Оборудование для обработки отверстий
Тема 3.
Сверление, зенкерование, развертывание, нарезание резьбы.
Сверление
Сверление - это слесарная операция, представляющая собой один из видов резания металла с помощью инструмента, называемого сверлом, совершающего вращательные и поступательные движения.
Сверление является весьма распространенной операцией, как на разнообразных машиностроительных заводах, так и в слесарных и механических мастерских, особенно при монтажно-сборочных работах.
Сверление применяют для получения отверстий не высокой степени точности, и для получения отверстий под нарезание резьбы.
Сверление применяется:
- для получения неответственных отверстий невысокой степени точности и значительной шероховатости, например под крепёжные болты, заклёпки, шпильки и т.д.;
- для получения отверстий под нарезание резьбы, развёртывания и зенкерование.
Свёрла бывают различных видов (рис. 3.1 а-и) и изготовляются из быстрорежущих, легированных и углеродистых сталей, а также оснащаются пластинками из твёрдых сплавов.
Сверло имеет две режущих кромки. Для обработки металлов различной твёрдости, применяют свёрла с различным углом наклона винтовой канавки. Для сверления стали пользуются свёрлами с углом наклона канавки 18…30 градусов, для сверления лёгких и вязких металлов – 40…45 градусов, при обработки алюминия, дюралюминия и электрона – 45 градусов.
|
|
Хвостовики у спиральных свёрл могут быть коническими и цилиндрическими.
Конические хвостовики имеют свёрла диаметром 6…80мм. Эти хвостовики образуются конусом Морзе. Шейка сверла, соединяющая рабочую часть с хвостовиком, имеет меньший диаметр, чем диаметр рабочей части.
Свёрла бывают оснащённые пластинками из твёрдых сплавов, с винтовыми, прямыми и косыми канавками, а также с отверстиями для подвода охлаждающей жидкости, твёрдосплавных монолитов, комбинированных, центровочных и перовых свёрл. Эти свёрла изготовляют из инструментальных углеродистых сталей У10, У12, У10А и У12А, а чаще – из быстрорежущей стали Р6М5.
Рис. 3.1. Работы, выполняемые на сверлильных станках: а — сверление отверстий; б — рассверливание; в — зенкерование; г — растачивание; д — зенкование; е — развертывание; ж — выглаживание; з — нарезание внутренней резьбы; и —цекование
Обработка отверстий
После выполнения отверстий в сплошном материале производится их обработка для увеличения размеров и снижения шероховатости поверх-ностей, а также обработка предварительно полученных отверстий (например, литьем, продавливанием и т.п.). Обработка отверстий выполняется несколькими способами, в зависимости от того, какие параметры точности и шероховатости поверхности отверстия заданы чертежом. В соответствии с выбранным способом обработки выбирается и инструмент для ее осуществления.
|
|
При обработке отверстий различают три основных вида операций:
сверление, зенкерование, развертывание и их разновидности:
рассверливание, зенкование, цекование.
Сверление - это операция по образованию сквозных и глухих
отверстий в сплошном материале, выполняемая при помощи режущего
инструмента - сверла. Различают сверление ручное – ручными пневматичес-кими и электрическими сверлильными устройствами (дрелями) и сверление на сверлильных станках. Ручные сверлильные устройства используются для получения отверстий диаметром до 12 мм в материалах небольшой и средней твердости (пластмассы, цветные металлы, конструкционные стали и др.). Для сверления и обработки отверстий большего диаметра, повышения производи-тельности труда и качества обработки используют настольные сверлильные и стационарные станки - вертикально-сверлильные и радиально-сверлильные.
Одной из разновидностей сверления является рассверливание -увеличение диаметра отверстия, просверленного ранее. В качестве инструментов для рассверливания отверстий, также как и для сверления, используют сверла. Не рекомендуется рассверливать отверстия, полученные в заготовке методом литья, ковки или штамповки. Такие отверстия имеют различную твердость по поверхности отверстия из-за окалины, образующейся при литье, а также
|
|
из-за неравномерной концентрации внутренних напряжений в металле на различных участках поверхности отверстий, полученных методом ковки или штамповки. Наличие мест с неравномерной и повышенной твердостью поверхности приводит к изменению радиальных нагрузок на сверло в процессе обработки отверстия, что ведет к смещению его оси, а также является причиной поломки сверла. Обработка отверстий сверлением и рассверливанием позволяет получить точность размеров обработанного отверстия до 10-го квалитета и шероховатость обработанной поверхности
до Rz 80.
Зенкерованием называется операция, связанная с обработкой предварительно просверленных, штампованных, литых или полученных другими методами отверстий с целью придания им более правильной геометрической формы (устранение отклонений от круглости и других дефектов), а также достиже-ния более высокой, по сравнению со сверлением, точности (до 8-го квалитета) и более низкой шероховатости (до Ra 1,25). Зенкерование ведут либо на настольных сверлильных станках (при небольших диаметрах отверстий), либо на стационарном сверлильном оборудовании, устанавли-ваемом на фундаменте. Ручное сверлильное оборудование для зенкерования не применяется, так как оно не может обеспечить получение требуемых точности и шероховатости поверхности. К разновидностям зенкерования относятся зенкование и цекование.
|
|
Основные правила зенкерования отверстий:
• сверление и зенкерование отверстий необходимо производить с одной установки детали (заготовки) на станке, т.е. меняя только обрабатывающий инструмент;
• при зенкеровании необработанных отверстий в корпусных деталях особое внимание следует обращать на надежность установки и прочность закрепле-ния детали;
• необходимо точно соблюдать величину припуска на зенкерование, руковод-ствуясь соответствующей таблицей;
• зенкерование следует производить на тех же режимах, что и сверление;
• необходимо соблюдать те же правила охраны труда, что и при сверлении.
Зенкование - это обработка на вершине просверленных отверстий цилиндри-ческих или конических углублений под головки винтов и заклепок, а также фасок. Операция выполняется при помощи специального инструмента - зенковки.
Основные правила зенкования отверстий:
• необходимо соблюдать правильную последовательность зенкования отвер-стий: вначале просверлить отверстие, а потом осуществить его зенкование;
• сверление отверстия и его зенкование следует производить с одной установки заготовки (детали), сменяя только инструмент;
• зенкование следует выполнять при ручной подаче зенковки и малой частоте вращения шпинделя (не более 100 об/мин) с применением эмульсии, глубину зенкования надо проверять штангенциркулем или линейкой станка;
• при зенковании отверстий цилиндрической зенковкой, когда диаметр цапфы больше диаметра отверстия, необходимо вначале просверлить отвер-стие по диаметру цапфы, а затем зенковать отверстие. Заключительная операция - рассверливание отверстия на заданный размер.
Цекование - это операция по зачистке торцевых поверхностей при обработке бобышек под шайбы, гайки, стопорные кольца. Операция производится с помощью специального инструмента - цековки, которая устанавливается на специальных оправках.
Развертывание - это операция по обработке ранее просверленных отверстий с высокой степенью точности (до 6-го квалитета) и малой шероховатостью (до Ra 0,63). Обработка развертыванием выполняется после редварительного сверления, рассверливания и зенкерования отверстия развертками, которые подразделяются на черновые и чистовые, ручные и машинные. Осуществляется развертывание как вручную, так и на станках, как правило, стационарных. Конструкция инструмента выбирается в зависимости от
применяемого метода обработки.
Основные правила развертывания отверстий:
• необходимо точно соблюдать величину припуска на развертывание, руководствуясь соответствующей таблицей;
• ручное развертывание следует выполнять в два приема: вначале черновое, а затем чистовое;
• в процессе развертывания отверстия в стальной заготовке необходимо
обильно смазывать обрабатываемую поверхность эмульсией или минераль-ным маслом, чугунные заготовки следует развертывать всухую;
• ручное развертывание следует осуществлять только по часовой стрелке во избежание задиров стенок отверстия стружкой;
• в процессе обработки следует периодически очищать развертку от стружки;
• точность обработки развернутых отверстий следует проверять калибрами: цилиндрических - проходным и непроходным; конических- по предельным рискам на калибре. Развернутое коническое отверстие допускается проверять контрольным штифтом «на карандаш»;
•сверление и развертывание отверстий на сверлильном станке машинной разверткой необходимо производить с одной установки заготовки, меняя только обрабатывающий инструмент.
Оборудование для обработки отверстий
Ручное оборудование
Различают следующие типы оборудования для обработки отверстий:
ручное; ручное механизированное; стационарное.
Ручное оборудование - это оборудование, в котором в качестве привода используется мускульная энергия человека; к нему относятся ручные дрели и трещотки.
Электрические дрели (рис. 3.2) легкого типа применяются для сверления отверстий диаметром до 10 мм, среднего типа – диаметром до 15 мм, тяжелого типа-диаметром до 32 мм. При работе электрические дрели легкого и среднего типа удерживают в руках. Электрические дрели тяжелого типа в процессе работы требуют дополнительных приспособлений для их крепления и удерживания. Такими приспособлениями являются различные подвесные
устройства на пружинах и тросах (рис. 3.3), винтовые устройства
с упором (рис. 3.4), а также устанавливаемый на дрель специальный грудной упор, позволяющий использовать мускульную энергию человека.
Электрическая сверлильная машина с угловой насадкой (рис. 3.5)
предназначена для сверления отверстий в труднодоступных местах. На корпус 6 машины установлена трубка 5, которая крепится при помощи гайки 4. С трубкой соединена головка 3, расположенная под углом 90° к трубке и корпусу. Внутри головки 3 расположен шпиндель, на котором установлен трехкулачковый патрон 2 со сверлом 1. Шпиндель соединен с электро-двигателем, находящимся в корпусе 6, при помощи валика 8 и конической зубчатой передачи, которая располагается в головке 3. Включение электрической машины осуществляется кнопкой 7. Головка, устанавливаемая
на сверлильную машину, может иметь также наклон к оси корпуса 45 °.
Рис.3.2. Электрические дрели: а - легкого типа; 6 - среднего типа; в - тяжелого тина
Рис. 3.3. Приспособления для удерживания электрических дрелей тяжелого типа: а - на пружине; б - на тросах
Рис. 3.4. Винтовое устройство с упором
Рис. 3.5. Электрическая сверлильная машина с угловой насадкой: а - машина с головкой 90°; б -- машина с головкой 45 1 — сверло; 2 – трехкулачковый патрон; 3 - головка; 4 - гайка крепления; 5 - трубка; 6 - корпус; 7 - кнопка выключения; 8 - валик
Пневматические дрели (рис. 3.6) выпускаются в двух вариантах:
легкого типа (рис. 3.6, а) и тяжелого типа (рис. 3.6, б). В связи с тем, что привод пневматических дрелей осуществляется от централизованной сети сжатого воздуха или индивидуального компрессора, они позволяют выпол-нять работы самого разного характера в различных условиях, в том числе и в труднодоступных местах.
Рис. 3.6. Пневматические дрели: а-легкого типа, б-тяжелого типа
Наиболее интересные конструкции имеют сверлильные машины моделей
Д-2 и УСМ-25.
Рис. 3.7. Ручная сверлильная пневматическая машина Д-2: 1 - патрон; 2 - насадка; 3 - ротор; 4 - кнопка; 5 - ниппель; 6 – ручка
Рис. 3.8. Ручная сверлильная пневматическая машина УСМ-25: I - сверло; 2 - трехкулачковый патрон; 3 - головка; 4 - корпус; 5 - кнопка пуска; 6 – гайка
Ручная сверлильная пневматическая машина Д-2 (рис. 3.7) имеет частоту вращения шпинделя 2500 об/мин при давлении воздуха в сети 0,5 МПа и массу 1,8 кг. Пневматическая машина имеет ручку 6, ротор 3, насадку 2, патрон 1, кнопку 4 и ниппель 5. Она поставляется с комплектом угловых и кондукторных насадок, которые закрепляются в корпусе машины, что позволяет производить обработку в труднодоступных местах.
Ручная сверлильная пневматическая машина УСМ-25 (рис. 3.8) широко
используется в слесарно-инструментальных, сборочных и ремонтных
работах. Она состоит из корпуса 4, на который навернута головка 3. Внутрь корпуса и головки установлен пневматический редуктор с расположенным на нем под углом 90° шпинделем с трехкулачковым патроном 2 со сверлом 1. Шланг воздухопровода закреплен на резьбовом ниппеле корпуса гайкой 6. Подача воздуха в редуктор машины осуществляется при нажатии кнопки 5.
Стационарное оборудование для сверления
Стационарным называется оборудование, находящееся на постоянном
месте, при этом обрабатываемая заготовка доставляется к нему. К стационарному оборудованию относятся настольные, вертикальные
и радиальные станки.
Настольные сверлильные станки (рис. 3.10) отличаются большим
разнообразием конструкций, однако принцип их действия и
область применения примерно одинаковы. В качестве примера
рассмотрим быстроходный сверлильный настольный станок высокой
точности с микрометрической подачей инструмента, предназначенный
для сверления отверстий диаметром от 0,3 до 4,0 мм.
Рис. 3.10. Настольный сверлильный станок:
а - общий вид; б - узел привода; 1 - стол; 2, 8, 10 - рукоятки; 3 - трехкулачковый патрон;
4 -шпиндель; 5 -хомутик; (5-лимб; 7-кожух; 9 - электрический двигатель; 11 -головка ; 12 - колонна; 13,15,24 - шарикоподшипники; 14 - стакан; 1 6 ,2 2 - шкивы; 17 – переходная втулка; - муфта; 19 - фланец; 20 - винт; 21 - упорная шайба; 23 - шестерня; 25 – нониус
Вертикально-сверлильные станки являются основным и наиболее
распространенным типом сверлильных станков, применяемым для обработки отверстий в деталях сравнительно небольшого размера. Эти станки позво-ляют выполнять следующие виды работ: сверление, рассверливание, зенкеро-вание, зенкование, цекование и развертывание.
Круг этих операций можно существенно расширить, применяя специальный
инструмент.
Рис. 3.11. Вертикально-сверлильный станок мод. 2Н118: 1 - фундаментная плита; 2 - стол; 3 - шпиндель; 4 – коробка подач; 5 - коробка скоростей; б - электрический двигатель; 7 - сверлильная головка; 8 - рукоятка; 9 – колонна
Радиально-сверлильные станки, как и вертикально-сверлильные,
предназначены для обработки отверстий сверлением, рассверливанием,
зенкерованием, зенкованием и развертыванием. При использовании
специальных инструментов их технологические возможности могут быть существенно расширены.
Принципиальное отличие радиально-сверлильных станков от вертикально-сверлильных состоит в том, что при обработке шпиндель может перемещаться относительно обрабатываемой детали в разные стороны. Это обеспечивает обработку тяжелых деталей, установка и выверка положения которых на столе станка требует значительного времени. Такая конструк-тивная особенность радиально-сверлильных станков позволяет обрабатывать тяжелые корпусные детали с большим количеством отверстий, расположен-ных в одной плоскости. Радиально-сверлильные станки являются универ-сальными и применяются, как правило, в условиях мелкосерийного про-изводства.
Наибольшее распространение получили следующие типы радиально-
сверлильных станков.
Рис. 3.12. Радиально-сверлильный станок: а - общего назначения; б - с подвижной колонной; в - на специальной тележке; г –переносной
Радиально-сверлильный станок общего назначения (рис. 3.12, а) имеет вертикально расположенный шпиндель, который может перемещаться
в трех направлениях: вокруг колонны, по радиусам окружности, определя-емым вылетом рукава, и вертикально вдоль своей оси. Заготовка устанав-ливается на столе станка.
Радиально-сверлильный станок
с подвижной колонной (рис.3.12, б), которая может перемещаться по направ-ляющим станины. Станок предназначен для обработки тяжелых крупногаба-ритных заготовок.
Радиально-сверлильный станок (рис. 3.12, в) может быть смонтирован на специальной тележке, которая перемещается по железнодорожной колее.
Такие станки применяются на вагоноремонтных заводах.
Радиально-сверлильный переносной станок (рис. 3.12, г) используется для обработки отверстий в крупногабаритных корпусных деталях; он устанавли-вается непосредственно на обрабатываемую заготовку.
Рис. 3.13. Радиально-сверлильный станок мод. 2А554: I - фундаментная плита; 2 - цоколь; 3 - рукав; 4 - механизм подъема; 5 – шпиндельная головка; б - пульт управления; 7 – стол
Основные правила работы на сверлильном станке
1. Сверление следует производить только правильно заточенным сверлом, при необходимости нужно произвести переточку или заправку сверла. Контроль заточки необходимо осуществлять с помощью шаблона (рис. 3.14, а) или специального угломера (рис. 3.14, б).
2. Необходимо прочно закреплять сверло с цилиндрическим хвостовиком
в патроне: торец сверла следует упереть в дно патрона, а затем закрепить его, поочередно вставляя ключ во все гнезда патрона.
3. Необходимо прочно закреплять сверло с коническим хвостовиком
(патрон со сверлом) в шпинделе станка.
4. Для обеспечения прочного и безопасного крепления обрабатываемой
детали необходимо:
• крупные корпусные заготовки закреплять на столе станка;
• призматические заготовки средней величины (длина 100... 120 мм,
ширина 50... 60 мм, высота 30... 40 мм) закреплять в машинных тисках;
• небольшие заготовки (длина 70... 80 мм, толщина 1... 5 мм) закреплять
в ручных тисочках;
• заготовки цилиндрической формы устанавливать и закреплять на призмах.
5. В месте сверления на детали нужно делать глубокое (1,0... 1,5мм) керновое углубление.
6. Сверление отверстий больших диаметров (свыше 10 мм) необходимо
выполнять в два приема: вначале сверлом диаметром 5 ... 6 мм, а затем сверлом необходимого диаметра.
7. Необходимо правильно определять скорость резания в зависимости
от обрабатываемого материала и рационально настраивать станок на частоту вращения шпинделя.
8. Следует соблюдать правильную последовательность сверления при ручной подаче сверла:
• совместить вершину сверла с керновым углублением на заготовке;
• включить станок;
• сверлить отверстие на полную глубину;
• при выходе сверла из отверстия нажатие ослабить.
9. Необходимо правильно определять величину автоматической подачи и настраивать станок на эту величину.
10. Следует соблюдать правильную последовательность обработки сквозных отверстий при автоматической подаче сверла:
• совместить вершину сверла с керновым углублением на детали;
• включить станок;
• просверлить отверстие на глубину 3 ... 5 мм, используя ручную
подачу;
• не выводя сверла из отверстия, включить автоматическую подачу;
• сверлить отверстие на полную глубину.
11. При сверлении отверстий по кондуктору необходимо соблюдать
следующие правила:
• заготовка должна быть прочно закреплена в кондукторе или
кондуктор на заготовке;
• диаметр сверла должен точно соответствовать диаметру отверстия
во втулке кондуктора.
12. При сверлении стальных деталей следует применять смазы-
вающе-охлаждающую жидкость.
Рис. 3.14. Шаблон для контроля заточки сверл: а - шаблон; б - контроль угла при вершине
13. Чугунные детали нужно сверлить без охлаждения сверла.
14. После окончания работы следует проверить соответствие
просверленных отверстий (диаметр, глубина) и межцентровых расстояний
требованиям чертежа.
Правила безопасности при сверлении:
• запрещается сверлить незакрепленную или слабо закрепленную заготовку;
• следует убирать волосы под головной убор;
• необходимо тщательно застегивать обшлага на рукавах;
• запрещается сильно нажимать на рычаг подачи сверла, особенно при сверлении отверстий малого диаметра;
• запрещается наклоняться близко к месту сверления во избежание попадания стружки в глаза;
• запрещается сдувать стружку.
Нарезание резьбы.
Элементы резьбы
Каждая резьба характеризуется определенными числовыми параметрами
- элементами (рис. 3.80), которыми являются шаг, угол профиля, высота профиля, наружный, внутренний и средний диаметры.
Шаг резьбы Р - это расстояние в миллиметрах между вершинами двух соседних витков резьбы, измеренное в направлении ее оси.
Рис. 3.15. Элементы резьб:
а - треугольной; 6 - прямоугольной; в - трапецеидальной; г - трапецеидальной упорной; д - круглой; а - угол профиля; Р - шаг резьбы; d - наружный диаметр резьбы; d1, - внутренний диаметр резьбы; d2 - средний диаметр резьбы
Высота профиля t - это расстояние от вершины резьбы до основания про-филя, измеренное в направлении, перпендикулярном оси резьбы.
Основание резьбы - это участок профиля резьбы, находящийся на наимень-шем расстоянии от ее оси.
Угол профиля а - это угол между прямолинейными участками сторон профиля резьбы.
Наружный диаметр резьбы d - это наибольший диаметр, измеряемый по вершинам резьбы перпендикулярно ее оси.
Внутренний диаметр резьбы d x - это наименьшее расстояние между
противоположными основаниями резьбы, измеренное перпендикулярно
ее оси.
Средний диаметр резьбы d2 - это диаметр условной окружности, проведен-ный посредине профиля резьбы между дном впадины (основанием резьбы) и вершиной выступа перпендикулярно оси резьбы.
Типы и системы резьб
Профиль резьбы (см. рис. 3.16) зависит от формы рабочей части инструмен-та, которым получают резьбу. По назначению резьбы делятся на крепежные и специальные. К крепежным резьбам относятся треугольные, а к специальным - прямоугольные, трапецеидальные, упорные и круглые. Крепежные резьбы бывают цилиндрическими и коническими, позволящими получить плотное соединение.
Рис. 3.16. Профили резьб: а - треугольный; в - трапецеидальный; в - прямоугольный; г - трапецеидальный упорный; г) - круглый; / - вершина; 2 - впадина; 3 - нитка резьбы
В машиностроении приняты три системы резьб: метрическая, дюймовая и трубная.
Рис. 3.17. Метрическая резьба (размеры указаны в миллиметрах): dcp - средний диаметр резьбы; е – нормированный зазор; d1 - внутренний диаметр резьбы; S - шаг резьбы; l0 – теоретическая высота профиля; l1, - расстояние между вершинами витков болта и гайки; l2 – расстояние от вершины витка до дна впадины
Рис. 3.18. Дюймовая резьба (размеры указаны в миллиметрах): da - наружный диаметр резьбы; d – внутренний диаметр резьбы болта; d1 - внутренний диаметр резьбы гайки; dcp – средний диаметр резьбы; S - шаг резьбы; l0 -высота профиля; е - нормированный зазор
Рис. 3.19. Трубная резьба (размеры указаны в миллиметрах): d0 - наружный диаметр резьбы; d1, - внутренний диаметр резьбы; l0 - высота профиля; r -радиус впадины; S - шаг резьбы
Рис. 3.20. Контроль резьб: а, 6 - шагомером-шаблоном; в – штангенциркулем
Инструменты для нарезания внутренних резьб
Для нарезания внутренних резьб как вручную, так и с использованием
различного механизированного оборудования применяют особый инстру-мент - метчик.
Метчики отличаются различными конструктивными решениями, которые зависят от характера и условий обработки, а также от материала обрабатыва-емой заготовки. Однако принцип конструкции у всех метчиков одинаков.
Метчик (рис. 3.21) представляет собой закаленный винт, на котором прореза-но несколько прямых или винтовых канавок, образующих режущие кромки инструмента. Канавки также обеспечивают размещение стружки, образую-щейся при резании, по ним стружка может выводиться из зоны резания.
Метчик состоит из двух частей - рабочей и хвостовика, на конце которого выполнен квадрат (у ручных метчиков). Рабочая часть метчика включает в себя: режущую (заборную) часть, которая обеспечивает удаление основной части припуска на обработку; калибрующую часть, осуществляющую окончательную обработку резьбы; стружечные канавки; перья (витки резьбы, разделенные стружечными канавками) и сердцевину, обеспечивающую метчику достаточную для обработки прочность и жесткость. Хвостовая часть
метчика служит для закрепления его в воротке, которым производятся
рабочие и холостые перемещения метчика.
Рис. 3.21. Метчик:
а - конструкция: I - нитка (виток); 2 - квадрат; 3 - хвостовик; 4 - канавка; 5 - режущее
перо; б - геометрические параметры: 1 - передняя поверхность; 2 - режущая кромка; 3 -
затылованная поверхность; 4 - задняя поверхность; 5 - режущее перо; а - задний угол; (3 -
угол резания; 8 - угол заострения; у - передний угол; в - с винтовой стружечной канавкой:
1 - канавка; г - нарезание сквозной резьбы; д - нарезание глухой резьбы: ш - угол
наклона винтовой канавки
Для нарезания внутренней резьбы метчиками вручную используют
приспособление - вороток, который устанавливают на квадратный конец хвостовой части метчика и сообщают ему вращательное движение.
Воротки (рис. 3.22) бывают различных конструкций, которые имеют свои преимущества и недостатки. Простейшим является вороток с тремя квадрат-ными отверстиями разного размера.
Рис. 3.22. Воротки:
а - раздвижной: 1 - рамка; 2 - муфта; 3 - рукоятка; 4 - подвижный сухарь; 5 - неподвижный
сухарь; а - сторона квадратного отверстия; 6 - предохранительный: 1 - корпус; 2 -
втулка; 3 - пружина; в - торцевой; г - с трещоткой
Универсальный вороток (рис. 3.22, а) представляет собой рамку 1 с двумя сухарями: подвижным 4 и неподвижным 5, образующими квадратное отверстие. Одна из рукояток 3 заканчивается винтом, перемещающим подвижный сухарь 4 и обеспечивающим закрепление квадрата хвостовика метчика. Надежность крепления обеспечивается муфтой 2 с отверстием для стопора. Для предохранения метчика от поломок используются воротки
с выключающимися кулачками (рис. 3.22, б). В этих воротках корпус 1 и втулка 2 имеют косые кулачки, сцепляющиеся между собой. Когда усилие, передаваемое рукояткой, превышает усилие пружины 3, кулачки корпуса выходят из зацепления с кулачками втулки. При этом корпус продолжает вращаться, а метчик остается неподвижным. Торцевой вороток (рис. 3.22, в) напоминает своим устройством торцевой ключ с ограничением вращательного момента. Такие воротки применяются при нарезании резьб в труднодоступных местах, так как они позволяют работать одной рукой.
Воротки с трещоткой (рис. 3.22, г) служат для нарезания резьб в отверстиях, расположенных в труднодоступных местах, когда за один прием можно повернуть вороток лишь на небольшой угол. Эти воротки бывают односторонними и двусторонними, т. е. с рукоятками по обе стороны головки.
Инструменты для нарезания наружных резьб
Для нарезания наружных резьб применяется специальный инструмент
- плашки. Принципиально конструкция их режущего аппарата аналогична конструкции метчика для нарезания внутренних резьб. Однако если метчик представляет собой винт с прорезанными вдоль него канавками, то плашка - гайку с прорезанными канавками, образующими режущие грани инструмен-та.
Рабочая часть плашки (рис. 3.23) состоит из двух частей – заборной и калибрующей. Заборная часть является конусной с углом 40... 60 она расположена по обе стороны плашки, а ее длина составляет 1,5... 2 витка. Калибрующая часть обычно состоит из 3... 5 витков.
При слесарном (ручном) нарезании наружных резьб применяются
плашки различных конструкций: круглые, которые иногда называются
лерками, раздвижные (клуппы) и специальные, для нарезания труб.
Круглые плашки (лерки) (см. рис. 3.23) представляют собой резьбовое
кольцо с несколькими канавками для образования режущих кромок и вывода стружки при нарезании резьбы. Круглые плашки изготовляются цельными и разрезными, пружинящими. Резьба на стержнях при помощи плашек нарезается вручную с использованием воротков или на сверлильных и токарных станках, с помощью специальных оправок. Разрезные плашки
благодаря своим пружинящим свойствам позволяют регулировать величину среднего диаметра резьбы.
Рис. 3.23. Круглая плашка: 1 - заборная часть; 2 – калибрующая часть; 3 - стружечная
Канавка
Круглые плашки изготавливают из инструментальных легированных сталей
марок 9ХС 'и ХВСГ или быстрорежущей стали.
Рис. 3.24. Квадратная (раздвижная) плашка: 1 - клупп; 2 – плашка
Квадратная {раздвижная) плашка (рис.3.24) состоит из двух половин, укрепляемых в специальной рамке с рукоятками - клуппе, угловые выступы которого входят соответственно в канавки плашки, удерживая ее половинки. Одну из половинок плашек можно перемещать для установления плашки на требуемый средний диаметр резьбы. Закрепляется плашка при помощи винтов. В настоящее время нарезание резьб с использованием таких плашек осуществляется весьма редко, так как они не обеспечивают достаточной
точности резьбы. Воротки для круглых плашек (рис. 3.25) представляют собой круглую рамку с выточкой, в отверстии которой помещается круглая
плашка. Плашка в отверстии удерживается от проворачивания при помощи трех стопорных винтов, конические хвостовики которых входят в углубле-ния, выполненные на образующей поверхности корпуса плашки. Четвертый винт позволяет регулировать средний диаметр резьбы.
Рис. 3.25. Вороток для круглых плашек
Смазывающе-охлаждающие жидкости (СОЖ) при нарезании резьб служат для облегчения условий работы инструмента, снижения шероховатости обработанной поверхности, а, следовательно, для повышения качества получаемой при нарезании резьбы. Выбор СОЖ зависит от материала обрабатываемой заготовки. Так, например, для охлаждения стали (конструкционной, инструментальной и легированной), чугуна, меди и алюминия чаще всего используется эмульсия. Кроме того, для охлаждения чугуна и алюминия применяется керосин. Нарезание резьб в меди, латуни и бронзе может выполняться без охлаждения.
Правила обработки наружных и внутренних резьбовыхповерхностей
1. Нарезание резьбы необходимо выполнять при обильном смазывании
плашки или метчика машинным маслом.
2. При нарезании резьбы следует периодически срезать образующуюся
стружку обратным ходом метчика или плашки на 1/2 оборота.
3. После нарезания резьбы на стержне или в отверстии нужно произвести контроль ее качества: внешним осмотром - не допуская задиров и сорванных ниток; резьбовым калибром (или эталонным болтом, гайкой) - проходная
часть калибра (болт, гайка) навинчивается от руки, не допускается качка в паре болт-гайка.
Т а б л и ц а 3.1
Типичные дефекты при нарезании резьб, причины их появления
и способы предупреждения
Правила нарезания наружной резьбы
1. Перед нарезанием резьбы следует проверить диаметр стержня (болта, шпильки, винта); он должен быть на 0,1 ...0,2 мм меньше номинального диаметра резьбы.
2. Необходимо обязательно опилить заборную фаску на вершине стержня (если ее нет на заготовке). При опиливании фаски нужно следить за ее концентричностью относительно оси стержня, а также диаметром, который не должен превышать величины внутреннего диаметра резьбы по торцевой поверхности. Кроме того, угол наклона фаски относительно оси стержня не должен превышать 60°.
3. Стержень следует закреплять в тисках прочно и перпендикулярно
губкам. Перпендикулярность закрепления стержня надо проверять
по угольнику.
4. Необходимо строго следить за перпендикулярностью торца плашки оси стержня при врезании плашки.
5. Перед накатыванием резьбы на стержне необходимо обязательно
проверять его диаметр; он должен быть равен среднему диаметру нарезаемой резьбы.
6. При нарезании резьбы на газовых и водопроводных трубах особое внимание следует обращать на соблюдение длины нарезаемой части для муфт и сгонов.
При нарезании внутренних резьб необходимо соблюдать следующие
правила.
1. Перед нарезанием резьбы следует проверить: соответствие диаметра отверстия размеру нарезаемой резьбы. Он должен соответствовать данным таблицы резьб; глубину отверстия для нарезания глухой резьбы. Она должна
соответствовать размеру, указанному на чертеже.
2. При врезании метчика нужно обеспечить перпендикулярность его оси верхней плоскости заготовки, в которой нарезается резьба.
3. При нарезании резьбы следует использовать весь комплект метчиков: первый - черновой; второй - получистовой; третий - чистовой.
4. При нарезании резьбы в глухом отверстии необходимо периодически
очищать его от стружки.
5. Особую осторожность следует соблюдать при нарезании резьб малого диаметра (5 мм и менее) во избежание поломки метчика.
6. При нарезании резьбы машинным метчиком на станке необходимо
закреплять его в предохранительном патроне.
Типичные дефекты при нарезании резьб, причины их появления и способы предупреждения приведены в табл. 3.1.
Дата добавления: 2020-11-23; просмотров: 3330; Мы поможем в написании вашей работы! |
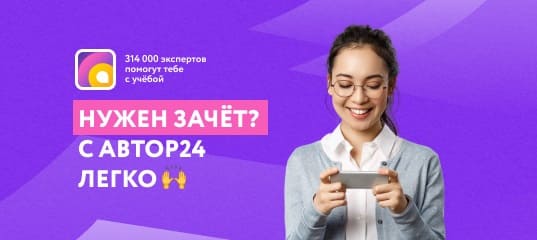
Мы поможем в написании ваших работ!