Пример расчета режима резания (токарная обработка)
Министерства образования и науки Российской Федерации
Федеральное агентство по образованию
Саратовский государственный технический университет
Балаковский институт техники, технологии и управления
и
НАЗНАЧЕНИЕ РЕЖИМОВ РЕЗАНИЯ
ДЛЯ ОСНОВНЫХ МЕТОДОВ ОБРАБОТКИ МЕТАЛЛОВ
Методические указания к выполнению технологической части
дипломного проекта
для студентов специальностей 120100, 060800
дневной, вечерней и заочной форм обучения
Одобрено
редакционно-издательским советом Балаковского института техники, технологии и управления
Балаково 2009
Введение
Значительная роль в развитии экономики страны принадлежит машиностроению. Первостепенное значение машиностроения объясняется тем, что оно обеспечивает все отрасли народного хозяйства машинной техникой, на основе которой осуществляются главные направления технического прогресса: электрификация, химизация, комплексная механизация и автоматизация производства.
В процессе самостоятельного проектирования технологического процесса механической обработки происходит накапливание опыта и закрепление навыков решения практических задач. При этом вырабатывается умение работы с технической литературой.
В ходе проектирования студент должен проявить способность применить теоретические знания, полученные в вузе, обоснованно принимать необходимые решения, технически грамотно формулировать выводы и предложения.
|
|
Выполнение курсовых и дипломных проектов по технологии машиностроения - важнейшая составляющая часть технической подготовки инженеров по специальности «Технология машиностроения», направ-ленная на закрепление, обобщение и углубление знаний, полученных студентами при изучении курса «Технология машиностроения» и смежных дисциплин.
Цель настоящей работы - помочь студентам в выполнении учебных проектов по технологии машиностроения.
Основные положения
Материал режущей части инструмента самым значительным образом влияет на уровень режима резания. Оснащение инструмента пластинками твердого сплава дает возможность повысить режимы резания по сравнению с инструментами из быстрорежущей стали в 2-3 раза.
Глубина резания оказывает относительно небольшое влияние на стойкость резца и скорость резания и поэтому при черновой (предварительной) обработке назначают по возможности максимальную глубину, соответствующую припуску на обработку. При чистовой (окончательной) обработке глубина резания назначается в зависимости от требований точности и шероховатости обработанной поверхности.
|
|
Подача. При черновой обработке назначают, возможно, большую подачу, допускаемую прочностью инструмента, прочностью механизма подачи и технологическими условиями обработки. При чистовой обработке подачу назначают в зависимости от требований точности и шероховатости обработанной поверхности.
Скорость и мощность резания. После выбора глубины резания и подачи назначается скорость резания по соответствующим таблицам или рассчитывается по эмпирическим формулам. Условия работы могут отличаться от принятых или рассчитанных величин, поэтому для уточнения полученной скорости используются поправочные коэффициенты, учитывающие качество обрабатываемого материала, состояние поверхности заготовки, качество материала инструмента (Kmv, Kпv, Kиv).
Режимы резания на черновых операциях проверяются в основном по мощности, а иногда и по допустимой силе подачи или крутящему моменту станка.
При чистовой обработке обычными проходными или расточными резцами (1< 2мм, S ≤ 0,6 мм/об), а также при обработке сверлами, зенкерами и развертками режим резания или ввиду незначительных сил резания по мощности не проверяется.
Выбранный режим резания должен удовлетворять условиям:
|
|
N ≤ N3 и 2М ≤ 2МСТ,
где N - мощность, потребная на резание, в кВт (определяется по картам или расчетам);
N3 - эффективная мощность станка в кВт (определяется по паспорту);
2М - двойной крутящий момент при резании в кГм;
2МСТ - двойной крутящий момент на шпинделе станка в кГм.
Достаточно точно двойной крутящий момент может быть подсчитан по формуле:
2M=PZ D/1000 кГм,
где Pz - тангенциальная сила резания в кГ (определяется по эмпирическим формулам);
Пример расчета режима резания (токарная обработка)
Произвести обточку валика с одной стороны (черновая) из заготовки, полученной методом горячей штамповки Ø 90 х 725 мм с припуском по шейкам вала 5 мм на сторону, материал заготовки сталь 40Х, σв=72 кг/мм2,
станок токарно-винторезный - 1К62, η=0,8. Инструмент - резец проходной, φ=45°, Т5К10, резец проходной упорный 16x25 ψ=90°, Т5К10.
Рис.1 Обработка ступеней валика | Приспособление - центры, хомутик. Паспортные данные станка 1К62 Число оборотов шпинделя в минуту: 12,5; 16 20; 25; 31,5; 40; 50; 63; 80; 100; 125;160; 200; 250; 315; 400; 500; 630; 800; 1000; 1250; 1600; 2000 об/мин Продольные подачи 0,07; 0,074; 0,084; |
0,097; 0,11; 0,12; 0,13; 0,14; 0,15; 0,17; 0,195; 0,21; 0,23; 0,26; 0,28; 0,30; 0,34; 0,39; 0,43; 0,47; 0,52; 0,57; 0,61; 0,70;0,78; 0,87; 0,94; 1;04; 1,14; 1,21; 1,40; 1,56; 1,74; 1,90; 2,08; 2,28; 2,42; 2,80; 3,12; 3,48; 3,80; 4,16 мм/об
|
|
Максимальное усилие подачи осевой 360 кг,
Мощность на шпинделе N = 8,5 кВт
1. Устанавливается глубина резания t=5 мм для обработки каждой шейки вала (весь припуск) (см. рис. 1).
2. По таблице 1 определяется подача 0,5-1,1 для диаметра детали 60-100 мм и размера державки 16x25 мм при глубине 3 -5 мм.
В среднем получается подача ST=0,8 мм/об.
3. Ближайшее значение подачи по паспорту станка Sct=0,78 мм/об.
4. Расчетная скорость резания определяется по эмпирической формуле [1,с.265]:
Vp=(Cp/Tmtxsy∙Kv
Значение коэффициента и показателей степени из табл.4 Для подачи S св. 0,7 CV=340, х=0.15, у=0.45, т=0.20,Т=60 мин (принимаем). Для поправочных коэффициентов по скорости резания из таблиц 5, 6, 7, 8 устанавливают величины поправок.
Кг=1,0 ; nv=l,0 (табл.6), Kпv=0,8 (табл.7), Kиv=0,65 (табл.8)
Kv =KmvKпvKиv ; Ку=1,0(750/720)1,0∙0,8∙0,65
Kv=l, 04∙0,8∙0,65=0,54
При подстановке в формулу скорости получаем
Vр=340/(600,250,150,780,45)∙0,54=340/(2,267∙1,27∙0,894)∙0,54=71,3 м/мин
5. Число оборотов шпинделя для обработки шеек Ø61,5; Ø71,5; Ø81,5
n1=(1000∙71,3)/π61,5=369,2 об/мин; n2=(1000∙71,3)/π71,5=317,5; n3=(1000∙71,3)/π81,5=278,6 об/мин.
6. По паспорту станка при назначении чисел оборотов шпинделя можно принять n=315 об/мин.
7. Реальная скорость резания для трех шеек получается
V1=(π61,5∙315)/1000=60,82 м/мин; V2=(π71,5·315)/1000=70,72 м/мин;
V3=(π81,5∙315)/1000=80,6 м/мин.
8. Разница с расчетной скоростью не превышает 10-15%, поэтому можно принять обработку трех шеек на общих оборотах n=315 об/мин.
9. Мощность резания рассчитывается по формуле
N=(Pz∙V)/1020·60 кВт,
где Рz - тангенциальная составляющая силы резания
Рz =Ср t
Основное время обработки на длине в 650 мм при принятой подаче Sст=0,78 мм/об получается
Т0=(L+l)/Sст∙nст=(650+4)/(0,78∙315)=2,66 мин.
Дата добавления: 2020-04-25; просмотров: 312; Мы поможем в написании вашей работы! |
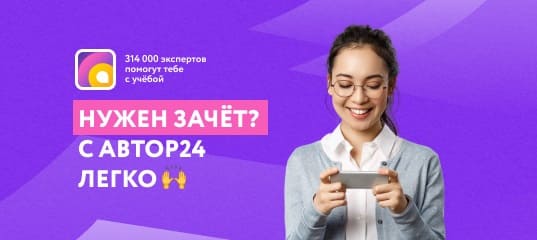
Мы поможем в написании ваших работ!