрезной широкий | - | - | 44 | 40 | 36 | 30 | 28 | 23 | 20 | 18 | |||
Твердый сплав | - | - | - | 110 | 100 | 85 | 77 | 65 | 57 | 52 | |||
Чугун | серый | - | - | - | 115 | 105 | 90 | 80 | 68 | 62 | 56 | ||
ковкий | - | - | - | 105 | 97 | 82 | 73 | 62 | 56 | 50 |
Примечания: Скорости резания для точения стали и ковкого чугуна даны с учетом применения эмульсии, для серых чугунов – без охлаждения. В случае охлаждения эмульсией при обработке чугунов скорости резания могут быть повышены на 15-20%. При скоростном точении стальных деталей эти же данные остаются неизменными и в случае работы без охлаждения.
КОЭФФИЦИЕНТЫ К1, К2, К3
Таблица 9
Таблица 10
Коэффициент К2 Проходные, подрезные, расточные и прорезные резцы
Обрабатываемый материал | Материал | К2 при стойкости Т р в минутах резания ' | ||||||||||
инструмента | до 30 | 60 | 100 | 200 | 300 | 400 | 600 | 800 | 1000 | 1500 | ||
Быстрорежущая сталь | 1,3 | 1,15 | 1,0 | 0,8 | 0,7 | 0,65 | 0,55 | 0,5 | 0,45 | 0,35 | ||
Сталь | Т15К.6 | 2,0 | 1,55 | 1,25 | 0,9 | 0,75 | ||||||
Т14К8 | 1,6 | 1,25 | 1,0 | 0,7 | 0,6 | |||||||
Т5КЮ | 1,25 | 1,0 | 0,8 | 0,55 | 0,5 | |||||||
Чугун серый | ВКЗМ, ВК2 | 1,6 | 1,4 | 1,2 | 0,95 | 0,85 | 0,7 | 0,6 | 0,55 | 0,5 | ||
ВК4, BIC6 | 1,35 | 1,15 | 1,0 | 0,8 | 0,7 | 0,6 | 0,5 | 0,45 | 0,4 | |||
ВК8 | 1,15 | 1,0 | 0,85 | 0,7 | 0,6 | 0,5 | 0,45 | 0,4 | 0,35 | |||
ВКЗМ, ВК2 | 2,1 | 1,75 | 1,45 | 1,1 | 0,9 | 0,8 | 0,65 | 0,5 | 0,45 | |||
Чугун ковкий и прочный | ВК4, ВК6 | 1,75 | 1,45 | 1,2 | 0,9 | 0,7 | 0,65 | 0,55 | 0,45 | 0,4 | ||
ВК8 | 1,45 | 1,2 | 1,0 | 0,75 | 0,6 | 0,55 | 0,45 | 0,35 | 0,3 | |||
Алюминиевые сплавы | Быстрорежущая сталь | 1,3 | 1,1 | 1,0 | 0,85 | 0,8 | ||||||
ВК4, ВК6 | 1,5 | 1,2 | 1,0 | 0,8 | 0,7 |
Фасонные резцы
Таблица 11
Тр | до 30 | 60 | 100 | 200 | 300 | 400 | Обрабатываемый материал – конструкционная сталь |
К2 | 1,4 | 1,15 | 0,85 | 0,8 | 0,75 |
Коэффициент К3
Таблица 12
Растачивание | Поперечное точение | |||||
d | >75 | <75 | ![]() | 0-0,4 | 0,5-0,7 | 0,8-1,0 |
К3 | 1,0 | 0,85 | К3 | 1,35 | 1,2 | 1,05 |
d1иd2- наибольший и наименьший диаметры обработки мм.
Фасонное точение
Таблица 13
Профиль резца | К3 при точении | |
предварительное | чистовое | |
простой | 1,0 | 0,8 |
Глубокий и сложный | 0,85 | 0,7 |
Дата добавления: 2022-07-02; просмотров: 43; Мы поможем в написании вашей работы! |
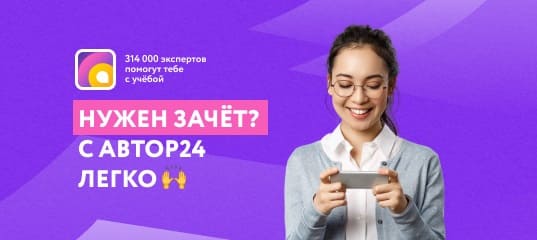
Мы поможем в написании ваших работ!