Стенды для диагностирования коробок передач, раздаточных коробок и главных передач
3.3.1 Стенд для диагностирования по мощности. КПД трансмиссии и ее составляющих – эффективный и наиболее объективный показатель качества ее конструкции. Однако применяемые в настоящее время стенды для испытаний трансмиссии не позволяют оперативно измерять данный показатель: на стендах нет устройств для определения мощностей на валах трансмиссии. Поэтому измеряют только крутящие моменты и частоты вращения, а затем уже по ним вычисляют мощности, передаваемые этими валами.
Такая работа не только трудоемка, но и не дает точных результатов, поскольку погрешности измерения моментов и частот вращения обычно весьма значительны.
Разработано устройство измерения мощности, которым можно оборудовать стенды испытания трансмиссий. Общая схема стенда с таким устройством показана на рисунке 3.21. Схема включает кинематически соединенные с валами испытываемой трансмиссии 24 двигатель внутреннего сгорания 1, электрический тормоз 45 с обмоткой 46 возбуждения, установленные на ведомом валу датчик частоты вращения 26 и широтно-импульсный модулятор 43 момента, установленные на ведущем валу датчик 3 частоты вращения, широтно-импульсный модулятор 22 момента, регулируемый источник 49 напряжения постоянного тока, магнитный усилитель 47 с обмоткой 48 управления (обмотка подключена к выходу источника 49 напряжения, магнитный усилитель 47 своим выходом – к обмотке 46 возбуждения электрического тормоза).
|
|
Стенд имеет канал 42 обработки информации, поступающей с ведомого вала, и канал 21 обработки информации, поступающей с ведущего вала. Каждый из каналов включает транзисторы 32 и 8, резистор нагрузки 29 и 6, сглаживающий фильтр 30 и 7, при этом коллекторные выходы транзисторов соединены с положительным выводом выхода соответствующего датчика частоты вращения, а эмиттер – с отрицательным выводом выхода соответствующего широтно-импульсного модулятора момента и с выводом резистора нагрузки. Базы 34 и 10 транзистора посредством резисторов 33 и 11 подключены к положительному выводу широтно-импульсного модулятора момента, выводы 25 и 2 резисторов нагрузки – к отрицательному выводу соответствующих датчиков частоты вращения. Сглаживающие фильтры соединены с выводами 9 и 33.
Рисунок 3.21 – Стенд для диагностирования по мощности
Каждый широтно-импульсный модулятор момента включает металлические диски (соответственно 14 и 23, 38 и 44) с радиальными прорезями, закрепленные на валах трансмиссии, импульсные щелевые преобразователи (13 и 15, 37 и 39), установленные вблизи вала, вычитающий элемент 16 и 40, выполненный на двух резисторах, выпрямитель 17 и 41 и параллельно подключенный к нему резистор 12 и 36. КПД трансмиссии определяется следующим образом.
|
|
При работе двигателя и отсутствии сигнала в обмотке 46 возбуждения электрического тормоза ротор тормоза вращается свободно. Регулированием сигнала на выходе источника 49 напряжения постоянного тока устанавливают различные токи возбуждения в этой обмотке и, соответственно, моменты на валах трансмиссии.
Сигналы о величине мощностей на валах трансмиссии формируются каналами 21 и 42 с помощью датчиков частот вращения валов и широтно-импульсных модуляторов обработки информации.
Так, в канале 42 происходит следующее. Положительный сигнал с выхода датчика 26 частоты вращения поступает на коллектор транзистора 31, положительный сигнал от широтно-импульсного модулятора момента 43 – на его базу, а отрицательный – на эмиттер. Причем на коллектор сигнал идет непрерывно, на базу – периодически. Очевидно, что при отсутствии сигнала на базе транзистор закрыт, сигнала на резисторе 29 нагрузки тоже нет. Когда же импульс от широтно-импульсного модулятора на базу поступит, транзистор открывается, причем на время, равное длительности поступившего импульса. При этом на выходе резистора нагрузки появляется прямоугольный импульс, высота которого равна уровню напряжения, поступающего от датчика частоты вращения, длительность – длительности импульса, поступающего от модулятора момента. На резисторе 5 нагрузки формируется периодический импульсный процесс с прямоугольными импульсами. Он сглаживается фильтром, на выходе которого и получается сигнал, пропорциональный мощности на ведомом валу. Точно так же работает и канал 21 обработки информации. Только на выходе сглаживающего фильтра этого канала получается сигнал, пропорциональный мощности на ведущем валу. Разделив показания прибора 31 на показания прибора 20 (величину мощности на ведомом валу на величину мощности на ведущем валу), получают КПД трансмиссии.
|
|
Устанавливая движком регулируемого источника питания различные по величине напряжения постоянного тока, а следовательно, и мощности на валах трансмиссии (агрегата) и записывая показания приборов 20 и 31, соответствующие этим мощностям, можно построить зависимость КПД ηтр трансмиссии (агрегата) от мощности Ртр на ее ведомом валу (рисунок 3.22).
|
|
|

Рисунок 3.22 – Зависимость КПД от мощности на ведомом валу
|
|
3.3.2 Стенд для диагностирования по крутящему моменту. При проведении теоретических и экспериментальных исследований коробок передач в исправном и неисправном состояниях было установлено, что статическая характеристика коробок передач на заданной передаче, представляющая собой зависимость крутящего момента на первичном валу коробки передач от крутящего момента на ее вторичном валу в установившемся режиме ее работы, претерпевает изменения в неисправной коробке передач по сравнению с исправной.
Примерный вид полученной зависимости представлен на рисунке 3.23, причем кривая 1 соответствует исправной коробке передач, а кривая 2 – неисправной. При наличии неисправностей в коробке передач при заданном значении момента на ее вторичном валу уровень крутящего момента на ее первичном валу увеличивается.
|
|
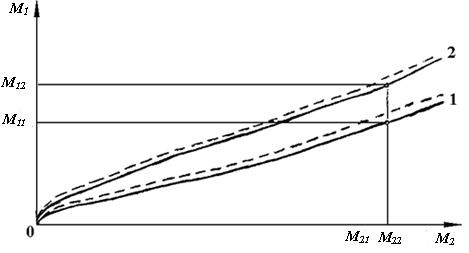
Рисунок 3.23 – Статические характеристики коробки передач
Изложенное выше дало основание предложить новый метод диагностирования механических коробок передач, заключающийся в том, что при заданной величине крутящего момента на вторичном валу коробки передач при ее работе на заданной передаче измеряют крутящий момент на ее первичном валу и, сравнивая его с нормативом, принимают решение о техническом состоянии этой коробки передач.
На основе предложенного метода был разработан стенд (рис. 3.24). Он содержит двигатель внутреннего сгорания 1, кинематически соединенный с первичным валом коробки передач 2, вторичный вал которой соединен с электрическим тормозом 3, первый датчик 4 момента, установленный на первичном валу коробки передач, второй датчик 5 момента, установленный на вторичном валу коробки передач, регулируемый источник 6 постоянного тока, включающий в себя автотрансформатор 7, выпрямитель 8, сглаживающий конденсатор 9, подключенный выходом к обмотке возбуждения 10 электрического тормоза 3. Каждый из датчиков крутящего момента имеет металлические диски с прорезями и выступами 11 и 12, преобразователи импульсные щелевые 13 и 14, установленные вблизи соответствующих валов с возможностью вхождения в их щели металлических дисков 11, 12, резисторы 15, 16, подключенные в противофазе к электрическим выводам преобразователей импульсных щелевых, выпрямители 17, подсоединенные к выходу резисторов, сглаживающие конденсаторы 18, резисторы 19.
Рисунок 3.24 – Стенд для диагностирования коробок передач
Крутящий момент на первичном валу коробки передач измеряется прибором 20, а крутящий момент на вторичном валу – прибором 21.
При пуске двигателя 1 внутреннего сгорания начинают вращаться валы коробки передач, включаются в сеть переменного тока автотрансформатор 7, источники напряжения постоянного тока, питающие преобразователи 13, 14 импульсные щелевые. Вращая движок автотрансформатора по регистрирующему прибору постоянного тока 21, подают на обмотку возбуждения 10 тормоза 3 напряжение постоянного тока такой величины, которое вызывает на вторичном валу коробки передач появление момента, равного по уровню заданному значению.
Металлические диски 11, 12 проходят в щели преобразователей 13, 14, в результате чего на электрических выводах этих преобразователей формируются прямоугольные импульсы одинаковой высоты и длительности. В случае отсутствия момента на валах сигналы на входе резисторов 15, 16 показаны на рисунке 3.25, а. С появлением момента на валах происходит относительное смещение полученных сигналов, т. к. при передаче крутящих моментов валы закручиваются. Импульсы, сформированные преобразователями, установленными у вала, соединенного с тормозом, отстают по фазе от импульсов, сформированных преобразователями, установленными у вала, соединенного с двигателем. Величина фазы отставания импульсов одной последовательности от импульсов второй пропорциональна моменту на данном валу.
На рисунке 3.25, б приведены сигналы, сформированные преобразователями при наличии момента на валах диагностируемой коробки передач. В результате суммирования противофазных импульсов на выходе последовательного соединения резисторов появляется сигнал, состоящий из разнополярных прямоугольных импульсов, длительность каждого из которых пропорциональна моменту на валу. Затем полученный сигнал выпрямляется и сглаживается. Графики сигналов до выпрямления, после выпрямления и сглаживания соответственно представлены на рисунках 3.25, в–д. Если заданное значение момента на вторичном валу равно М2 (см. рисунок 3.23), то на первичном валу диагностируемой коробки появляется крутящий момент, величина которого равна М11 в случае отсутствия неисправностей или М12 в случае наличия неисправностей в диагностируемой коробке передач. Следует учитывать при диагностировании, что КПД агрегата или трансмиссии в целом изменяется при их загрузке (рисунок 3.26).
| |||
|
|
|
|
|
|
|
|
|
|
|
|
|
|
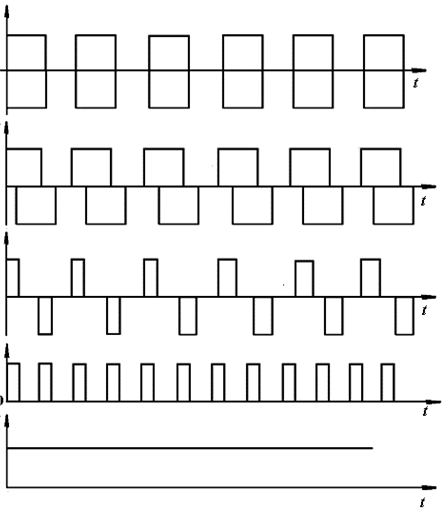
Рисунок 3.25 – Электрические сигналы в цепях стенда
|
|
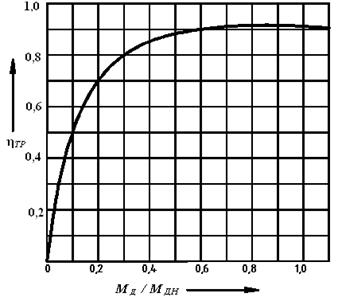
Рисунок 3.26 – Зависимость КПД от относительной нагрузки КП
Данный стенд может применяться для диагностирования как агрегатов, так и трансмиссии в целом, он прост по конструкции, обеспечивает высокую точность результатов диагностирования за счет применения нового метода и средств бесконтактных преобразователей для измерения крутящих моментов на валах диагностируемой коробки передач.
3.3.3 Стенд для диагностирования по амплитудно-частотным характеристикам. Теоретические и экспериментальные исследования механических коробок передач показали, что в процессе их эксплуатации амплитудно-частотная динамическая характеристика данных коробок передач претерпевает изменения из-за появления неисправностей. Это дало основание предложить новый метод диагностирования механических коробок передач на стенде, заключающийся в том, что диагностируемую коробку передач устанавливают на стенд, содержащий ДВС, электрический тормоз, валы, снабженные контрольно-диагностической аппаратурой и измерительными приборами с пультом управления, нагружают валы коробки передач крутящим моментом, включающим постоянную составляющую, равную половине номинального момента, и синусои-дальную составляющую, амплитуда которой меньше уровня постоянной составляющей момента, задают частоту синусоидальных колебаний момента и измеряют амплитуду колебаний момента на вторичном валу, затем, не меняя амплитуду синусоидальной составляющей момента на вторичном валу, измеряют амплитуду колебаний момента на вторичном валу для нескольких фиксированных частот колебаний момента, строят амплитудно-частотную характеристику коробки передач и по ее показателям определяют техническое состояние диагностируемой коробки передач.
Стенд для диагностирования механических коробок передач, общая схема которого изображена на рисунке 3.27, включает в себя следующие основные элементы: двигатель 1 внутреннего сгорания, кинематически соединенный с первичным валом коробки 2 передач, вторичный вал которой соединен с электротормозом 3, первый датчик 4 момента, установленный на первичном валу коробки передач 2, второй датчик 5 момента, установленный на вторичном валу коробки передач, регистрирующие приборы 6 и 7 записывающего типа, например, светолучевые осциллографы K12-22, подключенные к выходам соответствующих датчиков момента, генератор 8 синусоидальных сигналов, регулируемый источник постоянного тока 9, магнитный усилитель 10, выполненный с двумя обмотками постоянного тока, первая из которых подключена к выходу регулируемого источника постоянного тока, вторая – к выходу генератора синусоидальных сигналов. Выход магнитного усилителя подключен к обмотке 11 возбуждения электротормоза 3.
Каждый датчик момента включает в себя два металлических диска 12 и 13, закрепленных на валах неподвижно на некотором расстоянии один относительно другого, преобразователи импульсные щелевые 14 и 15, установленные вблизи валов с возможностью вхождения металлических дисков в их щели, вычитающий элемент 16, выпрямитель 17, конденсатор 18, резистор 19.
|
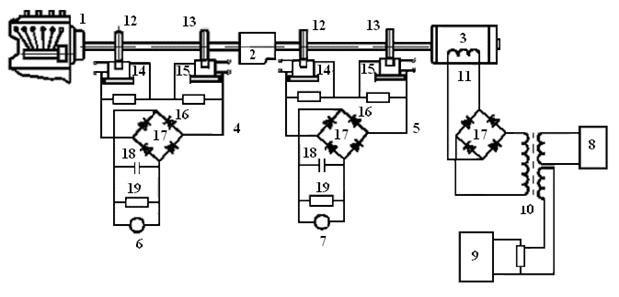
Рисунок 3.27 – Стенд для диагностирования КП
После запуска ДВС 1 приходят во вращение валы коробки 2 передач, на первую обмотку магнитного усилителя 10 от регулируемого источника постоянного тока подается напряжение, уровень которого больше амплитуды синусоидального напряжения, подаваемого на вторую обмотку магнитного усилителя. Напряжение, подаваемое на первую обмотку магнитного усилителя, показано на рисунке 3.28, а, подаваемое на вторую обмотку от генератора синусоидальных сигналов – на рисунке 3.28, б.
На выходе магнитного усилителя формируется сумма напряжений, которая и подается на обмотку 11 возбуждения электротормоза 3. Вследствие этого на вторичном валу коробки передач появляется момент, пропорциональный напряжению, приложенному к обмотке возбуждения 11. Этот момент имеет как постоянную, так и переменную составляющую
(рисунок 3.28, в).
|
|
|
|
|
|
|
|
|
|
|
|
|

Рисунок 2.28 – Сигналы в электрических цепях стенда
Металлические диски 12 и 13 (см. рисунок 3.27) проходят в щели преобразователей 14 и 15, в результате чего на электрических выводах этих преобразователей формируются прямоугольные импульсы одинаковой высоты и длительности, которые вычитаются, выпрямляются, сглаживаются, при этом на резисторах 19 формируется сигнал, пропорциональный моменту на каждом из валов коробки передач. На рисунке 3.28, в буквой A1 обозначена амплитуда переменной синусоидальной составляющей момента на вторичном валу диагностируемой механической коробки передач, буквой w1 – круговая частота этого синусоидального колебания.
Аналитическая запись момента, воспроизводимого на вторичном валу коробки передач:
(3.14)
где М0 – постоянная составляющая момента на этом валу;
A1 и w1 – амплитуда и круговая частота синусоидальной составляющей момента.
На первичном валу коробки передач устанавливается момент, постоянная составляющая которого равна U 20:
(3.15)
где i –передаточное число коробки;
h - КПД коробки на данной включенной передаче.
На первичном валу гармоническое колебание момента имеет амплитуду А2 и фазу j2, поэтому аналитическое выражение для момента на первичном валу коробки передач
(3.16)
Регистрирующими приборами 6 и 7 записываются эти два колебания моментов. Пусть круговая частота в первом опыте равна 0,2 рад/с. Затем по прибору 7 устанавливается новое колебание момента на вторичном валу, имеющее такую же амплитуду A1 и такую же постоянную составляющую М0, но другую круговую частоту w2, равную, например, 0,3 рад/с. Это колебание устанавливается вращением движка регулятора частоты выходного сигнала генератора 8 синусоидальных сигналов. Аналитическое выражение этого момента на вторичном валу коробки передач
(3.17)
Тогда на первичном валу изменяется как амплитуда синусоидальной составляющей момента, так и фаза этой составляющей, при этом выражение для момента на первичном валу примет вид:
(3.18)
По прибору 7 устанавливают одну и ту же амплитуду колебания момента на вторичном валу коробки передач, но, изменяя всякий раз частоту этого колебания, получают колебания момента на первичном валу с разными амплитудами и фазами. Опыт повторяется 10-12 раз. По полученным данным может быть построена амплитудно-фазовая частотная характеристика коробки передач на данной включенной передаче (АФЧХ), а также амплитудно-частотная (АЧХ) и фазочастотная (ФЧХ) характеристики коробки передач.
Для построения АФЧХ в декартовых координатах (рисунок 3.29) следует начертить вектор, начало которого совпадает с началом координат, модуль вектора r1 = A2/A1, а его фаза равна j2 (угол между положительным направлением оси абсцисс и вектором). У конца вектора делается отметка w1.
Для колебания частотой w3 аналогично строится вектор, модуль которого равен A3/A1, а фаза – j3, для колебания момента на вторичном валу с частотой w3 – вектор, модуль которого равен A4/A1, а фаза – j4. Соединяя концы векторов плавной линией, получают кривую, которая называется амплитудно-фазовой характеристикой (АФХ) коробки передач. Имея АФХ, для любой частоты момента на вторичном валу можно найти амплитуду и фазу момента на первичном валу коробки передач. Пусть частота момента на вторичном валу равна w*, на AФX определяется точка с данной частотой и соединяется с началом координат. Измерив полученный модуль по характеристике, рассчитывают амплитуду момента на первичном валу, угол j* определяется графически.
|
|
|
|
|
|
|
|
|
|
|
|
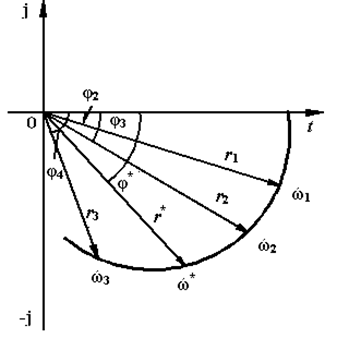
Рисунок 3.29 – Амплитудно-фазовая характеристика коробки передач
АЧХ коробки передач – зависимость амплитуды момента на первичном валу коробки передач от частоты момента на вторичном валу при постоянной амплитуде последнего – определяется следующим образом.
Зависимость Ап / А1 = r = f (w) называется амплитудно-частотной характеристикой. Для её построения по оси ординат откладывается модуль вектора r, по оси абсцисс - частота. Примерный вид АЧХ передачи показан на рисунке 3.30. Частота wр называется резонансной.
Из анализа графической зависимости, представленной на рисунке 3.31, видно, что с увеличением частоты момента на вторичном валу коробки передач от 0 до wр при его постоянной амплитуде амплитуда момента на первичном валу увеличивается, достигая максимального значения при резонансной частоте; при частоте вторичного момента выше резонансной амплитуда момента на первичном валу уменьшается.
|
|
|
|
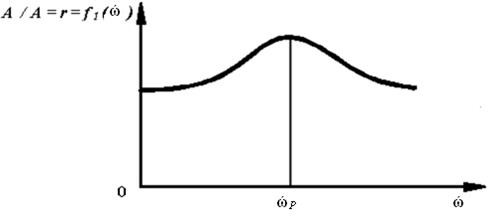
Рисунок 3.30 – Амплитудно-частотная характеристика коробки передач
|
|
|
|
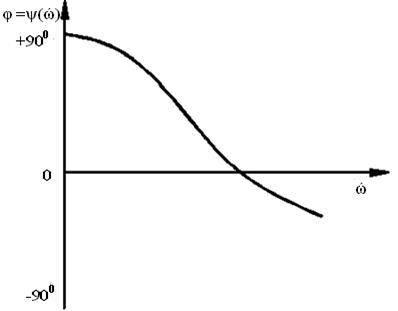
Рисунок 3.31 – Фазочастотная характеристика коробки передач
Фазочастотная характеристика включенной передачи (ФЧХ) может быть определена следующим образом. ФЧХ – это зависимость фазы момента на первичном валу коробки передач от частоты момента на её вторичном валу при постоянной амплитуде последнего. Зависимость j = y(w) и называется фазочастотной характеристикой. Для её построения по оси ординат откладывается угол между колебаниями моментов на валах в градусах, по оси абсцисс – круговая частота моментов. Из анализа графической зависимости, представленной на рисунке 3.31, можно сделать вывод, что с изменением частоты момента на вторичном валу фаза момента на первичном валу претерпевает изменения от +90 до –90°. При частоте момента на вторичном валу, равной резонансной, колебания синусоидальной составляющей на вторичном валу и первичном валу совпадают по фазе (фаза равна нулю).
Аналогично определяются частотные характеристики на других включенных передачах коробки передач. Полученные экспериментально частотные характеристики коробки передач можно использовать для целей диагностирования. Для этого их сравнивают с эталонными характеристиками, полученными для исправной коробки передач.
3.3.4 Стенд для диагностирования гидромеханических коробок передач. Для сокращения затрат на автомобильном транспорте можно применять многие организационные и технические решения, в том числе и внедрение новых инновационных методов и средств диагностирования гидротрансформаторов гидромеханических коробок передач на стендах.
Анализ стендов для диагностирования гидротрансформаторов как составляющих агрегатов гидромеханической коробки передач и их измерительных устройств показал, что они имеют недостатки. Основные измерительные устройства, используемые на известных стендах, выполнены с применением аналоговых элементов, и их использование снижает точность результатов диагностирования.
В результате исследований и анализа полученных результатов испытания гидротрансформатора был предложен новый метод диагностирования гидротрансформатора на стенде, заключающийся в определении его передаточного отношения и сравнении последнего с нормативной величиной, которая соответствует его номинальному коэффициенту полезного действия при нагружении гидротрансформатора номинальным моментом. Для реализации предложенного метода был разработан стенд для диагностирования гидротрансформатора, применение которого обеспечивает высокую точность задания нормативного параметра и определения диагностического параметра.
Стенд (рисунок 3.32) содержит ДВС 1, вал которого соединен с первым упругим валом 2, второй конец которого соединен с насосным колесом гидротрансформатора гидромеханической коробки передач 6, выходной вал этой коробки соединен вторым упругим валом 7 с валом электромагнитного тормоза 9, имеющего обмотку возбуждения 10, систему нагружения, включающую в себя последовательно соединенные автотрансформатор 14 с регулятором 15, трансформатор 13, выпрямитель 12 и конденсатор 11, соединенный с обмоткой возбуждения 10 электротормоза.
Рисунок 3.32 – Стенд для диагностирования гидромеханических коробок передач
На первом упругом валу стенда установлены два диска 3 и 5 с выступами и прорезями, используемые для измерения крутящего момента на ведущем валу гидромеханической коробки передач, а также третий диск 4 с выступами и прорезями для измерения частоты вращения насосного колеса гидротрансформатора. На втором упругом валу установлен четвертый диск 8 для измерения частоты вращения выходного вала гидромеханической коробки передач.
Датчик (рисунок 3.33) крутящего момента содержит два импульсных преобразователя 6 и 19, установленных с обеспечением возможности прохождения прорезей и выступов каждого из дисков 3 и 5 (см. рисунок 3.32) вблизи соответствующего преобразователя, подсоединенные к выходам преобразователей дифференцирующие цепи 8, 17, первая из которых выполнена на двух резисторах 7, 9 и конденсаторе 4 с подсоединенным к ее выходу диодом 5, вторая – на двух резисторах 16, 18 и конденсаторе 15 с подсоединенным к ее выходу диодом 14, триггер 10, выполненный на первом и втором биполярных транзисторах 3, 13 и четырех резисторах 1, 2, 11, 12, интегрирующую цепь 24, выполненную на резисторе 23 и конденсаторе 25, соединенную входом посредством эмиттерного повторителя 20, выполненного на транзисторе 21 и резисторе 22, с выходом триггера 10. При этом к выходу датчика подсоединен измерительный прибор 26 постоянного тока, а базы транзисторов 3, 13 подсоединены к дифференцирующим цепям 8, 17 с диодами 5, 14.
Рисунок 3.33 – Схема датчика крутящего момента
Каждый из цифровых датчиков частоты вращения содержит (рисунок 3.34) катушку 3 индуктивности с магнитным сердечником, жестко закрепленную вблизи прорезей и выступов соответствующего диска 4, 8 (см. рисунок 3.32), первую дифференцирующую цепь 4 с отсекающим диодом 2 на выходе, входом подсоединенную к катушке индуктивности и выполненную на первом и втором резисторах 5 и 6 и конденсаторе 1, вторую дифференцирующую цепь 22 с отсекающим диодом 21 на выходе, выполненную на резисторе 23 и конденсаторе 20, автоколебательный мультивибратор 15, выполненный на первом логическом элементе И-НЕ 7, втором логическом элементе И-НЕ 12, первом конденсаторе 11, втором конденсаторе 10, первом диоде 8, втором диоде 13, первом резисторе 9, втором резисторе 14, шестнадцатиразрядный суммирующий электронный счетчик 24, логический элемент И 18 с двумя входами 16, 17, первым входом 16 соединенный с первой дифференцирующей цепью 4, а вход второй дифференцирующей цепи 22 и второй вход 17 логического элемента И 18 параллельно соединены с выходом автоколебательного мультивибратора 15. Выход логического элемента И18 посредством резистора 19 соединен со счетным входом счетчика 24, выход второй дифференцирующей цепи 22 – со входом установки нуля счетчика 24.
Рисунок 3.34 – Схема датчика частоты вращения
Сопротивления первого и второго резисторов и емкости первого и второго конденсаторов автоколебательного мультивибратора 15 выбраны таким образом, что длительность формируемых на его выходе прямоугольных импульсов равна одной секунде.
Стенд снабжен устройством (рисунок 3.35) микропроцессорной обработки сигналов для определения передаточного отношения гидротрансформатора, включающим в себя микропроцессор 3 с внутренней памятью в виде семи регистров 4, 5, 6, 7, 8, 9, 10 общего назначения, цифроаналоговый преобразователь 19, выход которого соединен с регистрирующим прибором 20, генератор 1 тактовой частоты, таймер 2, соединенные с микропроцессором, буфер 11 адреса, шину 12 адреса, буфер 15 данных, шину 16 данных, шину 17 управления, оперативное 13 и постоянное 14 запоминающие устройства, каждое из которых имеет три канала, интерфейс 18 с пятью каналами, при этом первым каналом интерфейс соединен с первым цифровым датчиком 21 частоты вращения, вторым каналом – со вторым цифровым датчиком 22 частоты вращения, третьим каналом – со входом цифроаналогового преобразователя 19, четвертым каналом – через шину управления с микропроцессором и параллельно через эту шину с первыми каналами оперативного и постоянного запоминающих устройств, вторые каналы которых соединены с шиной адреса, а третьи – с шиной данных, пятым каналом интерфейс соединен через шину данных и буфер данных с микропроцессором, который через буфер адреса соединен с шиной адреса.
Рисунок 3.35 – Схема микропроцессорной системы обработки сигналов
Датчик (см. рисунок 2.33) крутящего момента работает следующим образом. При нагружении первого вала моментом этот вал закручивается на угол, пропорциональный моменту, при этом на выходе триггера формируются прямоугольные импульсы, длительность которых пропорциональна моменту. После интегрирования полученной последовательности прямоугольных импульсов крутящий момент, передаваемый первым валом, определяется прибором 26.
На выходе электронных суммирующих счетчиков формируются цифровые коды, отображающие величины частот вращения первого и второго валов стенда соответственно.
Диагностирование гидротрансформатора производится следующим образом. Устанавливается на стенд диагностируемая гидромеханическая коробка передач. Включается передача, на которой производится диагностирование, передаточное число передачи записывается в первый регистр 4 общего назначения, нагружается двигатель по прибору 26 до величины номинального момента перемещением движка автотрансформатора.
Используя характеристику гидротрансформатора, представляющую собой зависимость коэффициента полезного действия от передаточного отношения, находят передаточное отношение для исправного гидротрансформатора, соответствующее его номинальному коэффициенту полезного действия, и значение передаточного отношения записывают во второй регистр 5 общего назначения микропроцессора.
В третий и четвертый регистры 6, 7 общего назначения записываются коды, отображающие величины частот вращения насосного колеса гидротрансформатора и выходного вала гидромеханической коробки передач соответственно.
По программе, записанной в постоянном запоминающем устройстве, код, записанный в четвертом регистре 7, умножается на передаточное число механической части гидромеханической коробки передач, результат записывается в пятый регистр 8 общего назначения микропроцессора. Это и есть код, отображающий частоту вращения турбины гидротрансформатора.
Далее по программе производится деление кода, записанного в пятом регистре 8 на код, записанный в третьем регистре 6. Результат записывается в шестой регистр 9 общего назначения. Это и есть действительное значение передаточного отношения гидротрансформатора. Вычитая код, записанный в шестой регистр 9, из кода, записанного в первый регистр 4 общего назначения, получают код разности передаточных отношений гидротрансформатора. Этот код регистрируется прибором 20. Если он имеет значение, отличное от нуля, то в гидротрансформаторе имеются неисправности.
Испытания изготовленного стенда состояли в определении статической характеристики первого упругого вала, представляющей собой зависимость угла закручивания упругого вала от приложенного к валу крутящего момента. На основании полученной характеристики первого вала было определено количество выступов и прорезей дисков, установленных по концам данного упругого вала.
Для задания крутящего момента на первом валу, равного номинальному, применен датчик крутящего момента, выполненный в виде дисков и импульсных преобразователей с дифференцирующими цепями. Для формирования прямоугольных импульсов применен триггер, выполненный на двух биполярных транзисторах. Получены осциллограммы прямоугольных импульсов на выходе триггера, установлено, что длительность каждого из импульсов пропорциональна моменту на валу. С помощью интегрирующей цепи последовательность полученных прямоугольных импульсов преобразуется в непрерывный сигнал, уровень которого пропорционален крутящему моменту на данном валу стенда.
Аналогично проведены исследования цифровых датчиков частот вращения валов стенда. Установлено, что цифровые коды, полученные на выходах аналого-цифровых преобразователей, с высокой точностью отображают частоты вращения валов гидромеханической коробки передач.
Применение разработанного стенда для диагностирования гидротрансформатора гидромеханической коробки позволяет снизить затраты на эксплуатацию машин, т. к. с его помощью обеспечивается своевременное определение неисправностей, возникающих в процессе эксплуатации транспортных средств. Как аналоговый измеритель крутящего момента на первом валу стенда, так и разработанный цифровой измеритель частот вращения валов стенда имеет малую стоимость и большую надежность, т. к. являются бесконтактными.
В процессе диагностирования гидротрансформатора гидромеханической коробки передач на разработанном стенде измеряется передаточное отношение гидротрансформатора, сформированное в виде цифровых кодов, и сравнивается с нормативным передаточным отношением гидротрансформатора, также заданного в виде цифрового кода. Этим обеспечивается повышение точности результатов диагностирования гидротрансформатора.
Практическая значимость состоит в том, что создан, испытан и внедрен цифровой измеритель частоты вращения валов, устанавливаемый на стенд для диагностирования гидротрансформатора. Такие измерители совместно с микропроцессорными системами позволяют получить более точные результаты диагностирования гидротрансформаторов за счет повышения точности измерения частот вращения валов стенда.
3.3.5 Стенд для диагностирования главных передач. Установлено, что при увеличении момента на ведомом валу коэффициент полезного действия редуктора (главной передачи) возрастает (рисунок 3.36). При некотором значении момента на ведомом валу коэффициент полезного действия принимает максимальное значение. Это и есть область наиболее эффективного использования редуктора.
На стенде осуществляется также обработка информации, что сопровождается погрешностью из-за применения аналоговых устройств.
|
|
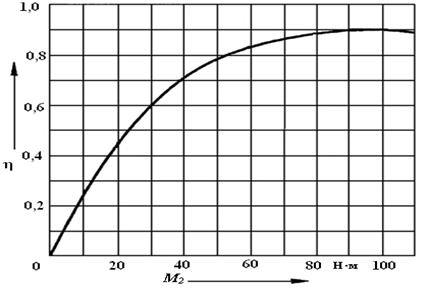
Рисунок 3.36 – Зависимость КПД от нагрузки
Разработанный стенд (рисунок 3.37) содержит привод 1, кинематически соединенный первым упругим валом 2 с ведущим валом редуктора 3, электротормоз 4 с обмоткой возбуждения 5, вал которого кинематически соединен вторым упругим валом 6 с ведомым валом редуктора, первый цифровой датчик 7 момента, установленный на первом упругом валу 2, второй цифровой датчик 8 момента, установленный на втором упругом валу 6, умножитель и делитель, выполненные в виде устройства 9 микропроцессорной системы обработки сигналов, содержащего интерфейс 10 с двумя входами и выходом, микроЭВМ 11, содержащую связанный с интерфейсом 10 посредством шины 12 данных микропроцессор 13 с внутренней памятью в виде восьми регистров 14, 15, 16, 17, 18, 19, 20, 21 общего назначения, дисплей 22, вход которого соединен с выходом интерфейса 10, регулируемый источник 23 постоянного тока с движковым регулятором 24, подключенный к обмотке 5 возбуждения электротормоза 4 и регулирующее устройство 25, выполненное в виде последовательно соединенных программного блока 26 и микро-привода 27, а выходной вал микропривода 27 регулирующего устройства 25 кинематически связан с осью движка регулятора 24 источника 23 постоянного тока.
Рисунок 3.37 – Стенд для диагностирования редукторов
Каждый из триггеров датчиков 7 и 8 момента включает в себя первый и второй металлические диски 28, 29 с одинаковыми радиальными прорезями и выступами, установленные по концам упругого вала, первый 30 и второй 31 импульсные преобразователи, установленные с обеспечением возможности прохождения каждого из дисков 28, 29 возле соответствующего преобразователя 30, 31, соединенные с выходом преобразователей первую и вторую дифференцирующие цепи 32, 33, выполненные на резисторе 34 и конденсаторе 35 с соединенным с их выходом импульсным диодом 36, триггер 37, выполненный на первом и втором транзисторах 38, 39 и четырех резисторах 40, 41, 42, 43, при этом базы и эмиттеры транзисторов 38, 39 соединены с соответствующими выводами выхода первой и второй дифференцирующих цепей 32, 33, триггер 44 со счетным запуском, выполненный на первом 45 и втором 46 транзисторах, диодах 47, 48, аноды которых соединены между собой, а катоды – с соответствующими базами транзисторов 45 и 46, третью дифференцирующую цепь 49, выполненную на конденсаторе 50 и резисторе 51, конденсаторах 52, 53, резисторах 54, 55, 56, 57, 58, 59, при этом два вывода резисторов 58 и 59 соединены между собой, а два других вывода этих резисторов – с базами соответствующих транзисторов 45 и 46 параллельно диодам 47, 48, источнике питания 60. При этом вход третьей дифференцирующей цепи 49 соединен с выходом первой дифференцирующей цепи 32, а ее выход – с катодами диодов 47, 48, источник питания 60 положительным полюсом соединен с отрицательным полюсом напряжения питания триггера 44 со счетным запуском, а отрицательным полюсом – с общим выводом резисторов 58 и 59.
Кроме описанных электронных устройств, в состав обоих датчиков 7 и 8 момента входят четыре дифференцирующие цепи 61, 62, 63, 64, каждая из которых состоит из резистора 65, конденсатора 66, диода 67, четыре логических элемента И 68, 69, 70, 71 с двумя входами, навыходе каждого из которых имеется резистор 72, четыре суммирующих электронных счетчика 73, 74, 75, 76 со счетным входом и входом установки нуля, автоколебательный мультивибратор 77, выполненный на двух транзисторах 78, 79, двух конденсаторах 80, 81, четырех резисторах 82, 83, 84, 85.
Регулируемый источник 23 постоянного тока включает в себя последовательно соединенные автотрансформатор 86, трансформатор 87, выпрямитель 88, конденсатор 89.
Выход триггера 37 датчика момента 8 соединен с первым входом логического элемента 68 и параллельно со входом дифференцирующей цепи 61, выход триггера 44 датчика момента 8 – с первым входом логического элемента 69 и параллельно со входом дифференцирующей цепи 62. Выход триггера 37 датчика момента 7 соединен с первым входом логического элемента 70 и параллельно со входом дифференцирующей цепи 63, выход триггера 44 датчика момента 7 – с первым входом логического элемента 71 и параллельно со входом дифференцирующей цепи 64.
Все вторые входы логических элементов 68, 69, 70, 71 соединены с выходом автоколебательного мультивибратора 77.
Выходы логических элементов 68, 69, 70, 71 соединены со счетными входами суммирующих счетчиков 73, 74, 75, 76 соответственно, а выходы дифференцирующих цепей 61, 62, 63, 64 – с входами установки нуля суммирующих счетчиков 73, 74, 75, 76 соответственно.
Стенд работает следующим образом. После запуска привода 1 начинают вращаться валы испытуемого редуктора 3, включаются регулирующее устройство 25 и регулируемый источник 23 постоянного тока. На обмотке 5 возбуждения электротормоза 4 появляется напряжение, возрастающее по линейной зависимости. На ведомом валу редуктора 3 появляется и изменяется момент (рисунок 3.38), величина которого пропорциональна напряжению, приложенному к обмотке 5, а на ведущем валу редуктора 3 момент М1изменяется по кривой, изображенной на рисунке 3.38.
Принцип действия триггеров 37 как первого, так и второго датчиков момента одинаков, поэтому в работе приводится описание принципа действия одного из них. При включении цифровых датчиков 7, 8 крутящего момента на валах редуктора 3 в исходном состоянии первый транзистор 38 триггера 37 закрыт, вследствие чего второй транзистор 39 триггера 37 открыт из-за наличия положительных обратных связей в триггере 37. Поэтому напряжение на коллекторе первого транзистора 38 U К38 принимает максимальное значение (рисунок 3.39, а), а на коллекторе второго транзистора 39 напряжение U К39 равно нулю (рисунок 3.39, б).
|
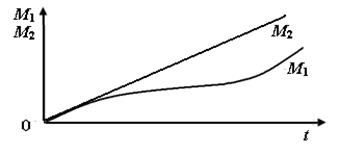
Рисунок 3.38 – Изменение моментов на валах
При вращении упругих валов 2 и 6 с первым диском 28 на выходе первого преобразователя 30 формируется импульс напряжения, который дифференцируется первой дифференцирующей цепью 32, выпрямляется диодом 36, при этом образуется положительный импульс напряжения U Б38 (рисунок 3.39, в), который подается на базу первого транзистора 38. Первый транзистор 38 открывается, а второй транзистор 39 закрывается. На коллекторе второго транзистора 39 появляется положительное напряжение.
При нагружении упругих валов они закручиваются на углы, пропорциональные приложенному моменту. Поэтому второй диск 29 закручивается относительно первого диска 28, вследствие чего на выходе второго импульсного преобразователя 31 формируется импульс напряжения, имеющий фазовое смещение относительно первого импульса, сформированного первым импульсным преобразователем 30. Полученный импульс напряжения дифференцируется второй дифференцирующей цепью 33, выпрямляется диодом 36, образуется положительный импульс напряжения U Б39 (рисунок 3.39, г), который подается на базу второго транзистора 39. Второй транзистор 39 открывается, а первый транзистор 38 закрывается. На коллекторе второго транзистора 39 опять устанавливается напряжение, равное нулю.
|
|
|
|
|
|
|
|
|
|
|
|
|
|
|
|
|
|
|
|
|

Рисунок 3.39 – Сигналы в цепях цифровых датчиков момента
Таким образом, на выходе второго транзистора 39 триггера 37 сформировался прямоугольный импульс (см. рисунок 3.39, б), длительность которого пропорциональна крутящему моменту на валу. Аналогично в процессе вращения упругих нагруженных валов 2 и 6 формируются прямоугольные импульсы, высота которых постоянна, а длительности их в любой момент времени пропорциональны моменту на валу. Эти импульсы подаются на первые входы логических элементов 70 и 68 соответственно от триггеров 37 датчиков момента 7 и 8.
Так как момент на упругом валу определяется фазой отставания второй импульсной последовательности импульсов от первой последовательности импульсов напряжения, а фаза отставания второй последовательности от первой равна отношению длительности полученных прямоугольных импульсов на выходе триггеров с двумя входами 37 к периоду их следования, то необходимо получить период следования импульсов в виде длительности прямоугольного импульса напряжения.
Эта операция выполняется с помощью триггера 44 со счетным запуском, принцип действия которого состоит в следующем (см. рисунок 3.37). Предположим, что до прихода первого импульса от дифференцирующей цепи 49 транзистор 45 закрыт, а транзистор 46 открыт. Тогда потенциал катода диода 47 является более низким, чем потенциал катода диода 48, поэтому при подаче положительного импульса от цепи 49 по диоду 47 начинает протекать ток, который является током базы транзистора 45, и транзистор 45 открывается, а транзистор 46 закрывается. Следующий положительный импульс, приходящий от дифференцирующей цепи, возвращает триггер 44 в исходное состояние. На выходе триггера образуются прямоугольные импульсы напряжения (рисунок 3.39, д), длительность которых равна периоду повторения входных импульсов.
На вторые входы логических элементов И непрерывно подаются короткие импульсы напряжения U К79 от автоколебательного мультивибратора 77 (рисунок 3.39, з), а сформированные импульсы от триггеров 37 и 44 поступают на первые входы логических элементов И соответственно. Короткие импульсы, формируемые на выходе автоколебательного мультивибратора 77, проходят на выходы логических элементов И только за время, равное длительности прямоугольных импульсов, поступающих от триггеров 37 и 44. Число этих коротких импульсов пропорционально величине момента на валах, что изображено на рисунке 3.39, ж, з соответственно. Короткие импульсы подаются на счетный вход счетчиков, подсчитываются последними и преобразуются в цифровые коды.
С выхода счетчика 73 сформированный цифровой код посредством интерфейса 10 и шины 12 данных записывается в регистр 14 общего назначения микропроцессора 13, с выхода счетчика 74 таким же образом – в регистр 15 общего назначения. С выхода счетчика 75 записывается код в регистр 16, а с выхода счетчика 76 – в регистр 17 общего назначения микропроцессора 13. Далее по программе, имеющейся в микроЭВМ, выполняется операция деления цифрового кода, записанного в регистре 14, на цифровой код, записанный в регистре 15, и результат от деления – код момента на ведомом валу – записывается в регистр 18. Аналогично по программе производится деление кода, записанного в регистре 16, на код, записанный в регистре 17. Результат от деления есть момент на ведущем валу редуктора, он записывается в регистр 19. Далее по программе выполняется операция умножения кода, записанного в регистре 19, на передаточное отношение и записывается в регистр 20, выполняется операция деления кодов, записанных в регистре 18, на код, записанный в регистре 20, при этом результат записывается в регистр 21 общего назначения.
Коды в регистре 18 и в регистре 21 общего назначения микропроцессора 13 выводятся на дисплей, после чего содержимое всех регистров обнуляется. На дисплее 22 отображается первая точка зависимости коэффициента полезного действия редуктора от момента на ведомом валу.
Аналогично определяются все остальные точки искомой зависимости и производится ее полное построение на дисплее. Использование полученной зависимости позволяет определить нагрузку на редукторе, при которой обеспечивается в последующей эксплуатации редуктора максимальное значение его коэффициента полезного действия.
Дата добавления: 2021-04-15; просмотров: 314; Мы поможем в написании вашей работы! |
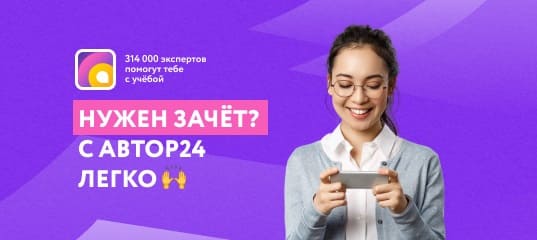
Мы поможем в написании ваших работ!