По организационным формам выявления и предупреждения брака:
Способы организации контроля. Особенности, результаты.
Тотальный контроль – 100% отслеживание брака на выходе изделия.
Он применяется в следующих случаях:
а) при ненадежности качества поставляемых материалов, полуфабрикатов, заготовок, деталей, сборочных единиц;
б) когда оборудование или особенности технологического процесса не обеспечивают однородность изготовляемых объектов;
в) при сборке в случае отсутствия взаимозаменяемости;
г) после операций, имеющих решающее значение для качества последующей обработки или сборки;
д) после операций с возможным высоким размером брака;
е) при испытании готовых изделий ответственного назначения;
Выборочный контроль - осуществляется не над всей массой продукции, а только над выборкой. Обычно он используется в следующих случаях:
а) при большом числе одинаковых деталей,
б) при высокой степени устойчивости технологического процесса;
в) после второстепенных операций.
Статистический контроль - является формой периодического выборочного контроля, основанный на методах математической статистики и позволяющий обнаружить и ликвидировать отклонение от нормального хода технического процесса раньше, чем эти отклонения приведут к браку. Основан на применении 7 инструментов в УК (карты Шухарта, диаграммы Парето, диаграммы рассеивания и др.).
Текущий предупредительный (превентивный) контроль - выполняется с целью предупреждения брака в начале и в процессе обработки. Он включает:
|
|
а) проверку первых экземпляров изделий;
б) контроль соблюдения технологических режимов;
в) проверку вступающих в производство материалов, инструментов , технологической оснастки и др,
г) FMEA – технологии или конструкции.
Многоступенчатый контроль - исполнителя плюс операционный плюс специальный плюс приемочный.
Технический контроль на предприятии. Виды, результативность.
Виды технического контроля:
По стадиям производственного процесса:
Входной контроль - предназначен для проверки качества сырья, материалов, полуфабрикатов, комплектующих изделий, получаемых по кооперации, а также инструментов и приспособлений до начала производства;
Пооперационный (промежуточный) контроль деталей, узлов, заготовок и т.п., выполняемый по ходу технологического процесса;
Приемочный (окончательный) контроль - проводится над заготовками, деталями, сборочными единицами, готовыми изделиями;
Контроль транспортировки продукции;
Контроль хранения продукции.
2)По степени охвата продукции (по объему проверки):
Сплошной контроль - выполняется при полном (100%-ном) охвате предъявляемой продукции. Он применяется в следующих случаях: а) при ненадежности качества поставляемых материалов, полуфабрикатов, заготовок, деталей, сборочных единиц; б) когда оборудование или особенности технологического процесса не обеспечивают однородность изготовляемых объектов; в) при сборке в случае отсутствия взаимозаменяемости; г) после операций, имеющих решающее значение для качества последующей обработки или сборки; д) после операций с возможным высоким размером брака; е) при испытании готовых изделий ответственного назначения;
|
|
Выборочный контроль - осуществляется не над всей массой продукции, а только над выборкой. Обычно он используется в следующих случаях: а) при большом числе одинаковых деталей, б) при высокой степени устойчивости технологического процесса; в) после второстепенных операций.
По особенностям проверки (по характеру воздействия на контролируемую продукцию):
Разрушающий контроль, при котором последующее использование продукции невозможно;
Неразрушающий конроль.
4)По степени механизации и автоматизации:
Ручной (немеханизированный) контроль;
Механизированный контроль;
Автоматизированный контроль (автоматизированные системы управления качеством).
|
|
5)По контролируемому параметру:
Контроль по количественному признаку, когда определяют численные значения одного или нескольких показателей, которые сравнивают с нормативными значениями;
Контроль по качественному признаку, когда каждую единицу проверяемой продукции приписывают к определенной группе, а решение принимают в зависимости от того, какое изделие попало в каждую группу;
Контроль по альтернативному признаку представляет собой частный случай контроля по качественному признаку, когда существуют две группы – годные и дефектные изделия.
По организационным формам выявления и предупреждения брака:
Летучий контроль, который выполняется контролером внезапно в случайные моменты времени (без графика) при систематическом обходе закрепленных за ним рабочих мест;
Кольцевой контроль, заключающийся в том, что за контролером закрепляется определенное количество рабочих мест, которые он обходит «по кольцу» периодически в соответствии с часовым графиком, причем продукция проходит контроль на месте ее изготовления;
Статистический контроль, являющийся формой периодического выборочного контроля, основанный на методах математической статистики и позволяющий обнаружить и ликвидировать отклонение от нормального хода технического процесса раньше, чем эти отклонения приведут к браку;
|
|
Текущий предупредительный (превентивный) контроль, выполняемый с целью предупреждения брака в начале и в процессе обработки. Он включает: а) проверку первых экземпляров изделий; б) контроль соблюдения технологических режимов; в) проверку вступающих в производство материалов, инструментов , технологической оснастки и др.
Понятие терминов «гемба», «голос потребителя». Методика QFD.
Гемба - место, где формируется продукция или предоставляются услуги. Идея гемба с позиции менеджмента заключается в том, что если проблема возникает, то специалисты должны идти в гемба, собрать на месте данные, установить причину и предложить решение проблемы.
Правила гемба
1)Когда возникает проблема (ненормальное положение), прежде всего, идите в гемба.
2) Проверяйте гембутсу — связанное с этим оборудование.
3) Принимайте контрмеры на месте.
4)Ищите коренную причину.
5)Стандартизируйте, чтобы избежать повторения.
Руководство несет ответственность за найм и обучение работников, установление стандартов для их работы, а также проектирование продукции, технологических процессов. Таким образом, менеджмент определяет условия в гемба, и что бы там ни случилось, это отразится на менеджменте. Менеджеры должны знать условия на предприятии; отсюда аксиома: «Прежде всего, идите в гемба». В качестве рутинного действия менеджеры и руководители должны немедленно пойти на площадку, встать на месте и в течение пяти минут внимательно изучать, что происходит. За пять минут можно узнать многое. Выработав привычку идти в гемба, менеджер с легкостью узнает ненормальность, когда она происходит, и обращается к таким проблемам. Когда вы в гемба, то, что вы видите, является реальными данными. Когда вы внимательно изучаете то, что произошло, есть шанс того, что проблема будет решена на месте, и никакой доклад не понадобится.
Одним из лучших способов оставаться в тесном контакте с гемба, является жизнь в гемба, а именно, перенести свой рабочий стол в гемба.
Многие японские компании ввели так называемых «проживающих инженеров». Это инженеры, которые были перемещены в гемба с тем, чтобы они могли быстро ответить на технические вопросы, задаваемые людьми гемба, или произвести технические изменения без волокиты. Инженерный отдел, находивший ранее в головном офисе компании в башне из слоновой кости, зачастую переводится на производственную площадку предприятия. Менеджеры должны поощряться часто выходить в гемба.
«Голос потребителя»
Чтобы выжить, производитель вынужден постоянно смотреть в рот потребителю, ловить каждое его слово и как можно быстрее выполнять все его пожелания. Потребитель становится главным действующим лицом в производственном процессе производителя. Он, и только он, может сказать, качественна ли наша продукция (или услуги). Значит качество, это не соответствие чертежу или техническим условиям на продукцию (хотя их никто и не отменял!), а мнение потребителя о том, годится ли ему наша продукция. Если он сочтет, что наша продукция не подходит, то никакие ссылки на чертеж нас не спасут. Более того, мы просто лишимся единственного источника существования - денег, которые нам не заплатят.
Разработана программа - структурирование функции качества (СФК) или методика QFD. Этот подход должен привести к наиболее рациональному использованию всех ресурсов организации. Значит у нее будут максимальные шансы удержаться на рынке. Часто говорят, что все это означает стремление услышать "голос потребителя".
Структурирование функций качества — это метод структурирования нужд и пожеланий потребителя через развертывание функций и операций деятельности по обеспечению на каждом этапе жизненного цикла проекта создания продукции такого качества, которое бы гарантировало получение конечного результата, соответствующего ожиданиям потребителя.
Основным инструментом СФК является таблица, получившая название «дом качества». В ней отображается связь между фактическими показателями качества (потребительскими свойствами) и вспомогательными показателями (техническими требованиями).
Центральная часть дома — это таблица, столбцы которой соответствуют техническим характеристикам, а строки потребительским. В клетках отмечается уровень зависимости, если она есть. Крышу дома представляют сведения о корреляции между техническими характеристиками.
Левое крыло — требования потребителей. Правое крыло — таблица рейтингов потребительских характеристик (с точки зрения пользовательского восприятия) для существующих на рынке подобных продуктов.
Подвал дома содержит результаты анализа технических характеристик конкурирующих продуктов, результаты выработки стратегии изменения технических характеристик своего продукта (планируемые показатели для первоначальной разработки), оценки абсолютной и относительной важности.
Система сбалансированных показателей BSC.
Balanced Scorecard разработана на основе выводов исследования, проведенного в 1990 году профессорами Гарвардской школы экономики Дэвидом Нортоном и Робертом Капланом.
Компания становится успешной только в том случае, если планомерно развивается. В аспекте управления понятие “планомерное развитие” означает создание и реализацию стратегических планов.
На практике исполнение стратегических планов становится самым серьезным испытанием для организации. Масса отдельных мероприятий и действий сотрудников должна быть скоординирована таким образом, чтобы реализовать цели, желательно с наименьшими затратами и в максимально сжатые сроки. Balanced Scorecard создавалась как инструмент, позволяющий согласовать действия подразделений и сотрудников для достижения основной цели, стоящей перед компанией.
Основной принцип Balanced Scorecard, который во многом стал причиной высокой эффективности этой технологии управления - управлять можно только тем, что можно измерить.
Иначе говоря, цели можно достигнуть только в том случае, если существуют поддающиеся числовому измерению показатели, говорящие управленцу, что именно нужно делать и правильно ли с точки зрения достижения цели он делает то, что делает.
Balanced Scorecard делает акцент на нефинансовых показателях эффективности, давая возможность оценить такие, казалось бы, с трудом поддающиеся измерению, аспекты деятельности как степень лояльности клиентов, или инновационный потенциал компании.
Авторы Balanced Scorecard предложили четыре направления оценки эффективности, отвечающие на самые значимые для успешной деятельности компании вопросы:
Финансы (”каково представление о компании у акционеров и инвесторов?”);
Клиенты (”какой компанию видят покупатели ее продуктов?”);
Бизнес-процессы (”какие бизнес-процессы требуют оптимизации, на каких организации стоит сосредоточиться, от каких отказаться?”);
Обучение и рост (”какие возможности существуют для роста и развития компании?”).
Технологически построение BSC для отдельно взятой компании включает несколько необходимых элементов:
· карту стратегических задач, логически связанных со стратегическими целями;
· непосредственно карту сбалансированных показателей (количественно измеряющих эффективность бизнес-процессов, “точку достижения цели” и сроки, в которые должны быть достигнуты требуемые результаты);
· целевые проекты (инвестиции, обучение и т.п.), обеспечивающие внедрение необходимых изменений;
· “приборные панели” руководителей различных уровней для контроля и оценки деятельности.
“Приборная панель” менеджера каждого уровня включает те показатели, которыми он оперирует в своей деятельности. Для топ-менеджера это показатели стоимости компании, эффективности использования капитала, эффективности инвестиций и т.д. На уровне руководителя производственной единицы - показатели операционных затрат, загрузки мощностей, величины брака и т. п. Построение BSC осуществляется таким образом, чтобы задачи и показатели менеджеров более высокого уровня в интегрированном виде отражали задачи и показатели менеджеров более низкого уровня оргструктуры.
Таким образом, удается сделать реализацию стратегии регулярной деятельностью всех подразделений, управляемой с помощью планирования, учета, контроля и анализа сбалансированных показателей, а также мотивации персонала на их достижение.
Дата добавления: 2021-11-30; просмотров: 85; Мы поможем в написании вашей работы! |
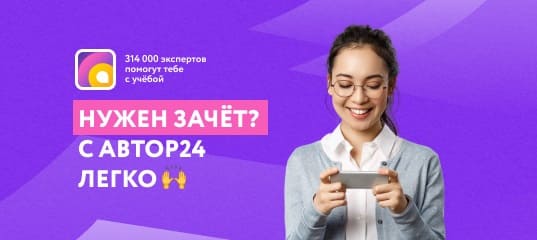
Мы поможем в написании ваших работ!