Сдача вагона экипировочной бригаде после рейса.
Введение.
Для того чтобы время, проведённое в поезде, было комфортным, приятным и безопасным для каждого путешественника, у проводников есть ряд должностных обязанностей. Настоящий СТО ФПК разработан в целях формирования единых требований к качеству обслуживания и предоставлению услуг в пассажирских поездах формирования акционерного общества «Федеральная пассажирская компания» и устанавливает данные требования в зависимости от класса вагона и категории пассажирского поезда.Требования настоящего Стандарта распространяются на филиалы АО «ФПК» и их структурные подразделения, осуществляющие подготовку и экипировку пассажирских поездов в рейс в пунктах формирования и оборота и обслуживание пассажиров в пути следования.Одним из механизмов политики в сфере безопасности движения является Стратегия гарантированной безопасности и надежности перевозочного процесса в холдинге «РЖД», основанная на построении эффективных систем менеджмента безопасности движения, опирающихся на инструменты риск менеджмента и принципы формирования особой культуры безопасности.
Общие сведения по теме.
Перевод подвижного состава железных дорог с винтовой упряжи на автосцепку был начат в 1935 г. и осуществлялся постепенно путем оборудования эксплуатировавшегося подвижного состава автосцепным устройством на ремонтных предприятиях.
В 1957 г. перевод на автосцепку подвижного состава был полностью завершен, что позволило в результате увеличения веса поездов в несколько раз повысить пропускную способность грузонапряженных линий, увеличить переработку вагонов на сортировочных станциях, ускорить оборот вагонов. Была ликвидирована опасная профессия сцепщика вагонов, повысилась безопасность движения поездов вследствие сокращения количества их обрывов (в 50-60 раз).
|
|
Применяемое в настоящее время автосцепное устройство существенно отличается от исходного варианта. Это отличие заключается в значительном повышении прочности деталей, передающих усилие на раму единицы подвижного состава, надежности действия устройства в эксплуатации, энергоемкости поглощающих аппаратов. Указанное повышение достигнуто при обеспечении взаимозаменяемости узлов и деталей автосцепного устройства.
Прочность корпуса автосцепки по сравнению с прежним вариантом, была повышена в три раза путем применения легированных сталей, эффективных режимов термообработки, совершенствования конструкции.
Таким образом, по мере усложнения условий эксплуатации, автосцепное устройство совершенствовалось и в настоящее время в целом удовлетворяет современным требованиям.
|
|
Документы ,регламентирующие процесс обслуживания пассажиров в поездах формирования АО «Федеральная Пассажирская Компания».
Проводник при исполнении своих служебных обязанностей должен руководствоваться требованиями настоящей Инструкции Федерального закона от 10 января 2003 г. № 18-ФЗ «Устав железнодорожного транспорта Российской Федерации»;
Федерального закона от 9 февраля 2007 г. № 16-ФЗ «О транспортной безопасности»;
Правил технической эксплуатации железных дорог Российской Федерации, утвержденных приказом Минтранса России от 21 декабря 2010 г. №286;
Правил пожарной безопасности на железнодорожном транспорте, утвержденных МПС России 11 ноября 1992 г. № ЦУО-112;
Инструкции по обеспечению пожарной безопасности в вагонах пассажирских поездов, утвержденной МПС России 4 апреля 1997 г. №ЦЛ-ЦУ0/448;
Правил оказания услуг по перевозкам на железнодорожном транспорте пассажиров, а также грузов, багажа и грузобагажа для личных, семейных, домашних и иных нужд, не связанных с осуществлением предпринимательской деятельности, утвержденных постановлением Правительства Российской Федерации от 2 марта 2005 г. № 111;
Правил перевозок пассажиров, багажа, грузобагажа железнодорожным транспортом, утвержденных приказом Минтранса России от 19 декабря 2013 г. № 473;
|
|
Санитарных правил по организации пассажирских перевозок на железнодорожном транспорте СП 2.5.1198-03, утвержденных Главным государственным санитарным врачом Российской Федерации 3 марта 2003 г.;
Санитарно-эпидемиологических требований к перевозке железнодорожным транспортом организованных групп детей СП 2.5.3157-14, утвержденных постановлением Главного государственного санитарного врача Российской Федерации от 21 января 2014 г. № 3;
Отраслевых правил по охране труда в пассажирском хозяйстве федерального железнодорожного транспорта ПОТ РО-13153-ЦЛ-923-02, утвержденных МПС России 20 ноября 2002 г.;
Правил по охране труда при эксплуатации электроустановок, утвержденных приказом Минтруда России от 24 июля 2013 г. № 328н;
Инструкции по охране труда для проводника пассажирского вагона структурного подразделения филиала АО «ФПК»;
Инструкции по организации работы нарядов полиции линейных управлений (отделов) МВД России на железнодорожном, водном и воздушном транспорте и работников локомотивных и поездных бригад по обеспечению правопорядка в поездах дальнего следования и пригородного сообщения, утвержденной совместным приказом МВД России и Минтранса России от 27 декабря 2013 г. № 1022/487;
|
|
Распоряжения ОАО «ФПК» от 9 апреля 2010 г. № 71р «О Регламенте организации работы резерва проводников»;
Распоряжения ОАО «ФПК» от 15 марта 2011г. № 193р «О мерах по противодействию актам незаконного вмешательства в деятельность пассажирского железнодорожного комплекса, обеспечению безопасности людей на объектах и транспортных средствах ОАО «ФПК»;
Методических пособий для проводников пассажирских вагонов АО «ФПК» по служебному этикету и культуре обслуживания;
Правила внутреннего трудового распорядка структурного подразделения филиала АО «ФПК»;
Сдача вагона экипировочной бригаде после рейса.
По прибытии пассажирского поезда в пункт формирования проводник обязан:
осмотреть пассажирское помещение вагона; при обнаружении забытых вещей сдать их по акту в камеру забытых вещей;
Сначала работники железной дороги непременно должны убедиться в безопасности оставленного предмета, затем оформить акт общей формы с подробным описанием внешнего вида найденных вещей и обстоятельств их обнаружения. Акт, подписанный начальником (механиком-бригадиром) пассажирского поезда в присутствии проводника вагона, обязательно составляется с участием лица, обнаружившего вещи.
Вещи, забытые и обнаруженные в поездах в пути следования, начальник поезда передает вместе с актом под расписку начальнику станции (вокзала) конечного пункта следования этого поезда. То есть если вещь оставлена в поезде Вологда - Санкт-Петербург, то ее передадут в камеру хранения Ладожского вокзала, а если в поезде Санкт-Петербург - Вологда, то, соответственно, на вокзал в Вологде.
при обнаружении посторонних и подозрительных предметов не прикасаться к ним, незамедлительно сообщить начальнику поезда, организовать охрану, не пользоваться радио- и мобильной связью вблизи предметов;
осмотреть внутреннее оборудование вагона, сообщить о выявленных неисправностях начальнику поезда или поездному электромеханику для принятия мер по их устранению, сделать запись в Журнале приемки, сдачи и технического состояния оборудования пассажирского вагона формы ВУ-8;
сдать нереализованные продукты чайной торговли;
сдать деньги за реализацию платных услуг;
сдать чистое и использованное белье;
собрать постельное белье, утилизировать мусор и шлак в специально отведенном месте на станции;
в зимнее время очистить подвагонное оборудование вагона;
произвести влажную уборку пассажирского помещения и подготовить вагон к посадке пассажиров.
сдать съемное оборудование и инвентарь сменной бригаде или в кладовую, если пассажирский вагон отставляется в резерв;
передать пассажирский вагон сменной бригаде или же дежурному проводнику в парке отстоя вагонов с отметкой об этом в маршрутном листе;
сдать в резерв проводников маршрутный лист, акты, составленные в пути следования;
сделать запись в Журнале приемки, сдачи и технического состояния оборудования пассажирского вагона (формы ВУ-8);
расписаться за время очередного выхода на работу.
Узел.Назначение узла.
Автосцепное оборудование.
Автосцепное оборудование предназначено для сцепления вагонов с локомотивом и между собой, для передачи тяговых и тормозных усилий, сжимающих и ударных нагрузок при движении поезда и при соударении.
Ударно-тяговые приборы относятся к основным и ответственным частям вагона. Они предназначены для соединения вагонов между собой и локомотивом, удержания их на определенном расстоянии друг от друга, передачи и смягчения действий продольных нагрузок (растягивающих и сжимающих), которые возникают при движении поезда и при маневрах.
Тягово-сцепные приборы обеспечивают сцепление вагонов и локомотивов, передачу и смягчение растягивающих усилий. Ударные приборы (буфера) передают и смягчают сжимающие усилия и удерживают вагоны и локомотивы на определенном расстоянии друг от друга.
Приборы, предназначены для непосредственного соединения вагонов и локомотивов, называют автосцепкой, совокупность частей, передающих и смягчающих действие тяговых усилий – упряжью. Если последняя расположена вдоль всего вагона и передает его раме часть тягового усилия, равного сопротивлению данного вагона движению, то такую упряжь называют сквозной. Если упряжные приборы расположены по концам рамы вагона, и она воспринимает все тяговые усилия, передаваемые упряжью, то упряжь называется несквозной, или разрезной. У цистерны разрезная упряжь.
На цистерне установлено автоматическое ударно тяговое сцепное устройство, обеспечивающее сцепление без участия человека.
Переходу к автоматической сцепке способствуют следующие преимущества:
достаточная прочность сцепных приборов, соответствующая большим продольным усилиям, возникающим в поездах большой массы;
ликвидация тяжелого труда сцепщиков, ускорение формирования поездов;
уменьшение тары вагонов тележечной конструкции за счет облегчения концевых и боковых балок рамы. Автосцепное оборудование состоит из: корпуса и расположенных в корпусе механизмов (расцепной привод, ударно – центрирующий прибор, упряжное устройство, поглощающий аппарат, опорные части).
Вагоны и локомотивы магистральных железных дорог РФ оборудованы автоматической сцепкой СА-3 в качестве типовой.
Рисунок 11. Автосцепное устройство грузового вагона
Основные части автосцепного устройства (рис. 11): корпус автосцепки с деталями механизма, ударно - центрирующий прибор, упряжное устройство, упоры и расцепной привод.
Корпус автосцепки 13 с механизмом предназначен для сцепления и расцепления вагонов, восприятия и передачи ударно – тяговых усилий упряжному устройству. Корпус установлен в окно ударной розетки 9 и своим хвостовиком соединён при помощи клина 8 с тяговым хомутом 6.
Корпус автосцепки (рис. 12) представляет собой пустотелую фасонную отливку, состоящую из головной части и хвостовика. Внутри головной части размещены детали механизма автосцепки.
Рисунок 12. Корпус автосцепки СА-3
Она имеет большой 1 и малый 4 зубья, которые, соединяясь, образуют зев. Торцовые поверхности малого зуба и зева воспринимают сжимающие усилия, а тяговые усилия передаются задним поверхностям большого и малого зубьев. На вертикальной стенке зева возле малого зуба имеется окно для замка 3, а рядом – окно для замкодержателя 2. В верхней части головы отлит выступ 5, который воспринимает жёсткий удар при полном сжатии поглощающего аппарата и передаёт его через розетку на раму вагона. Со стороны малого зуба внутри головы отлита полочка для верхнего плеча предохранителя замка от саморасцепа, а со стороны большого зуба имеется шип для навешивания замкодержателя. В нижней части головы выполнены отверстия для выступов замка автосцепки и горизонтальное отверстие для постановки валика подъёмника. В пустотелом хвостовике сделано продолговатое отверстие 6 для клина соединяющего корпус с тяговым хомутом. Торец хвостовика 7 служит для передачи ударных нагрузок и имеет цилиндрическую поверхность, обеспечивающие горизонтальные повороты автосцепки. Горизонтальная проекция зубьев, зева и выступающей части замка называется контуром зацепления.
Центрирующий прибор воспринимает от корпуса автосцепки избыточную энергию удара после полного сжатия поглощающего аппарата и центрирует корпус автосцепки. Прибор имеет ударную розетку 9, две маятниковые подвески 11 и центрирующую балочку 12. Ударная розетка 9 отлита заодно целое с передним упором и приклёпана или приварена к концевой балке рамы. У розетки есть окно для постановки корпуса автосцепки и отверстия для маятниковых подвесок, а также рёбра жёсткости в верхней ударной части. Центрирующая балочка 12 омегообразной формы с двумя плоскостями и двумя ограничителями (продольными и боковыми). Маятниковые подвески 11 имеют вид стержня диаметром 25 мм с двумя головками. Верхними головками подвески опираются на ударную розетку, а на нижние уложена центрирующая балочка.
Упоры автосцепки задние 1 и передние 9 служат для передачи растягивающих и сжимающих усилий на раму и кузов вагона. Передний упор совместно с розеткой представляет собой П - образную коробку с ребрами жёсткости. На расстоянии 625 мм от упорных плоскостей переднего упора к хребтовой балке приклёпан или приварен задний упор 1, который также представляет собой П - образную отливку с рёбрами жёсткости. Для предупреждения истирания вертикальных стенок хребтовой балки поглощающим аппаратом на них между упорами приклёпывают по две предохранительные планки.
Упряжное устройство передаёт упорам продольные силы от корпуса автосцепки и смягчает их действие. Оно размещено между передними и задними упорами автосцепного устройства и состоит из тягового хомута 6, поглощающего аппарата 5, клина 8, упорной плиты 7 и крепёжных деталей клина и поддерживающей планки. Нижней опорой тягового хомута и поглощающего аппарата является поддерживающая планка 4, прикрепляемая восемью болтами снизу к хребтовой балке. Тяговый хомут 6 представляет собой раму,, внутри которой размещён поглощающий аппарат и упорная плита. В головной части хомута имеется отверстие для клина. Внизу головной нижней части расположены приливы с отверстиями для болтов, предохраняющих клин от выпадения. Опорная площадка хомута снабжена усиливающими рёбрами. Клин тягового хомута прямоугольного сечения со скруглёнными кромками в нижней части имеет заплечики, которыми он опирается на болты, удерживающие его от выжимания. Выемки в верхней части боковых поверхностей клина сделаны для уменьшения его массы.
Рисунок 13. Механизм автосцепки
Расцепной привод служит для расцепления автосцепок. Привод представляет собой двуплечий рычаг 3, удерживаемый кронштейном 2 с полочкой и державкой 10. Цепь 14 соединяет короткое плечо рычага с валиком подъёмника 15.
Механизм автосцепки – это замок 1, замкодержатель 2, предохранитель от саморасцепа 3, подъёмник замка 4, валик подъёмника 5 и болт 6.
Замок 1 предназначен для запирания двух сцепленных автосцепок. Он представляет собой плоскую деталь сложной конфигурации. Утолщение его замыкающей части препятствует выжиманию замка из зева внутрь кармана корпуса силами трения при смещении смежных автосцепок.
Вверху замок снабжён шипом (б), служащим для навешивания предохранителя. Внизу замок имеет радиальную поверхность (а), которой он опирается на дно кармана головы корпуса автосцепки и может перекатываться по ней. В средней части замка находится овальное отверстие (в), через которое опускается валик подъёмника. Снизу замка расположены направляющий зуб (г) и сигнальный отросток (д), окрашенный в красный цвет.
Замкодержатель 2 вместе с предохранителем 3 удерживает замок в нижнем положении при сцепленных автосцепках, а вместе с подъёмником 4 фиксирует его в верхнем положении при расцепленных автосцепках до разведения вагонов. Он имеет лапу (ж), овальное отверстие (с) и противовес (т). Лапа замкодержателя взаимодействует со смежной автосцепкой. В собранном виде лапа под действием противовеса выходит в зев автосцепки. Овальное отверстие (с) служит для навешивания замкодержателя на шип, расположенный внутри кармана корпуса. Снизу под овальным отверстием находится расцепной угол (р), взаимодействующий с подъёмником замка.
Предохранитель 3 имеет форму двуплечего рычага. В сцепленном состоянии автосцепок торец верхнего плеча (у) перекрывается упором противовеса замкодержателя, препятствуя уходу замка внутрь кармана и предохраняя автосцепки от саморасцепа. Нижнее фигурное плечо (е) взаимодействует с подъёмником при расцеплении автосцепок. Отверстие предохранителя служит для навешивания его на шип (б) замка 1.
Подъёмник 4 служит для подъёма верхнего плеча предохранителя, увода замка внутрь кармана и удержания его вместе с замкодержателем в утопленном положении. Подъёмник имеет два пальца, из которых широкий (з) за нижнее плечо поворачивает предохранитель, поднимая его верхнее плечо, и уводит замок внутрь кармана, а узкий палец (к) взаимодействует с расцепным углом замкодержателя, удерживает замок внутри кармана до разведения вагонов.
Валик подъёмника 5 предназначен для поворота подъёмника замка при расцеплении автосцепок и удержания подъёмника в вертикальном положении. В средней части валик имеет квадратное сечение. Балансир валика (п) облегчает возвращение его в начальное положение. Отверстие (н) служит для соединения балансира валика с цепью привода, а выемка (о) – для установки запорного болта 6. Стержень валика имеет толстую, тонкую цилиндрическую и квадратную части. В собранной автосцепке цилиндрические части валика располагаются в отверстиях вертикальных стенок корпуса, а квадратная часть входит в соответствующее отверстие (л) подъёмника 4. Болт 6 с двумя гайками и шайбами служит для закрепления валика подъёмника, удержания деталей механизма в собранном состоянии.
Поглощающие аппараты обеспечивают гашение части энергии удара, уменьшение продольных растягивающих и сжимающих усилий, которые передаются через автосцепку на раму кузова.
По типу рабочего элемента, создающего силы сопротивления, и принципу действия поглощающие аппараты делятся на: пружинные, пружинно-фрикционные, с резинометаллическими элементами, гидравлические, эластомерные.
На вагонах железных дорог наибольшее распространение получили пружинно-фрикционные аппараты и аппараты с резинометаллическими элементами. Пружинно - фрикционные аппараты широко применяются на грузовых и пассажирских вагонах, так как они просты по конструкции и надёжны в эксплуатации.
Пружинно-фрикционные аппараты изготовляют по ГОСТ 22253-76. Для четырёхосных грузовых вагонов выпускались пружинно-фрикционные аппараты типа Ш-1-Т (шестигранный, первый вариант, термообработанный). Затем начали изготавливать модернизированные аппараты Ш-1-ТМ. С 1979 г. на грузовые четырёхосные вагоны устанавливают аппараты Ш-2-В (второй вариант, взаимозаменяемый).
Аппараты Ш-1-ТМ, Ш-2-В и Ш-2-Т устанавливают в автосцепное устройство, имеющее стандартное расстояние между передними и задними упорами (625 мм).
Рисунок 14. Поглощающий аппарат
Аппарат Ш-2-В (рис. 14) имеет литой корпус 3, три штампованных фрикционных клина 4, штампованный нажимной конус 1, наружную 5 и внутреннюю 6 пружины и стяжной болт 7 с гайкой 2.
Аппарат работает следующим образом. При сжатии усилием 240 кН клинья начинают перемещаться по горловине внутрь корпуса и сжимать пружины. Между горловиной и клиньями возникают силы трения, пропорциональные давлению между трущимися поверхностями. Давление клиньев на корпус увеличивается по мере сжатия пружин и к концу хода аппарата оно достигает наибольшего значения. Чтобы клинья при своем перемещении не смещались в одну сторону и не перекашивались, горловина корпуса аппарата выполнена шестигранной. Окончанием хода аппарата считается положение, при котором нажимной конус полностью входит в корпус аппарата, а упорная плита касается горловины корпуса. После уменьшения сжимающей силы происходит восстановление (отдача) аппарата за счет упругих сил пружин. Для облегчения возвращения клиньев в исходное положение грани горловины корпуса выполнены с наклоном 2°.
Дата добавления: 2021-07-19; просмотров: 428; Мы поможем в написании вашей работы! |
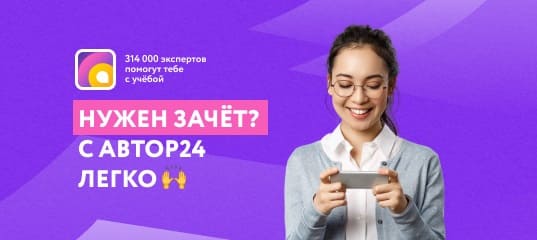
Мы поможем в написании ваших работ!