И 3.8. Электротермические установки
• Методика расчета
Расчет нагревателя электропечи включает:
- определение сечения проволоки или ленты,
- определение длины проволоки или ленты,
- размещение нагревателя в рабочей камере печи.
Руководствуясь известными данными печи (Рном, кВт; Размеры Ап х Вп х х Нп, м; тип), технологическими параметрами (t„3a конечная, °C) и параметрами электрической сети, выбирается схема включения электронагревателя (ЭН) и вариант его расчета.
При 3-380 В — это «звезда — Y» или «треугольник — V» с последова тельным или параллельным соединением секций (фазоветвей).
При 1-220 В — это однофазное включение секций.
а) Для проволочного ЭН где d — диаметр проволоки нагревателя, м;
![]() | |||
![]() | |||
Ьф — длина проволоки на фазоветвь ЭН, м;
Рф — мощность фазоветви, кВт;
1Эф — фазное напряжение, В;
р — удельное электрическое сопротивление материала нагревателя в горячем состоянии, Ом • м;
Принимается по [Таблице 3.8.1]; Ом • м • 10~6 = 9М_ММ , м
Таблица 3.8.1 — Жаростойкие и жароупорные сплавы
высокого сопротивления
Марка сплава | Топг., °C | Лента | Проволока | р сплава, Ом • мм2 м | Дополнительные сведения | |
Ь, мм | а, мм | d, мм | ||||
Х13Ю4 Х15Ю5 Х23Ю5 Х231О5Т Х27Ю5Т Х25Н20 Х15Н60 Х15Н60-Н Х20Н80 Х20Н80-Н ХН70Ю | 900 950 1150 1350 1300 900 950 1050 1050 1150 1175 | Холоднокатаная лента стандартной ширины Ь = 6...8О. 2,8,10,12,14, 15,16, 18,20,25, 30,32,36,40,45,50,60, 80 мм | о II н МП II g м л и л к д & Ю 3 СО | 0,2...7,5 0,2...7,5 0,3...7,5 0,3...7,5 0,5... 5,5 0,2...7,5 0,3...7,5 0,1...7,5 0,4... 7,5 0,1...7,5 1...7 | 1.18.. .1.34 1.24.. . 1,34 1,3...1,4 1.34.. . 1,45 1.37.. . 1,47 0,83...0,96 1,06...1,16 (при d<3 мм) 1,07...1,17 (при d > 3 мм) 1,04...1,15 (при d<3 мм) 1,06...1,17 (при d>3 мм) 1.25.. .1.35 | ТОпт — оптимальная рабочая температура; b и а — ширина и толщина ленты; d — диаметр проволоки; Рсплава- УДвЛЬНОе электрическое сопротивление при 20 °C; Горячекатаные прутки выпускают d = 13... 30 мм или квадратного сечения; а = b = 5...250 мм; _ , л_6 Ом мм2 Ом • м • 10 6 =---------- м |
|
|
Маркировка сплава:
1 — 1-й элемент сплава: X — Хром;
2 — примерное содержание 1-го элемента, %, по массе;
3 — 2-й элемент сплава: Ю — алюминий, Н — никель;
4 — примерное содержание 2-го элемента, %, по массе;
5 — 3-й элемент сплава: Т — титан.
Буква в конце марки (после «дефиса») означает структурные изменения предыдущего сплава.
W.10n — реальная допустимая удельная поверхностная мощность нагревателя при сроке службы не менее 10 000 часов, Вт/м2;
Waon — сс • WHJl, WHn — F(tHarp, tH3a С),
где \УИД — допустимая удельная поверхностная мощность идеального нагревателя, Вт/м2;
Принимается по (Рисунку 3.8.1).
![]() | ![]() |
|
![]() |
tmirp. — рекомендуемая температура для материала нагревателя, °C; tim. — максимальная температура нагреваемого изделия, °C;
|
|
Рис. 3.8.1. Зависимость \УИД = F(tHarp, tHU, °C)
где а — поправочный коэффициент, учитывающий тепловые потери мощности в печи.
Рекомендуемые усредненные значения «а»:
а = 0,2...0,3 для проволочных спиралей на полочках или трубах;
а = 0,4 для ленточных зигзагов; а = 0,6 для проволочных и литых ленточных зигзагов;
б) Для ленточного ЭН:
Рф-Р-Ю6 L _ Уф -m a2
2т(т + 1) Уф ■ Waon ’ ф Рф-р-103’
где а — толщина ленты, м; b — ширина ленты, м.
1)
т = —; В соответствии с сортаментом выпускаемой ленты для ЭН а
(m = 5...15) наиболее распространена лента с m = 10.
Рекомендуемый сортамент проволоки и лент:
d > 0,003 м для спиралей;
d > 0,006 м для «зигзагов»;
b х а > 0,01 х 0,001 м для НЭ с температурой (tHar.) до 1000 °C; b х а > 0,02 х 0,002 м для НЭ с температурой (tHar.) более 1000 °C.
![]() | ![]() | ![]() |
|
Рис. 3.8.2. Разновидность форм нагревателей: а) спираль проволочная, б) «зигзаг»
ленточный или проволочный.
Геометрические размеры элементов ЭН (Рисунок 3.8.2) принимаются в соответствии с соотношениями:
D — диаметр спирали проволочного нагревателя, м:
D = (4...6)d для хромоалюминиевых сплавов
D = (7... 10)d для нихромов
d — диаметр проволоки, м.
|
|
t — шаг спирали («зигзага»), м:
t = (3...5)d для витков спирали
t > (5...9)d для проволочного «зигзага»
t > (2.. .5)b для ленточного «зигзага»
b — ширина ленты, м.
R — радиус закругления «зигзага», м:
R = (4.. .5)a для ленточного
R > d для проволочного
a — толщина ленты, м.
Н3 — высота «зигзага», м:
Н = 0,15...0,3 для хромоалюминиевых сплавов
Н = 0,2...0,4 для нихромов
Если исходить из сортамента ленты или проволоки нагревателя, следует применить соотношения:
г. а Ь КФ. R I Л(1<КФ
*■ Р ’ Ф’Рф’ ф_ 4р ’
где R^ — расчетное сопротивление фазоветви, Ом.
Выбранный ЭН проверяется на допустимую удельную поверхностную мощность согласно условию: Wflon> WHar-
P.IO5
WHar = — (для проволочного ЭН);
лёЦ
Рф-103
WHar = —г (для ленточного ЭН).
2(а + Ь)-Еф
Если условие не выполняется, следует изменить схему соединения, повышая напряжение на фазоветвь (Уф), либо уменьшить мощность фазоветви (Рф), получив при том же сечении большую длину, а значит и площадь поверхности ЭН.
Для нагрева жидких и газообразных сред применяются трубчатые электронагреватели (ТЭН-ы).
• Методика расчета ЭН жидкой среды (вода техническая пресная, масло трансформаторное и т.п.)
а) Полезная энергия на нагревание жидкости определяется:
|
|
Wn = C»m-AT; m = р • V; АТ = Т2 - Ть
где Wn — полезная энергия, Дж;
m — масса жидкости, кг;
V — объем жидкости, м3;
Т] и Т2 — начальная (вход) и конечная (выход) температура жидкости на ЭН, °C;
Сж — удельная теплоемкость жидкости, Дж/(кг • град);
Св - 4190 Дж/(кг • град) — для пресной воды;
См = 1,6 • 103 Дж/(кг • град) — для трансформаторного масла; р — плотность жидкости, кг/м3;
рв = 103 кг/м3 (для пресной воды);
рм = 0,9 • 103 кг/м3 (для трансформаторного масла), б) Мощность ЭН:
V
где Рэн — мощность ЭН, кВТ;
т|эн — КПД нагревателя, отн. ед.;
при отсутствии данных принимается г|эн = 0,75...0,85
tj — время нагрева при одном полном обмене жидкости через резервуар, час;
п — количество обменов (насосом), шт.;
Q — производительность насоса, м3/час;
Тэад — заданная температура нагрева жидкости, °C;
То — температура жидкости перед началом нагрева, °C.
в) Мощность прокачивающего насоса для ЭН определяется (при необходимости) по методике подраздела 3.6.
• РПЗ-З.8. Нагреватель печи сопротивления.
Дано\
Вариант — 25 [Таблица 3.8.2]
Рном — 66 кВт
Тип печи — Ш (шахтная) для отжига стальных изделий
0 х Нп = 0,9 х 1,2 м
tHM. = 800 °C
Вид ЭН — ленточный «зигзаг»
Схема включения ЭН — Y («звезда»)
Требуется:
• определить и выбрать материал, сечение, длину ленты ЭН;
• выполнить проверку нагревателя;
• разместить ЭН в рабочей камере ПС.
Решение.
- Так как печь 3~380 В включается по схеме «звезда», то мощность фа- зоветви Рл. = ^ном = — = 22 кВт при VA = -Х=- = = 220 В.
ф 3 3 ф х/з 1,73
По (Рис. 3.8.1) определяется \¥ид = F(tHar., t„M., °C) = F(950, 800, °C) = = 3,75 • 104 Вт/м2.
По [Таблице 3.8.1] для ЭН выбран материал нихром Х15Н60 с tHar. = = 950 °C, р = 1,1 • Ю'6Омм
W.10n = а • WHJI = 0,4 • 3,75 • 104 = 1,5 • 104 Вт/м2;
Принимается для ленточных «зигзагов» а = 0,4
Определяются сечение и длина ленты:
Рф-р1°6 I 222 • 1,1 ■ 10~6 ■ 106 , . ,.-3
2m(m +1)-• Wflon \ 2-10(10 +1)-2202-1,5-104
где Рф — мощность фазоветви, кВт;
Уф — напряжение фазоветви, В;
Waon — допустимая удельная поверхностная мощность, Вт/м2; m — кратность сторон сечения ленты (Ь/а).
Принимается m = Шопт. = 10.
По [Табл. 3.8.1] в соответствии с сортаментом принимается лента b х а = = 15 • 10'3 х 1,5 • 10'3м.
а-Ь-Иф 1,5-10’3-15-Ю’3-2,2
I.. = — = = 4 5 м
Иф — расчетное электрическое сопротивление фазоветви, Ом;
![]() |
- Выбирается ленточный нагреватель (Ь х а = 15 • 10’3 х 1,5 • 10'3 м, Ьф = = 45 м) и проверяется на допустимую удельную поверхностную мощность:
2(а + Ь)-Ьф 2(1,5-10’3 + 15-10~3)-45
Waon(l,5 • Ю4 Вт/м2) > WHar(l,48 • 104 Вт/м2); ЭН выбран верно.
- Размещается ЭН в рабочей камере шахтной печи сопротивления (ПС). Строится развертка (Рисунок 3.8.3).
Нагреватель фазы выполняется в виде секций. Секции трех фаз размещаются друг над другом по высоте печи. Расстояние между секциями (обеспечение безопасности) ho = 0,1 м.
Применяя известные соотношения, определяются размеры ленточного
«зигзага»:
• Высота «зигзага» для нихромов принимается Н3 = 0,25 м.
• Радиус закруглений принимается R = 5 • а = 5 • 1,5 • 10'3 = 7,5 • 10’3 м.
• Вычисляется шаг «зигзага» t3 = 4 • R = 4 • 7,5 • 10'3 = 0,03 м.
• Длина ленты на один «зигзаг»
£зр = 2 • (Н3 - 2R) + 2nR = 2• (0,25 - 2 • 7,5 • 10 3) + 2 • 3,14 • 7,5 • 10’3 =
= 0,5171 м. Принимается £3 = 0,52 м
• определяется число «зигзагов» на фазу: Ьф 45
п= — =------------- = 86,54. Принимается п3 = 87.
р 0,52
Сп — сторона основания развертки цилиндрической шахтной печи сопротивления, Нп — высота ПС,
А, В, С — начало фазоветвей,
X, Y, Z — конец фазоветвей,
Н3 — высота «зигзага»,
t, — шаг «зигзага»,
R — радиус закругления «зигзага»,
ho — расстояние между фазоветвями,
hi — расстояние фазоветвей до низа и верха,
п3 — количество «зигзагов» в одной фазоветви, b х а — сечение ленты ЭН,
£3 — длина ленты одного «зигзага»
Рис. 3.8.3. Эскиз размещения ленточного ЭН
в рабочей камере шахтной печи сопротивления
Определяется возможность размещения ЭН в рабочей камере печи:
• Длина развертки Сп = л • Dn = 3,14 • 0,9 = 2,826 м;
• Длина фазоветви, сжатой «зигзагом»Ьф(з) = t3 • пз = 0,03 • 87 = 2,61 м;
• Расстояние между выводами должно быть не менее 0,1 м;
• Расстояние для монтажа электрических соединений определяется
См = Сп - Ьф(3) = 2,826 - 2,61 = 0,216 м > 0,1м,
что удовлетворяет требованиям электрической безопасности
• Расстояние фазоветвей от верха и низа камеры печи.
u H-3H3-2ho 1,2-3-0,25-2-0,1 Л
2 2
Ответ-. Для шахтной ПС выбран и размещен нихромовый ленточный ЭН, 3-фазный, Рф = 22 кВт, = 45 м, «зигзаг» (Н3 = 0,25 м; £3 = 0,52 м; t, = 0,03 м; R = 0,0075 м), п3 = 87, лента b х а = 15 х 1,5 мм.
Варианты индивидуальных заданий в [Таблице 3.8.2].
Таблица 3.8.2 — Варианты индивидуальных заданий «Электротермические установки»
Вариант | Р г ном, кВт | Тип ПС | Ап х Вп х Нп, м (0П х Нп, м) | t«i,oC | Схема включения ЭН | Вид ЭН | Дополнительные сведения |
1 | 55 | 111 | 0,3 х 0,3 х 2 | 950 | Y | ЗП | ПС — печь со- противления Ап х Вп х Нп — длина х ширина х высота печи 0П — диаметр печи Ш — шахтная загрузка К — камерная загрузка ЗП — «зигзаг» проволочный ЗЛ — «зигзаг» ленточный СП — спираль |
2 | 30 | ш | 00,45 х 0,8 | 950 | V | СП | |
3 | 70 | ш | 00,6 х 2,5 | 950 | Y | зл | |
4 | 65 | ш | 0,3 х 0,3 х 1,47 | 1300 | V | зл | |
5 | 95 | III | 0,3x0,3x2,21 | 1300 | Y | СП | |
6 | 75 | к | 1,8 х 0,9 х 0,6 | 950 | V | СП | |
7 | 50 | к | 0,7 х 0,45 х 0,35 | 1300 | Y | СП | |
8 | 45 | к | 1 х 0,5 х 0,32 | 1000 | V | СП | |
9 | 90 | к | 1,7 х 0,85 х 0,5 | 950 | Y | ЗП | |
10 | 70 | к | 1,3 х 0,65 х 0,4 | 1000 | V | СП | |
11 | 35 | ш | 0,3 х 0,3 х 1,2 | 950 | Y | зл | |
12 | ПО | ш | 00,95 х 0,95 | 950 | V | зл | |
13 | 250 | ш | 2,78 х 1,5 х 0,9 | 950 | Y | ЗП | |
14 | 300 | ш | 4 х 2,5 х 1 | 900 | V | зл | |
15 | 90 | ш | 1,7 х 0,85 х 0,5 | 850 | Y | СП | |
16 | 85 | к | 0,8 х 0,8 х 0,6 | 1200 | V | СП | проволочная При необходимо- сти, допускается вносить коррек- туру |
17 | 66 | к | 0,6 х 0,6 х 2 | 1100 | Y | зл | |
18 | 99 | к | 01,2 х 1,6 | 900 | V | зл | |
19 | 75 | к | 1,1 х 0,6 х 0,8 | 850 | Y | ЗП | |
20 | 45 | к | 0,8 х 1,2 х 1,6 | 950 | V | ЗП | |
21 | 84 | ш | 01,3 х 1,8 | 1150 | Y | СП | |
22 | 38 | ш | 01,2 х 1,8 | 1250 | V | зл | |
23 | 42 | ш | 0,9 х 0,9 х 1,2 | 800 | Y | ЗП | |
24 | 68 | ш | 1x1x1 | 950 | V | зл | |
25 | 66 | ш | 00,9 х 1,2 | 800 | Y | зл |
• Методика расчета
![]() |
а) Определяется мощность ЭП: где Рдр — расчетная мощность ЭП, кВт;
Рр — расчетная мощность удара, кВт;
Мр — расчетный момент удара, Н • м;
Мо — момент XX механизма, Н • м;
М| — максимальный момент на валу ЭД при пиковой нагрузке, Н • м;
t<j и t| — время XX механизма и продолжительность пиковой нагрузки действительная, с;
о) — угловая скорость ЭП при ударе, р/с;
А — работа, затрачиваемая на один удар, Дж.
Выбирается АД согласно условия: Рд.Ном^Рдр и проверяется по перегрузке. М] < 0,85 ■ Лм * Мном, где Мном — номинальный момент выбранного ЭД, кВт;
Хм — перегрузочная способность по моменту, отн. ед.
б) Для ЭД кузнечно-прессовых механизмов (КПМ) определяющим фактором является динамическая устойчивость при перегрузке.
Возможны следующие характерные случаи проверки выбранного ЭД на динамическую устойчивость.
Случай 1. Задана нагрузочная диаграмма КПМ (Рисунок 3.9.1 б) и суммарный момент инерции двигателя и механизма (JE, кг • м2).
Условие динамической устойчивости: 1доп > t(,
где taon — допустимая продолжительность пика нагрузки, с.
+ = 7т • Т • Т — п° $ном . т •
9,55-Мном
тк = F(p, Цо) определяется по кривым (Рисунок 3.9.1 а); цо=^;Мн = Хи-Мн0м, Мном=9550-^; ц=^-,
мк Пном Мк
где тк — относительное критическое время, отн. ед.;
Т,м — электромеханическая постоянная двигателя на линейном участке механической характеристики его, с;
Тк — электромеханическая постоянная двигателя на криволинейной части рабочего участка механической характеристики, с; Тк = 2ТЭМ.
Мном и Мк — номинальный и критический моменты ЭД, Н ■ м;
— перегрузочная способность ЭД по моменту, отн. ед.;
Цо и ц — коэффициенты относительных нагрузок при XX и пиковой
нагрузке механизма, отн. ед.;
![]() |

![]() |
Случай 2. Задана нагрузочная диаграмма КПМ (Рис. 3.9.1, б) и продолжительность пика нагрузки t]
Условие динамической устойчивости Ja> J£
1 9>55’Мном
2 Т к По S„OM
где Ja — динамический момент инерции ротора, кг • м2;
п0 — синхронная скорость АД, об/мин;
SHom — номинальное скольжение АД, %;
МКОм — номинальный момент АД, Н • м;
Ji — суммарный момент инерции КПМ, кг • м2.
По (Рис. 3.9.1 а) тк = F(po, ц).
Случай 3. Заданы момент инерции (J2), обеспечивающий устойчивость работы привода КПМ, продолжительность пика нагрузки ti и момент холостого хода Мо.
Условие динамической устойчивости Мк> Мь
По (Рис. 3.9.1 а) определяется ц = F(go, тк).
![]() |
где Мк — критический (максимальный) момент выбранного ЭД, Н • м.
Тогда допустимый пик момента М|Д0П = Ц ' Мк.
АД с КЗ-ротором для КПМ выбираются руководствуясь:
• обеспечением наилучшего выравнивания графика нагрузки,
• наименьшими потерями в двигателе,
• минимальным расходом ЭЭ за цикл работы.
В соответствии с этим для КПМ выпускаются промышленностью АД с повышенным скольжением (SH0M = 7... 15%) мощностью от 0,4 до 63 кВт. Режим работы —■ продолжительный или повторно-кратковременный (ПВ =
• РПЗ-З.9 Пресс.
Дано:
Вариант — 25 [Таблица 3.9.1 ]
А = 60 • 103 Дж за 1 ход пресса
N = 10 ходов/мин.
t| = 2 с
Мо = 42 Н • м
о)р = 145 р/с (пр = 1450 об/мин)
Требуется:
• Рассчитать и выбрать ЭД пресса
• Построить нагрузочную диаграмму пресса
• Проверить выбранный ЭД на динамическую устойчивость
Решение.
- Рассчитывается мощность ЭП пресса и выбирается АД с повышенным
скольжением:
![]() | ![]() | ![]() |
|
![]() |
Рр = Мр • сор • 1 СТ3 = 97 • 145 • 1(Г3 = 14,1 кВт;
|
![]() | ![]() | ![]() |
‘u"n‘io“6c; tu ‘‘ 6 2 4с=
ПРр = ti/tu = 2/6 = 0,33 (33 %),
где Рдр — расчетная мощность ЭП пресса, кВт;
Мр — расчетный момент пресса усредненный, Н • м;
Mi — момент на валу ЭД при пиковой нагрузке, Н • м; Рр — расчетная мощность ЭД при нагрузке, кВт; t„, U, tj — время цикла, холостого хода, удара, с; ПРр — продолжительность работы расчетная, %;
К3 — коэффициент загрузки ЭД, отн. ед.
Принимается К,= 1,3 (от 1,1 до 1,3)
По [Табл. Д.2А] выбирается АД повышенного скольжения из условия Рном Рдр, пс = 1500 об/мин, ПВ = 100 %.
т. АИРС М132М4УЗ; ПВ = 100 %; UH0M = 380 В.
Рном =11,8 кВт
Ином = 1400 об/мин (SH0M = 7 %)
П = 86,5 % cos(p = 0,83
VI — индекс механической характеристики
m = 83,5 кг
М„ом = 80,5 Н • м
Мп/МНом = 3,4
Мм/Мном = 3,5
1ном = 24,4 А
^гДнОМ 6,5
Ja = 0,045 кг • м2
Выбранный АД проверяется по перегрузке согласно условия М[(207 Н • м) < 0,85 • Хм • Мном = 0,85 • 3,5 • 80,5 = 240 Н • м.
Условие выполнено.
- Строится нагрузочная диаграмма пресса (Рис. 3.9.2).
- ЭД проверяется на динамическую устойчивость. Случай 2. Известны диаграмма нагрузки и продолжительность пика нагрузки (t|).
Условие динамической устойчивости J4>Ji, т.е. динамический момент инерции ротора АД должен быть не менее суммарного момента инерции КПМ.
J= Л- ■ 9’55' М^- = 2'9,55'80,5 = 0,037 кг • м2;
2тк noSHOM 2-2-1500-7
По [Рис. 3.8.1 а] тк = F(go, ц) = F(0,15; 0,7) = 2.
![]() | |||
![]() | |||
|
![]() |
мк = Ммакс = Хм • МНом = 3,5 • 80,5 = 281,75 Н • м~282 Н • м;
Ja(0,045 кг • м2) > Ji(0,037 кг ■ м2) Условие выполнено.
Ответ-. Для пресса выбран АД т. АИРС М132М4УЗ, ПВ = 100 %.
Рном= 11,8 кВт
Ином = 1400 об/мин
Условиям перегрузки и динамической устойчивости удовлетворяет.
Варианты индивидуальных заданий представлены в [Таблице 3.9.1].
Таблица 3.9.1 — Индивидуальные задания. «Кузнечно-прессовые механизмы»
Вариант | А, Дж/ход | N, ходов | (о, р/с | Мо, Нм | й,с | ПВК, % | Дополнительные сведения |
1 | 2 | 3 | 4 | 5 | 6 | 7 | 8 |
1 | 80 105 | 10 | 140 | 47 | 2 | 100 | А — работа привода за один рабочий цикл, Дж. N — число ходов (рабочих циклов) за минуту. Q — угловая скорость ЭД, р/с 1 об/мин - 0,105 р/с Мо — момент холостого хода, Нм ПВК — продолжительность |
2 | 80- 103 | 12 | 92 | 47 | 2 | 100 | |
3 | 80- 103 | 15 | 68 | 47 | 1 | 100 | |
4 | 80’ 103 | 20 | 69 | 47 | 1 | 100 | |
5 | 80 • 105 | 6 | 142 | 47 | 4 | 100 | |
6 | 90 • 103 | 20 | 135 | 50 | 1 | 40 | |
7 | 90- 103 | 15 | 140 | 50 | 2 | 40 | |
8 | 90 - 103 | 12 | 92 | 50 | 2 | 40 | |
9 | 90 - 103 | 10 | 67 | 50 | 2 | 40 | |
10 | 90 • 103 | 6 | 70 | 50 | 4 | 40 | включения каталожная, %. , t -102 t -102 пв%- ₽ - р tu tp+tn |
11 | 100- 103 | 6 | 140 | 52 | 5 | 100 | |
12 | 100- 103 | 10 | 142 | 52 | 2 | 100 | |
13 | 100- 103 | 12 | 92 | 52 | 2 | 100 |
1 | 2 | 3 | 4 | 5 | 6 | 7 | 8 |
14 | 100- 103 | 15 | 68 | 52 | 2 | 100 | ПВ — характеристика повтор- но-кратковременного режима ЭД, работающего с остановка- ми, % tp — время работы, мин — время паузы (стоянки), мин tu — время цикла (10 минут), мин. пр%- 1|1°2 -1,1°2 1ри 11 + ПР — продолжительность работы механизма при одном цикле, % t — время полезной работы механизма, с; — время холостого хода механизма, с; tpU — время рабочего цикла механизма, с. ЭП не останавливается. |
15 | 100 103 | 20 | 69 | 52 | 1 | 100 | |
16 | 70 ■ 103 | 20 | 135 | 45 | 1 | 40 | |
17 | 70 • 103 | 15 | 140 | 45 | 2 | 40 | |
18 | 70- 103 | 12 | 92 | 45 | 2 | 40 | |
19 | 70 ■ 103 | 10 | 70 | 45 | 2 | 40 | |
20 | 70 - 103 | 6 | 67 | 45 | 5 | 40 | |
21 | 60 ■ 103 | 20 | 69 | 42 | 1 | 100 | |
22 | 60 - 103 | 15 | 68 | 42 | 2 | 100 | |
23 | 60- 103 | 12 | 92 | 42 | 2 | 100 | |
24 | 60- 103 | 6 | 140 | 42 | 4 | 100 | |
25 | 60 - 103 | 10 | 145 | 42 | 2 | 100 |
Глава 4
Расчет и выбор ЭП металлорежущих станков
И 4.1. Токарные станки
• Методика расчета
а) Определяется мощность резания и приводного ЭД:
Pz= l,7 Fz vz- Ю"5;
Fz = 9,81 CF- txp • SYf • vz"F;
где Рдр — мощность двигателя расчетная, кВт;
Pz — мощность резания, кВт;
Fz — усилие резания, Н;
Fx и Fy — усилие осевое и радиальное, Н;
Fx = (0,2...0,3)-Fz; Fy = (0,3...0,5) • Fz;
vz — скорость резания, м/мин; Для изделий из углеродистой стали обработка резцами из быстрорежущей стали при vz = 30...60 м/мин.
CF — силовой коэффициент обработки материала, отн. ед.;
Cv — скоростной коэффициент обработки материала, отн. ед.
Хр, Ур, Пр и Xv, Yv, mv — силовые и скоростные показатели степени, зависящие от свойств обрабатываемого материала, резца, вида обработки, отн. ед.;
Для стали и чугуна принимаются по [Табл. 4.1.2 и 4.1.3]
t — глубина резания, мм;
Принимается t = 3.. .30 мм для черновых (обдирочных) работ, t = 0,1.. .2 мм для чистовых работ.
S — подача на максимальной производительности, мм/об; Принимается S = 0,4...3 мм/об для черновых работ
S = 0,1 ...0,4 мм/об для чистовых работ
При черновом растачивании S = Р(материал; t, мм; размер резца) по [Табл. 4.1.1]
Т — стойкость инструмента (резца), мин; Т = 60 мин.
т|ст — КПД главного привода при полной нагрузке, отн. ед.; Принимается т]ст = 0,7...0,8
т|п — КПД привода подачи, отн. ед.;
Принимается т|п = 0,1.. .0,2.
Таблица 4.1.1 — Подача (S, мм/об) при обработке материалов на токарном станке резцами из быстрорежущей стали
Размер резца, мм | Сталь | Чугун | ||||
Глубина резания, t, мм | ||||||
2 | 3 | 5 | 2 | 3 | 5 | |
010 | 0,08 | - | - | 0,12...0,16 | - | - |
012 | 0,10 | 0,08 | - | 0,12...0,2 | 0,12...0,18 | - |
016 | 0,1...0,2 | 0,15 | 0,1 | 0,2...0,3 | 0,15...0,25 | 0,1...0,18 |
020 | 0,15...0,3 | 0,15...0,25 | 0,12 | 0,3...0,4 | 0,25...0,35 | 0,12...0,25 |
025 | 0,25...0,5 | 0,15...0,4 | 0,12...0,2 | 0,4...0,6 | 0,3...0,5 | 0,25...0,35 |
030 | 0,4...0,7 | 0,2...0,5 | 0,12...0,3 | 0,5...0,8 | 0,4...0,6 | 0,25... 0,45 |
040 | - | 0,25...0,6 | 0,15...0,4 | - | 0,6...0,8 | 0,3...0,6 |
40x40 | - | 0,6...1,0 | 0,5...0,7 | - | 0,7...U | 0,5...0,9 |
60 х 60 | - | 0,9... 1,2 | 0,8...1,0 | - | 1,0...1,5 | 0,8... 1,2 |
75 х75 | - | 0,7...1,0 | 0,5...0,8 | - | 1,1...1,6 | 0,9... 1,3 |
Примечания-.
1) Р18 — марка быстрорежущей стали.
2) Черновая обработка: при t = 3.. .30 мм, S = 0,4.. .3 мм/об
Чистовая обработка: при t = 0,1.. .2 мм, S = 0,1.. .0,4 мм/об
Таблица 4.1.2 — Скоростные коэффициент и показатели степени при обработке на токарном станке резцами из быстрорежущей стали
Материал изделия | S, мм/об | Коэффициент, показатели степени | т, мин | Дополнительные сведения | |||
Су | Ху | Yv | mv | ||||
сталь | <0,25 | 87,5 | 0,25 | 0,33 | 0,125 | 60 | Чистовая обработка: при S<0,25 мм/об Черновая обработка: при S > 0,25 мм/об |
>0,25 | 56 | 0,60 | |||||
чугун серый НВ 190 | <0,25 | 37 | 0,15 | 0,30 | 0,10 | 60 | |
>0,25 | 35 | 0,40 | |||||
чугун ковкий НВ 150 | <0,25 | 106 | 0,20 | 0,25 | 0,125 | 60 | |
>0,25 | 75 | 0,50 |
Таблица 4.1.3 — Силовые коэффициент и показатели степени при обработке на токарном станке резцами из быстрорежущей стали
Материал изделия | Коэффициент, показатели степени | Дополнительные сведения | |||
cF | xF | yf | nF | ||
Сталь | 200 | 1,0 | 0,75 | 0 |
|
Чугун серый НВ 190 | 114 | ||||
Чугун ковкий НВ 150 | 100 |
б) Определяется мощность, затрачиваемая на подачу суппорта:
Рп = 1,7 • Fn • vn • 10’5; F„ = Fx + (Fz + Fy) • p; где Fn — суммарное усилие подачи суппорта с резцом, Н;
vn — скорость подачи, м/мин;
ц — коэффициент трения в направляющих суппорта, отн. ед.
При отсутствии данных принимается ц = 0,05...0,08 и так как vn vz,
Pn«(0,001...0,01)Pz,
в) Определяется машинное (технологическое) время обработки детали (tM, мин): где £ — длина обработки (проход резца), мм;
d — размер режущего инструмента, мм;
пшп — частота вращения шпинделя, об/мин;
S — подача, мм/об
При скоростном точении vz = 300.. .400 м/мин и соответствующей подаче.
г) Определяются потери мощности станка:
Р
АРст.ном = —- PZH0M (при номинальной нагрузке)
Лст.ном
АРСТН = а • Р7 ном + b • Р7 (при нагрузке, отличающейся от номинальной)
а + Ь = 1~'1стном; а= 1,5Ь
Лст.ном
ЛРст хх- 0,6АРст.ном; (для практических расчетов)
где АРст.ном, АРст.н, АРст.хх — потери мощности станка при номинальной, неноминальной нагрузке, холостом ходе, кВт;
Ргном — номинальная мощность резания, кВт;
а и b — коэффициенты постоянных и переменных потерь, отн. ед.; Лст.ном — КПД станка при номинальной нагрузке, отн. ед.
При выполнении вспомогательных операций ЭД не отключается от сети, а работает на холостом ходу.
• РПЗ-4.1. Токарный станок.
Дано\
Вариант — 25 [Таблица 4.1.4]
Материал изделия — чугун ковкий НВ 150
Операция — черновая обработка
Размер резца — 40 х 40 мм (сталь Р18)
Глубина резания t = 5 мм
Длина обработки £ = 850 мм
Требуется’.
• Рассчитать и выбрать ЭД главного привода станка,
• Определить vn, tM,
• Определить потери мощности станка при Pz = 0,5-PZ.HOM Решение.
![]() |
а) Определяется расчетная мощность ЭП и выбирается ЭД:
Pz = l,7-Fz-vz-10'5 = 1,7-3777-37,5-10’5 = 2,41 кВт;
Fz = 9,81 • CF • txp • SYf • vj-' = 9,81 • 100 • 51>0 • 0,7°’75 • 37,5° = 3777 H;
![]() |
|
где Рдр — мощность ЭД расчетная, кВт;
г|ст — КПД станка (главное движение), отн. ед.;
Fz — усилие резания, Н;
vz — скорость резания, м/мин;
Силовые и скоростные коэффициенты, показатели степени принимаются по [Табл. 4.1.3 и 4.1.2] при черновой обработке ковкого чугуна, глубине резания t = 5 мм, резцом из быстрорежущей стали Р18 40-40 мм, подаче S = 0,7 мм/об [Таблица 4.1.1].
S = F(HB 150, 5 мм, 40 х 40 мм) = 0,7 мм/об (от 0,5 до 0,9 мм/об)
CF = 100; XF = 1,0; YF = 0,75; n = 0
Cv = 75; Xv = 0,2; Yv = 0,5; mv = 0,125; T = 60 мин
T — стойкость инструмента, мин.
Согласно условия Рд> Рдр по [Таблице Д.1] выбирается АД для токарного станка:
т. AHP100S2Y3 Рном = 4 кВт; КПД = 87 %; cos(p = 0,88;
![]() |
|
Kmax = 2,2;
“■min 1 ,6,
Уровень шума — 68 дБ
m = 21,6 кг
- Определяются скорость подачи (vn, м/мин) и технологическое время обработки детали (tM, мин)
Р -105 2 41-10_2-105
1) v=-2------------ = ■ = 1,13 м/мин;
![]() |
п 1 ” г 1,7-1257
ц — коэффициент трения в направляющих, отн. ед.;
Принимается ц = 0,06 (от 0,05 до 0,08)
Рп = (0,001 ...0,01)Pz = (0,001 ...0,01)-2,41 = 2,41-10'3...2,41-10'2 кВт.
Принимается мощность подачи Рп = 1,ЗТ0'2 кВт.
пч 850
2) tM =------------ =-------------- = 4,1 мин;
пшп-Б 299-0,7
п = • 103 = —• 103 = 299 об/мин;
шп л-d 3,14-40
где d — диаметр инструмента (ширина резца), мм; d = 40 мм - Определяются потери станка при Pz = 0,5-Pz.HOm
ДРст.н = а Рг.ном + b-Pz = (0,2 + 0,13-0,5)-2,41 = 0,64 кВт.
a + b = l~1,CT"0M; 1,5Ь + Ь = 1 ~°’75; 2,5Ь = -;
•Whom 0,75 3
Ь = —— = 0,13; а= 1,5-Ь =
3-2,5
Ответ'. Выбран АД т. АИР100Б2УЗ Режим работы S1 Р„ом = 4 кВт
п„ом = 2850 об/мин
vn = 1,13 м/мин; tM = 4,1 мин; АРст.н = 0,64 кВт
Варианты индивидуальных заданий в [Таблице 4.1.4].
Таблица 4.1.4 — Варианты индивидуальных заданий. «Токарные станки»
Вариант | Материал изделия | Операция | Размер инструмента, мм | t, мм | €, мм | Потери при Pz | Дополнительные сведения |
1 | сталь | черновая | 0 30 | 3 | 500 | 0,6’Р г. НОМ | t — глубина |
2 | чугун НВ 190 | обработка | 0 30 | 3 | 1200 | 0,7’РЛНОм | резания |
3 | чугун НВ 150 | 0 40 | 3 | 900 | 0,8-РЛНОМ | £ — длина | |
4 | сталь | 040 | 3 | 450 | 0,9-РЛНОМ | обработки | |
5 | чугун НВ 190 | 40-40 | 3 | 1100 | 0,5-PiHOM | ||
6 | чугун НВ 150 | чистовая | 0 10 | 2 | 950 | 0,5-PZ.HOM | |
7 | сталь | обработка | 0 16 | 2 | 550 | 0,6‘PZHOM | |
8 | чугун НВ 190 | 0 12 | 2 | 1150 | 0,7'PZHOM | ||
9 | чугун НВ 150 | 0 16 | 2 | 1000 | 0>8-РДНОМ | ||
10 | сталь | 0 20 | 2 | 350 | 0,9-РГНОМ | ||
11 | чугун НВ 190 | черновая | 40-40 | 5 | 1300 | 0,9-PiHOM | |
12 | чугун НВ 150 | обработка | 60-60 | 5 | 1050 | 0,8-РЬНом | |
13 | сталь | 40-40 | 5 | 400 | 0,7-PZHOM | ||
14 | чугун НВ 190 | 75-75 | 5 | 1250 | 0,6-PiHOM | ||
15 | чугун НВ 150 | 0 30 | 5 | 1100 | 0,5PZHOM | ||
16 | сталь | чистовая | 0 25 | 2 | 300 | 0,5-PZHOM | |
17 | чугун НВ 190 | обработка | 0 20 | 2 | 600 | 0,6-PiHOM | |
18 | чугун НВ 150 | 0 25 | 2 | 550 | 0,7-P^om | ||
19 | сталь | 0 30 | 2 | 200 | 0,8'Рдлом | ||
20 | чугун НВ 190 | 0 16 | 2 | 400 | 0,9-PiHOM | ||
21 | чугун НВ 150 | черновая | 40x40 | 5 | 450 | 0,9-Pz.HOM | |
22 | сталь | обработка | 60x60 | 5 | 250 | 0,8-PrHOM | |
23 | сталь | 75x75 | 5 | 600 | 0,7-PiHOM | ||
24 | чугун НВ 190 | 040 | 5 | 700 | 0,6’PZHOM | ||
25 | чугун НВ 150 | 40x40 | 5 | 850 | 0,5-PtHOM |
■ 4.2. Сверлильные и расточные станки
• Методика расчета
а) Определяется расчетная мощность ЭД (Рдр, кВт) главного привода:
Р Р
Рлр = —— (при сверлении); Р = —— (при растачивании)
Лет Лет
где Р/х и Pzp — мощности резания при сверлении и растачивании, кВт; г|ст — КПД станка, отн. ед.;
При отсутствии данных принимается г|ст = 0,7...0,8 (для главного привода при полной нагрузке) и т|п = 0,1 ...0,2 (для привода подачи).
![]() |
|
![]() |
Pzc = M • Пшп-; М = 9,81 • См • t*M • SYm • dJM (рассверливание, зенкерование);
где М — вращающий момент на шпинделе при сверлении, Н м;
пшп — частота вращения шпинделя, об/мин;
Fzp — усилие резания при растачивании, Н;
vzc и Vq, — скорости резания при сверлении и растачивании, м/мин;
См, Cv и CF — моментный, скоростной и силовой коэффициенты обработки материала, отн. ед.;
Хм, YM, ZM; Xv, Yv, mv и XF, YF, nF — моментные, скоростные и силовые показатели степени, зависящие от свойств обрабатываемого материала, вида обработки, инструмента, отн. ед.
Для стали и чугуна принимаются по [Таблицы 4.2.1...4.2.3]
t — глубина резания, мм;
dc — диаметр сверла, мм;
tc = 0,5 dc при сверлении;
tp = 0,5(D - d) при рассверливании и зенкеровании;
d и D — диаметр отверстия до и после рассверливания, мм;
S — подача инструмента, мм/об; по [Табл. 4.2.4 и 4.2.5];
Т — стойкость инструмента, мин; по [Табл. 4.2.6];
При черновой обработке: t = 3...30 мм, S = 0,4...3 мм/об.
При чистовой обработке: t = 0,1...2 мм, S = 0,1...0,4 мм/об.
б) Определяется расчетная мощность ЭД подачи (Рдп, кВт):
![]() |
где Fn — суммарное усилие подачи суппорта с инструментом, Н; Fx, Fy, Fz — составляющие усилия подачи по осям, Н;
ц — коэффициент трения в направляющих суппорта, отн. ед.;
При отсутствии данных принимается ц = 0,05...0,08.
При отсутствии данных принимается Рп = (0,001 ...0,01) ■ Ргр где Рп — мощность подачи суппорта, кВт
vn — скорость подачи, м/мин
г|п — КПД подачи, отн. ед.
Таблица 4.2.1 — Скоростные коэффициент, показатели степени при обработке материала изделий сверлами из быстрорежущей стали
Материал изделия | Операция | S, мм/об | Коэф( | >ициент, показатели степени | Дополнительные сведения | |||
Cv | xv | Yv | Zv | mv | ||||
сталь | СВ | «0,2 | 7,0 | 0 | 0,7 | 0,4 | 0,2 | Pl 8 — марка быстрорежущей стали СВ — сверле- ние PC — рассвер- ливание ЗЕН — зенке- рование РТ — растачи- вание |
>0,2 | 9,8 | 0,5 | ||||||
PC | — | 16,2 | 0,2 | 0,5 | 0,4 | ОД | ||
ЗЕН | - | 16,2 | 0,3 | 0,3 | ||||
РТ | <0,25 | 87,5 | 0,25 | 0,33 | — | 0,125 | ||
>0,25 | 56 | 0,66 | ||||||
чугун | СВ | <0,3 | 14,7 | 0 | 0,55 | 0,25 | 0,125 | |
>0,3 | 17,1 | 0,4 | ||||||
PC | - | 23,4 | 0,1 | 0,4 | 0,25 | 0,125 | ||
ЗЕН | - | 18,8 | 0,2 | |||||
РТ | <0,25 | 37 | 0,15 | 0,3 |
| 0,1 | ||
>0,25 | 35 | 0,4 |
Таблица 4.2.2 — Силовые коэффициент, показатели степени при обработке материала изделий сверлами из быстрорежущей стали
Материал изделия | Операция | Коэффициент, показатели степени | Дополнительные сведения | ||||
Cf | xF | Yf | ZF | nF | |||
Сталь | точение | 200 | 1,0 | .0,75 | — | 0 |
|
Чугун | 114 |
Таблица 4.2.3 — Моментные коэффициент, показатели степени при обработке материала изделий сверлами из быстрорежущей стали
Материал изделия | Операция | Коэффициент, показатели сте пени | Дополнительные сведения | |||
см | хм | YM | zM | |||
сталь | сверление | 0,0345 | - | 0,8 | 2,0 |
|
рассверливание | 0,09 | 0,9 | 0,8 | 1,0 | ||
зенкерование | 0,943 | 0,8 | 0,95 | 0,75 | ||
чугун НВ 190 | сверление | 0,021 | - | 0,8 | 2,0 | |
рассверливание | 0,088 | 0,75 | 0,8 | 1,0 | ||
зенкерование | 0,196 | 0,8 | 0,7 | 0,85 |
Таблица 4.2.4 — Показатели S = F (материал, de)
dc, мм ► | <2 | 2...4 | 4...6 | 6...8 | 8...10 | |
S, мм/об | сталь | 0,05...0,06 | 0,08...0,10 | 0,14...0,18 | 0,18...0,22 | 0,22...0,26 |
чугун | 0,09...0,11 | 0,18. ..0,22 | 0,27...0,33 | 0,36...0,44 | 0,47...0,57 | |
dc, мм ► | 10...13 | 13...16 | 16...20 | 20...25 | 25...30 | |
S, мм/об | сталь | 0,25... 0,31 | 0,31...0,37 | 0,35...0,43 | 0,39...0,47 | 0,45...0,55 |
чугун | 0,52...0,64 | 0,61...0,75 | 0,7...0,86 | 0,78...0,96 | 0,9...1,1 |
Таблица 4.2.5 — Показатели S = F (материал, Dm, t)
Пш, мм ► | 80 | 110 | 150 | 200 | t, мм | |
S, мм/об | сталь | 0,40...0,60 | 0,50...0,70 | 0,75...0,95 | 1,0...1,2 | 5 |
0,35...0,50 | 0,40...0,60 | 0,70...0,85 | 0,80... 1,0 | 8 | ||
0,30...0,40 | 0,30...0,50 | 0,65...0,70 | 0,60...0,80 | 10 | ||
чугун | 0,60...0,75 | 0,60...0,95 | 1,05...1,38 | 1,20... 1,56 | 5 | |
0,50...0,60 | 0,50...0,75 | 0,90...1,10 | 1,0...1,29 | 8 | ||
0,40...0,50 | 0,40...0,60 | 0,70...0,87 | 0,90... 1,0 | 10 |
Таблица 4.2.6 — Показатели Т = F (материал, операция, dj
dc, мм ► | <5 | 6...10 | 11...20 | 21...30 | 31...40 | 41...50 | 51...60 | 61...80 | Операция | |
т, мин | сталь | 15 | 25 | 45 | 50 | 70 | 90 | НО | - | Сверле- ние и рассверливание |
чугун | 20 | 35 | 60 | 75 | ПО | 140 | 170 | |||
сталь и чугун | — | — | 30 | 40 | 50 | 60 | 80 | 100 | Зенкеро- вание |
в) Анализ. Какое влияние окажет на работу станка отклонение от номинального значения одного из параметров инструмента: стойкость (Т, мин), глубина резания (t, мм) или подача (S, мм/об)? Для логического рассуждения использовать формулы «методики расчета».
• РПЗ-4.2. Сверлильные и расточные станки.
Дано\
Вариант — 25 [Таблица 4.2.7]
Материал изделия — углеродистая сталь
Операция — сверление, т]ст = 80 %
Инструмент — dc = 30 мм
Требуется’.
• Рассчитать и выбрать ЭД шпинделя,
• Выбрать ЭД подачи суппорта,
• Анализ при S > $зад.
Решение.
1) Определяется расчетная мощность и выбирается ЭД шпинделя сверлильного станка:
![]() |
Р = Мс ■ =173,6 • = 4,8 кВт;
“ 9550 9550
v 1 24 8 1
—. 1 о3 = —• 103 = 263 об/мин; 7tdc 3,14-30
Cv-dZv 9,8-ЗО0,4 О4О 7
------------ v =------------- 7ГЧ--------- лТ = 24,8 М/МИН, Tmv.sYv 5Оо,2-О,50,5 где vzc — скорость резания при сверлении, м/мин;
Cv и Yv, Zv, mv — скоростные коэффициент, показатели степени, отн. ед.
По [Табл. 4.2.1] для сверления (СВ) стали при S > 0,2 мм/об принимаются:
Cv = 9,8; Yv = 0,5; zv = 0,4; mv = 0,2
По [Табл. 4.2.4] для сверления стали при de = 30 мм принимается S = = 0,5 мм/об.
Т — стойкость сверла, мин.
По [Табл. 4.2.6] принимается Т = F (сталь, 30 мм, СВ) = 50 мин.
Мс = 9,81 • См ■ SYm • dZm = 9,81 • 0,0345 • 0,5°’8 • 302 = 173,6 Н • м,
где Мс — вращающий момент на шпинделе при сверлении, Н • м;
См и Хм, YM, zM — моментные коэффициент и показатели степени, отн. ед.
По [Табл. 4.2.3] для сверления стали принимаются:
См = 0,0345; YM = 0,8; zM = 2.
Согласно условия Рдш> Рдр по [Таблице Д.1] выбирается ближайший по шкале мощностей АД серии АИ. Особых требований к ЭП станка не предъявляется.
т. АИР112М2УЗ, VH0M = 380 В
Рном = 7,5 кВт
КПД = 87,5 %
coscp = 0,88
SH0M = 3,5 %
J = 0,01 кг • м2
m = 41 кг
Уровень шума — 75 дБ
![]() |
2) Определяется мощность и выбирается ЭД подачи суппорта станка:
Р 9 64 ,
Рлп =-П- = ^—10-2 =0,176 кВт,
Д Пп 0Л5
где Рп — мощность подачи суппорта, кВт;
Рп = (0,001.. .0,01) • Ргс = (0,001.. .0,01 )4,8 = 4,8-1О'3.. .4,8-10'2 кВт.
Принимается Рп = 2,64 ■ 10‘2 кВт, т|п — КПД подачи, отн. ед.
Принимается г|п = 0,15 (от 0,1 до 0,2)
По [Табл. Д.1] выбирается АД
т. АИР56А2УЗ, VH0M = 380 В
Рном = 0,18 кВт
КПД = 68 %
cos<p = 0,78
J = 0,00042 кг • м2 m = 3,4 кг
Уровень шума — 61 дБ Кп = 2,2
![]() |
3) Анализ. Если S > S^. (0,5 мм/об), то мощность резания прямо пропорциональна двум сомножителям Р2С = Мс - пшп, т.к. Мс= S, то он возрастет, а пшп = vzc = 1/S, уменьшится.
![]() |

Окончательный вариант определяется превалирующим сомножителем по показателю степени УДО,8) > УДО,5).
Момент (Мс) будет увеличиваться больше, чем частота вращения шпинделя (пшп) уменьшаться, значит Р2С > Р2С заданное.
ЭП будет работать с перегрузкой и в перспективе сработает «тепловая защита».
Ответ: Для сверлильного станка выбраны АД
т. АИР112М2УЗ (шпинделя) и т. АИР56А2УЗ (суппорта) Рном = 7,5 кВт Р„ом = 0,18 кВт
Ином = 2895 об/мин Ином = 2730 об/мин
Режим — S1 Режим — S1
Варианты индивидуальных заданий в [Таблице 4.2.7].
Таблица 4.2.7 — Варианты индивидуальных заданий. «Сверлильные и расточные станки»
Вариант | Материал изделия | Операция | de мм | 0, мм | D, мм | Пег, % | Анализ | Дополнительные сведения |
1 | сталь | PC | - | 4 | 5 | 70 | S> | СВ — сверление PC — рассверли- вание ЗЕН — зенкерова- ние — это точная обработка отвер- стий многолезвий- ным инструмен- том (зенкером) de — диаметр сверла (для пер- вичного сверле- ния) 0 — диаметр отверстия (под рассверливание) D — диаметр от- верстия (после рассверливания) Знаки означают: > (превышение), < (понижение) указанного пара- метра, по сравне- нию с заданным значением |
2 | - | 8 | 10 | 74 | Т> | |||
3 | - | 16 | 20 | 76 | t> | |||
4 | - | 20 | 30 | 78 | S< | |||
5 | - | 25 | 40 | 80 | т< | |||
6 | чугун | СВ | 30 | - | - | 80 | т> | |
7 | 25 | - | - | 78 | s> | |||
8 | 20 | - | - | 76 | т< | |||
9 | 15 | - | - | 74 | s< | |||
10 | 10 | - | - | 70 | dc> | |||
И | сталь | ЗЕН | - | 60 | 80 | 80 | t> | |
12 | - | 40 | 60 | 78 | s> | |||
13 | - | 30 | 50 | 76 | т> | |||
14 | - | 20 | 40 | 74 | т< | |||
15 | - | 16 | 30 | 70 | т< | |||
16 | чугун | PC | - | 4 | 10 | 70 | s> | |
17 | - | 8 | 10 | 70 | т> | |||
18 | - | 16 | 20 | 76 | t> | |||
19 | - | 20 | 30 | 78 | s< | |||
20 | - | 25 | 40 | 80 | t< | |||
21 | сталь | СВ | 25 | - | - | 78 | т> | |
22 | 20 | - | - | 76 | dc> | |||
23 | 15 | - | - | 74 | s< | |||
24 | 12 | - | - | 70 | T< | |||
25 | 30 | - | - | 80 | s> |
■ 4.3. Продольно-строгальные станки
• Методика расчета
а) Определение расчетной мощности главного привода при прямом ходе стола (Рд.пр, кВт).
F -v
1 z,,p-10~3;
60-Лп
Ft = Fz + (Fn + FCT + Fx + Fy) • p;
Fz =9,81 CF • tXp SYf • v^;
C„
Vznp jmv Xv gYv ’
где FT — тяговое усилие на рейке стола, Н;
Fz — наибольшее усилие резания, Н;
Fx и Fy — продольная и поперечная составляющие усилия резания, Н;
Fx = (0,2...0,3)Fz; Fy = (O,3...O,5)FZ;
FH и FCT — усилие на перемещение изделия и стола, Н;
F„ = q • GH; FCT = q • GCT; q = 9,81 м/с2;
G„ и GCT — масса изделия и стола, кг
Vznp — скорость резания при прямом ходе стола, м/мин
t — глубина резания, мм;
S — подача изделия (стола), мм/двойной ход
При отсутствии данных принимается:
При черновой обработке t = 6.. .30 мм; S = 1...7 мм/дв. ход.
При чистовой обработке t = 0,05...0,3 мм; S > 10...30 мм/дв. ход.
Т — стойкость инструмента, мин; Принимается Т = 60 мин.
При отсутствии данных принимается: vz = 4...6 м/мин (при черновой обработке); vz = 75...100 м/мин (при чистовой обработке)
ц — коэффициент трения стола о направляющие, отн. ед. Принимается ц = 0,05...0,08
CF и Cv — силовой и скоростной коэффициенты обрабатываемости материала при продольном строгании, отн. ед.
XF, YF, nF и Xv, Yv, mv — силовые и скоростные показатели степени, зависящие от свойств материала изделия, вида обработки, инструмента, отн. ед.
Для стали и чугуна принимаются по [Табл. 4.3.2 и 4.3.3].
Таблица 4.3.1 — Показатели S - F (материал, сечение инструмента, t)
t, мм ► | <8 | 8...12 | 12...20 | Сечение резца, мм | Дополнительные сведения | |
S, мм/двойной ход | сталь | 0,9... 1,2 | 0,5...0,8 | - | 25 х 40 | S — подача при черновой обработке t — глубина резания |
1,3...1,8 | 0,8...1,2 | 0,4...0,6 | 30x45 | |||
2,5...3,5 | 1,6...2,2 | 0,8...1,4 | 40x60 | |||
чугун, медные сплавы | 1,6...2,0 | 1,1...1,5 | - | 25 х 40 | ||
2,4...3,0 | 1,6...2,4 | 0,8...1,4 | 30x45 | |||
3,5...4,0 | 2,5... 3,0 | 1,8...2,4 | 40x60 |
Таблица 4.3.2 — Скоростные коэффициент, показатели степени при продольном строгании резцом из быстрорежущей стали
![]() |
Таблица 4.3.3 — Силовые коэффициент, показатели степени при продольном строгании резцом из быстрорежущей стали
Материал изделия | Коэффициент, показатели степени | Дополнительные сведения | |||
Cf | xF | Yf | nF | ||
сталь | 200 | 1,0 | 0,75 | 0 |
|
чугун НВ 190 | 114 | ||||
чугун НВ 150 | 100 |
б) Определение производительности (NaBX.) и машинного времени (tM, мин) продольно-строгального станка.
60-К-% . . _ Ви
NjtBX “ 60LCT(H-K) + tpee K -vnp ; ’N^-S’
где Ыдв.х. — число двойных ходов стола в минуту, дв.х./мин;
LCT и Ви — длина хода стола и ширина обрабатываемого изделия, м; Vnp и Vo6p — скорости хода стола при прямом и обратном ходе, м/мин;
V - Vq6 P •
Vnp
tpeB — время реверсирования стола с прямого хода на обратный или наоборот, с;
Практика показывает, что в продольно-строгальных станках момент инерции двигателя меньше общего приведенного момента инерции движущихся поступательно и вращающихся частей: Ддв = (0,8...0,85) • JE.
Время переходного процесса (пуска и торможения) сильно зависит от этого параметра, поэтому рекомендуется реверсирование стола при помощи реверсивной электромагнитной муфты либо устанавливать вместо одного два ЭД половинной мощности. Для современных станков время переходного процесса составляет от 0,1 до 0,2 с.
tM — машинное время при строгании, затрачиваемое на обработку одного изделия, мин;
S — подача на один двойной ход, мм/дв.х;
При чистовой обработке скорость резания vz = 75...100 м/мин
при черновой — vz = 4.. .6 м/мин
Таблица 4.3.4 — Показатели продольно-строгальных станков (ориентировочно)
Г абарит | FT, кН | G„, тн | Для стола | 1 | Электропрйвод | |
Дет, ОТН. ед. | Lctj м | Вст, М | ||||
легкий | до 50 | до 5 | 3...4 1 | 1,5...4 | от 0,7 до 4 | АД |
средний | 50...70 | 5...10 | 6...8 1 | 4...5 | Г-Д пост, т или тп-д | |
тяжелый | более 70 | 10...200 | 15...25 1 | 5...12 |
Примечание'. FT — наибольшее тяговое усилие станка;
GH — наибольший вес обрабатываемого изделия; Дст — диапазон регулирования скорости стола; LCT — длина стола (строгания, наибольшая);
Вет — ширина стола (строгания, наибольшая)
Таким образом, основными величинами, характеризующими размеры и технологические возможности различных продольно-строгальных станков являются:
- ход стола (наибольшая длина строгания) LCT = 1,5... 12 м,
- ширина обработки Вет = 0,7...4 м,
- наибольшее тяговое усилие FT = 30...70 кН и более.
Нормативная скорость прямого хода (скорость резания) определяется твердостью обрабатываемого материала, свойствами режущего инструмента и видом обработки (чистовая, черновая).
Для увеличения производительности станка скорость обратного хода устанавливают больше скорости резания.
Время цикла состоит
где tn пр и tn обр — время пуска при прямом и обратном ходах, с;
tnp и to6p — время прямого и обратного ходов (установившиеся движения), с;
кпр и Добр — время торможения при прямом и обратном ходах, с. При отсутствии данных вес стола можно определить
CjCt Y ’ LCT * BCT ■ HCT,
где GCT — вес стола, кг;
LCT, Вот и Нст — длина, ширина и толщина стола, м; у— удельная плотность материала стола, кг/м3 Принимается для стали у = 7,85 • 103 кг/м3.
• РПЗ — 4.3 Продольно-строгальные станки.
Дано\
Вариант — 20 [Таблица 4.3.5]
Материал изделия — чугун НВ 190
Операция — продольное строгание
Вид обработки — черновая
Инструмент — резец из стали 30 х 45 мм
t = 8 мм; Kv = 4; Ви = 1 м
Размеры стола: LCT х Вст х Нст = 3 х 1 х 0,05 м
Масса изделия — GH = 500 кг
Главное — движение стола
Требуется’.
• Рассчитать и выбрать ЭД привода стола
• Определить Ыдв.х и tM станка
• Анализ при t > t3W мм
Решение.
1) Определяется расчетная мощность приводного АД при прямом ходе стола и выбирается по каталогу ЭД.
Р, пр = • I О"3 = 19056 11,8 • 10’3 = 5,4 кВт;
л пр 60 ч„ 60 0,7
FT = Fz + (FCT + Fn + Fx + Fy) • ц =
= 17788 + (11556 + 4905 + 3558 + 5336) • 0,05 = 19056 H;
Fz = 9,81 • CF • txp • SYf • v£F = 9,81 • 114 • 81 • 2,50’75 • 11,8° = 17788 H;
Fn = q-GH = 9,81 -500 = 4905 H; FCT = q • GCT = 9,81 • 1178= 11556 H;
GCT = y-LCT-BCT-HCT = 7,85- 103 • 3 - 1 0,05= 1178 кг;
C 35
vz =----------- v nT7 7ГТ = 11,8 М/МИН.
Tmv . tXv . gYv 6q0, I . g0,15.2,50,4
По [Таблице 4.3.1] S = F (материал, сечение инструмента, t) = F (HB 190, 30 x 45, 8 mm) = 2,4.. .3 мм/дв.х
Принимается S = 2,5 мм/дв.ход.
По [Таблице 4.3.2] для чугуна НВ 190 при S > 0,25 мм/дв.ход.
Cv = 35; Xv = 0,15; Yv = 0,4; mv = 0,1; Т = 60 мин.
По [Таблице 4.3.3] CF = 114; XF = 1; YF = 0,75; nF = 0.
Fx = 0,2 • Fz = 0,2 • 17788 = 3558 H; FY = 0,3 • Fz = 0,3 • 17788 = 5336 H
Согласно условия РДНОм^Рд.пр по [Таблице Д. 1] выбирается ближайший по шкале мощностей АД т. АИР100Ь2УЗ, VH0M = 380 В
Рном — 5,5 кВт
КПД = 88 %
costp = 0,89
Shom = 5 %
J = 0,0075 кг • м2
m = 27,4 кг
Уровень шума — 68 дБ
Кп = 2
^таах — 2,2
^-мин — 1,6
Ki = 7,5
2)
![]() |
Определяется производительность станка (N дв.х/мин) и его машинное время (tM, мин).
, „ = 3,12 дв.х/мин;
60-3-(1 + 4) + 0,15-4-11,8
tM = ——— = —— = 128 мин,
N,B.X-S 3,12-2,5
где tpeB — время реверсирования стола с прямого хода на обратный или наоборот, с;
Принимается tpeB = 0,15 с (от 0,1 до 0,2 с).
3) Анализ. Если t > (8 мм), то ЭП будет перегружен, что, в конечном
итоге, приведет к срабатыванию тепловой защиты.
Из расчетных формул видно, что Рд.пр= FT • vz, a FT^ Fz= txp
Однако, XF > Xv, следовательно из двух сомножителей (FT • vz) первый будет увеличиваться больше, чем уменьшаться второй, а значит Рд > Рном.
Ответ-. В качестве ЭП продольно-строгального станка выбран АД
т. АИР100Ь2УЗ
Рном 5,5 кВт
п„ом = 2850 об/мин
Режим работы — S1
Варианты индивидуальных заданий в [Таблице 4.3.5].
Таблица 4.3.5 — Варианты индивидуальных заданий. «Продольно-строгальные станки»
Вари ант | Материал изделия | LCT х Вст х Нст, м | Kv | Размер резца, мм | t, мм | Ви,м | Gh, TH | Дополнительные сведения |
1 | сталь | 1,5x0,7x0,04 | 3 | 25 х 40 | 8 | 0,6 | 1 | Черновое про- дольное стро- гание. Главное — движение сто- ла. К - Vq6p Vnp (отношение скоростей прямого и об- ратного ходов) t — глубина резания Ви — ширина изделия GH — вес (мае- са) изделия Анализ выпол- нить по одно- му из заданных преподавате- лем парамет- ров: Т, t, S При необхо- димости зада- НИЯ можно усложнять |
2 | 2 х 1,5 х 0,05 | 4 | 30x45 | 10 | 1,2 | 2 | ||
3 | 2,5 х 2 х 0,06 | 3,5 | 40x60 | 20 | 1,5 | 3 | ||
4 | 3 х 2,5 х 0,07 | 3 | 25 х 40 | 10 | 2 | 4 | ||
5 | 3,5 х 3 х 0,08 | 4 | 30x45 | 20 | 2,5 | 5 | ||
6 | чугун НВ 150 | 4x4x0,12 | 3 | 40x60 | 18 | 3 | 5,5 | |
7 | 3 х 3 х 0,08 | 4 | 30x45 | 14 | 2 | 4,2 | ||
8 | 2 х 2 х 0,06 | 3,5 | 25 х 40 | 12 | 1,2 | 1,0 | ||
9 | 3 х 2,5 х 0,07 | 3 | 30x45 | 16 | 2,1 | 1,5 | ||
10 | 4 х 3 х 0,1 | 4 | 40 х 60 | 16 | 2,2 | 2,1 | ||
11 | сталь | 4 х 2,5 х 0,11 | 3 | 30x45 | 18 | 2,4 | 2,2 | |
12 | 4,5x4x0,15 | 4 | 40x60 | 20 | 3,5 | 3,4 | ||
13 | 5 х 3 х 0,14 | 3,5 | 40 х 60 | 16 | 2,8 | 2,5 | ||
14 | 3,5 х 2 х 0,07 | 3 | 30x45 | 20 | 1,9 | 0,9 | ||
15 | 3 х 2,5 х 0,07 | 4 | 30x45 | 18 | 2,4 | 2 | ||
16 | чугун НВ 190 | 4 х 4 х 0,12 | 3 | 40x60 | 15 | 3 | 1,2 | |
17 | 3,5 х 3,5 х 0,12 | 4 | 30x45 | 16 | 2,5 | 1,1 | ||
18 | 2 х 2 х 0,05 | 3,5 | 25 х 40 | 8 | 1,5 | 0,8 | ||
19 | 2,5 х 2 х 0,06 | 3 | 25 х 40 | 10 | 1,8 | 0,6 | ||
20 | 3 х 1 х 0,05 | 4 | 30x45 | 8 | 1 | 0,5 | ||
21 | сталь | 4x3,5x0,15 | 3 | 40x60 | 15 | 3 | 5 | |
22 | 4,5 х 3 х 0,12 | 4 | 40x60 | 18 | 2,5 | 4 | ||
23 | 5x4x0,18 | 3,5 | 40 х 60 | 20 | 4 | 5,5 | ||
24 | 2 х 2 х 0,06 | 3 | 25 х 40 | 12 | 2 | 0,6 | ||
25 | 3 х 1 х 0,05 | 4 | 30x45 | 8 | 1 | 0,5 |
■ 4.4. Фрезерные станки
• Методика расчета
а) Определение расчетной мощности на валу главного ЭП (Рдв.р, кВт), соответствующей наибольшей (номинальной) мощности резания.
1) Для станков зубофрезерных и общего назначения
p„»o=—; p, = Fz v\ ; F,=9,8i cF-tXF -sYF
д,р Пст 2 6O1O3 2 F
v Cv-Dq-
VZ ym, gYv (XV . gUv ,znv ’ где Pz — мощность резания, кВт;
Fz — усилие резания (окружное усилие при фрезеровании), Н; vz — нормативная скорость резания при фрезеровании, м/мин; t — глубина фрезерования (толщина слоя металла, снимаемого за один проход), мм;
S — подача на зуб фрезы, мм/зуб;
z — число зубьев фрезы, шт.;
D — диаметр фрезы, мм;
Т — стойкость фрезы, мин;
В — ширина фрезерования (фрезы), мм. (Для торцовых В = D).
При отсутствии данных принимается:
- глубина фрезерования t — до 15 мм;
- подача S = 0,02...0,6 мм/зуб при черновом (грубом) фрезеровании на мощных станках цилиндрическими фрезами, S = 0,02...0,08 мм/зуб при чистовом фрезеровании;
- стойкость цилиндрических, торцевых, дисковых и фасонных фрез
Т = 180 мин (при обработке стали и ковкого чугуна), Т = 240 мин (при обработке серого чугуна),
CF и Cv — силовой и скоростной коэффициенты обрабатываемости материалов при фрезеровании, отн. ед.;
Хр, Yf, UF, qF и Xv, Yv, Uv, mv, nv — силовые и скоростные показатели степени, зависящие от свойств обрабатываемого материала, вида обработки, инструмента, отн. ед.
Для стали и чугуна принимаются по [Табл. 4.4.1 и 4.4.2] г|ст — КПД станка при номинальной нагрузке, отн. ед.;
Принимается т|ст = 0,75...0,8.
Таблица 4.4.1 — Скоростные коэффициент, показатели степени при фрезеровании плоскостей фрезой из быстрорежущей стали
Материал изделия | Тип фрезы | S, мм/зуб | Коэффициент, показатели степени | ||||||
Су | Qv | Ху | Yv | Uy | nv | Шу | |||
сталь | торцовая | >0,1 | - | - | 0,1 | 0,4 | 0,1 | 0,1 | 0,2 |
цилиндрическая | >0,1 | - | - | 0,3 | 0,4 | 0,1 | 0,1 | 0,33 | |
чугун НВ 190 | торцовая | - | 42 | 0,2 | 0,1 | 0,4 | 0,1 | 0,1 | 0,15 |
цилиндрическая | >0,15 | 27 | 0,7 | 0,5 | 0,6 | 0,3 | 0,3 | 0,25 | |
чугун НВ 150 | торцовая | >0,1 | - | - | 0,1 | 0,4 | 0,15 | 0,1 | 0,2 |
цилиндрическая | >0,1 | - | - | 0,3 | 0,4 | 0,1 | 0,1 | 0,33 |
Таблица 4.4.2 — Силовые коэффициент, показатели степени при фрезеровании плоскостей фрезой из быстрорежущей стали
Материал изделия | Тип фрезы | Коэффициент, показатели степени | Дополнительные сведения | ||||
СР | 4f | XF | yf | uF | |||
сталь | цилиндрическая | 68 | 0,86 | 0,86 | 0,74 | 1,0 | Pl 8 — марка быстрорежу- щей стали |
торцовая | 88 | 1,1 | U | 0,8 | 0,95 | ||
чугун | цилиндрическая | 48 | 0,83 | 0,83 | 0,65 | 1,0 | |
торцовая | 70 | 1,14 | 1,14 | 0,7 | 0,9 |
2) Для тяжелых продольно-фрезерных станков (подача стола)
Рд. Р = Рт 'Убп 3; FT = Fz + (F„ + F„) • и; vm = (1,5.. .4,2) • vz. р 60-T|nl°
FT — тяговое усилие (наибольшее) электропривода, Н;
(Fn + FCT) • ц — усилие перемещения стола с изделием, Н;
ц — коэффициент трения стола о направляющие, отн. ед. Принимается ц = 0,05...0,08.
Убп — скорость быстрого перемещения стола (наибольшая), м/мин; т]п — КПД передачи, отн. ед.
Принимается т|п = 0,2...0,48.
Технические данные столов фрезерных станков в [Таблице 4.4.6].
Таблица 4.4.3 — Стойкость фрезы Т = F (тип, D)
Диаметр фрезы D, мм ► | 26...40 | 41...60 | 61...75 | 76...150 | 151...250 | 251...300 | 301...400 | |
т, мин | Тип фрезы | |||||||
торцовая | 120 | 180 | 240 | 300 | 420 | |||
цилиндрическая с ножами | — | 180 | — | |||||
цилиндрическая с мелким зубом | — | 120 | 180 | — |
Таблица 4.4.4 — Подача S = F (тип фрезы, материал изделия) при черновом фрезеровании, мм/зуб
Фрезы торцовые | Фрезы цилиндрические | ||
сталь | чугун | сталь | чугун |
0,2...0,3 | 0,4...0,6 | 0,4...0,6 | 0,6...0,8 |
Таблица 4.4.5 — Технические данные фрез из быстрорежущей стали
Тип фрезы | Параметры | Дополнительные сведения | ||
D, мм | В, мм | Z | ||
Цилиндрическая | 75 | 60,75 | 8 | D — диаметр |
с ножами из Р18 | 90 | 60,75, 100 | 8 | фрезы |
110 | 60, 75,100, 125 | 10 | В — ширина | |
130 | 60,75, 100, 125, 150 | 10 | фрезерования | |
150 | 60, 75,100,125,150 | 12 | z — число зубьев фрезы | |
Цилиндрическая | 50 | 50, 63, 80 | 12 | |
с мелким зубом | 63 | 50, 63, 80, 100 | 14 | |
Торцовая | 40 | 40 | 10 | Для торцовых |
50 | 50 | 12 | фрез В = D | |
63 | 63 | 14 | ||
80 | 80 | 16 | ||
100 | 100 | 18 | ||
Торцовая с но- | 80 | 80 | 10 | |
жами из Р18 | 100 | 100 | 10 | |
125 | 125 | 14 | ||
160 | 160 | 16 | ||
200 | 200 | 20 |
Таблица 4.4.6 — Технические данные стола фрезерного станка
Размер стола L х В, мм | 1600 х 450 | 2200 х 650 | 3000 х 900 | 4250 х 1250 | 6000 х 1800 | 8500 х 2500 | 12000 х 3000 |
Масса изделия макс. GH, тн | 1,5 | 2,5 | 5 | 8 | 14 | 35 | 120 |
Тяговое усилие макс. FT, Н | 500 | 700 | 700 | 1800 | 1800 | 2200 | 5700 |
РПЗ-4.4 Фрезерные станки
Дано’.
Вариант — 25 [Таблица 4.4.7]
Материал изделия — чугун НВ 190
£и = 0,85 м на столе LCT х Впх Нст = 1,6 х 0,45 х 0,01 м
Фреза D = 50 мм, цилиндрическая
Операция — черновое фрезерование
t = 5 мм
Главное движение — вращение фрезы
Требуется’.
• рассчитать и выбрать ЭД главного привода
• определить N и tM
• анализ при Т < Тзад, мин
Решение.
1) Определяется расчетная мощность на валу главного ЭД (Рд.р, кВт), выбирается ЭД стандартный по каталогу (справочнику).
Так как привод подачи от ЭД главного движения, то Рд.р увеличивается на 5 %.
Р,„ =1,05-Ь- = 1,05 — = 7,9 кВт;
Р Лет 0,75
![]() | ![]() |
CvD4v у —---------------- --------------------- = z Tmv ,SYV ,tXv BUV znv | 27 • 5O0,7 = n7, n, =10,2 м/мин, 12O0,25 • 0,7°’6 • 50,5 • 500,3 • 120’3 |
F= 9,81 -CF - tXfr -SYp z — = 9,81 -48-50’83 z F D4f |
501 500,83 |
= 33114 H; |
где г|ст — КПД станка при номинальной нагрузке, отн. ед.; Принимается Т|ст = 0,75 (от 0,75 до 0,8)
Ср и Cv — силовой и скоростной коэффициенты обрабатываемости чугуна при фрезеровании плоскости, отн. ед.;
Хр, Yf, Up, qF и Xv, Yv, Uv, qv, mv, nv — силовые и скоростные показатели степени, зависящие от свойств материала изделия, вида обработки, инструмента, отн. ед.
Для стали и чугуна принимаются по [Табл. 4.4.1 и 4.4.2].
S — подача, мм/зуб; Согласно [Табл. 4.4.4] принимается S = F (цилиндрическая фреза, чугун) = 0,7 мм/зуб.
Согласно [Табл. 4.4.5] выбирается тип фрезы и ее данные: цилиндрическая с мелким зубом D = 50 мм, В = 50 мм, z = 12.
Т — стойкость фрезы, мин. Согласно [Табл. 4.4.3] принимается Т = = F (фреза цилиндрическая с мелким зубом, D = 50 мм) = 120 мин.
Для главного привода фрезерного станка согласно условия Рном Рд р по [Таблица Д. 1 ] выбирается АД
т. АИР132М2УЗ
Рном = 11 кВт
КПД = 88 %
coscp = 0,9
Shom = 3 %
J = 0,023 кг • м3
G = 64 кг
Уровень шума — 77 дБ
К, = 1,6
^-тах = 2,2
^-мин — 1,2
К, = 7,5
2) Определяются параметры фрезы.
„ к, v -10’ 10,2 10’ „
Скорость вращения N = —------------ =-------------- = 65 об/мин.
я-D 3,14-50
Скорость подачи продольной vn = S - z • N • 10’3 = 0,7 - 12 • 65 • 10'3 = = 0,55 м/мин.
М * 0>85 1 сс
Машинное время tM= —=-------------- = 1,55 мин.
vn 0,55
3) Анализ. Если Т < Тзад (120 мин), что соответствует фрезе ухудшенного качества, то ЭП будет перегружаться и возможно срабатывание тепловой защиты.
Из расчетных формул видно, что Pflp=Fz • vz, a Fz не зависит от Т и vz ; тогда при Fz = const и возрастании vz увеличится мощность Pz, а следовательно и Рдр.
При более тонкой оценке следует учитывать величину превышения мощности выбранного ЭД над расчетной (Рном-Рд.р.) и время обработки изделия. Возможно срабатывание тепловой защиты не обязательно. Ответ-. Для главного привода фрезерного станка выбран АД
т. АИР132М2УЗ
Рном = 11 кВт
пном = 2910 об/мин
Режим работы — S1
N = 65 об/мин
tM = 1,55 мин
Варианты индивидуальных заданий в [Таблице 4.4.7].
Таблица 4.4.7 — Варианты индивидуальных заданий. «Фрезерные станки»
Вариант | Материал изделия | Фреза | t, мм | LCT х Вст, м | Си» м | FT,H | Дополнительные сведения | |
Тип | D, мм | |||||||
1 | чугун НВ | цилинд- | 75 | 2 | 1,6x0,45 | U | 500 | D — диаметр |
2 | 190 | рическая | 90 | 5 | 2,2 х 0,65 | 1,5 | 700 | фрезы |
3 | с ножа- | ПО | 4 | 3x0,9 | 2,3 | 700 | t — глубина фрезерования 1-ст X Вст | |
4 | ми из Р18 | 130 | 7 | 4,25 х 1,25 | 3,8 | 1800 | ||
5 | 150 | 10 | 6х 1,8 | 5 | 1800 | |||
6 | сталь | Торцо- | 40 | 1,5 | 1,6x0,45 | 0,9 | 500 | длина х шири- на стола Си — длина изделия |
7 | вая | 50 | 2,5 | 2,2 х 0,65 | 1,8 | 700 | ||
8 | 63 | 3,5 | 3x0,9 | 2,5 | 700 | |||
9 | 80 | 4,5 | 4,25 х 1,25 | 3,6 | 1800 | |||
10 | 100 | 5,5 | 6х 1,8 | 5,2 | 1800 | Максимальная | ||
11 | чугун НВ | торцовая | 80 | 6,8 | 3x0,9 | 2,4 | 700 | масса изделия |
12 | 150 | с ножа- | 100 | 5,2 | 4,25 х 1,25 | 4 | 1800 | для конкретно- |
13 | ми из Р18 | 125 | 4 | 6х 1,8 | 5,6 | 1800 | го стола указа- | |
14 | 160 | 2,2 | 8,5 х 2,5 | 8 | 2200 | на в [Табл. 4.4.6] | ||
15 | 200 | 1,8 | 12x3 | 10 | 5700 | |||
16 | сталь | цилинд- | 75 | 6,5 | 1,6 х 0,45 | 1,4 | 500 | |
17 | рическая | 90 | 7,5 | 2,2 х 0,65 | 2 | 700 | FT — тяговое | |
18 | с ножа- | 110 | 8,5 | 3x0,9 | 2,1 | 700 | усилие пере- мещения стола | |
19 | ми из Р18 | 130 | 9,5 | 4,25 х 1,25 | 4,1 | 1800 | ||
20 | 150 | 10 | 6х 1,8 | 4,8 | 1800 | с максимальной | ||
21 | чугун НВ | цилинд- | 50 | 9 | 4,25 х 1,25 | 2,9 | 1800 | нагрузкой, |
22 | 190 | рическая | 63 | 8 | 3x0,9 | 2,2 | 700 | используется |
23 | с мел- | 50 | 7 | 1,6 х 0,45 | 0,7 | 500 | при главном — | |
24 | КИМ зубом | 63 | 6 | 2,2 х 0,65 | 2 | 700 | движении стола | |
25 | 50 | 5 | 1,6x0,45 | 0,85 | 500 |
■ 4.5. Шлифовальные станки
• Методика расчета.
1) Схемы движений в шлифовальных станках (Рисунок 4.5.1).
2) Определение расчетной мощности главного ЭП станка.
Во всех шлифовальных станках главным движением является вращение шлифовального круга.
р х
РдР=—; Pz(n) = С -vj t р-Sf -dJJp (при шлифовании периферией Пет
круга);
в) г)
а) круглошлифовальный; б) внутришлифовальный;
в) плоскошлифовальный с прямоугольным столом
г) плоскошлифовальный с круглым столом
1 — обрабатываемая деталь; 2 — шлифовальный круг;
So — вертикальная подача;
Sj — продольная подача (в направлении оси шлифовального круга);
S2 — поперечная подача (подача на глубину резания);
vK — скорость резания линейная (вращение шлифовального круга — главное движение);
vn — скорость подачи (движение изделия);
сок — угловая скорость вращения круга;
(ои — угловая скорость вращения изделия
Рис. 4.5.1. Схемы движений в шлифовальных станках
Р/(т) = Ср • vj • tXp • Bzp (при шлифовании торцом круга).
п _ 60 ' v k ' *п . 1 гр. : _ ' пном .
Ином j 1и ’ *п , лЗ ’
n-dk 60vK-10
где Pz — мощность резания (шлифования), кВт;
vH — скорость изделия окружная (при круглом шлифовании) или линейная (при плоском шлифовании), м/мин;
В — ширина шлифования, мм;
vK — скорость резания (окружная скорость круга), м/с;
dk — диаметр круга, мм;
nk — скорость вращения круга об/мин;
Скорость резания определяется окружной скоростью круга и находится в пределах от 30 до 50 м/с (редко до 75 м/с).
t — глубина шлифования, мм;
Принимается t = 0,005.. .0,015 (при чистовом шлифовании),
t = 0,015...0,05 (при черновом шлифовании).
S] — подача в направлении оси шлифовального круга (продольная или поперечная), мм/об (при вращении детали) или мм/дв.х (при движении стола);
При движении стола принимают:
с 0,3...0,7 о ч о 0,2...0,3 D t
Э! =----------------- Вк (черновое) и S] —--------------------- Вк (чистовое)
дв.х дв.х
Вк — толщина шлифовального круга, мм;
Ср — мощностной коэффициент обрабатываемости материала при шлифовании, отн. ед.
гр, Хр, Yp, qp, zp — мощностные показатели степени, зависящие от свойств обрабатываемого материала, вида обработки и инструмента, отн. ед. Для стали и чугуна принимаются по [Таблица 4.5.1].
Режимами резания при шлифовании определяются vH, м/мин; t, мм; S по [Табл. 4.5.2].
При отсутствии данных можно ориентироваться на следующие показатели:
Абразивные круги плоского прямого профиля dk = 250...750 мм и Втах = = 75 мм имеют рабочие окружные скорости;
vK = 50...75 м/с при чистовом (скоростном) шлифовании или
vK = 30...50 м/с при черновом (обычном) шлифовании.
Таблица 4.5.1 — Мощностные коэффициент, показатели степени при шлифовании
Вид шлифования | Характер шлифования | Материал шлифовального круга | Обрабатывав- мый материал | Коэффициент, показатели степени | |||||
Ср | гр | хР | YP | Чр | Zp | ||||
круглое наружное | периферийное | электрокорунд | сталь | 1,2 | 0,75 | 0,85 | 0,7 | — | — |
плоское на прямоугольном столе | периферийное | 0,53 | 0,53 | 0,8 | 0,65 | 0,7 | — | ||
торцом | 0,39 | 0,7 | 0,5 | — | - | 0,6 | |||
плоское на круглом столе | торцом | 3,6 | 0,3 | 0,25 | - | - | 0,3 | ||
торцом | карборунд | чугун | 4,03 | 0,4 | 0,4 | - | - | 0,45 |
Таблица 4.5.2 — Режимы резания при шлифовании
Вил шлифования | Характер шлифования | Тип стола | v„ м/мин | t, мм | с ‘-’попер, доли Вк | Дополнительные сведения |
плоское | черновое перифер. | прямоугольный | 8...30 | 0,015...0,04 | 0,4...0,7 | vn — скорость изделия (при плоском шлифовании — линейная, а при круглом — окружная) |
чистовое перифер. | 15...20 | 0,005...0,015 | 0,2...0,3 | |||
черновое торцом | 4...12 | 0,015...0,04 | ||||
чистовое торцом | 2...3 | 0,005...0,01 | ||||
черновое торцом | круглый | 10...40 | 0,015...0,03 | |||
чистовое торцом | 10...40 | 0,005 | ||||
круглое наруж- ное | черновое перифер. |
| 20...30 | 0,015...0,05 | 0,3...0,7 | |
чистовое перифер. | 15...55 | 0,005...0,015 | 0,25... 0,5 |
• РПЗ-4.5. Шлифовальные станки
Дано’.
Вариант — 25 [Таблица 4.5.3]
Вид шлифования — плоское на прямоугольном столе
Характер шлифования — черновое, периферией круга
Материал шлифовального круга — электрокорунд
Обрабатываемый материал — сталь
Диаметр круга dk = 250 мм, ширина круга В = 20 мм, vK = 30 м/с Требуется’.
• определить мощность ЭД главного привода
• вычислить требуемое передаточное число (in)
• анализ при уменьшении vH и увеличении dk одновременно Решение.
1) Определяется расчетная мощность и выбирается ЭД привода шлифовального круга по каталогу (справочнику)
Рд = = — = 27,6 кВт.
ДР Чет 0,8
При шлифовании периферией круга
Pz( п) = Ср • v'₽ • tXp • S^p • dJP = 0,53 • 200,53 • O,O20’8 • 100’65 • 250°’7 = 22,1 кВт.
При плоском черновом шлифовании периферией круга на прямоугольном столе изделия из стали по [Таблица 4.5.1] выбираются мощностной коэффициент и показатели степени
Ср = 0,53; гр = 0,53; Хр = 0,8; Yp = 0,65; qp = 0,7.
По [Табл. 4.5.2] принимаются
vn = 20 м/мин (от 8 до 30 м/мин); t = 0,02 мм (от 0,015 до 0,04 мм);
S] = °’3“ 0’7 • В = (0,3...0,7) • 20 = (6...14) мм/дв.х. дв.х
Принимается S] = 10 мм/дв.х qCT = 0,8 (от 0,75 до 0,85)
По [Табл. Д.1] выбирается согласно условия Рном> Рд.РАД
т. АИР180М2УЗ
Рном = 30 кВт
КПД = 91,5%
cos (р = 0,9
Shom = 2,5 %
J = 0,07 кг • м[7] [8] [9]
G= 180 кг
Уровень шума — 82 дБ
Кп = 2,2
^Чпах ~' 3
A-min = 1,9
Ki = 7,5
2) Определяется требуемое передаточное число (in)
Рном = 30 кВт пном = 2925 об/мин Режим работы — S1 in = 1,3 Варианты индивидуальных заданий в [Таблице 4.5.3]. |
Вид |
ант | шлифо вания | шлифования | изделия | Материал круга | 4, мм | Вк, мм | vK, м/с | тельные сведения |
1 | плоское | чистое тор- | сталь | электро- | 250 | 20 | 50 | dfc — диаметр |
2 | на прямо- | цом круга | корунд | 300 | 50 | 60 | шлифоваль- | |
3 | угольном | 350 | 40 | 55 | ного круга Вк — толщи- на шлифо- вального | |||
4 | столе | 400 | 60 | 65 | ||||
5 | 450 | 70 | 70 | |||||
6 | круглое | черновое | сталь | электро- | 350 | 60 | 30 | круга |
7 | наруж- | периферией | корунд | 750 | 50 | 35 | vK — окруж- | |
8 | нос | круга | 400 | 40 | 40 | ная скорость | ||
9 | 500 | 30 | 30 | круга | ||||
10 | 600 | 20 | 35 | |||||
11 | плоское | черновое | чугун | карборунд | 250 | 35 | 40 | |
12 | на круг- | торцом круга | 750 | 45 | 35 | |||
13 | лом | 300 | 55 | 30 | ||||
14 | столе | 700 | 65 | 40 | ||||
15 | 600 | 70 | 30 | |||||
16 | круглое | чистовое | чугун | Карбо- | 300 | 75 | 50 | |
17 | наруж- | периферией | РУВД | 650 | 70 | 55 | ||
18 | ное | круга | 350 | 65 | 60 | |||
19 | 550 | 60 | 65 | |||||
20 | 400 | 55 | 70 | |||||
21 | плоское | черновое | сталь | Электро- | 300 | 60 | 40 | |
22 | на прямо- | периферией | корунд | 350 | 50 | 35 | ||
23 | угольном | круга | 400 | 40 | 30 | |||
24 | столе | 450 | 30 | 40 | ||||
25 | 250 | 20 | 30 |
|
Таблица 4.5.3 — Варианты индивидуальных заданий. «Шлифовальные станки» |
Характер |
Шлифовальный круг |
Материал |
Дополни- |
Глава 5
Курсовое проектирование ОУ и ЭП
■ 5.1. Рекомендации по организации выполнения и защиты
Дата добавления: 2019-07-17; просмотров: 1206; Мы поможем в написании вашей работы! |
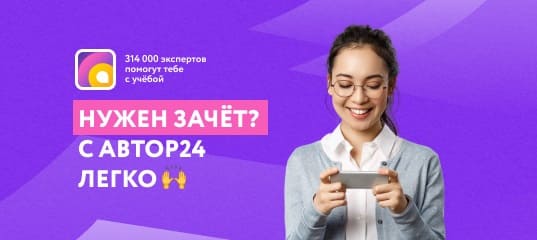
Мы поможем в написании ваших работ!