Виды машиностроительных производств
Расскажите об обогащении руд цветных металлов. Дайте характеристику производства алюминия.
Производство глинозема
n Осуществляется щелочными и кислотными способами. Выбор способа зависит от состава сырья и количества в нем кремнезема.
n При мокром щелочном способе размолотый и просушенный боксит смешивается с каустической содой и загружается в автоклав, где перемешивается при высокой температуре. В результате большая часть алюминия переводится в растворимое соединение (алюминат натрия) и отделяется от других соединений.
n Недостатком этого способа получения глинозема является то, что щелочь расходуется и для связи кремнезема. По щелочному способу перерабатываются бокситы с небольшим содержанием кремнезема.
n В специальных чанах под воздействием воды алюминат натрия охлаждается и распадается с выделением гидроокиси алюминия.
n Гидроокись же алюминия подвергается прокаливанию в трубчатых вращающихся печах, где теряет воду и образуется окись алюминия, или глинозем.
n Бокситы с высоким содержанием кремнезема перерабатывают сухим щелочным способом.
n Боксит смешивается с кальцинированной содой и известняком. Смесь прокаливается во вращающихся печах.
n Кремнезем вступает в соединение с известняком, и образовавшийся шлам удаляется.
n Окислы металлов (алюминия и железа) и остатки кремнезема вступают в соединение с содой с образованием алюмината натрия и других соединений.
|
|
n Путем ряда операций отделяется алюминат натрия, который подвергается дальнейшей переработке по аналогичному способу с мокрым щелочным с получением в итоге глинозема.
Получение алюминия из глинозема
n Осуществляется электролитическим путем.
n Для уменьшения тепловых потерь в электролит загружают криолит, который растворяет глинозем.
n В электролит загружается глинозем в количестве 8—10% от веса электролита и добавляется по мере его расхода при электролизе.
n При пропускании постоянного тока алюминий оседает на дне ванны, он удаляется один раз в сутки с помощью вакуум-ковша.
n Алюминий подвергается хлорированию с целью удаления неметаллических примесей — криолита, глинозема.
n Электролиз глинозема — очень электроемкий процесс.
16. Расскажите о составе хим. промышленности. Дайте характеристику производства серной кислоты: башенный и контактный способы.
Состав химической промышленности
n Химические производства подразделяются на следующие специализированные отрасли:
n А. Химическая промышленность
n 1. Горно-химическая промышленность.
n 2. Основная химия.
n 3. Промышленность химических волокон.
|
|
n 4. Промышленность синтетических смол и пластмасс.
n 5. Лакокрасочная промышленность.
n 6. Промышленность бытовой химии.
n 7. Другие отрасли химической промышленности.
n Б. Нефтехимическая промышленность
n 1. Производство синтетического каучука.
n 2. Производство продуктов основного органического синтеза.
n 3. Сажевая промышленность.
n 4. Резиноасбестовая промышленность.
Каждая из указанных подотраслей имеет свою сырьевую базу, технологию и специфику производства, а производимая продукция — свое экономическое назначение.
Производство серной кислоты. Серная кислота представляет собой тяжелую (удельный вес — 1,84) маслянистую жидкость, легко растворимую в воде.
Трудно найти такую отрасль народного хозяйства, где бы она не применялась. Крупнейшим потребителем серной кислоты является туковая промышленность — производство минеральных удобрений. Па производство суперфосфата и сульфата аммония расходуется более 50% производимой серной кислоты. Серная кислота пригоняется в больших количествах, для производства других кислот и солей, в очистке нефтепродуктов, в различных производствах органического синтеза, в гидролизной, пищевой и текстильной промышленности, в цветной металлургии, в машиностроении и других отраслях промышленности.
|
|
Сырьем для получения серной кислоты являются: природная сера, серный колчедан, или пирит, углекислый колчедан, отделяемый при обогащении углей, медный колчедан, отходящие газы в цветной металлургии и сера, извлекаемая при очистке нефти и природного газа. Основное место в сырьевом балансе занимают отходящие газы цветной металлургии и серный колчедан. Содержание серы в колчедане составляет от 46 до 53%.
Поскольку серная кислота представляет собой соединение серного ангидрида с водой, а сам этот процесс протекает довольно активно, то вся сложность в производстве серной кислоты сводится к получению серного ангидрида, т. е. доокислению сернистого газа. В обычных условиях этот процесс идет крайне медленно. В зависимости от способа окисления сернистого газа существуют два способа получения серной кислоты — башенный (нитрозный) и контактный.
Башенный способ получения серной кислоты применяется в нашей стране с 1805 г. В качестве окислителя применяются окислы азота, которые растворяются в серной кислоте.
В результате их взаимодействия образуется их раствор (нитроза). Процесс окисления сернистого газа нитрозой производится в башнях, имеющих высоту 15-18 м и диаметр 4-10 м, футерованных изнутри кислотоупорным материалом (андезитом). В верхней части башни разбрызгиваются нитроза и вода. Поступающий сернистый газ в результате взаимодействия с нитрозой образует серный ангидрид, который здесь же соединяется с водой с образованием серной кислоты. Расход нитрозы составляет 1—2% от веса вырабатываемой серной кислоты.
|
|
Готовая серная кислота (обычно 75% концентрации) из первой башни поступает по змеевику в холодильник, поскольку имеет высокую температуру (до 250°). Охладившись, она поступает в сборник. Затем серная кислота может поставляться потребителю или подвергаться концентрации путем выпаривания из нее воды. С помощью выпаривания воды ее концентрация доводится до 93—98%. Серная кислота, имеющая концентрацию до 93% —купоросное масло.
Контактный способ (является основным в производстве серной кислоты) основан на применении твердого окислителя, в качестве которого чаще выступает пятиокись ванадия.
Установки и аппаратура для получения серной кислоты этим способом отличаются от тех, что применяются при нитрозном способе (имеются дополнительные газоочистительные аппараты, помещенные в башнях, и др.). Дополнительная очистка газа в основном от окисей мышьяка и селена, связана с тем, что вышеуказанные окислы «отравляют» катализатор, а это замедляет или даже прекращает ход реакции.
Очищенный сернистый газ в смеси с воздухом подается в контактный аппарат, где поддерживается температура около 4500. При таком температурном режиме пятиокись ванадия окисляет сернистый газ в серный ангидрид. Восстановившись, ванадий сразу же превращается в окись за счет кислорода воздуха, снова отдает кислород и снова окисляется. Образующийся серный ангидрид поглощается разбавленной серной кислотой (30%), разбрызгиваемой в специальной абсорбционной башне, и ее концентрация увеличивается до 98% и более.
Преимущество контактного способа получения серной кислоты перед нитрозным в том, что он дает возможность получить высоко концентрированную серную кислоту, не требующую выпаривания воды, и более длительное время использовать аппаратуру. Недостатком является то, что он более дорогой, главным образом за счет большего (в 2—2,5 раза) расхода электроэнергии на 1 т получаемой кислоты. Использование природной серы в качестве сырья но контактному способу значительно упрощает производство, ускоряет технологический процесс и снижает себестоимость продукции.
Расход серы — 0,3—0,35 т или серного колчедана — 0,7 т для, производства 1 т серной кислоты, т. е. меньше выхода готовой продукции. Это обстоятельство и малая транспортабельность серной кислоты определяют целесообразность размещения ее производства в районах потребления. Серная кислота производится на всех суперфосфатных заводах, а также в цехах других предприятий, которые потребляют ее в большом количестве. Сернокислотное производство, работающее на базе отходящих газов, образующихся при обжиге концентратов цветных металлов, комбинируется с предприятиями цветной металлургии. Потребители серной кислоты в этом случае создаются в местах ее производства.
17. Расскажите о технологиях производства минеральных удобрений: фосфорных, азотных и калийных.
Расскажите о технологиях производства минеральных удобрений: фосфорных, азотных и калийных.
Производство минеральных удобрений (туковая промышленность) является самой многотоннажной отраслью химии. Она в основном производит фосфорные, азотные и калийные удобрения. Их производство в 1975 г. составило 90,2 млн. т, а в 1979 г.— 94,5 млн. т (в пересчете на условные единицы).
Для получения суперфосфата используется измельченный фосфорит или апатит, или их смеси и серная кислота 68—70%-ной концентрации. То и другое в определенной пропорции загружается в реакторы непрерывного действия. (Чаще всего это медленно вращающиеся барабаны.) В результате взаимодействия серной кислоты с фосфоритом и апатитом происходят следующие конечные реакции:
Са3 (РО4)2 + 2Н2SО4 = Са (Н2РО4)2 + 2СаS04
ЗСа3 (Р04)2 + СаF2 + 7Н2SО4 = ЗСа (Н2РО4)2 + 7СаSО4 + 2НF
На первом этапе реакции образуются фосфорная кислота и гипс, а часть фосфорита или апатита не реагирует с серной кислотой. На втором этапе образовавшаяся фосфорная кислота взаимодействует с фосфоритом или апатитом и переводит их в кислые фосфаты. Второй этап (вызревание суперфосфата) происходит в камерах хранения в течение нескольких (10—20) суток.
После вызревания суперфосфат содержит кислый фосфат кальция, гипс и небольшую часть непрореагировавшего фосфорита или апатита. Последние два компонента (80% и более по весу) являются балластом, с чем и связано низкое содержание усваиваемой растениями части в простом суперфосфате. Расход серной кислоты при использовании апатитов составляет 0,36 т на тонну простого суперфосфата (в переводе на моногидрат) и 0,53 т — при использовании фосфоритов. Эти обстоятельства определяют и размещение производства простого суперфосфата в районах потребления, а суперфосфатные заводы имеют сернокислотные цехи.
Двойной суперфосфат содержит в 2 раза больше питательного вещества и поэтому более транспортабелен.
Для получения двойного суперфосфата на фосфорит или апатит воздействуют фосфорной кислотой, в результате образуется кислый фосфат кальция.
Фосфорная кислота получается путем воздействия фосфатное сырье кислотами, гл образом серной.
Можно вообще не применять серную кислоту, использовав ортофосфорную кислоту, полученную на базе фосфора. В этом случае фосфор получают возгонкой из его соединений, расходуя до 20 тыс. кВт • ч электроэнергии на производство тонны продукции. Этот путь, получения двойного суперфосфата более дорогой.
Для того чтобы суперфосфат, как и некоторые другие виды удобрений, не слеживался, его гранулируют в комки во вращающихся барабанах с добавлением в суперфосфат небольшого количества воды. Гранулированный суперфосфат легче транспортировать, удобнее вносить в почву, а его потери при перевозках значительно сокращаются. Размещается производство суперфосфата в районах потребления.
Азотная промышленность включает производство аммиака, азотной кислоты, азотных удобрений и некоторых других азотных соединений. Важное значение в азотной промышленности имеет производство аммиачной селитры, важнейшего удобрения сельскохозяйственных полей.
Рассмотрим получение синтетического аммиака. Азот для синтеза аммиака получают из воздуха, отделяя его от кислорода методом глубокого охлаждения и используя разность температур кипения азота (-196°) и кислорода (-183°).
Второй компонент — водород получают сейчас в основном из метана. Для этой цели используют также попутный и коксовый газы. Природный газ — метан смешивается с водяным паром, и при определенных условиях происходит реакция конверсии:
СН4 + 2Н2О=4Н2 + СО2
Расход природного газа в расчете на 1 т аммиачной селитры составляет 400 м3. Синтез аммиака из азота и водорода происходит и специальных колоннах при давлении от 100 до 1000 атмосфер н температуре 450 и более градусов при наличии катализаторов. Чисть аммиака идет на получение азотной кислоты, которая используется для получения аммиачной селитры путем воздействия на аммиак:
НNO3 + NH3 = NH4NO3
Производство азотных удобрений имеет несколько вариантов размещения: в угольных районах (Донбасс, Кузбасс, где ранее использовался для получения водорода и аммиака коксовый газ); и газовых районах (Узбекистан, Северный Кавказ, Поволжье, Украина) и на путях газовых магистралей (БССР, Прибалтика, Центр и др.); в центрах металлургической промышленности при использовании аммиака, получаемого при коксовании угля, азота, извлекаемого из воздуха при производстве кислорода для доменного процесса.
Для производства калийных удобрений в качестве сырья используется ряд минералов, содержащих калий: сильвинит (КС1+NаС1), Где содержится 30% хлористого натрия, карналлит (КС1 • МgС12 • 6Н20) и др.
Основным сырьем калийной промышленности является сильвинит. Его добыча осуществляется открытым или шахтным способом в Белоруссии и Пермской области.
Добытый сильвинит размалывается и поступает на химическую фабрику для разделения входящих в него солей. Этот процесс основан на разности температур их растворения и кристаллизации. При нагревании раствора солей (маточного раствора) способность растворяться и образовывать перенасыщенный раствор у хлористого калия значительно выше, чем у хлористого натрия
При повышении температуры растворимость хлористого калия резко растет, а у хлористого натрия, наоборот, понижается. При охлаждении раствора хлористый калий кристаллизуется и выпадает в осадок.
После охлаждения маточного раствора с помощью центрифуг хлористый калий отделяется от него. Этот процесс повторяется многократно.
Подобным же образом происходит разделение карналлита с получением хлористого калия и хлористого магния. Последний используется для получения магния, а имеющиеся примеси в карналлите (бром, йод) также извлекаются. Хлористый калий имеет большую влажность и для ее удаления просушивается.
Работниками Березниковского 3-го калийного комбината разработан флотационный способ получения хлористого калия. Сущность его сводится к тому, что размолотый сильвинит обрабатывается флотореагентом. Флотореагент выборочно воздействует на частицы хлористого калия и делает их не смачиваемыми водой. Во флотационных машинах при пропускании воздуха через пульпу частицы хлористого калия поднимаются на поверхности и таким образом отделяются от хлористого натрия, который имеет чистоту до 98% и может быть использован для получения хлора и соды.
Производство калийных удобрений размещается в районах сырья, поскольку расход сырья (4—5 т сильвинита и 10—12 т карналлита на 1 т удобрений) значительно превышает выход готовой продукции.
18. Охарактеризуйте производство синтетического каучука и резиновых изделий. Расскажите о технологии производства химических волокон.
Каучук является исходным продуктом для получения резины.
Резина же благодаря своей механической прочности, эластичности, химической стойкости, водогазонепроницаемости применяется почти во всех отраслях народного хозяйства. Сначала использовался только натуральный каучук, состоящий из полиизопрепа. Наша страна является первой страной в мире, получившей синтетический каучук (СК) на базе бутадиена — С4Н6 (дивинила), полученного на основе этилового спирта. Честь открытия принадлежит академику С. В. Лебедеву. Все первые советские заводы СК работали по натрий бутадиеновому способу, расходуя по 2—2,2 т спирта на 1 т СК. Для получения спирта расходовалось пищевое сырье: на 1 т расход составлял картофеля — 10 т, овса — 5т, ржи и пшеницы — 3,6 т, патоки — 3,5 т. Поэтому заводы СК были размещены в зерновой и картофельной зонах.
Бутадиен же стали получать непосредственно из нефтегазового сырья, минуя стадию винного спирта (помимо бутадиена, аналогичными способами получают изопрен, также являющийся сырьем для получения СК), и полимеризовать его со стиролом и другими углеводородами.
Бутадиенстирольный каучук (СКС) производится путем совместной полимеризации бутадиена со стиролом эмульсионным методом. В водную среду, где находятся частички нерастворимых мономеров бутадиена и стирола, вводят различные вещества, которые ускоряют процесс полимеризации. Используя метилстирол, получают бутадиенметилстирольный СК.
Эмульсионным способом также получают хлоропреновый каучук (СКХ) путем полимеризации хлоропрана. Он отличается высокой стойкостью по отношению к растворителям. Исходным сырьем для его производства являются ацетилен и хлористый водород. Полиизопреновый каучук получают полимеризацией изопрена при температуре 30—40° в присутствии катализаторов (лития и др.). По свойствам он превосходит все синтетические каучуки и приближается к натуральному.
Переход к получению дивинила и изопрена для выработки синтетического каучука непосредственно из нефтяных и попутных газов, минуя стадию выработки синтетического спирта, позволил создать новые заводы СК в Закавказье (Сумгаит), Поволжье и Урале (Волжский, Тольятти, Стерлитамак, Нижнекамск, Чайковский), Западной Сибири (Омск), что привело к резкому изменению географии промышленности синтетического каучука. Главным районом его производства на основе месторождений нефти стало Поволжье.
Натуральный и синтетический каучук путем вулканизации перерабатывают в резину. Обычно в состав сырой резиновой смеси входят следующие вещества: каучук, вулканизатор (сера и др.), ускоритель вулканизации, пластификаторы, или мягчители (жирные кислоты, вазелин, сосновая смола, парафин и др.), противостарители (фенолы, воск, фенил), наполнители (сажа, двуокись кремния, называемая белой сажей, цинковые белила, каолин, красители).
Смешивание указанных компонентов производят в закрытых смесителях, представляющих собой камеру, в которой вращаются навстречу друг другу с разными скоростями два ротора (вала или барабана) овальной или трехгранной формы, снабженные гребнями. Камеры и роторы имеют устройство для охлаждения — отвода тепла, выделяющегося при пластификации каучука. Для избежания преждевременной вулканизации серу вводят в конце смешения.
Приготовленную резиновую смесь формируют пропусканием через валки-каландры, в виде непрерывной ленты равномерной толщины, разрезаемой затем на листы. Из сформованной в листы резиновой смеси и прорезиненных тканей вырубают или выкраивают детали и заготовки резиновых изделий. Дальнейшая переработка деталей и заготовок в изделии различна в зависимости от их форм.
Для формирования резиновой смеси применяют также шприц-машины, в которых резиновую смесь продавливают через отверстия, разнообразные по форме и размерам. Так делают резиновые трубы, рукава.
Вулканизация является конечной стадией изготовления резиновых изделий. Вулканизацию каучука можно проводить при обычной температуре (холодная вулканизация) или при нагревании (горячая вулканизация). Холодная вулканизация происходит под действием 2—3%-ных растворов полухлористой серы в течение 1—3 минут. Холодную вулканизацию применяют только для изготовления тонкостенных изделий из резиновой смеси. Горячая вулканизация проводится при +150, + 1600С в прессах или специальных котлах — автоклавах.
Производство химического волокна. Химические волокна являются сырьем для производства тканей и трикотажных изделий. Они требуют меньших затрат человеческого труда Для своего производства и обладают более высокими механическими свойствами по сравнению с натуральными волокнами.
Важной областью применения химических волокон являются шинная, сетевязальная, канатная и другие отрасли промышленности.
Химические волокна делятся на искусственные и синтетические. Первые получают из природных высокомолекулярных соединений, главным образом из целлюлозы, а вторые — из высокополимерных соединений, получаемых на химических заводах. Исходным сырьем для производства таких полимеров служат ацетилен, этилен, фенол и другие вещества, которые получают из природных и нефтяных газов, нефти и каменноугольной смолы. Среди синтетических волокон наиболее широкое распространение получили капрон, нейлон, лавсан, нитрон, полихлорвиниловые волокна и другие.
Искусственные и синтетические волокна получаются в виде бесконечной нити или коротких отрезков нити — штапельного волокна.
Штапельное волокно изготовляют из некрученого волокна, нарезая его на отрезки (штапельки) определенной длины (от 35 до 150 мм), соответствующей длине хлопкового волокна или шерсти.
Штапельное волокно, подобно хлопку и шерсти, представляет собой полупродукт, из которого путем дальнейшей текстильной переработки получают пряжу. Часто штапельное волокно смешивают с хлопком или шерстью и прядут вместе.
Искусственное волокно получают из целлюлозы древесины, по преимуществу ели, в которой содержится до 45% целлюлозы, отходов хлопчатобумажных очистительных заводов (хлопковый пух с содержанием 97—98% целлюлозы) и может быть получено из соломы, камыша и другого сырья, содержащего целлюлозу.
Из 1 т целлюлозы можно получить до 4000 м2 шелковой ткани, а из 1 м3 древесины — до 200 кг целлюлозы, или 160 кг вискозного волокна.
Для получения вискозного волокна используются каустическая сода, сероуглерод, серная кислота, сульфат цинка или натрия. Первоначально целлюлоза обрабатываётся каустической содой в специальных пресс-ваннах. Здесь протекает процесс соединения целлюлозы и щелочи. Образуется комплексное вещество — щелочная целлюлоза.
Листы щелочной целлюлозы отжимаются прессом под давлением 300 атмосфер и измельчаются. Измельченная масса погружается в медленно вращающиеся трубы, где она дозревает в течение суток, и обрабатывается сероуглеродом при температуре 20—25°. Сероуглерод вступает в соединение со щелочной целлюлозой и образует ксантогенат целлюлозы. При его растворении в разведенной натриевой щелочи образуется густая темно-бурая жидкость — вискоза. Она определенное время выдерживается и освобождается от пузырьков воздуха, после чего идет для получения вискозной нити. Вискозный раствор с помощью насосиков продавливается через фильеру. Струйки вискозы попадают в осадительную ванну, где содержится раствор серной кислоты, сульфатов натрия и цинка. Ксантогенат целлюлозы разлагается с образованием вискозного волокна, сероуглерода и образованием сернокислого натрия. Восстановленная вискоза имеет форму нити, которая и наматывается на бобину (катушку). Намотка производится или бобинным способом, или центрифугальным. В последнем случае вискозная нить скручивается с помощью центрифуги. Полученное вискозное волокно далее идет для получения корда или отправляется на текстильные предприятия. Для получения 1 т вискозного волокна расход сырья составляет: целлюлозы (91,5%) — 1,2 т, едкого натра (92%)—0,93 т, серной кислоты— 1,34 т, сероуглерода — 0,34 т, сульфата цинка — 0,16 т. Как видно, производство вискозного волокна связано с большим расходом каустика и серной кислоты. Другой разновидностью искусственного волокна является ацетатное волокно. Оно обладает рядом ценных свойств: высокой механической прочностью, эластичностью, водостойкостью, пропускает ультрафиолетовые лучи.
Для получения ацетатного волокна используются целлюлоза, уксусная кислота, ацетон и спирт. Целлюлоза обрабатывается уксусным ангидридом в присутствии уксусной и серной кислот. Образуется ацетилцеллюлоза, которая в просушенном виде представляет собой белую хлопьевидную массу.
Ацетилцеллюлоза растворяется в смеси ацетона и спирта. При пропускании указанного раствора через фильеры происходит образование нитей ацетатного волокна, ацетон и спирт быстро испаряются, а ацетилцеллюлоза затвердевает. Испаряющиеся ацетон; и спирт улавливаются и снова используются в производстве.
Синтетические волокна получают путем синтеза простых углеводородов — продуктов переработки каменного угля (бензол), нефти, попутного и природного газа.
Синтетическое волокно капрон получают из полиамидных смол. Исходным сырьем для получения полиамидных смол является белое кристаллическое вещество — фенол. Путем взаимодействия фенола с различными добавками получают капролактам, который подвергают полимеризации. Процесс происходит в автоклавах при давлении 15 атмосфер и температуре 260°. В результате образуются молекулы капрона. Обычно на предприятия, выпускающие капрон, поставляется капролактам, который подвергается полимеризации. Образующаяся полиамидная смола продавливается через фильеры. В обычных условиях полиамидная смола застывает и поэтому, пройдя через фильеры, дает прочные нити, которые наматываются на катушки.
Волокно анид (нейлон) получают из соли АГ— белый кристаллический порошок, легко растворимый в; воде. Полимеризация указанной соли дает смолу анид, из которой получают волокно анид.
Для превращения АГ-соли в смолу соль растворяют в дистиллированной воде и добавляют небольшое количество стабилизатора (уксусной или адипиновой кислоты). В специальных аппаратах — автоклавах — происходит поликонденсация АГ-соли и образование смолы. Весь процесс ведут в атмосфере чистого азота. Расплавленную смолу после тщательной отгонки воды (под вакуумом) продавливают через щелевое отверстие в днище аппарата в ванну, заполненную холодной водой. При этом лента смолы застывает. Затем ее сушат, измельчают и направляют на прядительные машины. Там ее плавят при температуре 275—280°. В дальнейшем производство волокна анид аналогично получению капронового волокна.
Волокно анид более теплостойко и упруго, чем капрон, что важно для изготовления кордной ткани.
Все полиамидные волокна характеризуются высокими механическими и физико-химическими показателями.
Волокно нитрон формуют из смолы, получаемой полимеризацией акрилонитрила. Сырьем для синтеза акрилонитрила являются ацетилен (или этилен) и синильная кислота, синтезируемая из аммиака и окиси углерода. Акрилонитрил производится химической промышленностью в больших количествах, так как является одним из исходных материалов (наряду со стиролом и дивинилом) для получения некоторых видов синтетического каучука.
Смолу нитрон в виде мелкого белого сухого порошка растворяют в специальном растворителе. Порошок сначала набухает, а затем при нагревании переходит в раствор, который и является прядильным раствором.
Волокно нитрон обладает рядом ценных свойств. Оно превосходит все остальные волокна по светостойкости, отличается эластичностью, имеет шерстистый вид и пригодно для смеси с шерстью или для замены ее. Изделия из такого волокна хорошо сохраняют тепло.
Производство волокна состоит из трех основных процессов: получения и подготовки смолы, формования волокна и его дальнейшей обработки.
Полиэфирное волокно лавсан получают из смолы лавсан. Смола в виде сухой крошки поступает в прядильный цех. Формование волокна осуществляется на машинах, аналогичных машинам, применяемым в производстве капрона.
Для получения штапельного волокна некрученые нити большого числа прядительных бобин, установленных на специальном шпулярнике, складываются вместе, образуя толстый жгут из нескольких десятков тысяч тонких элементарных волокон. Лавсан по виду и свойствам подобен шерсти; ткани из лавсана носки и не мнутся.
Волокно хлорин получают из ацетилена и хлористого водорода или этилена и хлора. На основе указанных продуктов получают поливинилхлорид, который при обработке хлором превращается в смолу хлорин. Последняя и используется для получения хлорина.
Производство химических волокон энергоемко: затрачивается: от 5 до 13 ту.т.; материалоемко: на 1 т вискозного волокна расходуется 4—5 т целлюлозы и химических материалов. В суммарном грузообороте предприятий промышленности химических волокон удельный вес перевозок топлива составляет 58—86%, перевозок сырья —8—33%, а готовой продукции — всего около 5—13%. На 1т волокна расходуется от 5 до 11 тыс.кВт • ч электроэнергии, до 1200 т воды. Исходя из топливо-энерго-водоемкости производств химических волокон их размещение осуществляется с учетом указанных факторов (Поволжье, Украина, Сибирь и др.).
19. Дайте понятие о машинах–двигателях, рабочих машинах. Расскажите о видах машиностроительных производств. Охарактеризуйте литейное и кузнечно-штамповочное производства.
Машина — это механизм или сочетание механизмов совершающих управляемые целесообразные движения: для производства работы или преобразования энергии.
Исторически машина возникла из простого орудия, каковыми являются топор, лопата, пила, веретено, шило, ведро и т. п. Машина является средством производства, с помощью которого используются природные силы и природные ресурсы. Машинному производству предшествовало мануфактурное производство, при котором использовались лишь отдельные орудия производства, но не машины. Создание и внедрение машин привело к промышленной революции.
Машины облегчают труд человека, делают его более производительным, их широкое внедрение делает возможным производить больше прибавочного продукта и повышать благосостояние народа. Благодаря развитию машинного производства создаются условия преодоления существующих различий между городом и деревней, физическим и умственным трудом. В условиях же капитализма машина является средством производства прибавочной стоимости, средством эксплуатации рабочего класса капиталистами.
Машиностроение — это важнейшая отрасль технического прогресса. Только благодаря машиностроению возможны такие направления технического прогресса, как комплексная механизация и автоматизация производства.
Машиностроение обеспечивает все отрасли народного хозяйства орудиями труда и является основным потребителем металла, пластмасс, резины и другой продукции разных отраслей промышленности.
Общее понятие о машинах . Машина, механизм совершает своими орудиями те же действия и операции, которые ранее теми же орудиями совершал человек.
Для выполнения этих операций машина или система машин должна, во-первых, приводиться в движение, во-вторых, передавать силу движения, в-третьих, иметь соответствующие орудия, воздействующие на предмет. Этим трем операциям соответствуют три части системы машин.
Главное место в системе машин занимает рабочая машина. Именно она воздействует на предмет труда. От ее совершенства зависят полнота и скорость выполняемых операций. Рабочая машина может выполнять только основные операции, часть вспомогательных операций или все операции без содействия человека. Эти ступени развития рабочей машины свидетельствуют о степени механизации и автоматизации процесса.
В век научно-технического прогресса трехзвенная система машин заменяется четырехзвенной системой машин: контрольные функции за работой системы машин берет на себя система машин и приборов. Роль человека в производстве сводится к наблюдению за регулирующим устройством системы машин, пуском их в действие, наладкой.
Все машины могут быть разделены на две группы, или классы: машины-двигатели и машины-орудия (рабочие машины). В зависимости от функции все машины подразделяют на средства производства, предметы потребления, средства обороны. Машины-двигатели преобразуют один вид энергии в другой. Например, энергия воды превращается в механическую, механическая — в электрическую или электрическая энергия превращается в механическую и т. д.
Машины-орудия, воздействуя на предмет, производят изменение формы, свойства и качества предмета труда.
Рабочие машины служат для преобразования какого-либо вида энергии в конкретную работу для обработки данного продукта. Например, металлорежущий станок — это рабочая машина, на которой .с помощью режущих инструментов обрабатываются изделия из металла, пластмассы и других материалов в соответствии с заранее заданной формой и размерами.
Рабочие машины по своему назначению делятся на технологические, применяемые в различных технологических процессах (литейные, кузнечнопрессовые, сварочные, металлорежущие, деревообрабатывающие, текстильные, пищевые, горные, счетные, сельскохозяйственные и др.), транспортные (тепловозы, теплоходы, тракторы, автомобили, самолеты и т.п.), транспортирующие (подъемные и мостовые краны, конвейеры, эскалаторы и др.).
Каждая рабочая машина имеет три основных механизма: двигательный, передаточный и исполнительный.
Двигательные и передаточные механизмы служат для передачи или, вернее, для осуществления движений, необходимых для работы исполнительного механизма.
Если рабочая машина, кроме рабочих ходов, производит без помощи человека и холостые ходы, то такая машина называется автоматом. Автоматизация освобождает человека от тяжелого физического труда. Такие функции, как управление, контроль и регулирование машин, полностью или частично выполняются автоматическими устройствами.
С развитием техники машины становятся все сложнее. Сейчас десятки машин объединяются вместе, происходит комбинирование машин. Создаются угольные, зерновые и другие комбайны, которые осуществляют несколько операций. Усложнение машин осуществляется при одновременной автоматизации их работы.
Виды машиностроительных производств
Машиностроение, как уже отмечено, выпускает самую разнообразную продукцию, начиная от простейших орудий и предметов и кончая сложными автоматическими линиями, авиационной, космической техникой, электронно-вычислительными машинами. Оно обеспечивает все отрасли хозяйства орудиями труда и является основным потребителем металла, пластмасс, а также использует продукцию деревообрабатывающей, легкой, стекольной и других отраслей промышленности. В машиностроении сильно развиты специализация и кооперирование предприятий, что существенно влияет на его размещение.
Для всех машиностроительных производств (предприятий) характерно наличие заготовительных производств (получение литья, поковок, штамповок), которые выделяются в отдельные цехи, обрабатывающих производств (цехов), где осуществляется механическая, термическая, электрохимическая и другие виды обработки деталей, сборочных производств где из поступающих деталей собирают готовое изделие, вспомогательных производств (цехов), которые включают инструментальные, ремонтно-механические, модельные, энергетические, тарные, транспортные и другие цехи. Вспомогательные цехи обеспечивают нормальную работу основных цехов, обеспечивая их инструментом, тарой, энергией, моделями и т. п., своевременно ремонтируя оборудование. Отдельные производства (цехи) в составе предприятия могут отсутствовать, если завод, кооперируясь с другими предприятиями, получает заготовки, тару и т. п.
Производимая машиностроительными заводами продукция может быть массовой, а может быть единичной. В зависимости от количества изготавливаемой продукции все производства делятся на три вида: единичное, серийное и массовое.
При единичном производстве изделие изготовляется в одном экземпляре.
Серийное производство имеет дело с изготовлением изделий партиями или сериями, которые единообразны по размерам и конструкции. Количество деталей в партии или количество машин в серии может быть различным. Массовым производством называют такое, в котором при большом количестве одинаковых изделий производство их ведется непрерывно. При этом виде производства за каждым станком закреплена одна операция, отсутствуют переналадки станка для других операций, станки расположены по технологическому процессу. Оборудование можно применять специальное, широко используют специальный режущий и измерительный инструмент, можно ввести автоматическое транспортирование деталей.
Машины и механизмы состоят из соединенных между собой деталей. Деталь—это составная простейшая часть машины. Отдельные машины, например самолет, имеют более 100 тыс. деталей. Детали различаются по форме, размеру, назначению и материалу. К каждой детали предъявляются требования по надежности и долговечности. По своему назначению детали машин подразделяются на: корпусные,— это рамы, стойки, станины, коробки и др., детали для передачи движения —.валы, оси, зубчатые колеса, шкивы, шатуны, муфты и другие, крепежные детали — болты, гайки, шурупы, шпонки и т.п. Применяются также поддерживающие детали — кронштейны, упоры, стойки.
Литейное производство — процесс получения деталей или заготовки путем заливки жидкого металла в соответствующие, заранее приготовленные формы, соответствующие нужной заготовке иди детали. Полученная деталь, называется отливкой.
Большинство литых деталей получают из серого чугуна благодаря его высоким литейным качествам. Применяется также стальное литье и цветное литье. В литейном производстве применяют три рода форм: разовые, полупостоянные и постоянные.
Разовые формы изготовляют из формовочных песчано-глинистых смесей. Чтобы освободить застывшую готовую отливку, такие формы разрушают после каждой заливки. Полупостоянные формы — керамические — применяют при отливке изложниц, плит и других деталей простой конфигурации. Они выдерживают от 5 до 100 заливок металла.
Постоянные формы — из чугуна или стали — используют для изготовления нескольких сот тысяч отливок простой и средней конфигурации из чугуна, стали и цветных металлов.
Кроме отливки. в земляные формы, получили распространение другие способы литья; а) литье в металлические формы (кокили), б) литье под давлением, в) центробежное литье, г) точное, или так называемое прецизионное, литье и др.
В разовых земляных формах отливается до 90% литых заготовок. Для производства отливок земляных формах необходима модель изделия. Модели изготавливают из дерева, металла и других материалов. Учитывая усадку заливаемого металла, модель делают больше, чем должна быть отливка (на 1—2%).
Стержневой ящик — форма для изготовления литейных стержней, создающих внутреннюю полость отливки. Стержневые ящики — деревянные или металлические — обычно делают из двух половин, в разъеме который; создается внутренний профиль детали, увеличенный с учетом усадки металла.
Опоки — бездонные ящики (рамки), в которых создается. форма. Делают их из дерева, иногда из чугуна или алюминиевый сплавов. Для удержания смеси у больших опок внутри делают вспомогательные ребра.
Формовочные и стержневые смеси, необходимые для изготовления разовых форм и стержней, состоят из смеси песка и глины. Для связи смесей добавляют спиртосульфидную барду, минеральные и растительные масла, цемент и другие крепители. Расход формовочных смесей в 4—8 раз превышает объем отливок. В целях экономии расхода свежего песка и глины в большом количестве используют старую землю из выбитых форм. Формовку производят ручным или машинным способом. Машинная формовка применяется главным образом при массовом и серийном литье. При этом механизируют в основном две операции: 1) заполнение и уплотнение смесей в опоках, 2) извлечение моделей из форм.
Изготовление стержней можно производить ручным или машинным способом. Для прочности стержни снабжают металлическими каркасами. Установку стержней в форму производят после удаления моделей. Литниковая система, т. е. каналы, по которым расплавленный металл будет поступать в форму, создается специальными моделями при формовке.
Для получения хорошей отливки исходный материал должен обладать текучестью, т. е. расплавленный металл должен хорошо заполнять литейную форму, малой усадкой — большая усадка металла дает в отливке раковины, трещины, т.е. приводит к браку, легкоплавкостью — чем меньше температура плавления металла или сплава, тем легче получить отливку.
Чугун занимает первое место среди литейных материалов. Серый чугун — самый дешевый из применяемых в литейном производстве металлов и сплавов.
Стальное литье занимает второе место в литейном производстве. Литейные свойства стали уступают литейным свойствам чугуна (температура плавления — около 1500°, меньшая текучесть, усадка — до 2,5 %), Но стальные отливки имеют высокую прочность и вязкость.
Для производства отливок из цветных металлов применяют главным образом сплавы алюминия, магния и меди. Невысокая температура плавления, большая текучесть сплавов цветных металлов являются их отличительными особенностями.
Кокильное литье представляет собой литье в постоянные металлические формы. Заполнение металла происходит под действием его силы тяжести. Получаемые отливки имеют чистую нарушенную поверхность, большую точность размеров, идентичность деталей, залитых в одну и ту же форму.
Литье под давлением является разновидностью кокильного литья. Этот способ обеспечивает большую точность размеров отливок, в большинстве своем не требующих дальнейшей, механической обработки. В ряде случаев применяют вакуумное литье, выкачивая из формы воздух.
При центробежном литье залитый в форму металл подвергают действию центробежных сил вследствие вращения формы вокруг своей оси. Отливки, полученные этим способом, имеют большую плотность и высокое качество.
Литье по выплавляемым моделям применяется для мелких деталей и режущего инструмента. Модель изготавливают из легкоплавкого материала (воск, парафин, стеарин и др.) в гипсовых или металлических формах.
Прогрессивной формой литья является литье в оболочковые (корковые) формы. Они состоят из двух тонкостенных оболочек, скрепленных между собой. Технологический процесс сводится к следующему. Металлическую плиту с закрепленной на ней половинкой металлической модели нагревают до 220—280°, смазывают ее эмульсией, чтобы не пристыла формовочная масса, и засыпают формовочной смесью (песок со смолой).
Соприкасаясь с горячей моделью, смола, оплавляясь, обволакивает песчинки, и смесь становится пластичной, тестообразной. При дальнейшем нагреве в печи до 250—380° слой смеси затвердевает, смола переходит в неплавкое состояние. Обе полуформы скрепляют и устанавливают для заливки. После затвердевания металлокорковая форма разрушается, а отливка освобождается. Применение коркового литья в 10 раз сокращает расход формовочной смеси.
Кузнечно-штамповочное производство В машиностроении много деталей получают давлением — ковкой, штамповкой и прессованием. Результат ковки — металлическая заготовка нужной формы, которая называется поковкой. Основными операциями свободной ковки (свободная ковка — изготовление одиночных поковок) являются: осадка, вытяжка, прошивка, рубка, изгибание, закручивание, кузнечная сварка.
При осадке уменьшается длина заготовки, а поперечное сечение увеличивается. Если осадка производится на одном участке заготовки, то ее называют высадкой. Вытяжка увеличивает длину поковки за счет уменьшения поперечного сечения. Прошивкой получают сквозные отверстия в заготовке. Рубкой отделяют от заготовки часть металла. Изгибанием (гибкой) заготовку изгибают под необходимым углом. Закручиванием изгибают часть заготовки по отношению к другой вокруг общей оси. Кузнечной сваркой соединяют в одно целое куски металла или концы заготовки. В месте соединения производят нагрев до пластического состояния, затем ударами молота или давлением соединяют свариваемые концы.
Горячая штамповка (штамповка — обработка материалов давлением с помощью специальных штампов) более целесообразна при серийном и массовом производстве. Штамповка в десятки раз производительнее свободной ковки. Стоимость же штампов окупается в короткий срок. Штамповку с предварительным подогревом называют горячей штамповкой. Холодная штамповка производится без подогрева. При штамповке заготовка изменяет форму при сдавливании ее между нижним и верхним штампами, в которых вырезана обратная копия готовой поковки. Течение металла здесь ограничено рабочей поверхностью полости (ручья) штампа. Такую штамповку называют объемной в отличие от листовой, где исходный материал — прокатанные листы, полосы или свернутые в рулоны ленты. Холодная объемная штамповка (холодная высадка или выдавливание) применяется для изготовления мелких металлических изделий: заклепок, болтов, гаек, шурупов, шплинтов, железнодорожных костылей, шариков и роликов подшипников качения, гвоздей, колец, пробок и т. д. Исходными материалами при этом являются проволока и калиброванные прутки из стали, цветных металлов и их сплавов.
Холодную высадку производят в основном на кузнечно-высадочных автоматах, дающих точность, близкую к точности деталей, изготовленных на металлорежущих станках. Листовая штамповка дает большую точность размеров поковки и почти не нуждается в дальнейшей механической обработке.
Штампы для листовой штамповки имеют две основные части: нижнюю неподвижную часть — матрицу, которая крепится к основанию штампа, и пуансон — подвижную часть штампа. Для отделки поверхности поковки, повышения точности ее размеров и получения точного веса применяют чеканку (калибровку), являющуюся отделочной операцией. Чеканку выполняют в специальных штампах с ручьями, форма которых соответствует конфигурации поковки и требуемым размерам.
Кузнечнопрессовое оборудование включает молоты и прессы. Молот — машина ударного действия, деформирующая металл. Мощность молота определяется весом падающих частей. В зависимости от способа подъема падающих частей молоты делят на пневматические, паровоздушные и рычажные (штамповочные — паровоздушные, фрикционные и винтовые). Кроме того, молоты подразделяют на молоты простого и молоты двойного действия. Первые производят удар только за счет веса падающих частей, а вторые, кроме энергии падающих: частей, имеют дополнительные усилия (пара, воздуха).
Прессы воздействуют на поковку не ударом, а давлением. При работе они не вызывают сотрясения почвы и более глубоко деформируют металл, чем при ковке. К ним относятся гидравлические прессы, парогидравлические, фрикционные, винтовые.
Дата добавления: 2021-01-20; просмотров: 106; Мы поможем в написании вашей работы! |
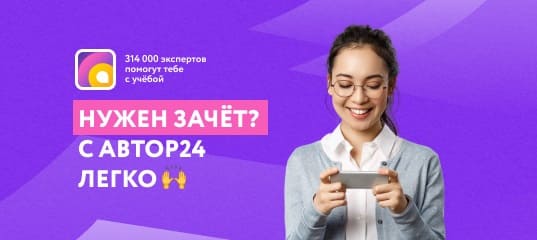
Мы поможем в написании ваших работ!