Вариант детали из поковки штампованной (из штамповки)
ПРИМЕР ВЫПОЛНЕНИЯ КОНТРОЛЬНЫХ РАБОТ
Исходные данные
а) Сборочный чертеж «Клапан дроссельный»
б) Чертеж сварной детали «Корпус подшипника» - 135340 (приложение А.
в) Тип производства:
- литой детали – серийное производство;
- штампованной детали – массовое производство.
Функциональное назначение корпуса подшипника
Корпус подшипника своим отверстием Ø 140 + 0,04 обеспечивает опору (конструкторскую базу) для подшипника качения одного из концов вала заслонки, а сам, базируясь своим основанием на конструкторской базе (на раме), должен обеспечивать соосность и параллельность оси своего отверстия оси отверстия под подшипник во втором корпусе. Поэтому в чертеже корпуса предусмотрен допуск 0,016 на непараллельность отверстия Ø 140 + 0,04 относительно основания пов. «А» в вертикальной плоскости.
Для обеспечения соосности этих отверстий обоих корпусов в горизонтальной плоскости предусмотрено самоустановление корпусов подшипниками и валом за счет продолговатых крепежных отверстий в основании корпуса с большими зазорами между ними и крепежными болтами.
Для обеспечения соосности подшипников в вертикальной плоскости при сборке предусматривается установка регулировочных прокладок между основанием корпуса и рамой клапана.
Для подачи консистентной смазки в подшипник в корпусе предусмотрено отверстие М10х1-7Н под прессмасленку.
|
|
Для предохранения подшипника от пыли, учитывая очень малую периодическую скорость вращения вала, в корпусе предусмотрено два простых лабиринтных уплотнения: радиусные пылесборные канавки, и торцевые канавки, создающие лабиринтное уплотнение в сопряжении корпуса с пылезащитной шайбой.
Фиксация вала с подшипником вдоль оси обеспечивается торцем корпуса и торцем крышки, прикрепляемой шестью винтами к корпусу.
Для исключения недопустимой для болтовых соединений эксцентричной нагрузки опорные для гаек поверхности нельзя оставлять с уклонами, с облоем, с местными неровностями, т.е. они должны быть механически обработаны с обеспечением их параллельности основанию корпуса.
Для уменьшения влияния неплоскостности сварной рамы клапана, на которую устанавливается корпус подшипника, в его основании предусмотрены две выемки с сохранением опорной средней части основания для исключения деформации корпуса подшипника от радиальных сил со стороны вала заслонки.
Эти же выемки являются элементами технологичности корпуса, уменьшающими величину обрабатываемых механически поверхностей.
Установление свободных поверхностей
Исходя из функционального назначения корпуса, сопрягаемыми его поверхностями, качество которых необходимо обеспечить мехобработкой, являются: основание корпуса, опорные поверхности под гайки, отверстие под
|
|
подшипник и его торец под крышку, упорный для подшипника торец внутри корпуса, отверстие для выхода вала, крепежные отверстия М10-7Н, отверстие М10х1-7Н и его торец под масленку. Остальные несопрягаемые поверхности свободные, в т.ч. продолговатые крепежные отверстия в основании.
Вариант литой детали
4.4.1 Выбор способа литья.
Исходя из назначения клапана дроссельного, устанавливаемого на газоходах металлургического грязного, малолюдного производства, к шероховатости литых поверхностей, которые остаются в корпусе подшипника после мехобработки, не предъявляются требования по эстетике и эргономике. Тогда влияющими на выбор способа литья остаются: тип производства – серийный и экономичность получения заготовки – отливки. Значит целесообразным будет стальное литье в песчано-глинистую форму, когда требуется в качестве спецоснастки модель и стержневой ящик, а все остальные элементы технологии литья универсальные в отличии от других более точных способов, применяемых в крупно-серийном и массовом производстве, которые кроме более сложной спецоснастки (форм) требуют специального оборудования и более дорогих вспомогательных материалов.
|
|
4.4.2 Отработка чертежа корпуса подшипника на технологичность.
Учитывая возможности литья и требований по его технологичности целесообразно изменить многогранную форму тела корпуса на округлую, более равностенную, с меньшим количеством термических узлов, с радиусными сопряжениями тела корпуса с его основанием, с радиусными скруглениями кромок (кроме кромок по разъему литейной формы и в местах сопряжения знаков стержней с формой, где будут образовываться заливы – облой).
Размеры продолговатых крепежных отверстий позволяют их получить литьем без последующей мехобработки.
Для сокращения объема мехобработки целесообразно предусмотреть выступание торца отверстия Ø 140 + 0,04 за боковую поверхность его основания не менее, чем на 1 мм.
Исходя из назначения клапана дроссельного и корпуса подшипника, целесообразно на его свободных поверхностях допустить остатки облоя,
остатки литниковой системы величиной до 2 мм, допустить наличие формовочных уклонов.
По свободной поверхности торца со стороны отверстия Ø 90,8 мм от усадочных утяжин в зоне термических узлов целесообразно допустить неплоскостность в зависимости от степени коробления отливки.
|
|
Допуски на размеры по свободным литым поверхностям требуется оставить литейные, в т.ч. по размерам, образованным одной литой и другой
механически обработанной поверхностью, но только устанавливаются на 2 класса точнее.
4.4.3 Анализ вариантов расположения плоскости разъема литейной формы.
4.4.3.1 Вариант 1 (рисунок 1).
Достоинства:
а) Форма отливки более приближается к форме готовой детали и с меньшей ее массой по сравнению со сварным вариантом.
б) Литниковая система и облой по разъему литейной формы, а также облой по овальным крепежным отверстиям располагаются по обрабатываемым поверхностям детали, что не требует их зачистки заподлицо с поверхностью отливки.
Недостатки:
в) Нарушено требование по выбору самой малой (из трех габаритных размеров) высоты отливки, которая обеспечивает минимальный путь для выхода воздуха и газов из формы при заливке и максимальную площадь для выхода того же воздуха и газов через форму. По этому варианту есть риск получения газовых и шлаковых раковин (от обрушения формы) в основании корпуса.
г) Нарушено требование о равностенности стенок отливки, значит есть риск получения усадочных раковин (рыхлот) и утяжин в двух термических узлах «Т». Это же приводит к увеличению массы детали.
д) Нарушено требование обходиться без стержней, которых по этому варианту 3 штуки. В связи с наличием стержней обязательно будет перекос отверстий и их смещение из-за зазоров в сопряжении знаков стержней и знаковых полостей полуформ, что потребует увеличения припусков на мехобработку. Кроме этого по периметру сопряжения знаков стержней с полуформами из-за тех же зазоров обязательно будет облой (заливы) по линиям «5», «6» и «7», который по необрабатываемому торцу «П» требуется зачищать до требуемой величины и который по дугам линий «5» и по торцу «Р» будет вызывать мехобработку с ударами.
е) Боковые поверхности корпуса (по его высоте) со всех сторон имеют формовочные уклоны, которые приводят к увеличению массы отливки и детали. Кроме этого уклоны, облой по отверстиям создают трудности базирования заготовки на первой операции мехобработки, а именно при фрезеровке основания корпуса.
1 – стояк; 2 – выпоры; 3 – стержни; 4 – знаковые части стержней; 5, 6 и 7 – линии разъемов стержней с формой.
Рисунок 1 – Вариант 1 расположения разъема литейной формы.
|
|
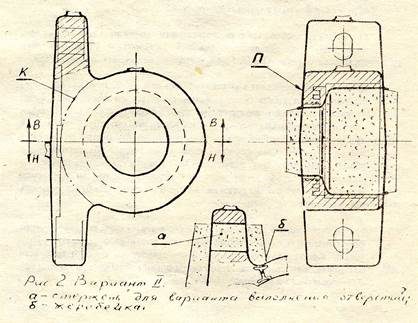
а – стержень для варианта выполнения отверстий; б – жеребейка.
Рисунок 2 – Вариант 2 расположения разъема литейной формы.
ж) По этому варианту при мехобработке торца отверстия Ø 140 + 0,04 необходимо будет в конце хода резца подрезать часть основания по линии «К», что будет вызывать работу с ударами, снижающими режимы резания.
4.4.3.2 Вариант 2 (рисунок 2).
Достоинства в сравнении с 1 вариантом:
а) Конфигурация стержня для центрального отверстия более простой формы, создающая облой только по окружности торцев отверстий.
б) По обоим торцам центрального отверстия имеется облой только по обоим краям отверстия.
Недостатки (дополнительно к недостаткам по п.п.: 4.3.3.1 в, г, д, е, ж 1 варианта):
в) Требуется зачистка до допустимой величины остатков литниковой системы и облоя по разъему формы по необрабатываемому торцу «П» центрального отверстия.
г) Требуется мехобработка продолговатых крепежных отверстий, которые литьем выполнить очень рискованно из-за ненадежной опоры стержня «а», зависающий знак которого опирается на жеребейку «б», установленную на наклонную поверхность формы.
д) Увеличивается трудоемкость мехобработки основания, когда вместо одного прохода «насквозь» требуется еще 2 прохода для получения двух выемок в основании.
4.4.3.3 Вариант 3 (рисунок 3).
Достоинства в сравнении с 1 вариантом:
а) Конфигурация отливки наиболее приближается к форме готовой детали, более равностенная, а готовая деталь будет с меньшей массой;
б) Для получения отливки требуется только одна модель, которая литейной полуформой обеспечивает получение центрального отверстия без стержня, т.е. без перекоса и смещения относительно наружного контура отливки;
в) Так как отливка получается нижней полуформой и с минимальной высотой, то она будет иметь минимальные литейные дефекты;
г) Боковые поверхности корпуса (самые протяженные) не имеют уклонов и облоя, что создает благоприятные условия для базирования заготовки на первой операции мехобработки (фрезеровки основания);
д) Поверхность обрабатываемого торца отверстия Ø 140 + 0,04 минимально необходимая и без облоя для безударного резания.
Недостатки в сравнении с 1 вариантом:
е) Конфигурация стержней для получения литьем крепежных продолговатых отверстий сложней, но не значительно;
ж) Требуется зачистка до требуемой величины остатков литниковой системы по механически не обрабатываемому торцу корпуса;
з) Требуется зачистка до требуемой величины облоя по разъему литейной формы по необрабатываемой части периметра «П» протяженностью чуть больше облоя от знака стержня поз.4 по 1 варианту (рисунок 1).
4.4.3.4 Вариант 4 (рисунок 4).
Достоинств по сравнению с 3 вариантом нет, а есть недостаток: наличие стержня для получения центрального отверстия с его возможным смещением и перекосом, увеличивающими припуски на мехобработку.
Рисунок 3 – Вариант 3 расположения разъема литейной формы.
Рисунок 4 – Вариант 4 расположения разъема литейной формы.
Рисунок 5 – Вариант 5 расположения разъема литейной формы.
а) объемная горячая штамповка; б) обрубка облоя и просечка перемычки «С».
Рисунок 6 – Технология штамповки корпуса подшипника.
4.4.3.5 Вариант 5 (рисунок 5).
Достоинства в сравнении с 3 вариантом нет, а есть недостатки:
а) Требуется две полумодели.
б) Наличие смещения в отливке по разъему литейной формы, увеличивающего припуски на мехобработку.
в) Наличие облоя внутри центрального ступенчатого отверстия (по разъему литейной формы), увеличивающего местный припуск на мехобработку и создающего ударное резание.
Из анализа расположения плоскости разъема литейной формы следует вывод, что самым оптимальным вариантом является вариант 3.
4.4.4 Чертеж детали.
4.4.4.1 С учетом выбранного варианта расположения плоскости разъема литейной формы и с учетом отработки чертежа на технологичность разработан чертеж корпуса подшипника (Приложение Б).
4.4.4.2 Вместо стали ст.3 деталей сварного корпуса принимается литейный материал – сталь 20Л, имеющий мехсвойства не хуже стали ст.3, а рядом указывается определяющий качество литого металла ГОСТ 977-88 – Отливки стальные. Общие технические условия.
4.4.4.3 Шероховатость Ra50 оставшихся после мехобработки литых поверхностей корпуса переносится из чертежа отливки.
4.4.4.4 В ТТ чертежа детали первым пунктом вводится требование по точности отливки (по всем показателям точности), а в следующих пунктах оговариваются требования:
- по неуказанным размерам радиусных скруглений;
- по величине формовочных уклонов;
- по недопущению остатков облоя и литниковой системы либо по допустимой их величине;
- по допустимым отклонениям от правильной геометрической формы и расположения поверхностей.
Эти требования также переносятся из чертежа заготовки-отливки. При этом переносятся только те требования, которые остаются в детали после мехобработки.
4.4.5 Чертежи отливки.
4.4.5.1 Параллельно в соответствии с разрабатываемым чертежом детали вычерчивается чертеж отливки с учетом припусков на мехобработку в масштабе чертежа детали. Чертеж оформляется в соответствии с требованиями ГОСТ 3.1125-88 Правила графического выполнения элементов литейных форм и отливок (кроме его пункта 3.1).
При этом по мелким элементам детали: по 6 отв. М10-7Н, по отв. М10х1-7Н и его торцу, по всем лабиринтным канавкам, по канавке Ø 140,5 мм предусматривается литейный напуск, т.е. они литьем не оформляются. (Приложение В).
4.4.5.2 Указанные в чертеже точность отливки 11–5-15-11 и шероховатость поверхностей соответствуют требованиям ГОСТ26645-85* Отливки из металлов и сплавов. Допуски размеров, массы и припуски на механическую обработку.
Они имеют следующие обоснования:
а) Первая цифра 11 - размерная точность отливки корпуса подшипника 11 класса установлена по таблице 9 Приложения 1 для нетермообрабатываемых отливок из черных сплавов, отлитых в песчано-глинистую форму прочностью 60 …120 кПа (средняя прочность) для диапазона наибольших габаритных размеров 250 … 630 мм (наибольший габарит корпуса – 330 мм) с учетом примечания 1 к таблице 9 (из диапазона классов точности 9т-13). Но согласно п. 2.2 в связи с формированием отливки, кроме размеров 86 и 88, только в одной полуформе точность остальных размеров принимается на 2 класса точнее, т.е. по 10 классу.
б) Вторая цифра - степень коробления – 5-я элементов отливки установлена по таблице 10 приложения 2 для нетермообрабатываемого литья в разовую форму для отношения наименьшего размера отливки – 86 мм, к наибольшему – 330 мм, равному: 86/330 = 0,26 из диапазона 3 – 6 с учетом примечания 1 к таблице для нашего корпуса с тонкими концами его основания.
в) Третья цифра - степень точности – 15я поверхностей отливки установлена по таблице 11 приложения 3 аналогично п. 4.4.5.2,а.
г) Четвертая цифра - класс точности 11-й по массе отливки установлен по таблице 13 приложения 5 аналогично п. 4.4.5.2,а.
д) После степени точности предусматривается указание о величине смещения по разъему формы, но для нашей детали в связи с тем, что отливка получается в одной нижней полуформе без применения стержня для отверстий Ø 140 и Ø 90,8 мм требований по допустимому смещению по плоскости разъема, по смещению и перекосу указанных отверстий устанавливать не требуется.
е) Шероховатость Ra50 поверхностей отливки установлена по таблице 12 приложения 4 для 15-й степени точности поверхностей. Шероховатость указывается в правом верхнем углу КЭ под номером операции.
4.4.5.3 Неуказанные размеры радиусов скруглений зависят от размеров элементов отливки и приняты 6 … 8 мм в соответствии с рекомендацией справочника [1, стр.105].
4.4.5.4 Формовочные уклоны зависят от высоты (литейной) элементов отливки и для высоты ≈ 90 мм приняты 30 в соответствии с рекомендацией справочника [1, стр.79].
4.4.5.5 В соответствии с функциональным назначением корпуса подшипника и с учетом места установки клапана дроссельного конструктивно принимается допустимая величина остатков облоя и литниковой системы не более 2 мм.
4.4.5.6 Учитывая конфигурацию отливки в зоне термических узлов из-за термической усадки появится «утяжина» - неплоскостность величиной не более
1,2 мм согласно таблицы 3 [6] для 15 степени точности поверхности. Исходя из назначения корпуса подшипника такую неплоскостность по несопрягаемому торцу – пов. «В» (Приложение Б) можно допустить, поэтому это требование вносится в оба чертежа (детали и отливки).
4.4.5.7 Согласно п. 2.5 и таблицы 2 [6] устанавливаем допуски на отклонения от правильной геометрической формы и расположения поверхностей отливки для 5-й степени коробления:
а) Неперпендикулярность пов. А по ее ширине 86 мм относительно торца поверхности Ø 185 мм для 5 степени корабления допускается до 0,32 мм. Эта неперпендикулярность должна быть скомпенсирована дополнительным припуском по пов. А при фрезеровке размера 195 мм в детали с базированием детали по торцу Ø 185. Но в чертеж это требование не вводится, т.к. по поверхности А имеется формовочный уклон.
б) Непрямолинейность поверхности А по ее длине 330 мм таблицей 2 допускается до 1 мм. Эта непрямолинейность должна быть скомпенсирована дополнительным припуском по пов. А при фрезеровке размера 195 мм в детали.
в) Непараллельность торца поверхности Ø 185 мм относительно необрабатываемого торца не требует дополнительного припуска по нему, т.к. он будет обработан от чистовой базы пов.А. Но непараллельность допускаемая согласно таблицы 2 [6] до 0,5 мм будет влиять на размер 88. В связи с тем, что эта непараллельность меньше устанавливаемого допуска на размер 88, она будет входить в его пределы и оговаривать ее в ТТ не требуется..
г) Из-за несимметричности конфигурации отливки отверстия отливки под размеры Ø 140 и Ø 90,8 будут некруглыми, но согласно п. 2.6 [6] эта некруглость учитывается в величине допуска на их размеры.
4.4.5.8 Согласно п.2.8 и таблицы 1[6] смещение и перекос продолговатых отверстий шириной 28 мм, формируемых стержнями, для самой тонкой стенки 15 мм (30±1)-R15=15) для 10 класса точности (принятом на два класса точнее от установленной в п. 4.3.5.2.а точности 11 класса) равен 1,8 мм.
Учитывая, что на каждую сторону между крепежными болтами М24х120 и стенками продолговатых отверстий предусмотрен зазор также по 2 мм, то, не вызывая значительного уменьшения прочности основания в опасном сечении, необходимо увеличить длину и ширину отверстий на 2 мм, т.е. до 30 мм и 36 мм.
4.4.5.9 Размеры отливки рассчитываются с учетом общего припуска, устанавливаемого таблицей 6 [6] на каждую сторону обрабатываемого размера (для среднего уровня точности обработки).
Общий припуск устанавливается в зависимости от вида окончательной мехобработки (черновая, получистовая, тонкая), от ряда припуска – 8, выбранного по таблице 14 и от общего (условного) допуска, который является геометрической суммой допуска на размер отливки и допусков на отклонение от правильной геометрической формы и на неправильное расположение
обрабатываемой поверхности относительно литой технологической базы. Эта геометрическая сумма устанавливается таблицей 16 приложения 8 [6].
Вид окончательной механической обработки устанавливается таблицей 7 [6] в зависимости от допуска на размер отливки и от его соотношения с допуском на размер детали.
Значения параметров для расчета размеров отливки и сам расчет сведены в таблицу 1.
4.4.5.10 Предусмотренные в отливке толщины стенок сравниваются с минимально допустимой толщиной 12 мм для стального литья [1, стр. 84].
4.4.5.11 Радиусное сопряжение основания с телом корпуса устанавливается величиной 14 мм в зависимости от толщины сопрягаемых стенок [1, стр. 93].
4.4.5.12 В последних пунктах ТТ вносятся пункты:
п.8 – материал отливки – сталь 20Л ГОСТ 977-88.
п.9 – масса отливки.
п.10 – масштаб 1:2.
4.4.5.13 Расчет массы отливки.
Масса отливки рассчитывается по формуле
, (1)
где - объем отливки, рассчитываемый по чертежу отливки в см3;
=0,00785 кг/см3 – плотность стали 20Л.
Для расчета объема отливки ее конфигурацию расчленим на простые геометрические фигуры: два кольца и основание (с учетом допусков, увеличивающих объем отливки).
Кольцо А: наружный максимальный диаметр DА = 185 мм = 18,5 см
минимальное отверстие dА = 75,8 мм = 7,58 см
максимальная толщина hА = 95,5 – 57,8 = 37,7 мм = 3,77 см.
Кольцо Б: Наружный диаметр DБ = 185 мм = 18,5 см
минимальное отверстие dБ = 123 мм = 12,3 см
максимальная толщина hБ = 60,2 = 6,02 см.
Основание В, состоящее из 2-х одинаковых частей (до сопряжения с телом корпуса с учетом наличия продолговатых отверстий):
Максимальная толщина SВ = 48 мм = 4,8 см
ширина ТВ = 86 мм = 8,6 см
длина LВ = 120 мм = 12 см,
Таблица 1 – Допуски, припуски и размеры отливки.
Размеры детали | Точность размера детали | Допуск разме-ра детали Тдет. | База отливки для получения размера детали | Допуск размера отливки Тотл. | Соотно- шение Тдет./Тотл. | Вид оконча-тельной мехобра-ботки (табл.7) | Допуск формы и располож. | Общий (условный) допуск размера отливки (табл.16) | Общий припуск на сторону для ряда припуска – 8 (табл.6) | Расчет номинального размера отливки | Размер в чертеже отливки |
1 | 2 | 3 | 4 | 5 | 6 | 7 | 8 | 9 | 10 | 11 | 12 |
330 | 10кл.лит.*1 | Тотл. | - | -4,0 | - | - | - | - | - | - | 330-4,0 |
40 *2 МОР вместо р-ра 100 | 10кл.лит.*3 | -2,2 | Поверхность противопо-лож. пов.А и торец Ø185 | -2,2 | 1,0 | черновая | Непрямол. 1,0 Неперп. -0,32 | 3,2 | 2,9 | 35+2,9=37,9 | 37,9-2,2 |
86 | 11кл.лит. | Тотл. | - | -4,4 | - | - | - | - | - | - | 86-4,4 |
35 | h14 | -0,62 | Пов.А | -2,2 | 0,28 | черновая | непрямол. 0,2 *4 | 2,4 | 2,5 | 37,9+2,5=40,4 | 40,4-2,2 |
Ø185 | 10кл.лит. | Тотл. | - | -3,6 | - | - | - | - | - | - | 185-3,6 |
59 | Н8 | +0,046 | Торец Ø 140 | ±1,2 1* | - | - | - | - | Припуск равен припуску по размеру 88, тогда размер в отл. 59±1,2
| ||
Ø90,8 | Н12 | +0,35 | Пов.А | +2,8 | 0,125 | полу-чист. | Смещ.1,4*5 | 2,4 *6 | 3,4 | 90,8-2х3,4= = 84 | 84+2,8 |
Ø140 | Н7 | +0,04 | Пов.А | +3,2 | 0,013 | тонкая | Смещ.1,4*5 | 2,4 *6 | 4,1 | 140-2х4,1= =131,8 | 131,8+3,2 |
30 (отв.) | 10кл.лит. | Тотл. | - | +2,2 | - | - | - | - | - | - | 30+2,2 |
36(отв.) | 10кл.лит. | Тотл. | - | +2,2 | - | - | - | - | - | - | 36+2,2 |
Продолжение таблицы 1
1 | 2 | 3 | 4 | 5 | 6 | 7 | 8 | 9 | 10 | 11 | 12 |
46,5 | 10кл.лит. | Тотл. | - | ±1,2 | - | - | - | - | - | - | 46,5±1,2 |
30 | 10кл.лит. | Тотл. | - | ±1,1 | - | - | - | - | - | - | 30±1,1 |
88 | 10кл.лит.*3 | -2,8 | Торец Ø 140 | -4,4 | 0,64 | черновая | - | 4,4 | 3,5 | 88+3,5=91,5 | 91,5-4,4 |
Примечания: *1 – Согласно п.4.4.4.5.2 а); *2 – Ориентировочный размер, получаемый при фрезеровке пов.А с учетом наличия припуска для последующей фрезеровки в размер 35; *3 – Согласно п.4.4.2; *4 – От коробления пов.А длиной 330 мм до непрямолинейности в 1 мм на длине 64 мм при фрезеровке размера 35 непрямолинейность в отливке составит: 1:330х64=0,2; *5 – Допуск ±1,4 по размеру 100 является допуском расположения для отверстий; *6 – Общий допуск установлен по таблице 16 приложения 8 [6] для половины допуска на диаметр (согласно п.4.2.1 [6]) и с учетом допуска на смещение. |
где длина определена замером по чертежу (с учетом его масштаба) с условным приведением фасонной формы к параллелепипеду.
vотл. = VА + VБ +2 VВ.. (2)
(3)
(4)
(5)
Отсюда
По таблице 4 [6] для нашего 11 класса точности по массе поле допуска составляет 16% от номинальной массы отливки, тогда допуск по массе :
(6)
В ТТ чертежа отливки с учетом симметричного расположения поля допуска указывается масса отливки.
Вариант детали из поковки штампованной (из штамповки)
4.5.1 Выбор способа штамповки.
Исходя из заданного массового типа производства, из конфигурации, размеров, материала корпуса подшипника выбираем способ штамповки на кривошипном горячештамповочном прессе (КГШП), т.е. способ, который производительней штамповки на молоте, на фрикционном винтовом прессе и тем более на тихоходном гидропрессе. Кроме этого штамповка на КГШП, имеющим механизм выталкивания, более точная по размерам и с меньшими штамповочными уклонами, чем на молоте и фрикционном прессе.
Конфигурация корпуса исключает штамповку на горизонтально-ковочной машине (ГКМ), на которой целесообразно штамповать стержневые заготовки с высаженными элементами по длине стержня.
Исходной заготовкой для штамповки на КГШП целесообразна заготовка из круглого горячекатанного проката, а еще лучше из квадратного из стали ст.3.
4.5.2 Отработка чертежа корпуса подшипника на технологичность.
Учитывая возможности штамповки и требования по ее технологичности, так же как и для литья, многогранную форму тела корпуса целесообразно
изменить на округлую с меньшей массой, с радиусными сопряжениями и скруглениями кромок.
В связи с тем, что размер продолговатых крепежных отверстий меньше их длины, по ним будет предусмотрен кузнечный напуск.
Для сокращения объема мехобработки, так же как и у отливки, целесообразно предусмотреть выступание торца отверстия Ø140+0,04 за боковую поверхность основания не менее, чем на 1 мм.
На свободных поверхностях корпуса подшипника целесообразно допустить остатки облоя по разъему штампа до 2 мм и наличие штамповочных уклонов.
Допуски на размеры свободных поверхностей целесообразно изменить на поковочные по ГОСТ7505-89 Поковки стальные штампованные. Допуски, припуски и кузнечные напуски.
4.5.3 Анализ вариантов расположения плоскости разъема штампа.
Рассматривая варианты расположения плоскости разъема штампа аналогично I и II вариантам для литья (рисунок 1 и рисунок 2), отмечаем, что они не приемлемы из-за размера исходной заготовки с малой стороной квадрата (менее 86 мм, чтобы она вошла в полость штампа) и с большой ее длиной (для обеспечения требуемой массы металла), которая недопустима из-за продольного изгиба исходной заготовки во время штамповки (допустимая высота исходной заготовки Hисх. Должна быть Нисх. ≤2,5 Dисх.заг., где Dисх. – диаметр или сторона квадрата).
Кроме этого при таких положениях разъема штампа по главному отверстию корпуса будет напуск.
Из оставшихся вариантов, аналогичных III, IV и V для литья (в соответствии с рисунками 3, 4 и 5), можно штамповать по любому из них.
Но целесообразней принять схему расположения плоскости разъема штампа по середине высоты штамповки и с расположением его пуансонов для образования главного отверстия (в соответствии с рисунком 6). Такая схема обеспечивает равномерную для каждого полуштампа деформацию заготовки и меньшее усилие штамповки, а значит равномерный и меньший износ полуштампов по сравнению с несимметричным по высоте разъемом; обеспечивает, хотя и незначительно, меньшую массу исходной заготовки из-за двусторонних штамповочных уклонов вместо односторонних; обеспечивает гарантированное центрирование заготовки из предыдущего ручья штампа в окончательном ручье в связи с утопанием (а не выступанием) пуансона нижнего полуштампа.
4.5.4 Чертеж детали.
Исходя из концепции по технологичности штамповки и принятой схемы расположения разъема штампа разработан чертеж детали (Приложение Г). При этом, исходя из назначения корпуса и клапана дроссельного, а также из
возможностей штамповки, устанавливаем шероховатость штампованных поверхностей Rz80 и вводим в технические требования чертежа корпуса допустимые для него дефекты (по скруглениям, уклонам, облою, смещению), остающиеся после мехобработки.
В графе «Материал» основной надписи чертежа указывается марка материала ст.3 ГОСТ8479-70, определяющий качество кованного металла.
4.5.5 Чертеж штамповки.
4.5.5.1 Проекция корпуса подшипника на главном виде вычерчивается в положении, в котором он штампуется (Приложение Д).
4.5.5.2 В соответствии с возможностями штамповки по мелким элементам детали: 6 отв.М10-7Н, отв.М10х1-7Н, по всем лабиринтным канавкам, по канавке Ø140,5 мм для выхода инструмента, а также по обоим продолговатым крепежным отверстиям предусматривается кузнечный напуск.
4.5.5.3 В правом верхнем углу карты эскиза под основной ее подписью указывается шероховатость штампованных поверхностей Rz80.
4.5.5.4 Указанные ТТ чертежа штамповки, установлены в соответствии с требованиями ГОСТ7505-89 Поковки стальные штампованные. Допуски, припуски и кузнечные напуски.
Они имеют следующие обоснования:
а) По таблице 19 Приложения 1 для открытой штамповки на КГШП рекомендуются классы точности штамповки Т4 и Т5. Исходя из назначения корпуса подшипника на клапане дроссельном, принимаем класс точности – Т5.
По таблице 1 для стали ст.3 с массовой долей углерода до 0,35% устанавливаем группу стали – М1.
По п.2 Приложения 2 определяется степень сложности штамповки по отношению ее ориентировочной массы - к массе простой геометрической фигуры -
, в которую вписывается фигура штамповки
, (7)
где
кг – масса детали из штамповки;
= 1,5 – расчетный коэффициент для определения ориентировочной массы поковки, устанавливаемый по таблице 20, Приложения 3.
Тогда кг.
Фигура штамповки корпуса подшипника вписывается в параллелепипед с ориентировочными размерами (с учетом припусков): 330х197,5х89 (мм).
Тогда с учетом плотности стали 0,00785х4 см3:
кг. (8)
(9)
В соответствии с указанием в п.4 Приложения 2 устанавливается степень сложности С2.
Для определения припусков и допусков по таблице 2 для штамповки массой 18,36 кг, с группой стали М1, степени сложности С2 и классу точности Т5 устанавливается исходный индекс – 9, что и вносится в п.1 ТТ чертежа штамповки.
б) Допустимое смещение по плоской поверхности разъема штампа равное 1, 2 мм устанавливается по таблице 9 (п.2 ТТ чертежа).
в) Допустимая величина остаточного облоя равная 1,4 мм устанавливается по таблице 10 (п.3 ТТ чертежа). Для исключения травм рук рабочих, а также для товарного внешнего вида наружные заусенцы после обрезки облоя недопускаются.
г) Неконцентричность пробиваемого после объемной штамповки отверстия равная 2,5 мм устанавливается по таблице 12 (графика чертежа).
д) Допускаемая неплоскостность боковых поверхностей корпуса и изогнутость (непрямолинейность) основания корпуса равные по 1,6 мм устанавливаются по таблице 13 (п.4 ТТ чертежа).
е) Штамповочные уклоны: наружные – 50 ±
, внутренние – 70 ±
устанавливаются по таблице 18 и п.5.24.
ж) Учитывая минимальную величину радиуса скругления наружных углов при глубине полости ручья штампа порядка 45 мм равную 4 мм (таблица 7) и допуска 3 мм на радиусы скругления (таблица 17), а также указание п.6.4 вносится п.5 ТТ чертежа. При этом учитывается, что чем больше радиус внутренних углов штамповки, тем больше стойкость штампа.
4.5.5.5 Размеры штамповки рассчитываются с учетом основных припусков, назначаемых по таблице 3 [4]на одну сторону в зависимости от исходного индекса 9, размера по толщине штамповки ≈ 90 мм (высотного ее размера, получаемого обоими полуштампами), иных размеров (длины, ширины, диаметра, глубины уступов) и шероховатости поверхности после мехобработки.
Для компенсации смещения по разъему штампа по таблице 4 по размеру 195 назначается дополнительный припуск 0,5 мм по основанию корпуса, а по отв. Ø90,8 – припуск на диаметр: 0,5х2=1 мм.
Для компенсации неплоскостности по торцу Ø140+0,04 и непрямолинейности основания корпуса по таблице 5 назначаются дополнительные припуски по 0,8 мм.
Допуски на размеры назначаются по таблице 8 [4] с учетом п.5.2.
Результаты расчета размеров штамповки сведены в таблицу 2.
Таблица 2 – Припуски, допуски и размеры штамповки.
Размер по черт. Детали | Требу-ем. шеро-хов. | Основ-ной припуск на сторону | Дополн. припуск на сторону | Допуск на разм. штам-повки | Расчет размера штамповки | Исполнит. размер в черт. штам-повки |
1 | 2 | 3 | 4 | 5 | 6 | 7 |
330 Т5 | Rz80 | - | - | +1,4;-0,8 | - | ![]() |
195h15 | Ra12,5 | 1,3 | 0,5+0,8 | +1,1;-0,5 | 195+1,3+0,5+0,8=197,6 | ![]() |
Ø185Т5 | Rz80 | - | - | +1,3;-0,7 | - | ![]() |
Ø140Н7 | Ra1,6 | 1,6 | - | +0,5;-1,1 | 140-2х1,6=136,8 | ![]() |
Ø90,8Н12 | Ra6,3 | 1,1 | 0,5 | +0,5;-1,1 | 90,8-2х1,1-2х0,5=87,6 | ![]() |
88h15 | Rа6,3 | 1,4 | 0,8 | +0,9;-0,5 | 88+1,4+0,8=90,2 | ![]() |
59Н8 | Ra3,2 | 1,4 | - | +0,5;-0,9 | 59-1,4=57,6 | ![]() |
35h14 | Ra12,5 | 1,0 | 0,8 | +0,9;-0,5 | 35+1,3+1,3+1,0+0,8= =39,4(1*) | ![]() |
![]() | - | - | - | ±0,5 (2*) | - | ![]() |
20Т5 | - | - | - | +0,4;-0,8 | - | ![]() |
38±JT17/2 | - | - | - | ±1,5 (3*) | 38-2(1,3+0,5+0,8)=32,8 (4*) | 32,8±1,5 |
82±JT17/2 | - | - | - | ±1,5 | 82+2(1,3+0,5+0,8)=87,2 | 87,2±1,5 |
Продолжение таблицы 2.
1 | 2 | 3 | 4 | 5 | 6 | 7 |
![]() | - | - | - | ±0,8 | 10+1,3+0,5+0,8=12,6 (4*) | 12,6±0,8 |
86Т5 | - | - | - | +0,9;-0,5 | - | ![]() |
1* - В расчете учтены припуски с двух сторон с учетом припуска по размеру 195. 2* - Допуск установлен по таблице 14 [4] как на межцентровое расстояние. 3* - На размеры детали: 38h17, 82h17; 10±JT17/2 и на соответствующие размеры штамповки установлены нестандартные допуски в связи с тем, что эти размеры не сопрягаемые, а их отклонения будут зависеть от отклонений по размеру 195h15 (197Т5) с учетом влияния скосов под углом 450. 4* - В расчетах размеров штамповки по размерам детали: 38h17; 82h17; 10±JT17/2 учтены величины припусков по размеру 197Т5 с учетом двухсторонних скосов под углом 450.
|
Размер до вырубаемой перемычки в отверстии взят конструктивно для получения толщины перемычки порядка 10 мм, чтобы при ее вырубке не было деформации (коробления) штамповки от большого усилия вырубки.
4.5.5.6 На основании чертежа штамповки рассчитывается уточненная ее масса:
(10)
где - объем штамповки, рассчитываемый по чертежу штамповки;
= 0,00785 кг/см3 – плотность стали ст.3.
Объем штамповки рассчитаем, расчленив фигуру штамповки на составные части простой формы: два кольца и основание.
Кольцо Г: наружный диаметр Dг =185 мм = 18,5 см
отверстие dг = 86 мм = 8,6 см
толщина hг = 30 мм = 3,0 см
Кольцо Е: наружный диаметр DЕ =185 мм = 18,5 см
отверстие dЕ = 134 мм = 13,4 см
толщина hЕ = 59 мм = 5,9 см
Основание Ж, состоящее из 2-х одинаковых частей (до сопряжения с телом корпуса), приведенных к форме параллелепипеда:
Толщина SЖ =40 мм = 4 см
Ширина ТЖ = 86 мм = 8,6 см
Длина LЖ = 100 мм = 10 см.
Тогда:
Vшт. = VГ +VЕ +2VЖ. (11)
(12)
(13)
(14)
Отсюда:
(15)
(16)
4.5.5.7 Последними пунктами в технические требования вносятся:
- материал штамповки – сталь ст.3;
- масса штамповки – 16,3 кг;
- масштаб 1:2.
СПИСОК ЛИТЕРАТУРЫ
1 Анисимов Н.Ф., Благов Б.Н. Справочник «Проектирование литых деталей».- М.: Машиностроение, 1967.
2 Афонькин М.Г., Магницкая М.В. «Производство заготовок в машиностроении». – Л.: Машиностроение, 1987.
3 Проектирование и произвосдтво заготовок в машиностроении. Уч. пособие /Под ред. Плескача – К.: Высшая школа, 1991.
4 ГОСТ 7505-89. Поковки стальные штампованные. Допуски, припуски и кузнечные напуски.
5 ГОСТ 8479-70. Общие технические условия для поковок из конструкционной стали.
6 ГОСТ 26645-85*. Отливки из металлов и сплавов. Допуски размеров, массы и припуски на механическую обработку.
7 ГОСТ3.1125-88. Правила графического выполнения элементов литейных форм и отливок.
8 ГОСТ3.1126-88 Правила выполнения графических документов на поковки.
9 СТП164-08-98 Работы учебные. Общие требования к оформлению текстового и графического материала. – КазНТУ, 1997.
10 Аристов Н.С. и др. «Основы технологии кузнечно-штамповочного производства». – М.: Машиностроение, 1971.
11 Брюханов А.Н. «Ковка и объемная штамповка». – М.: Машиностроение, 1975.
12 Косилова А.Г., Мещеряков Р.К., Калинич М.А. «Точность обработки, заготовки и припуски в машиностроении». – М.: Машиностроение, 1972.
13 Охрименко Я.М. «Технология кузнечно-штамповочного производства». – М.: Машиностроение, 1976.
14 Скарбинский М.С. «Конструирование отливок». – М.: Машгиз, 1961.
15 Степанов Ю.А. и др. «Технология литейного производства. Специальные виды литья». – М.: Машиностроение, 1987.
16 Титов Н.Д., Степанов Ю.А. и др. «Технология литейного производства». – М.: Машиностроение, 1985.
17 «Литейное производство». Уч.пособие./Под ред. Куманина Н.В.-М.: Машиностроение, 1971.
18 «Литейное производство»/Под ред. Михайлова А.М., Баумана Б.В., Благова Б.Н. и др. – М.: Машиностроение, 1987.
19 Справочник «Ковка и штамповка» /Под ред. Семенова В.Н. в 4-х томах. – М.: Машиностроение, 1985.
Приложение А
|

Приложение Б
|
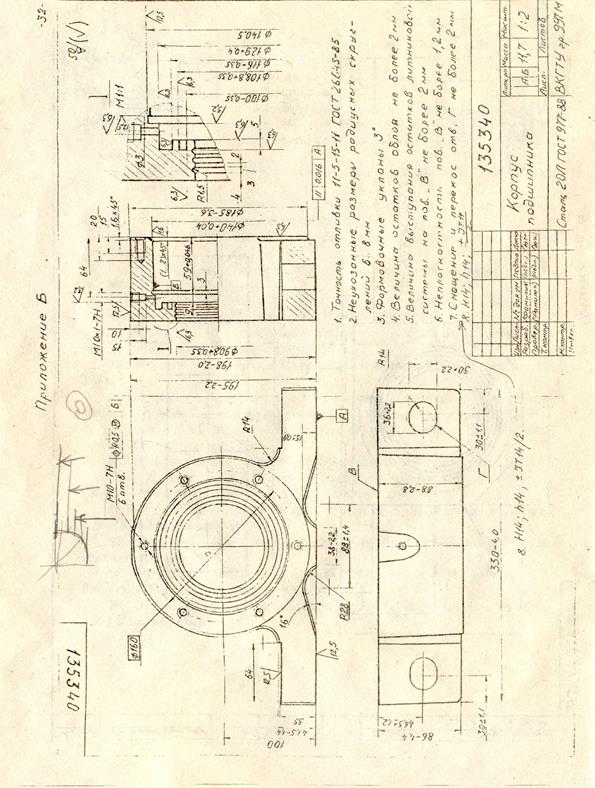
Приложение В
|
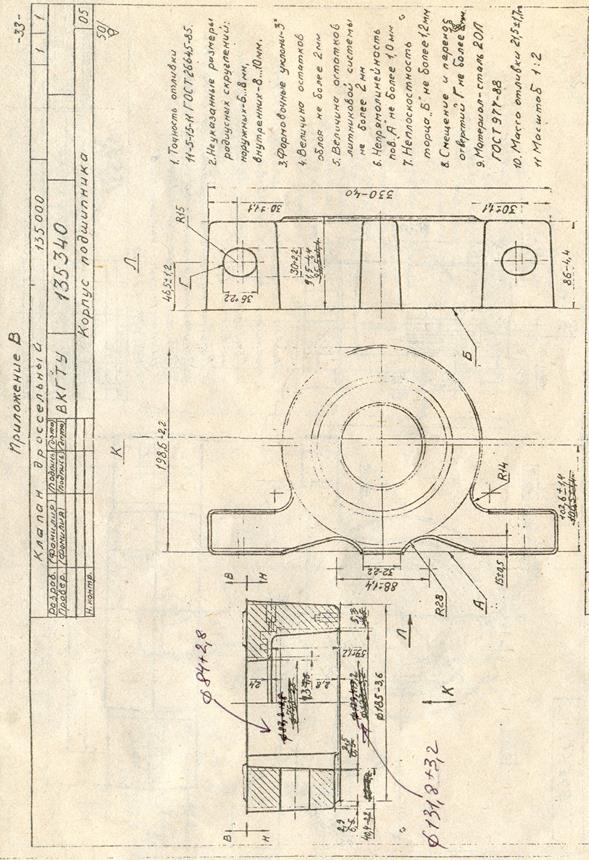
Приложение Г
|

Приложение Д
Дата добавления: 2021-04-05; просмотров: 172; Мы поможем в написании вашей работы! |
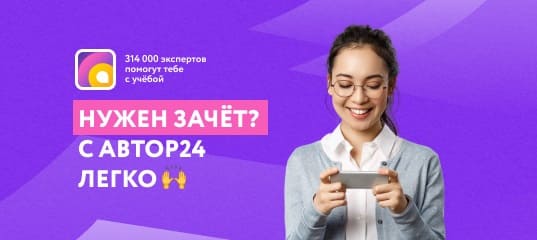
Мы поможем в написании ваших работ!