Перспективы развития литейного производства
Литье под давлением.
Сущность процесса заключается в получении отливок путем заливки расплавленного металла в металлическую форму (пресс-форму) под принудительным внешним давлением от 30 до 100Мпа. Конечное давление на расплав может достигать 490Мпа. Давление снимается после полного затвердевания отливки в пресс-форме.
Материалы и оснастка:
- пресс-форма
- смазка (машинное масло)
- прессующая машина
Основные технологические операции:
- Очистка пресс-формы.
- Нагрев пресс-формы до 120…2200С и покрытие поверхности смазкой.
- Сборка пресс-формы.
- Залив расплавленного металла в камеру прессования и запрессовка расплава под давлением в полость пресс-формы.
- Охлаждение и затвердевание отливки под внешним давлением.
- После затвердевание отливки внешнее давление снимается и извлекается отливка.
Область применения:
Используется для изготовления отливок цветных металлов сложной конфигурации с тонкими стенками массой до 45кг.
Применяется в машиностроении.
Преимущества:
- получают сложные тонкостенные отливки
- низкая шероховатость поверхности, следовательно, снижается механическая обработка отливок на 90-95%
- высокая точность геометрических размеров
- мелкозернистая структура
- улучшенные санитарно-гигиенические условия
Недостатки:
- высокая стоимость пресс-формы, сложность ее изготовления
- наличие газовоздушной пористости
|
|
- ограничение номенклатуры получения отливок по размерам и массе.
Центробежное литье заключается в заливке металла во вращающуюся форму вокруг своей оси. Центробежными силами металл разбрасывается к стенкам формы, образуя пустотелую отливку высокой плотности.
Преимущества данного способа:
- Высокая производительность;
- Высокое качество отливки;
- Высокий коэффициент использования металла из-за отсутствия литников, выпоров и малых припусков на механическую обработку.
Недостатки:
- Затруднено получение отливок из сплавов, склонных к ликвации;
- Загрязнение внутренней поверхности отливок неметаллическими включениями;
- Дорогостоящее оборудование;
- Возможна отливка только тел вращения.
В автомобилестроении данным методом изготовляют заготовки поршневых колец, золотниковые втулки, тормозные барабаны и т.п.
Оболочковые формы применяют при массовом производстве отливок небольших размеров (до 1 м и массой до 200 кг), как правило тонкостенных. Литье в оболочковые формы заключается в том, что поворотный бункер заполняется формовочной смесью, состоящей из 92-95 % мелкого кварцево го песка и 5-8 % бакелитового порошка. Подогретую до температуры 200-250 °С металлическую модель помещают в поворотный бункер.
|
|
Бункер с формовочной смесью переворачивают таким образом, чтобы нагретая модель оказалась под смесью. Под действием нагретой плиты смола в слое, покрывающем плиту, плавится и спекает песок. Вокруг модели быстро образуется оболочка толщиной 6-8 мм, которую вместе с моделью выдерживают 1 мин в печи при температуре 300-350°С, в результате чего она приобретает необходимую прочность. При обратном повороте устройства на форме остается корка (оболочка), а избыток смеси остается в бункере. Для завершении реакции затвердевания оболочку вместе с плитой помещают на 30-40 с в печь, нагретую до температуры 250-300 °С. Затвердевшую оболочку снимают с плиты толкателем и спаривают с другой оболочкой (полуформой) зажимами или склеивают. Готовую оболочковую форму заливали металлом. После затвердевания отливки легко освобождаются. В оболочковые формы заливают чугун, сталь, а также сплавы цветных металлов.
Преимущества:
- формовка легко автоматизируется (производительность до 500 шт./ч);
- точность отливок достигает 0,3-0,7 мм на 100 мм линейного размера при высоком качестве обработки поверхности. Поэтому уменьшается или вообще отпадает необходимость механической обработки;
|
|
- расход формовочных материалов по сравнению с формовкой в опоках уменьшается в 8-18 раз, нет необходимости в опоках.
Все это в десятки раз сокращает грузопоток в литейных цехах.
Литье по газифицируемым моделям позволяет изготовлять модели сложной конфигурации без использования стержневого смесеприготовительного оборудования. Литье осуществляется по пенополистирольным моделям, которые не удаляются из формы, а остаются в ней и газифицируются под действием тепловой энергии металла, заливаемого в форму. По сравнению с традиционными, этот метод наиболее экономичен и прогрессивен. Литье по газифицированным моделям в настоящее врем и один из самых перспективных видов литья.
Преимущества:
- высокая точность отливок даже при сложной конфигурации;
- высокое качество и плотность металла в отливке обеспечиваются частичным вакуумированием;
- высокое качество поверхности отливок позволяет в некоторых случаях совсем отказаться от механической обработки, которая была бы необходима при другом способе изготовления;
- минимальные припуски на механическую обработку, если она все же необходима;
- полная идентичность отливок в серии.
|
|
Область применения литья по газифицированным моделям - отливки различной серийности, от единичного производства до промышленных серий массой от 1 до 300 кг, а при штучном производстве - до 1 т.
Материалы отливок: практически все марки чугунов, в том числе износостойкие; стали - от простых углеродистых до высоколегированных, теплостойких и жаропрочных; практически все литейные марки бронз.
Перспективы развития литейного производства
(Для изучения данного вопроса можно дать задание приготовить сообщение по этому вопросу студенту).
(сообщение студента) Литейное производство является основной заготовительной базой машиностроения, его развитие зависит от уровня машиностроительного комплекса в целом. Общее количество предприятий, входящих в машиностроительный комплекс России, составляет около 7500 единиц. Доля машиностроения в общем промышленном выпуске продукции составляет около 20%.
В современных условиях отдельным отраслям промышленности присущи различные темпы развития. Удельная доля отраслей в общем объёме машиностроительного производства составляет: автомобильная – 56%; электротехническая – 14%; тяжелое и энергетическое машиностроение – 8%; химическое и нефтяное машиностроение – 4%; дорожное и коммунальное машиностроение – 3,5%; станкостроение и приборостроение – 2,5%.
Литейное производство выгодно отличается от других заготовительных производств (поковки, штамповки, сварки) тем, что методом литья возможно изготавливать заготовки, максимально приближённые по геометрии к самым сложным деталям машин. При современных литейных технологиях коэффициент использования металла достигает 95-97% в цветном литье и более 80% - в чугунолитейном производстве. Без сомнения, литейное производство и в будущем сохранит лидирующее положение среди заготовительных производств.
В настоящее время в России насчитывается около 1650 литейных предприятий, которые по экспертной оценке произвели в 2006 году 7,68 млн. тонн отливок, в том числе из чугуна – 5,28 млн. тонн, из стали – 1,3 млн. тонн, из цветных сплавов – 1,1, млн. тонн.
Объёмы производства литых заготовок находятся в пропорциональной зависимости от объёмов производства машиностроительной продукции, так как доля литых деталей в автомобилях, тракторах, комбайнах, танках, самолётах и других машинах составляет 40-50%, а в металлорежущих станках и кузнечнопрессовом оборудовании доходит до 80% массы и до 25% стоимости изделия.
Резкое снижение выпуска продукции энергетического, тяжёлого машиностроения, судостроения, металлорежущих, деревообрабатывающих станков и кузнечнопрессового оборудования, тракторов, военной техники и др., начиная с 90-х гг., привело к тому, что выпуск отливок в России сократился с 18,5 млн. тонн в 1985 г. до 4,85 млн. тонн в 2000 г.
Серьёзной проблемой литейного производства остаётся экология. При производстве одной тонны отливок из сплавов чёрных металлов выделяется около 50 кг пыли, 250 кг окиси углерода, 1,5-2 кг окиси серы, 1 кг окиси углеводородов. Весьма важной проблемой является утилизация твёрдых отходов литейного производства. Отработанные формовочные и стержневые смеси, относящиеся к 4-й категории опасности, составляют 90% отходов. Поэтому для каждого предприятия с точки зрения экономической целесообразности и экологической безопасности производства требуется регенерация отработанных смесей в местах их образования. С этой целью необходима срочная реконструкция литейных цехов, которая должна осуществляться на базе новых, экологически чистых технологических процессов и материалов, прогрессивных плавильных агрегатов, смесеприготовительного и формообразующего оборудования, обеспечивающих получение высококачественных отливок, которые будут отвечать европейским и мировым стандартам.
Поэтому необходимо смелее и увереннее использовать отечественное литейное оборудование (формовочные машины, линии)..., отечественные формовочные связующие материалы, лигатуры и модификаторы. Для получения качественных литых заготовок в разовых песчаных формах в России имеются все необходимые исходные материалы (пески, глины, бентониты), выпускаемые Миллеровским, Хакасским, Воронежским, Лужским, Серпуховским горно-обогатительными комбинатами и другими предприятиями.
За последние годы меняются приоритеты в развитии технологических процессов литейного производства в сторону их совместимости с окружающей средой. На первый план выходят экологические аспекты производства, которые определяются вредными выбросами в атмосферу, жёстко регламентируемыми Киотским протоколом.
В последнее десятилетие наблюдается активное вхождение в экономику России и города сборочных электротехнических и автомобильных производств таких компаний, как Электролюкс, Нокиа, Форд, Нисан, Тойота, Дженерал Моторс и других. Заявленная мощность в России к 2010 году автомобильных сборочных заводов должна составить свыше 1,2 млн. единиц техники в год. К этому времени автосборочные производства потребуют примерно 300 тысяч тонн высокоточного литья.
Приведём ещё один факт: по информации группы Volkswagen AG, средний европейский автомобиль имеет массу около 1185 кг, в составе которых имеются следующие материалы: 540 кг листовой стали, 130 кг чугуна, 75 кг поковок, 80 кг легких сплавов, 120 кг пластиков, 90 кг резины, 50 кг стекла, 35 кг краски и 65 кг других материалов. Содержание в среднестатистическом автомобиле деталей из чёрных и цветных металлов, произведенных путём литья, составляет 25-30 % от общей массы машины.
Одним из основных условий размещения в России заводов иностранных автоконцернов является требование о не менее чем 40% локализации производства комплектующих на местных российских предприятиях.
Дата добавления: 2020-12-22; просмотров: 143; Мы поможем в написании вашей работы! |
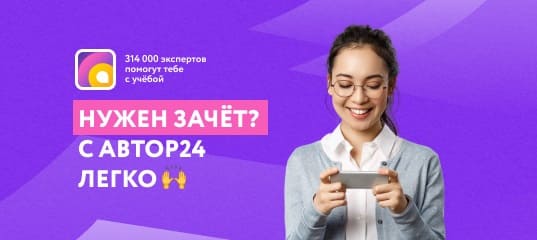
Мы поможем в написании ваших работ!