Рекомендуемые и предпочтительные посадки
Определения типов посадок, примеры и параметры
Типы посадок и параметры, характеризующие эти посадки |
1.Посадка с зазором - посадка, при которой в соединении, всегда образуется зазор, т.е. наименьший предельный размер отверстия больше наибольшего предельного размера вала или равен ему. При графическом изображении поле допуска отверстия расположено над полем допуска вала, причем, относительно нулевой линии они могут занимать различные положения
Примечания:
1. Наименьший зазор (Smin) – разность между наименьшим предельным размером отверстия и наибольшим предельным размером вала в посадке с зазором:
S min = D min – d max = EI – es
2. Наибольший зазор (Smax) – разность между наибольшим предельным размером отверстия и наименьшим предельным размером вала в посадке с зазором или в переходной посадке
S max = D max – d min = ES – ei
3.Средний зазор (Sc) – это среднее арифметическое наибольшего и наименьшего зазоров.
Sc=(S max + S min ) / 2
Пример посадки с зазором: Æ ![]() ![]() ![]() |
2. Посадка с натягом - посадка, при которой в соединении всегда образуется натяг, т.е. наибольший предельный размер отверстия меньше наименьшего предельного размера вала или равен ему. При графическом изображении поле допуска отверстия расположено под полем допуска вала, относительно нулевой линии они могут также занимать различные положения.
Примечания:
1.Наименьший натяг (Nmin) – разность между наименьшим предельным размером вала и наибольшим предельным размером отверстия до сборки в посадке с натягом:.
N min = d min – D max = ei – ES
2. Наибольший натяг (Nmax) – разность между наибольшим предельным размером вала и наименьшим предельным размером отверстия до сборки в посадке с натягом или в переходной посадке:
N max = d max – D min = es – EI
3. Средний натяг (Nc) – это среднее арифметическое наибольшего и наименьшего натягов:
Nc = (N max + N min ) / 2
Пример посадки с натягом: Æ ![]() ![]() ![]() ![]() |
3. Переходная посадка - посадка, при которой в соединении возможно получение как зазора, так и натяга, в зависимости от действительных размеров отверстия и вала. При графическом изображении поля допусков отверстия и вала перекрываются полностью или частично.
Примечание:
Переходная посадка характеризуется наибольшими значениями натяга (Nmax) и зазора (Smax).
Пример переходной посадки: Æ ![]() ![]() |
|
|
|
|
|
|
4.
Система отверстия — это совокупность посадок, в которых при одном классе точности и одном номинальном размере предельные размеры отверстия остаются постоянными, а различные посадки достигаются путем изменения предельных отклонений валов (рис. 95, а). Во всех стандартных посадках системы отверстия нижнее отклонение отверстия равно нулю. Такое отверстие называется основным.
Система вала — это совокупность посадок, в которых предельные отклонения вала одинаковы (при одном номинальном размере и одном классе точности), а различные посадки достигаются путем изменения предельных отношений отверстия. Во всех стандартных посадках системы вала верхнее отклонение вала равно нулю. Такой вал называется основным.
|
|
Смотри 3
5.
Точность размеров определяется допуском - с уменьшением допуска точность повышается, и наоборот.
Каждый технологический метод обработки деталей характеризуется своей экономически обоснованной оптимальной точностью, но практика показывает, что с увеличением размеров возрастают технологические трудности обработки деталей с малыми допусками и оптимальные допуски при неизменных условиях обработки несколько увеличиваются. Взаимосвязь между экономически достижимой точностью и размерами выражается условной величиной, называемой единицей допуска.
Единица допуска (
) выражает зависимость допуска от номинального размера и служит базой для определения стандартных допусков.
Единицу допуска, мкм,вычисляют по формулам:
для размеров до 500 мм
для размеров свыше 500 до 10000 мм
где - средний диаметр вала в мм.
В приведенных формулах первое слагаемое учитывает влияние погрешностей обработки, а второе - влияние погрешностей измерений и температурных погрешностей.
К размерам, даже имеющим одинаковые значение, могут предъявляться различные требования в отношении точности. Это зависит от конструкции, назначения и условий работы детали. Поэтому вводится понятие квалитет.
Квалитет - характеристика точности изготовления детали, определяемая совокупностью допусков, соответствующих одинаковой степени точности для всех номинальных размеров.
Допуск (Т) для квалитетов,за некоторым исключением, устанавливают по формуле
, (11)
где а - число единиц допуска;
i(I) - единица допуска.
По системе ИСО для размеров от 1 до 500 мм установлено 19 квалитетов. Под каждым из них понимают совокупность допусков,обеспечивающих постоянную относительную точность для определенного диапазона номинальных размеров.
Допуска19 квалитетов в порядке убывания точности ранжируют: 01, 0, 1, 2, 3, 17, и условно обозначают IT01, IT0, IT1, IT17. здесь IT - это допуска отверстий и валов, что означает “допуск ИСО”.
В пределах одного квалитета “а” постоянна, поэтому все номинальные размеры в каждом квалитете имеют одинаковую степень точности. Однако допуски в одном и том же квалитете для разных размеров все же изменяются,так как с увеличением размеров увеличивается единица допуска, что следует из выше приведенных формул. При переходе от квалитетов высокой точности к квалитетам грубой точности допуски увеличиваются вследствие увеличения числа единиц допуска, поэтому в разных квалитетах изменяется точность одних и тех же номинальных размеров.
Из всего изложенного следует, что:
- единица допуска зависит от размера и не зависит от назначения,условий работы и способов обработки деталей, то есть единица допуска позволяет оценить точность различных размеров и является общей мерой точности или масштабом допусков разных квалитетов;
- допуски одинаковых размеров в разных квалитетах различны, так как зависят от числа единиц допуска “а”, то есть квалитеты определяют точность одинаковых номинальных размеров;
- различные способы обработки деталей обладают определенной экономически достижимой точностью: “черновое” точение позволяет обрабатывать детали с грубыми допусками; для обработки с весьма малыми допусками применяют тонкое шлифование и т.д., поэтому квалитеты фактически определяют технологию обработки деталей.
Область применения квалитетов:
- квалитеты от 01-го до 4-го используют при изготовлении концевых мер длины, калибров и контркалибров, деталей измерительных средств и других высокоточных изделий;
- квалитеты от 5-го до 12-го применяют при изготовлении деталей, преимущественно образующих сопряжения с другими деталями различного типа;
- квалитеты от 13-го до 18-го используют для параметров деталей, не образующих сопряжений и не оказывающих определяющего влияния на работоспособность изделий.
6.
Основным называется одно из 2-х отклонений, которое определяет положение поля допуска относительно нулевой линии. Основным является ближайшее к нулевой линии отклонение.
Стандартом установлены 27 основных отклонений для отверстий и 27 основных отклонений для валов.
Основные отклонения отверстий обозначаются большими буквами латинского алфавита, а валов – малыми (см. рисунок).
A, B, C, CD, D, DE, E, F, FG, G, H, Js, K, M, N, P, R, S, TU, V, X, Y, Z, ZA, ZB, ZC.
a, b, c, cd, d, … h, js, k … za, zb, zc.
Рисунок - Основные отклонения валов и отверстий.Поле допуска образуется сочетанием основного отклонения и квалитета точности.
7.
Основными называются посадки, которые выполнены в системе вала или отверстия и в одном квалитете точности:
H9 ; E7; H6 ; M7
f9 h7 k6 h7
Комбинированными – посадки, выполненные в разных квалитетах точности или полученные сочетанием не основных деталей.
H8 ; F8 ; D8 ; F8
e7 f8 f8 f7
Рекомендуемые и предпочтительные посадки
Из множества полей допусков установленных стандартом, для практического применения выделены рекомендуемые поля.
Для отверстий - 86 рекомендуемых, из них 16 предпочтительного применения.
Для валов – 72 рекомендуемые, 10 предпочтительные.
Применение предпочтительных полей допусков обеспечивает уменьшение номенклатуры режущего инструмента.
На чертежах деталей предельные отклонения указываются непосредственно после номинального размера. При этом обычно на рабочих чертежах отклонения указываются числовыми значениями, а на сборочных чертежах условными обозначениями - символами (буквами), присвоенными той или иной посадке с добавлением индекса, указывающего класс точности сопряжения. Числовые значения отклонений, проставляемые на рабочих чертежах, выписываются из таблиц.
Допустим, что на чертеже проставлен размер . Он читается так: номинальный размер диаметра равен 50 мм, наибольший предельный размер диаметра равен: 50 + 0,5 = 50,5 мм, наименьший предельный размер: 50-0,03 = 49,97 мм. Все детали изготовленные с действительными размерами диаметра, колеблющимися в пределах от 49,97 до 50,05 мм, окажутся годными.
Буквенные обозначения, относящиеся к отверстию, пишутся над чертой дроби, а относящиеся к валу - под чертой дроби, например . Такая запись означает, что сопряжение имеет номинальный размер 25, выполняется по системе вала В (основной деталью является вал), а сопрягаемая деталь - отверстие- изготовляется с допуском, соответствующим плотной (П) посадке. Отверстие выполняется по 2а классу точности, а вал -по 3-му.
8.
Расчет и выбор посадки с зазором сводится к определению двух предельныхфункциональных зазоров Sminф. и Smaxф.по которым производится выбор стандартной посадки.
Минимальный функциональный зазор Smin ф. определяется из условия обеспечения жидкостного трения между валом и вкладышем.
Минимальный слой смазки, при котором обеспечивается жидкостное трение hmin = hж.с.:
hж.с. ≥ k (Rz1 + Rz2 + hg),
где Rz1, Rz2 – шероховатость контактирующих поверхностей;
hg – добавка, учитывающая отклонение нагрузки, температуры, скорости от расчетных, а также механические включения масла ( hg = 1…4 мкм);
k – коэффициент запаса надежности по толщине масляного слоя (k ≥ 2).
Минимальный функциональный зазор:
Максимальный функциональный зазор определяется из условия неразрывности масленого слоя и зависит от вязкости смазки, частоты вращения цапфы (вала), радиальной нагрузки на соединение, длины и диаметра соединения.
По полученным предельным функциональным зазорам Sminф., и Smaxф. подбирается стандартная посадка, при этом обеспечиваются условия выборапосадки:
1.S min таб. > S min ф.
2.S max таб. ≤ Smaxф.
Разность между Smin ф., и Smaxт. называется запасом на износ.
Полагая, что износ вала и втулки происходит с одинаковой интенсивностью, то для них запас на износ делится на 2.
Пример.Для номинального диаметра соединения 16 мм по рассчитанным предельным значениям функциональных зазоров Smin ф.= 10мкм, Smaxф. = 69 мкм подобрать стандартную посадку в системе отверстия и рассчитать запасы на износ для отверстия и вала. Построить схему полей допусков выбранной посадки.
Решение. Решение задачи начинаем с построения схемы полей допусков. По условию задана система отверстия, поэтому на нулевой линии строим поле допуска основного отверстия Н. Задаемся квалитетом точности 7 (посадку рекомендуется выбирать в 6…9 квалитетах точности), выписываем из стандарта предельные отклонения для Н7.
Для обеспечения зазора в соединении поле допуска вала должно располагаться ниже поля допуска отверстия, т. е. в данном случае ниже нулевой линии. Строим поле допуска вала (схематично, без обозначений).
Величина минимального табличного зазора будет определяться верхним предельным отклонением вала по ГОСТ 25347-82. Поэтому, в стандарте необходимо найти такое поле допуска вала, у которого верхнее отрицательное отклонение было бы больше (по модулю) или равно Smin ф =10 мкм (первое условие выбора). Подбор ведем начиная с 6-го квалитета точности. При выборе поля допуска вала первое условие может обеспечивать несколько полей. Рекомендутся выбирать предпочтительное поле (если такое имеется) и обеспечивающее наибольший запас на износ. Такому условию удовлетворяет вал с полем допуска и квалитетом точности f7, которое является предпочтительным.
Smin ф ≤ Smin т; 10 < 13 мкм.
Зная предельные отклонения вала и отверстия рассчитаем максимальный табличный зазор и сравним его с максимальным функциональным:
Smax т < Smax ф, 43 < 69, т.е. выполняется второе условие. Следовательно выбранная посадка обеспечивает условия выбора.
Запишем выбранную посадку Ø16 , для
Рассчитываем запас на износ:
Sз.и. = (Smax ф - Smax т) / 2 = (69 - 43) / 2= 13 мкм.
9.
Посадки с натягом применяются для получения неподвижных соединений без дополнительных средств крепления (шпонок, штифтов и др.).
Условием годности посадки с натягом является обеспечение минимальным натягом передачи внешней нагрузки без разрушения соединения, а максимальный натяг должен обеспечивать прочность соединения при сборке (отсутствие разрушения соединения).
Разрушение – появление на поверхностях контакта сопрягаемых деталей пластических деформаций.
Способы соединения с натягом:
- механическая запрессовка;
- запрессовка с применением смазки;
- запрессовка с нагревом охватывающей детали (при несложной конструкции);
- с охлаждением охватываемой детали (сухой лёд).
Целью расчета посадки с натягом является определение минимального и максимального функциональных натягов Nmin ф., Nmaxф.
Исходные данные для расчета:
- номинальный диаметр соединения
- передаваемые соединением крутящий момент и осевая сила.
Минимальный функциональный натяг рассчитывается из условия обеспечения относительной неподвижности сопрягаемых деталей.
Максимальный функциональный натяг рассчитывается из условия обеспечения прочности сопрягаемых деталей.
По полученным значениям выбираем стандартную посадку исходя из условия:
Условия выбора посадки с натягом:
1. Nmax т.<Nmax ф.
2. Nmin т. > Nmin ф.
Выполнение условий выбора посадки обеспечивает запас на сборку (задается по максимальному натягу для исключения разрушения деталей при сборке) и запас на эксплуатацию (задается по минимальному натягу для исключения проворачивания деталей в процессе эксплуатации).
Запас на сборку
Nз.с. = Nmax ф. - Nmax т.
Запас на эксплуатацию
Nз.с. = Nmin т. - Nmin ф.
Пример. Для номинального диаметра соединения 60 мм по рассчитанным предельным значениям функциональных натягов Nminф.= 20 мкм; Nmaxф.= 240 мкм подобрать стандартную посадку в системе отверстия и рассчитать запас на эксплуатацию и запас на сборку.
Решение. Решение задачи начинаем с построения схемы полей допусков. По условию задана система отверстия, поэтому на нулевой линии строим поле допуска основного отверстия Н. Задаемся квалитетом точности 7 (посадку рекомендуется выбирать в 6…9 квалитетах точности), выписываем из стандарта предельные отклонения для Н7.
Для обеспечения натяга в соединении поле допуска вала должно располагаться выше поля допуска отверстия. Строим поле допуска вала (схематично, без обозначений).
Величина максимального табличного натяга будет определяться верхним предельным отклонением вала по ГОСТ 25347-82. Поэтому, в стандарте необходимо найти такое поле допуска вала, у которого верхнее положительное отклонение было бы меньше (близкое) Nmax ф. =101 мкм (первое условие выбора). Подбор ведем начиная с 6-го квалитета точности. При выборе поля допуска вала первое условие может обеспечивать несколько полей. Рекомендутся выбирать предпочтительное поле (если такое имеется) и обеспечивающее наибольший запас на эксплуатацию. Такому условию удовлетворяет вал с полем допуска и квалитетом точности s6.
Nmax т.<Nmax ф.; 39 < 101 мкм.
Зная предельные отклонения вала и отверстия рассчитаем минимальный табличный натяг и сравним его с минимальным функциональным:
Nmin т. > Nmin ф, 43 < 69, т.е. выполняется второе условие. Следовательно выбранная посадка обеспечивает условия выбора.
Запишем выбранную посадку Ø16 , для которой
Рассчитываем запас на сборку
Nз.с. = Nmax ф. - Nmax т.; N з.с. = 240 – 133 = 107 мкм.
Запас на эксплуатацию
Nз.с. = Nmin т. - Nmin ф.; N з.э. = 41 – 20 = 21 мкм.
Схема расположения полей допусков выбранной посадки с зазором приведена на рисунке.
10.
Выбор переходных посадок определяется требуемыми точностью центрирования и легкостью сборки и разборки соединения. Легкость сборки и разборки соединения с переходными посадками, а также характер этих посадок определяются вероятностью получения в них зазоров и натягов.
При ориентировочных проектных расчетах вероятностные значения зазоров и натягов достаточно определить приближенным методом, в основу которого положено предположения, что размеры отверстия и вала распределяются по нормальному закону с центром группирования в середине поля допуска
) и средним квадратичным отклонением
, т.е.
(21)
Тогда значения зазора и натяга также будут распределяться по нормальному закону симметрично относительно среднего значения
если
или
если
Среднее квадратичное отклонение посадки
Вероятностный допуск посадки
(24)
Вероятностные предельные зазоры или натяги
(25)
Вероятности получения зазоров и натягов определяются с помощью интегральной функции вероятности .
Порядок расчета рассмотрим на примере.
Пример3
Обосновать выбор посадки для соединения тяжелонагруженных зубчатого колеса со втулкой, обеспечивающей хорошее центрирование и легкость сборки и разборки, диаметр соединения – 80 мм.
**Ø
Для соединения зубчатого колеса со втулкой выбираем посадку
Ø80 , применяя метод аналогов (табл.3) и учитывая рекомендации справочной литературы (1,2).
2. Определяем по формулам (2, 3, 4, 6,22)
3.По формулам 21 и 23 определяем
4. Вероятность получения соединений с натягом и зазором определяем с помощью интегральной функции вероятности , пользуясь таблицей значений функций
(2,т.1, с.12).
Предел интегрирования определяем
5.Рассчитаем вероятность натягов (зазоров) по формулам 26, 27
Где z – предел интегрирования
При
Вероятность натяга (26)
Вероятность зазора (27)
При
(28)
(29)
Следовательно, при сборке примерно 99,3% всех соединений будут с натягами и 0,7 % соединений с зазорами, что удовлетворяет эксплуатационным требованиям.
11.
Калибры – средства измерительного контроля, предназначенные для проверки соответствия действительных размеров, формы и расположения поверхностей деталей заданным требованиям.
Калибры применяют для контроля деталей в массовом и серийном производствах. Калибры бывают нормальные и предельные.
Нормальный калибр – однозначная мера, которая воспроизводит среднее значение (значение середины поля допуска) контролируемого размера. При использовании нормального калибра о годности детали судят, например, по зазорам между поверхностями детали и калибра, либо по «плотности» возникающего сопряжения между контролируемой деталью и нормальным калибром. Оценка зазора, следовательно, результаты контроля в значительной мере зависят от квалификации контролера и имеют субъективный характер.
Предельные калибры – мера или комплект мер обеспечивающие контроль геометрических параметров деталей по наибольшему и наименьшему предельным значениям. Изготавливают предельные калибры для проверки размеров гладких цилиндрических и конических поверхностей, глубины и высоты уступов, параметров резьбовых и шлицевых поверхностей деталей. Изготавливают также калибры для контроля расположения поверхностей деталей, нормированных позиционными допусками, допусками соосности и др.
При контроле предельными калибрами деталь считается годной, если проходной калибр под действием силы тяжести проходит, а непроходной калибр не проходит через контролируемый элемент детали. Результаты контроля практически не зависят от квалификации оператора.
По конструкции калибры делятся на пробки и скобы. Для контроля отверстий используют калибры-пробки, для контроля валов – калибры-скобы.
По назначению калибры делятся на рабочие и контрольные.
Рабочие калибры предназначены для контроля деталей в процессе их изготовления и приёмки. Такими калибрами на предприятиях пользуются рабочие и контролеры отделов технического контроля (ОТК). Контрольные калибры используют для контроля жестких рабочих предельных калибров-скоб или для настройки регулируемых рабочих калибров.
Стандарт предусматривает следующие гладкие калибры для валов и относящиеся к ним контрольные калибры:
ПР — проходной калибр-скоба;
НЕ — непроходной калибр-скоба;
К-ПР — контрольный проходной калибр для нового гладкого калибр-скобы;
К-НЕ — контрольный непроходной калибр для нового гладкого калибр-скобы;
К-И — контрольный калибр для контроля износа гладкого проходного калибр-скобы.
Для контроля отверстий предусмотрены:
ПР — проходной калибр-пробка;
НЕ — непроходной калибр-пробка.
Рис. 2.43. Калибр-пробки
Дата добавления: 2020-04-08; просмотров: 1779; Мы поможем в написании вашей работы! |
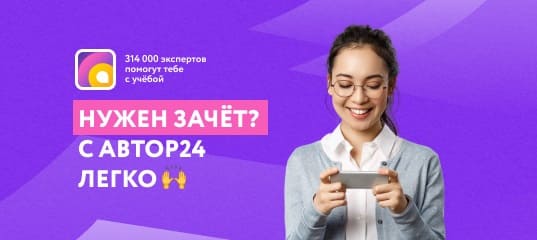
Мы поможем в написании ваших работ!