Виды и режимы термической обработки.
ПРАКТИЧЕСКАЯ РАБОТА № 1
МАРКИРОВКА СТАЛИ
Цель работы:
• Изучить маркировку сталей.
• Познакомиться с механическими свойствами сплавов.
• Выбирать материалы для конструкций по их назначению и условиям эксплуатации;
проводить исследования и испытания материалов
Общие теоретические сведения.
Классификация сталей
Сталью называется сплав железа с углеродом, в котором углерода да 2,14 %. Согласно принятой классификации стали подразделяются:
1) по способу производства :
· мартеновская,
· конверторная,
· электросталь;
2) по назначению :
· конструкционная (строительная, машиностроительная, судостроительная);
· инструментальная (У7, У8, 9Х1, ХВ4, 9ХС, Х9ВФ, 75ХМ и др.) ;
3) по химическому составу:
· углеродистые :
- малоуглеродистые -углерода до 0,25% ( ст2,Ст3, Ст4, 05, 08, 10, 15, 20, 25 )
- среднеуглеродистые - углерода 0,25 - 0,6 % (30, 35, 40, 50 )
- высокоуглеродистые - углерода 0,6 - 2,14 % (60, 65, 70, 80);
· легированные:
- низколегированные (09Г2, 14Г2, 12ГС, 09Г2С, 10Г2БД, 10ХСНД, 35ГС, 25Г2С и др);
- среднелегированные (15Х, 20Х, 40Х, 10Г2, 40ХФА, 20ХГСА, 30ХН3А, 30ХН3М2ФА, 38Х2НМФ и др);
- высоколегированные (30Х13Н7С2, 20Г13Н4Г6, 15Х25Т, 08Х18Н10Т, 12Х18Н10Т и др).
Углеродистые стали подразделяются по степени раскисления в процессе выплавки на кипящую, полуспокойную и спокойную. Степень раскисления указывается в марках стали индексами: сп - спокойная, пс - полуспокойная, кп - кипящая.
|
|
Кипящая сталь выплавляется с неполным раскислением. После разливки стали в изложницы остатки закиси железа (FeO) продолжают реагировать с углеродом. Выделение пузырьков газа создает впечатление, что металл кипит. При затвердевании такой стали остается большое количество газовых пузырей. При горячей прокатке эти пузыри завариваются, но при сварке такие стали склонны к образованию трещин при сварке, хуже свариваются и чувствительны к концентрации местных напряжений. Кипящие стали являются самыми дешевыми. Но их-за своих свойств применяются для неответственных конструкций.
Спокойная сталь выплавляется с более полным раскислением, для чего в ванну печи до разливки дополнительно вводят ферросилиций (FeSi) - активный раскислитель, а при разливки стали - алюминий, что обеспечивает спокойную кристаллизацию стали без перемешивания, исключает газообразование.
Полуспокойная сталь - промежуточная между кипящей и спокойной. Для получения полуспокойной стали вводят меньшее количество раскислителей.
Спокойную и полуспокойную сталь применяют в сварных конструкциях, работающих при температуре до минус 400С, а кипящую сталь в конструкциях, работающих при температуре не ниже + 100С.
|
|
В состав легированных сталей при выплавке специально вводят химические элементы, придающие стали определенные свойства- химические, механические, технологические. Введение тех или иных элементов приводит к увеличению прочности стали, повышает коррозионную стойкость, жаростойкость, жаропрочность.
Влияние примесей на сталь
Как известно чистое железо редко встречается в природе. В руде железо сопровождают примеси - марганец, кремний, сера, фосфор, которые оказывают влияние на свойства выплавленной стали. Разное содержание этих примесей приводит к разным механическим свойствам сталей.
Углерод - важная составляющая стали, определяющая ее прочностные свойства: прочность, вязкость, закаливаемость и свариваемость. Чем больше углерода в стали, тем выше предел прочности. Содержание углерода до 0,25 % не ухудшает свариваемость стали, при более высоком содержании углерода свариваемость резко ухудшается.
Марганец и кремний - раскислители, вводят в сталь для устранения вредных включений закиси железа и серы. Марганец повышает прочность стали.
Фосфор - в процессе производства стали, фосфор содержащийся в железной руде удаляется. Растворяясь в феррите фосфор сильно искажает кристаллическую решетку и увеличивает пределы прочности и текучести, но уменьшает пластичность и вязкость. Фосфор - вредная примесь, с его увеличением увеличивается способность к распространению трещин.
|
|
Сера - нерастворима в железе и является вредной примесью в стали. Вызывает трещины при деформации стали во время прокатки или ковки. присутствие в стали марганца связывает серу в тугоплавкое соединение MnS и процесс развитие трещин исключается. Сернистые включения сильно снижают механические свойства, особенно ударную вязкость и пластичность. Содержание серы в стали резко ограничивают в пределах 0,035 - 0,06 %.
Введение в сталь меди и никеля в небольших количествах увеличивает коррозионную стойкость сталей в атмосферных условиях.
Никель - увеличивает пластичные и прочностные свойства стали не ухудшая свариваемости.
Хром - увеличивает прочностные свойства, но при этом снижает пластичность.
Молибден - увеличивает несущую способность стали при ударных нагрузках.
Ванадий - способствует закаливаемости стали, чем затрудняет сварку. Измельчает зерно.
Вольфрам - резко увеличивает твердость стали и ее работоспособность при высоких температурах, но затрудняет сварку.
|
|
Титан и ниобий - вводят в сталь для повышения коррозионных свойств. Ниобий измельчает зерно, что ведет к увеличению прочностных свойств.
Механические свойства металлов и сплавов
При выборе материала исходят из комплекса свойств, которые подразделяют на механические, физические, химические и технологические.
Физические свойства определяют поведение материалов в тепловых, гравитационных, электромагнитных и радиационных полях. К физическим относятся такие свойства материалов как плотность, теплоемкость, температура плавления, термическое расширение, магнитные характеристики, теплопроводность, электропроводность.
Под химическими свойствами понимают способность материалов вступать в химическое взаимодействие с другими веществами, сопротивляемость окислению, проникновению газов и химически активных веществ. Характерным примером химического взаимодействия среды и металла является коррозия.
Технологические свойства металлов и сплавов характеризуют их способность подвергаться горячей и холодной обработке. Комплекс этих свойств включает в себя технологичность при выплавке, горячем и холодном деформировании, обработке резанием, термической обработке и, особенно, сварке.
При конструировании изделий в первую очередь руководствуются механическими свойствами материалов.
Механические свойства материалов характеризуют их способность сопротивляться деформированию и разрушению под действием различного рода нагрузок. Механические нагрузки могут быть статическими, динамическими и циклическими. Кроме того, материалы могут подвергаться деформации и разрушению как при разных температурных условиях, так и в различных, в том числе агрессивных средах. Для того, чтобы обеспечить надежную работу конкретных машин и приборов, необходимо учитывать условия эксплуатации, т.е. к материалу предъявляют эксплуатационные требования.
К основным механическим свойствам относят прочность, упругость, ударную вязкость, пластичность, твердость. Механические свойства некоторых марок сталей приведены в таблице 1.
Для определения механических свойств материалов разработаны различные методы испытаний. При статических методах материал подвергают воздействию постоянной силы, возрастающей весьма медленно. При динамических испытаниях материал подвергают воздействию удара или силы быстро возрастающей.
Определение прочности, пластичности, упругости
Прочность – способность материала сопротивляться разрушению под действием внешних сил.
Пластичность – способность материала к пластической деформации, т.е. к получению остаточного изменения формы и размеров без разрушения.
Упругость – свойство материала восстанавливать свои размеры и форму после прекращения действия нагрузки.
Прочность, пластичность и упругость материала определяют при статических испытаниях на растяжение.
Рис. 1.1. Статические испытания на растяжение:
а – схема испытания; б – диаграмма растяжения
Испытания производятся на цилиндрических (или плоских) образцах с определенным соотношением между длиной l0 и диаметром d0. Образец растягивается под действием приложенной силы P (рис. 1.1.) до разрушения. Внешняя нагрузка вызывает в образце напряжение и деформацию. Напряжение σ – это отношение силы P к площади поперечного сечения F, МПа:
=
,
Деформация характеризует изменение размеров образца под действием нагрузки, %
=
100,
где l – длина растянутого образца. Деформация может быть упругой (исчезающей после снятия нагрузки) и пластической (остающейся после снятия нагрузки).
При испытаниях строится диаграмма растяжения, представляющая собой зависимость напряжения от деформации. На рис 1.1, б приведена такая диаграмма для низкоуглеродистой стали. После проведения испытаний определяются следующие характеристики механических свойств.
Предел упругости σу – это максимальное напряжение, при котором в образце не возникают пластические деформации.
Предел текучести – это напряжение, соответствующее площадке текучести на диаграмме растяжения (рис. 1.1, б). Если на диаграмме нет площадки текучести (что наблюдается для хрупких материалов), то определяют условный предел текучести
– напряжение, вызывающее пластическую деформацию, равную 0,2%.
Предел прочности (или временное сопротивление) – это напряжение, отвечающее максимальной нагрузке, которую выдерживает образец при испытании.
Относительное удлинение после разрыва – отношение приращения длины образца при растяжении к начальной длине l 0, %:
=
· 100,
где lk – длина образца после разрыва.
Относительным сужением после разрыва называется уменьшение площади поперечного сечения образца, отнесенное к начальному сечению образца, %:
=
· 100,
где Fk – площадь поперечного сечения образца в месте разрыва. Относительное удлинение и относительное сужение являются характеристиками пластичности.
Определение твердости
Твердость – способность материала сопротивляться проникновению в него другого тела.
Твердость материала испытывается при статическом характере вдавливания в него шарика, конуса или пирамиды.
Наиболее широкое применение нашли методы определения твердости по Бринеллю, Роквеллу и Виккерсу (рис. 1.2.).
Твердость по Бринеллю (НВ) определяется вдавливанием в испытываемую поверхность под нагрузкой Р стального шарика диаметром Д (рис. 1.2, а).
После снятия нагрузки на поверхности образца остается отпечаток (лунка).
Твердость определяется по формуле
НВ = , Па,
где F – площадь поверхности отпечатка.
Рис. 1.2. Схемы определения твердости:
а – по Бринеллю; б – по Роквеллу; в – по Виккерсу
Диаметр шарика выбирают в зависимости от толщины изделия (Д = 10; 5; 2,5 мм). Нагрузку Р выбирают в зависимости от диаметра шарика и измеряемой твердости. При Д = 10 мм Р = 30000 Н, время – 10 секунд.
Практически величину твердости определяют не по формуле, а по прилагаемой к прибору таблице в зависимости от диаметра отпечатка.
Между твердостью по Бринеллю и пределом прочности металла существует приближенная зависимость
= к · НВ, Па
Для стали = 0,34 … 0,35 НВ.
Твердость по Роквеллу определяют по глубине отпечатка. Метод основан по вдавливании в испытуемый образец закаленного стального шарика диаметром 1,588 мм (шкала В) или алмазного конуса с углом при вершине 1200 (шкалы А и С). Вдавливание производится под действием двух нагрузок – предварительной Р0, равной 100 Н и окончательной Р, равной 600, 1000, 1500 Н для шкал А, В и С соответственно. Число твердости по Роквеллу HRA, HRB и HRC определяется по разности глубин вдавливания в условных единицах.
Твердость по Виккерсу определяют вдавливанием в испытываемую поверхность (шлифованную или даже полированную) четырехгранной алмазной пирамиды с углом при вершине 1360. Метод используют для определения твердости деталей малой толщины и тонких поверхностных слоев, имеющих высокую твердость. Число твердости по Виккерсу HV определяется отношением приложенной нагрузки к площади поверхности отпечатка.
Практически величину твердости определяют не по формуле, а по прилагаемым к прибору таблицам по измеренной величине d (диагональность отпечатка) рис. 1.2., в.
Ударная вязкость
Вязкость – свойство материала сопротивляться разрушению под действием динамических нагрузок.
Ударная вязкость определяется работой А, затраченной на разрушение образца, отнесенной к площади его поперечного сечения F; Дж/м2:
КС =
Испытания проводятся ударом специального маятникового копра. Для испытания применяется стандартный надрезанный образец, устанавливаемый на опорах копра. Маятник определенной массы наносит удар по стороне, противоположной надрезу.
КС – ударная вязкость, Дж/м2: индексы V, U (KCV, KCU) характеризуют форму надреза.
Таблица 1
Механические свойства сталей
Марка стали | Свойства | |||
![]() | ![]() | ![]() | НВ, МПа | |
10 | 340 | 31 | 55 | 1430 |
20 | 420 | 25 | 55 | 1630 |
30 | 500 | 21 | 50 | 1790 |
40 | 580 | 19 | 45 | 2170 |
50 | 640 | 14 | 40 | 2410 |
60 | 690 | 12 | 35 | 2550 |
70 | 730 | 9 | 30 | 2690 |
У8 | 1100 | 6 | 30 | 2850 |
Порядок выполнения работы
Задание № 1
Выписать назначение стали используя "Марочник сталей и сплавов"
и определить принадлежность стали к определенной группе.
Марка стали | Расшифровка |
09Г2 | |
10Г2БС | |
10ХСНД | |
35ГС | |
25Г2С | |
20Х | |
20ХГСА | |
30ХН3А | |
30ХН3М2ФА | |
38Х2НМФ | |
30Х13Н7С2 | |
20Г13Н4Г6 | |
08Х22Н6Т | |
45Х | |
45Г2 | |
30ХГСН2А | |
У7 | |
9Х1 | |
Х6ВФ | |
9Х2 | |
75ХМ | |
Ст3 сп | |
Сталь 08 | |
Сталь 25 | |
Сталь 35 | |
Сталь 45 | |
Сталь 65 | |
Сталь ШХ15 |
Задание № 2
Ответить на вопросы
1. Почему для сварных конструкций используют спокойные стали?
2. Чем отличаются конструкционные стали от инструментальных?
3. Что такое прочность? Методы измерения, характеристики, единицы измерения.
4. Чем отличается упругая деформация от пластической?
5. Что такое пластичность? Методы измерения, характеристики, единицы измерения.
6. Что такое твердость? Методы определения твердости.
7. Что такое ударная вязкость?
8. Чем отличаются статические методы испытаний от динамических?
Задание № 3
Пользуясь информационным банком, составьте группы сталей и сплавов, обладающие следующими свойствами:
- жаропрочные ______________________________________________________________________
- жаростойкие _______________________________________________________________________
- теплостойкие ______________________________________________________________________
- магнитные ________________________________________________________________________
- с высоким омическим сопротивлением ________________________________________________
- коррозионно-стойкие _______________________________________________________________
- немагнитные ______________________________________________________________________
Информационный банк: 08Х14Н28В3Т3ЮР, ХН777ЮР, ОХ23ЮБ, 10Х13, 80НХС, ЕХ9К15М,
ОХ27ЮБА, 45Г17Ю3, 79ХМ, 12Х18Н9Т, Н36К8, 13Х12Н2В2МФ, 12Х2МФСР, ЕХ3, 55Г9Н9.
Задание № 4
Определите предел прочности (Ϭв) и марку конструкционной стали (ГОСТ 1050-88), если при испытании на растяжение образца (см.рис.1.1) из этой стали наибольшая нагрузка Рmax=159 кН
(d0=10 мм, l0=100мм).
Предполагаемые марки стали:
30 (Ϭв = 500 МПа)
35 (Ϭв = 540 МПа)
Решение: __________________________________________________________________________
___________________________________________________________________________________
Ответ:_____________________________________________________________________________
Задание № 5
Подчеркните интервал температур, 0С, при котором могут быть использованы жаропрочные стали и сплавы на основе железа, никеля и кобальта:
а) 700...950;
б) 900...1000;
в) 200...300;
д) 850...900.
ПРАКТИЧЕСКАЯ РАБОТА № 2
Виды и режимы термической обработки.
Цель работы:
- изучить процессы кристаллизации и структурообразования металлов и сплавов, основу их термообработки
- научиться расшифровывать маркировку сталей и сплавов
Дата добавления: 2020-01-07; просмотров: 352; Мы поможем в написании вашей работы! |
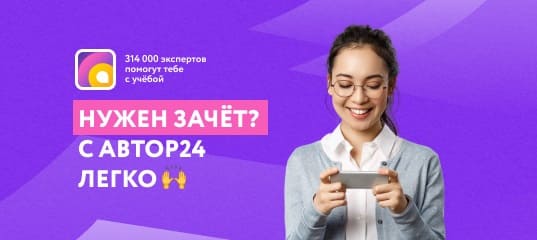
Мы поможем в написании ваших работ!