Производство мелкосортной стали
Производство крупносортной стали
В качестве исходного материала на крупносортных прокатных станах (рис. 6) используют блюмы сечением 300×300 мм и длиной 6 м. Блюмы со склада загружаются краном на приемные решетки 1 крупносортного стана 500. С приемных решеток блюмы по одному попадают на загрузочный рольганг 2 нагревательных печей. Для нагрева блюмов установлены методические печи 3.
Нагретые до температуры прокатки блюмы выдаются на подводящий рольганг 4 черновой группы клетей стана, состоящей из четырех рабочих клетей с горизонтально расположенными валками. Номинальный диаметр первых четырех рабочих клетей 630 мм, остальных пяти 530 мм.
При необходимости блюм кантуется перед черновой группой кантователем. После окончания прокатки в черновой группе клетей раскат поступает для обрезки переднего конца на ножницах и задается в последующие рабочие клети. Все рабочие клети расположены в трех параллельных линиях — в первой линии пять рабочих клетей, во второй — три и в третьей — одна.
Передача раската между рабочими клетями осуществляется рольгангами, между параллельными линиями клетей — цепным шлеппером 5. В каждой линии рабочих клетей установлены кантователи, позволяющие кантовать раскат на 45 или 90°.
На крупносортном полунепрерывном стане 500 получают двутавровые балки и швеллеры № 10–20, уголки № 8–16, круг диаметром от 50 до 120 мм, квадрат сечением от 50×50 до 100×100 мм и др. В зависимости от площади поперечного сечения готовый прокат получают после группы (черновой) рабочих клетей на первой, второй или третьей линии. Весь прокат разрезается дисковыми пилами 6 на длины от 6 до 24 м, и на каждую полосу наносится клеймо. Порезанный на мерные длины прокат передается на холодильники и после остывания подвергается правке на роликоправильных машинах и прессах, холодной резке, укладке.
|
|
Рис. 6. План расположения оборудования крупносортного стана
Среднегодовая производительность стана составляет 1 млн. т готового проката.
Производство среднесортвой стали
В качестве исходного материала на среднесортном стане используется квадратная заготовка сечением от 150×150 до 200×200 мм, длиной до 12 м. Заготовки после осмотра и зачистки загружаются краном на приемные решетки 1 (рис. 7). Для нагрева заготовок установлены методические нагревательные печи 2. Нагретые до температуры прокатки заготовки по одной выталкиваются на рольганг и транспортируются к прокатному стану. На прокатном стане предусмотрена прокатка заготовок непосредственно после НЗС.
Рис. 7. План расположения оборудования непрерывного среднесортного стана
|
|
В этом случае заготовка подогревается в печи 3, стоящей в линии прокатного стана, укрупняется на стыкосварочной машине 4, подогревается в секционной печи 5 до 1250 °С и далее следует по рольгангу на прокатку. Прокатный стан 450 состоит из черновой I, промежуточной II и чистовой III групп рабочих клетей. Черновая группа состоит из шести двухвалковых клетей, две из которых с вертикально расположенными валками.
При прокатке балок, швеллеров и полосы (штрипса) применяют горизонтальное расположение валков в комбинированных рабочих клетях. На валках рабочих клетей нарезаны ручьи ящичных калибров системы ромб — квадрат, овал — квадрат и калибров для формирования балок, швеллеров, уголков. Готовый прокат при скорости 3–15 м/с режется летучими ножницами 7. Штрипс сматывается в рулон массой до 3 т двумя попеременно работающими моталками 8 и передается на транспортер конвейерного типа 6 для охлаждения и обвязки.
Сортовой прокат режется летучими ножницами на длины, соответствующие ширине холодильника. После охлаждения прокат правится, режется на мерные длины на ножницах или дисковых пилах (балки, швеллеры), маркируется и поступает на упаковку.
Годовая производительность стана составляет 1,4 млн. т готового проката.
|
|
Производство мелкосортной стали
В качестве исходного материала на мелкосортном стане 250 используется квадратная заготовка сечением 80×80 мм, длиной 12 м. Со склада заготовок подготовленные к прокатке заготовки краном загружаются на приемные решетки стана 250. С загрузочных решеток заготовки по одной сталкиваются на приемный рольганг, которым транспортируются к методической печи.
Нагретые до температуры прокатки заготовки выталкиваются из печи на рольганг и задаются в непрерывную черновую группу клетей. При необходимости передний конец заготовки обрезается на летучих ножницах, установленных перед черновой группой стана. На валках нарезаны ручьи ящичных калибров системы квадрат — овал — круг, квадрат — ромб и калибров для прокатки угловой стали.
На стане применен индивидуальный привод валков каждой рабочей клети от отдельного электродвигателя. Промежуточная и чистовая группы стана включают рабочие клети с вертикальным расположением валков, что исключает необходимость кантовки раскатов. На мелкосортном стане 250 прокатывают круглую сталь диаметром 10–30 мм, квадрат со стороной 8–27 мм, полосу толщиной 2–4 мм и шириной 12–70 мм и уголки до 50×50 мм.
|
|
После прокатки в чистовой группе клетей готовый прокат поступает на моталки или в виде прутков на двусторонний холодильник. За каждой чистовой группой клетей установлены по четыре моталки и летучие ножницы. Круглая сталь диаметром до 25 мм и полосовая сталь сматывается в бунты, перевязывается и передается на крюковой конвейер.
Остальной прокат режется летучими ножницами на прутки и поступает на двусторонний холодильник длиной 125 мм. После охлаждения прокат осматривают, сортируют, режут на мерные длины, пакетируют и отправляют на склад.
Годовая производительность мелкосортного стана 250 составляет 650 тыс. т.
Производство катанки
В качестве исходного материала на проволочном стане 250 используют квадратную заготовку 60×60 мм, длиной 12 м. После осмотра и зачистки заготовки подают краном на загрузочные решетки прокатного стана, с которых по одной поступают на приемный рольганг нагревательной методической печи.
Загрузку и продвижение заготовок в печи осуществляют толкателем; выдача нагретых до 1180–1200 °С заготовок обеспечивается выталкивателем. Распределение заготовок по калибрам первой черновой клети осуществляется распределительным устройством барабанного типа. После распределителя заготовок установлены ножницы, которыми при необходимости обрезают передний конец заготовки или заготовки режут в скрап при аварии на стане. Непрерывный проволочный стан 250 состоит из трех групп клетей: черновой, промежуточной, чистовой.
На валках первых двух клетей черновой группы выполнены ручьи вытяжных ящичных калибров, обеспечивающих хорошее удаление окалины. На валках остальных клетей черновой группы выполнены калибры системы овал — квадрат, ромб — квадрат. На валках промежуточной и чистовой групп клетей нарезаны ручьи калибров системы овал — квадрат.
В валки последней чистовой рабочей клети задается овальный раскат, который после обжатия получает форму круга диаметром от 6,5 до 10 мм.
Готовый прокат со скоростью 12–30 м/с по водоохлаждаемым трубам поступает на моталки.
За каждой чистовой группой клетей установлено по две моталки. Бунты катанки пластинчатым транспортером передаются к сбрасывающему устройству и навешиваются на крюки крюкового конвейера. После охлаждения бунты катанки снимаются бунтосъемной машиной с крюкового конвейера, перевязываются в двух местах и поступают на пакетировочную машину. На современных специализированных проволочных станах скорость прокатки в последних рабочих клетях ≥ 60 м/с.
Температура металла после последней клети составляет 1000 °С.
С целью уменьшения окалинообразования после прокатки, получения мелкозернистой структуры сорбита проволочные прокатные станы оборудуются устройствами для ускоренного охлаждения катанки перед смоткой в бунты.
Годовая производительность проволочного прокатного стана составляет 700–800 тыс. т.
Производство рельсов и балок
В рельсо-балочных цехах производят железнодорожные рельсы массой до 75 кг на метр длины, двутавровые балки высотой до 400 мм, швеллеры, угловой профиль до 230×230 мм, шпунтовой профиль и круглый прокат диаметром 120–350 мм.
Заготовкой для рельсо-балочного стана является блюм. Масса блюма составляет 2–4 т. Нагрев блюмов осуществляют в методических печах.
Блюмы для прокатки рельсов нагревают до 1180–1200 °С. Через торцовое окно методической печи они выдаются на подводящий рольганг обжимной клети. В обжимной клети за пять проходов получают заготовку, имеющую грубую форму рельса.
В следующей прокатной трехвалковой клети за 3–4 прохода производят дальнейшее уменьшение площади поперечного сечения и приближение его к форме рельса. Четыре рабочие клети рельсо-балочного стана расположены в линию (линейная схема). Последняя рабочая клеть двухвалковая, в ней за один проход придают прокату окончательную форму. Из одного блюма получают два рельса длиной 25 м. В зависимости от массы метра длины рельсы прокатывают за 12–14 проходов.
На отводящем рольганге рельсы разрезаются дисковыми пилами на куски 25 м.
На поверхности ручья чистового калибра выполняют углубления (буквы и цифры), которые образуют клеймо: марка завода-изготовителя (буквенная), марка стали, год и месяц изготовления, тип рельса (Р43, Р50,… Р75), обозначение вида термической обработки (И — изотермическая выдержка). Кроме этого, после резки выдавливается на штемпельной машине номер плавки.
Рельсы, разрезанные на куски, при температуре 450–500 °С проходят замедленное охлаждение в колодцах или изотермическую выдержку. Далее в поточной линии рельсы подвергают термической обработке. Твердость головки рельса должна находиться в пределах НВ 320–380. В рельсоотделочном отделении рельсы правят в холодном состоянии, фрезеруют торцы, сверлят отверстия. Заключительной операцией является высокочастотная закалка концов рельсов.
Годовая производительность рельсо-балочного стана составляет ~ 1,5 млн. т.
Дата добавления: 2019-11-16; просмотров: 359; Мы поможем в написании вашей работы! |
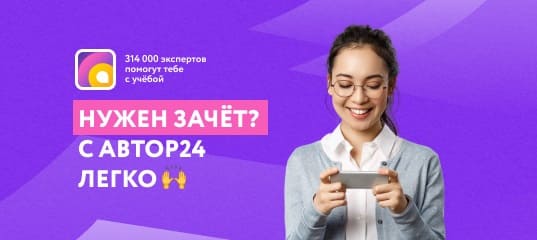
Мы поможем в написании ваших работ!