Р асчет режима резания и построение картограммы
Министерство науки и высшего образования Российской Федерации
Федеральное государственное автономное образовательное
учреждение высшего образования
«Южно-Уральский государственный университет
(национальный исследовательский университет)
Филиал ФГАОУ ВО «ЮУрГУ» (НИУ) в г. Златоусте
Факультет техники и технологий
Кафедра «Электрооборудование и автоматизация производственных процессов»
Проектирование электропривода подачи многооперационного станка
ПОЯСНИТЕЛЬНАЯ ЗАПИСКА
К ИТОГОВОМУ ЗАДАНИЮ
по дисциплине
«Системы управления электроприводами»
13.03.02.2021.343.12.00 ПЗ
| Проверил | |||||||
|
| к.т.н., доцент |
| |||||
|
|
| В.М. Сандалов | |||||
| « » |
| 2021г. | |||||
| ||||||||
| Выполнил студент группы ФТТ-533 | |||||||
| Ф.С. Петров | |||||||
« » |
| 2021 г. | ||||||
| ||||||||
|
Работа защищена с оценкой | |||||||
| ||||||||
« » |
| 2021 г. | ||||||
Златоуст 2021
АННОТАЦИЯ
Петров Ф.С. Расчет привода подачи многооперационного станка. –
Златоуст: ЮУрГУ, ФТТ; 2020, 36с. 19 ил.,
библиографический список–5 наим.
|
|
В данном итоговом задании целью является выбор электродвигателя для металлообрабатывающего станка ИР320ПМФ4. Для этого были произведены расчеты циклограмм работы электропривода, а также построение нагрузочной диаграммы и формирование желаемой механической характеристики с оценкой статических и динамических показателей. На основе которых выбирается электродвигатель с оптимальной работой станка в различных режимах его работы.
СОДЕРЖАНИЕ
Введение. 4
1 Технические данные. 6
2 Расчет режима резания и построение картограммы.. 8
3 Расчет циклограмм. 10
4 Выбор шага винта. 18
5 Выбор двигателя. 20
6 Построение желаемой механической характеристики. 21
7 Моделирование в среде VisSim.. 23
Заключение. 35
Библиографический список. 36
Введение
Данное итоговое задание посвящено расчету электропривода многооперационного станка. Решение данной задачи имеет важное значение, так как от правильности проектирования системы автоматизированного электропривода зависят режимы работы станка, показатели его надежности, точности и времени обработки детали.
Разработка систем электропривода на современном уровне предполагает системный подход к проектированию, моделирование режимов работы с учетом действия технологических факторов. Повышение качества системы возможно только при комплексном подходе, когда выбор отдельных элементов, например, электродвигателя, производится с учетом особенностей построения механической части и системы управления. Особенности системы электропривода, в свою очередь, влияют на режимы работы механической части и системы управления.
|
|
Электроприводы металлорежущих станков с программным управлением являются одним из направлений применения высокоточных систем электро-привода с жесткими технологическими требованиями.
В связи с вышесказанным, в курсовом проекте необходимо решить следующие задачи:
- расчет статических мощностей и моментов;
- расчет циклограмм работы электроприводов станка;
- построение нагрузочной диаграммы привода;
- формирование желаемой механической характеристики электропривода;
- выбор электродвигателя с учетом способа регулирования;
- построение структурной схемы и расчет параметров электропривода;
- оценка статических и динамических показателей системы;
- выбор системы управления электропривода, проверка электропривода на заданные производительность и точность.
|
|
Технические данные
Произвести расчет электропривода многооперационного станка ИР320ПМФ4. Направление подачи – продольная. Вид обработки – растачивание. Материал детали – медь.
В таблице 1 указаны основные параметры многооперационного станка.
Таблица 1 – основные параметры многооперационного станка ИР320ПМФ4
Параметры | Значение |
Размеры рабочей поверхности стола | 500 х 400 |
Наибольшая масса обрабатываемого изделия, кг | 300 |
Наибольшее перемещение стола: продольное поперечное шпиндельной бабки (вертикальное) | 500 500 500 |
Расстояние от оси шпинделя до рабочей поверхности стола | 65…555 |
Расстояние от торца шпинделя до центра стола | 230…730 |
Конус отверстия шпинделя | 45 |
Вместимость инструментального магазина, шт. | 30 |
Наибольший диаметр инструмента загружаемого в магазин | 160 |
Число ступеней вращения шпинделя | 19 |
Частота вращения шпинделя, об/мин | 32…2000 |
Рабочие подачи, мм/мин | 2,5…2500 |
Наибольшая сила подачи стола, кН | 7,5 |
Скорость быстрого перемещения, мм/мин | 5000 |
Мощность электродвигателя привода главного движения, кВт | 4,5 |
Продолжение таблицы 1
|
|
Габаритные размеры: | |
длина | 2790 |
ширина | 2060 |
высота | 2000 |
Масса, кг | 5082 |
Р асчет режима резания и построение картограммы
Карта обработки представляет собой траекторию движения инструмента относительно детали. Размеры детали и инструмента принимаются максимально возможными для геометрии станка и мощности главного привода.
По [1] выбираем расточный державочный упорный резец с углом в плане φ=900 для прямого крепления. Выбранный резец изображен на рисунке 1.1, где В=16, Н=16, L=80.
Рисунок 1.1 – Резец из быстрорежущей стали
На рисунке 1.2 схематически представлено положение шпинделя и рабочего стола.
Рисунок 1.2 – Взаимное положение шпинделя и рабочего стола
На рисунке 1.3 представлена карта обработки.
Рисунок 1.3 – Карта обработки детали
3 Расчет циклограмм
3.1 Расчет режимов резания при растачивании
При назначении элементов режимов резания учитывают характер обработки, тип и размеры инструмента, материал его режущей части, материал и состояние заготовки, тип и состояние оборудования.
Скорость резания V, м/мин при растачивании рассчитывают по эмпирической формуле:
(1)
где Cv – коэффициент, принимаем по таблице 17 ([1], с. 270) Cv=182;
Т – период стойкости инструмента, принимаем 60 мин;
t – глубина резания, мм, t=0,5...2,0 мм, принимаем t= 2 мм;
s – подача, мм/об, принимаем по таблице 12 ([1], с. 265) s=0,3 мм/об;
m – показатель степени, принимаем по таблице 17 ([1], с. 270) m=0,23;
x – показатель степени, принимаем по таблице 17 ([1], с. 270) x=0,12;
y – показатель степени, принимаем по таблице 17 ([1], с. 270) y=0,3;
Кv – коэффициент, является произведением коэффициентов:
, (2)
где Кмv – коэффициент, учитывающий влияние материала заготовки, по таб-
лице 4 ([1], с. 263) Кмv=8;
КПv – коэффициент, учитывающий влияние состояния поверхности, по
таблице 5 ([1], с. 263) КПv=0,9;
КИv – коэффициент, учитывающий влияние материала инструмента, по
таблице 6 ([1], с. 263) КИv=0,74,
Силу резания Р, Н принято раскладывать на составляющие силы, направленные по осям координат станка (тангенциальную Рz , радиальную Ру , и осевую Рх). При растачивании эти составляющие рассчитывают по формуле:
, (3)
где Ср – постоянная, для тангенциальной составляющей Рz по таблице
22 ([1], с.273) Ср=55;
х, у, n – показатели степени, для тангенциальной составляющей Рz по
таблице 22 ([1], с.273) х=1; у=0,66; n=0;
Кр – поправочный коэффициент, определяется по формуле:
, (4)
где Кмр – коэффициент, учитывающий влияние качества обрабатываемого
материала на силовые зависимости, по таблице 10 ([1], с. 265) Кмр=1,7;
Кjр, Кgр, Кlр, Кrр – коэффициенты, учитывающие влияние геометрических
параметров режущей части инструмента на составляющие силы резания,
для тангенциальной составляющей Рz по таблице 23 ([1], с. 275) Кjр=1,08;
Кgр=1,15; Кlр=1;Кrр=0,87.
Значения коэффициентов СР, Кр и показателей степени х, у, n для радиальной и осевой имеют такие же значения, как и для тангенциальной составляющей.
Мощность резания N, кВт рассчитывают по формуле:
(5)
Частота вращения шпинделя , об/мин определяется по формуле:
(6)
где r – радиус обрабатываемого отверстия, примем r=100 мм.
Рабочая скорость при растачивании находится по формуле:
(7)
3.2 Расчет времени обработки
На рисунке 3.1 представлены графики зависимости скорости инструмента и сил от времени.
Рисунок 3.1 – Графики зависимости скорости инструмента и сил от времени
Ускорение до скорости быстрого хода определяется по формуле:
(8)
Принимаем Sразг=S0-1=3 мм, тогда:
Время, затраченное на разгон привода до скорости быстрого хода t, с, определяется по формуле:
(9)
Время, за которое скорость быстрого хода снизится до рабочей скорости, находим по формуле:
(10)
Путь, который пройдет рабочий орган за время t2-3:
(11)
Время быстрого хода инструмента находим по формуле:
(12)
где S – расстояние от заготовки до резца, S=50 мм.
Время, затрачиваемое на врезание в деталь на рабочей скорости:
(13)
где S3-4 – путь, проходимый инструментом за время, затрачиваемое на вре-
зание в деталь на рабочей скорости, принимаем S3-4=1 мм.
Время, затрачиваемое на обработку детали, определяем по формуле:
(14)
где – путь, проходимый инструментом за время, затрачиваемое на обра-
ботку детали, по карте обработки:
Время, требующееся на остановку:
(15)
Разгон до скорости рабочего хода равен времени, требующимся на остановку:
Время, за которое произойдет движение резца в обратном направлении на рабочей скорости:
(16)
Время
На рисунке 3.2 представлена циклограмма работы.
Рисунок 3.2 – Циклограмма движения инструмента
3.3 Расчет сил
Динамическая сила Fдин, Н определяется по формуле:
(17)
где mконс – масса консоли, принимаемая как 40% от массы станка:
(18)
Сила трения скольжения:
(19)
где – коэффициент трения скольжения,
g – коэффициент свободного падения, g=9,8 м/с2.
Сила трения с учетом силы трения в подшипниковых парах и передаче:
(20)
где ηп – КПД подшипника качения, ηп=0,99;
ηпер – КПД передачи винт-гайка ηпер=0,9.
(21)
Вычислим суммарную силу. Результаты сведем в таблицу 2.
Таблица 2 – Значения суммарной силы
Участок | Формула FS i, Н | Результат FS i, Н | Dti, с | (FS i)2×Dti, Н2×с |
0-1 | ![]() | 5394,39 | 0,072 | 2095159,93 |
1-2 | ![]() | 691,29 | 0,56 | 267613,84 |
2-3 | ![]() | -4011,81 | 0,069 | 1110528,74 |
3-4 | ![]() | 1147,70 | 0,25 | 329303,82 |
4-5 | ![]() | 1604,10 | 113,1 | 290764459,53 |
Продолжение таблицы 2
Участок | Формула FS i, Н | Результат FS i, Н | Dti, с | (FS i)2×Dti, Н2×с |
5-6 | ![]() | -4011,81 | 0,0034 | 54721,71 |
6-7 | ![]() | -2176,36 | 0,0034 | 16104,25 |
7-8 | ![]() | -256,43 | 113,35 | 7453481,69 |
8-9 | ![]() | -2176,36 | 0,069 | 326821,46 |
9-10 | ![]() | -256,43 | 0,56 | 36823,55 |
10-11 | ![]() | 1663,50 | 0,072 | 199240,72 |
∑ | 228,01 | 302654259,25 |
Время работы Dt=228,01 с, межоперационное время tмо принимаем tмо=90 с, тогда время цикла tц равно:
(22)
Среднеквадратичная сила Fск определяется по формуле:
(23)
4 Выбор шага винта
Выбираем передачу винт-гайка по динамической грузоподъемности:
(24)
где С – динамическая грузоподъемность передачи винт-гайка качения;
Fmax – наибольшая сила подачи по техническому заданию,
Fmax = 7,5 кН;
Fдин – динамическая сила, Fдин = 4,7 кН.
Выбираем передачу с С=8,9 кН:
Параметры выбранных передач приведены в таблице 3.
Таблица 3 – Параметры передачи
Параметр | Значение |
Номинальный диаметр d01 (d02) , мм | 25 (20) |
Осевая жесткость с1 (с2), Н/мкм не более | 420 (300) |
Шаг резьбы t1 (t2), мм | 5 (8) |
Длина винта lвинта принимается равной 1,5 длины максимального перемещения: то есть lвинта =1,5×630 мм = 945 мм.
(25)
где Smax – максимальное перемещение, по карте обработки Smax = 500 мм.
Масса винта равна:
, (26)
где rст – плотность стали, равная 7,8×103 кг/м3.
Момент инерции винта:
(27)
Частота вращения равна:
(28)
Угловая скорость определяется по формуле:
(29)
Передаточное отношение находим по формуле:
(30)
5 Выбор двигателя
Номинальный момент двигателя определяется по номинальной силе:
(31)
Номинальный момент двигателя:
(32)
По номинальному моменту выберем два двигателя: 2ДВУ115S и 2ДВУ115L, параметры которых приведены в таблице 4.
Таблица 4 – Параметры выбранных двигателей
Параметр | 2ДВУ115S | 2ДВУ115L |
Номинальный момент, H×м | 3,5 | 7 |
Максимальная частота вращения nмах, об/мин | 3000 | 3000 |
Момент инерции двигателя Jдв, кг×м2 | 4,2×10-4 | 7,3×10-4 |
Масса, кг | 6 | 9 |
6 Построение желаемой механической характеристики
Приведённая масса винта и двигателя к режущему органу определяется:
(33)
В результате расчета выбираем двигатель 2ДВУ115L и винт с d01=20 мм, t=8мм.
Приведённая масса винта и двигателя:
Масса консоли:
На рисунке 4.1 представлена предварительная механическая характеристика электропривода.
Рисунок 4.1 – Предварительная механическая характеристика электропривода
По механической характеристике выберем двигательДВУ165М.
При выборе двигателя должны соблюдаться условия:
(34)
(35)
(36)
Допустимая длительная (минутная) перегрузка двигателя не должна превышать удвоенную номинальную силу:
(37)
Допустимая кратковременная (секундная) перегрузка двигателя не должна превышать номинальную силу больше, чем в 4 раза:
(38)
Все условия выполняются, следовательно двигатель выбран правильно.
7 Моделирование в среде VisSim
Перевод в относительные единицы
Момент трения винта на холостом ходу
Момент трения двигателя
Масса стола общая
Скорость двигателя подачи при скорости быстрого хода
Сила трения в шарико-винтовой паре, приведённая к столу
Постоянная механическая
Число пар полюсов принимаем равным р = 4.
Частота пульсации поля, Гц
Период оборота ротора один электрический оборот, с
Самый неблагоприятный случай 15 градусов
Постоянная якоря, с
Принимаем Tя равной
Частота ШИМа принимается равной
Для блока преобразователя, время запаздывания преобразователя
Для блока преобразователя, постоянная фильтрующей цепи
Определим постоянные времени регулятора тока
Частота среза контура регулирования тока (КРТ)
Частота среза контура регулирования скорости (КРС)
Определим постоянные времени регулятора скорости
Коэффициент регулятора скорости Kрс
Скорость двигателя подачи при скорости быстрого хода
За базу напряжения принимаем номинальное напряжение двигателя
Напряжение преобразователя минимальное, в относительных единицах
За базу тока принимаем ток короткого замыкания двигателя
Ток номинальный, в относительных единицах
Ток пусковой (максимальный), в относительных единицах
За базу момента берём момент короткого замыкания двигателя
Момент номинальный, в относительных единицах
Момент XX в винте, в относительных единицах
Момент трения в двигателе и перегрузочный в 2 раза, в относительных единицах
Момент максимальный при подаче стола, в относительных единицах
Базовое значение силы принимаем
Максимальное значение тока в относительных единицах
За базу скорости принимаем скорость холостого хода двигателя
Скорость быстрого хода, в относительных единицах
Скорость максимальная двигателя, в относительных единицах
Скорость рабочая, в относительных единицах
Скорость максимальной подачи, в относительных единицах
Скорость номинальная двигателя, в относительных единицах
За базу пути принимаем путь, пройденный столом на холостом ходу двигателя
Путь максимальный стола, в относительных единицах
Напряжение питания схемы управления
Базовое значение напряжения питания
Сила трения в направляющих, в относительных единицах
Сила трения в винте, в относительных единицах
Сила трения при резании, в относительных единицах
Сила резания, в относительных единицах
Сила динамическая, в относительных единицах
Задание силы резания
На один зуб фрезы приходится сила, считаем, что в работе участвуют 4 зуба
Координата первой точки
Точка касания фрезой детали
Конец врезания
Точка конца полной обработки
Точка выхода фрезы
Частота вращения фрезы
Частота пульсации зубьев
Переводим в относительные единицы силу резания, приходящуюся на 1 зуб
Осевая жёсткость винта, G = 300 Н/мкм.
Полная жёсткость винта, с учётом длины винта, Н
Перевод в относительные величины
Рисунок 6 – Блок «Преобразователь»
Рисунок 7 – Блок «Двигатель»
Рисунок 8 – Блок «Регулятор тока»
Рисунок 9 – Блок «Регулятор Скорости»
Рисунок 10 – Блок «Инструмент»
Рисунок 11 – Блок «Передача»
Рисунок 12 – Блок «Задатчик интенсивности»
Рисунок 13 – Блок «Задание скорости»
При настройке контура тока на вход подаем единичный сигнал, а на выходе снимаем характеристику тока якоря. При подборе параметров регулятора тока добиваемся перерегулирования не более 15% и запаса по фазе около 60о. Настроенный так двигатель будет обеспечивать высокую точность и низкую скорость реакции на возмущения. В данном случае перерегулирование составляет 9%, а запас по фазе 57о.
Рисунок 14 – Результат настройки контура тока
При настройке контура тока на вход подаем скорость быстрого хода в относительных единицах, а на выходе снимаем характеристику скорости двигателя (график справа - синий) и тока якоря (график справа - красный). В данном случае перерегулирование составляет 9%, а диаграмма тока якоря близка к прямоугольной. При включении нагрузки ток резко увеличивается, а скорость падает. В этом случае интегральный канал отрабатывает сигнал и приводит систему к установившемуся режиму на той же скорости.
Рисунок 15 – Результат настройки контура скорости с задатчиком интенсивности при подключенной нагрузке
Рисунок 16 – График зависимости скорости от перемещения
Рисунок 17 – График зависимости скорости от силы
Заключение
Таким образом, в ходе выполнения итогового задания был произведен расчет электропривода подачи многооперационного металлорежущего станка.
Были рассчитаны и построены циклограммы и нагрузочные диаграммы работы электропривода, сформирована желаемая механическая характеристика электропривода.
Был произведен выбор передачи винт-гайка по максимальной силе подачи и выбор электродвигателя по номинальному моменту. Приведенная масса винта и двигателя составила 511,1 кг, при этом масса консоли составляет 2032,8 кг. Выбранный двигатель был проверен по длительно и кратковременно возможным перегрузкам.
Библиографический список
1. Косилова, А.Г. Справочник технолога-машиностроителя / А.Г. Косилова, Р.К. Мещеряков. – М.: Машиностроение, 1986. – 496 с.
2. Кочергин А.И. Конструирование и расчёт металлорежущих станков и станочных комплексов. Курсовое проектирование: Учеб. пособие для вузов. – М.: Выш. шк., 1991. – 382 с.
3. Копылов И.П Справочник по электрическим машинам: В 2 т. Т. 2 / И. П. Копылов, Б. К. Клоков. – М.: Энергоатомиздат, 1989. – 688 с.
4. Усынин Ю.С. Системы управления электроприводов: Учеб. пособие. - Челябинск: Изд-во ЮУрГУ, 2001. – 358 с.
5. Москаленко В.В. Электрический привод: учеб.пособие. – М.: Издательский центр «Академия», 2007. – 368 с.
Дата добавления: 2021-02-10; просмотров: 119; Мы поможем в написании вашей работы! |
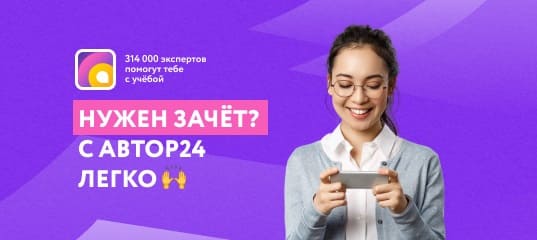
Мы поможем в написании ваших работ!