Сложная ректификационная колонна (схема)
МАССООБМЕННЫЕ ПРОЦЕССЫ
1 вопрос
Процессами массообмена называют такие процессы, в которых основную роль играет перенос вещества из одной фазы в другую. Движущей силой этих процессов является разность химических потенциалов (см. гл. 2). Как и в любых других процессах, движущая сила массообмена характеризует степень отклонения системы от состояния динамического равновесия. В пределах данной фазы вещество переносится от точки с большей к точке с меньшей концентрацией. Поэтому обычно в инженерных расчетах приближенно движущую силу выражают через разность концентраций, что значительно упрощает расчеты массообменных процессов.
Массообменные процессы широко используются в промышленности для решения задач разделения жидких и газовых гомогенных смесей, их концентрирования, а также для защиты окружающей природной среды (прежде всего для очистки сточных вод и отходящих газов). Например, практически в каждом химическом производстве взаимодействие обрабатываемых веществ осуществляется в реакторе, в котором обычно происходит только частичное превращение этих веществ в продукты реакции. Поэтому выходящую из реактора смесь продуктов реакции и непрореагировавшего сырья необходимо подвергнуть разделению, для чего эту смесь направляют в массообменную аппаратуру, из которой непрореагировавшее сырье возвращается в реактор, а продукты реакции направляются на дальнейшую переработку или использование.
|
|
Наибольшее распространение получили рассмотренные ниже массообменные процессы.
1. Абсорбция- избирательное поглощение газов или паров жидким поглотителем. Этот процесс представляет собой переход вещества из газовой (или паровой) фазы в жидкую. Наиболее широко используется для разделения технологических газов и очистки газовых выбросов.
Процесс, обратный абсорбции, т. е. выделение растворенного газа из жидкости, называют Десорбцией.
2. Перегонка и Ректификация — разделение жидких гомогенных смесей на компоненты при взаимодействии потоков жидкости и пара, полученного испарением разделяемой смеси. Этот процесс представляет собой Переход компонентов из жидкой фазы в паровую и из паровой в жидкую. Процесс ректификации используется для разделения жидких смесей на составляющие их компоненты, получения сверхчистых жидкостей и для других целей.
3. Экстракция (жидкостная)- извлечение растворенного в одной жидкости вещества другой жидкостью, практически не смешивающейся или частично смешивающейся с первой. Этот процесс представляет собой Переход извлекаемого вещества из одной жидкой /)азы в другую. Процесс применяют для извлечения растворенного вещества или группы веществ сравнительно невысоких концентраций.
|
|
4. АДсорбция- избирательное поглощение газов, паров или растворенных в жидкости веществ твердым поглотителем, способным поглощать одно или несколько веществ из смеси. Этот процесс представляет собой Переход веществ из газовой, паровой или жидкой 1шзы в твердую. Адсорбцию применяют для извлечения того или иного вещества (или веществ) достаточно низкой концентрации из six смеси. Процесс, обратный адсорбции, т. е. выделение сорби-рованного вещества из твердого поглотителя, называют Десорбцией.
5. Ионный обмен- избирательное извлечение ионов из растворов электролитов. Этот процесс представляет собой Переход извлекаемого вещества из жидкой фазы в твердую. Процесс применяют для извлечения веществ из растворов, в которых эти вещества находятся при низких концентрациях.
6. Сушка — удаление влаги из твердых влажных материалов, ц основном путем ее испарения. Этот процесс представляет собой Переход влаги из твердого влажного материала в газовую или паровую фазы. Сушку широко применяют в технике для предварительного обезвоживания перерабатываемых веществ или обезвоживания готового продукта.
|
|
7. Растворение и экстрагирование из твердых тел-это процессы перехода твердой фазы в жидкую(растворитель). Извлечение на основе избирательной растворимости какого-либо вещества (или веществ) из твердого пористого материала называют Экстракцией из твердого материала, или выщелачиванием.Применяют ее для извлечения ценных или токсичных компонентов из твердых материалов.
8. Кристаллизация-выделение твердой фазы в виде кристаллов из растворов или расплавов. Этот процесс представляет собой Переход вещества из жидкой фазы в твердую. Применяется, в частности, для получения веществ повышенной чистоты.
9. Мембранные процессы- избирательное извлечение компонен- ов смеси или их концентрирование с помощью полупроницаемой перегородки-мембраны. Эти процессы представляют собой Пере-од вещества (или веществ) из одной фазы в другую через разделяющую их мембрану. Применяются для разделения газовых и жидких смесей, очистки сточных вод и газовых выбросов.
Таким образом, во всех перечисленных выше процессах общим является переход вещества (или веществ) из одной фазы в другую. Процесс перехода вещества (или нескольких веществ) из одной фазы ^ другую в направлении достижения равновесия называют массопе-редачей. В отличие от теплопередачи, которая происходит обычно через стенку, массопередача осуществляется, как правило, при непосредственном соприкосновении фаз (за исключением мембранных процессов). При этом граница соприкосновения-т. е. поверхность контакта фаз-может быть подвижной (система газ-жидкость, пар-жидкость, жидкость-жидкость) или неподвижной (газ-твердое тело, пар-твердое тело, жидкость-твердое тело).
|
|
Перенос вещества внутри фазы — из фазы к границе раздела фаз или наоборот — от границы раздела в фазу — называют массоотдачей (по аналогии с процессом переноса теплоты внутри фазы-теплоотдачей).
Процессы массопередачи обычно обратимы. Причем направление перехода вещества определяется концентрациями вещества в фазах и условиями равновесия.
Процесс перехода вещества из одной фазы в другую в изолированной замкнутой системе, состоящей из двух или большего числа фаз, возникает самопроизвольно и протекает до тех пор, пока между фазами при данных условиях температуры и давления не установится подвижное фазовое равновесие. При этом в единицу времени из первой фазы во вторую переходит столько же молекул, сколько в первую из второй. Если теперь количество распределяемого вещества увеличить (например, в фазе Фу) на Пмолекул, то распределяемое вещество будет переходить из фазы Фу в фазу Ф^. Причем скорость перехода будет определяться не общим числом молекул (тА-п) вещества М, находящегося в фазе Фу, а числом молекул, избыточным по отношению к равновесному (т). Так как концентрация пропорциональна числу молекул, то скорость перехода распределяемого вещества из одной фазы в другую пропорциональна разности между фактической (или рабочей) концентрацией распределяемого вещества в данной фазе (т+п) и равновесной (w). А это означает, что чем больше такая разница, тем больше (при всех прочих равных условиях) перейдет вещества М из одной фазы в другую. Если эта разница отрицательна, то вещество М переходит из фазы Ф^ в фазу Фу (т. е. процесс пойдет в обратном направлении).
Таким образом, знание равновесных концентраций распределяемого вещества позволяет определить направление процесса-из какой фазы в какую будет переходить вещество М — и в определенной степени-скорость процесса.
Как отмечалось выше, массообменные процессы протекают лишь при нарушении фазового равновесия. Только при этом условии распределяемое вещество переходит из одной фазы в другую. При этом различают два вида переноса вещества — Молекулярный и конвективный.
В неподвижной среде распределяемое вещество переходит из внутренних слоев данной (первой) фазы к поверхности раздела фаз и, пройдя ее, распределяется по всему объему другой фазы, находящейся в контакте с первой. Такой переход массы вещества из одной фазы в другую называют Молекулярной диффузией. Она является следствием теплового движения молекул (ионов, атомов), которому оказывают сопротивление силы внутреннего трения.
Конвективный перенос (конвективная диффузия) характеризуется перемещением (переносом) вещества движущимися частицами по-ока в условиях турбулентного движения фаз. Конвективный перенос вещества под действием турбулентных пульсаций иногда называют Турбулентной диффузией.
Основным кинетическим уравнением массообменных процессов является уравнение массопередачи, которое основано на общих кинетических закономерностях химико-технологических процессов.
Скорость процесса [в кг/(м2 — с)] Равна движущей силе Д, Деленной ‘Ui сопротивление R:
1 i, c dM-количество вещества, перешедшего из одной фазы в другую в единицу времени; dF поверхность контакта фаз.
Обозначив /R = К, получим
В последнем выражении, называемом Основным уравнением массопередачи, величина К характеризует скорость процесса переноса вещества из одной фазы в другую. По аналогии с процессом теплопередачи коэффициент К называют Коэффициентом массо-чсредачи.
Найдем размерность коэффициента массопередачи:
I. e. Коэффициент массопередачи К показывает, какое количество /•^определяемого вещества переходит из фазы в фазу в единицу времени через единицу поверхности контакта фаз при движущей < Иле, равной единице. Размерность движущей силы может быть ;различной, а от нее зависит и размерность К.
Обычно уравнение массопередачи применяют для определения поверхности F контакта фаз, а исходя из этой поверхности — размеров массообменных аппаратов. В интегральной форме уравнение массопередачи, записанное относительно величины F, примет следующий вид:
Обычно величина К является функцией многих переменных, и единого уравнения для определения значения К нет.
При анализе массообменных процессов будем исходить из условия состояния границы контакта фаз, что существенно различает механизмы процессов переноса массы. По этому принципу массообменные процессы подразделяют на Массопередачу в системах со вободной границей раздела фаз (газ-жидкость, пар-жидкость, жидкость-жидкость), Массопередачу в системах с неподвижной поверхностью контакта фаз (системы газ-твердое тело, пар-твердое тело, жидкость-твердое тело) и Массопередачу через полупроницаемые перегородки (мембраны).
2 вопрос
Основной закон массопередачи можно сформулировать, исходя из общих физических кинетических закономерностей химико-технологических процессов: скорость процесса равна движущей силе, делённой на сопротивление, то есть
,
где - количество вещества, перешедшего из одной фазы в другую;
- поверхность фазового контакта;
- время;
- движущая сила массообменного процесса;
- сопротивление.
Если вместо взять обратную величину
- коэффициент скорости или, как его называют в рассмотренном явлении, коэффициент массопередачи, предыдущее уравнение имеет вид:
(11.5)
При условии, когда отнесено к единице времени, уравнение (11.5) можно переписать так:
(11.6)
Уравнения (11.5) и (11.6) называются основными уравнениями массопередачи.
В аппаратуре, используемой для проведения массообменных процессов, равновесные концентрации распределяемого вещества никогда не достигаются. Действительные концентрации распределяемого вещества, илирабочие концентрации, всегда отличаются от равновесных.Разность между этими концентрациями, характеризующая степень отклонения от равновесия, и представляет собой движущую силу массообменных процессов.
3 вопрос
Насыщенный и перегретый пар и их параметры
Насыщенным называется пар, находящийся в равновесном состоянии с жидкостью. Температура такого пара зависит от давления, т.е. определённому давлению насыщенного пара соответствует определённая температура.
Насыщенный пар может быть сухим и влажным. Сухой парне содержит жидкости. Влажный насыщенный пар – это смесь пара с жидкостью, равномерно распределённой по его массе.
Состояние сухого насыщенного пара определяется только одним параметром – давлением или температурой.
Состояние влажного насыщенного пара определяется двумя параметрами: давлением или температурой и степенью сухости.
Степенью сухости (Х) – называется массовая доля сухого пара в составе водяного пара.
Теплосодержание (энтальпия) насыщенного пара слагается из тепла нагрева жидкости до температуры испарения СВ (tК - tН) и скрытой теплоты парообразования или теплоты испарения (r).
Н = СВ (tК - tН) + r [кДж/кг о С].
Теплота парообразования r, характеризуется количеством теплоты, необходимым для превращения 1 кг воды в сухой насыщенный пар.
При температуре 374оС и давлении 2,25 МПа вся масса воды мгновенно превращается в пар без дополнительной затраты теплоты, т.е. образуется перегретый пар, температура которого выше температуры насыщенного пара того же давления. Этот пар не имеет определённой зависимости между температурой и давлением.
4 вопрос
давления насыщенного пара при заданной температуре является расчет по уравнению Антуана:
; Рs
,
где
Рs - давление насыщенного пара, кПа;
tР - рабочая (заданная) температура, 0С;
А, В, С - константы уравнения Антуана из справочной литературы
Давление насыщенного пара может быть так же определено по номограмме
(в мм рт.ст.)
Зная давление насыщенного пара можно рассчитать его концентрацию в паро-воздушной смеси и установить пожарную опасность смеси насыщенного пара с воздухом.
Расчет объемной концентрации паров по давлению насыщенного пара | Пример 10. Резервуар заполнен бензолом С6Н6. Вычислить объемную и массовую концентрацию паров бензола в свободном пространстве резервуара. Температура 100С, давление 780 мм рт.ст. |
Решение:
Зная величину давления насыщенного пара в емкости, можно определить объемную концентрацию паров жидкости при данных условиях. Величина давления насыщенного пара не зависит от объема жидкости в резервуаре.
Объемная концентрация паров (газов) в замкнутом объеме рассчитывается через давление насыщенного пара по формуле:
, % ,
где
jОБ - объемная концентрация газа или пара, %;
Р S- давление насыщенного пара при данной температуре, мм рт.ст., кПа,
МПа, атм; Р s рассчитывают по уравнению Антуана или определяют по
номограмме.
Р АТМ - внешнее давление, мм рт.ст., кПа, МПа, атм.
При температуре 100С для бензола Р ПАР = 40 мм рт.ст.( по номограмме). Тогда
5,1 %
Определяем массовую концентрацию паров бензола.
Для этого воспользуемся формулой для определения массовой концентрации паров
где
jМАС - массовая концентрация, кг(г)/м3;
Рs - давление насыщенного пара, мм рт.ст., кПа, МПА, атм;
Р АТМ - внешнее давление, мм рт.ст., кПа, МПа, атм;
М - молярная масса вещества, г/моль, кг/кмоль,
VМ - молярный объем газа или пара, л/моль, м3/кмоль.
Давление насыщенных паров (ДНП) — это давление паров при определенной температуре в условиях динамического равновесия с жидкостью. Давление насыщенных паров — важный физический показатель, характеризующий испаряемость
5 вопрос
Парциа́льное давление (лат. partialis «частичный» от pars «часть») — давление отдельно взятого компонента газовой смеси[1][2]. Общее давление газовой смеси является суммой парциальных давлений её компонентов.
В химии парциальное давление газа в смеси газов определяется как указано выше. Парциальное давление газа, растворённого в жидкости, является парциальным давлением того газа, который образовался бы в фазе газообразования в состоянии равновесия с жидкостью при той же температуре. Парциальное давление газа измеряется как термодинамическая активность молекул газа. Газы всегда будут вытекать из области с высоким парциальным давлением в область с более низким давлением; и чем больше разница, тем быстрее будет поток. Газы растворяются, диффундируют и реагируют соответственно их парциальному давлению и не обязательно зависимы от концентрации в газовой смеси.
Для идеального газа парциальное давление в смеси равно давлению, которое будет оказываться, если бы он занимал тот же объём, что и вся смесь газов, при той же температуре. Причина этого в том, что между молекулами идеального газа по определению не действуют силы притяжения или отталкивания, их соударения между собой и со стенками сосуда абсолютно упруги, а время взаимодействия между молекулами пренебрежимо мало по сравнению со средним временем между столкновениями. Насколько условия реально существующей смеси газов близки этому идеалу, настолько общее давление смеси равно сумме парциальных давлений каждого газа смеси,
6 вопрос
Ректификация применяется для разделения жидких смесей на компоненты или фракции, различающиеся летучестью, (фугитивностью), и осуществляется путем многократного двустороннего массо-и теплообмена между противоточно движущимися паровым и жидкостным потоками — флегмой.
Взаимодействие фаз при ректификации представляет собой диффузию легколетучего компонента (л.л.к.) из жидкости в пар и труднолетучего компонента (т.л.к.) из пара в жидкость. Способ контактирования потоков может быть ступенчатый (в тарельчатых колоннах) или непрерывный (в насадочных колоннах).
Назначение контактных устройств (тарелок, насадки) состоит в создании условий, способствующих максимальному приближению парового и жидкостного потоков. Чтобы эти потоки могли обмениваться веществом и энергией, они должны быть неравновесны друг к другу. При контактировании парового и жидкостного потоков в результате массо- и теплообмена величина неравновесности уменьшается затем потоки отделяются один от другого, и процесс продолжается путем нового контактирования этих фаз уже на другой смежной ступени, с другими жидкими и паровыми потоками. В результате многократно повторяющегося на последовательных тарелках (ступенях), контактирования движущихся в противотоке по высоте колонны жидкости и пара состав взаимодействующих фаз существенно изменяется: паровой поток при движении вверх обогащается л.л.к., а жидкостный, стекая вниз, обедняется им, т. е. обогащается т.л.к. При достаточно большом пути контактирования противоположно движущихся потоков можно получить пар, выходящий из верхней части колонны, представляющий собой более или менее чистый л.л.к., конденсация которого дает дистиллят, а из нижней части колонны — сравнительно чистый т.л.к., так называемый кубовый остаток.
Флегма образуется в результате частичной конденсации паров, выходящих из верхней части колонны, в специальных теплообменных: аппаратах — дефлегматорах — или вводится в колонну в виде питания. Для создания парового потока в колонне в ее нижнюю часть вводят определенное количество тепла непосредственным впуском греющего пара (случай открытого обогрева колонны) или подачей его в специальный теплообменник, через поверхность теплопередачи которого тепло передается кипящему кубовому остатку (случай закрытого обогрева).
Чаще разделяемую смесь (питание) в жидком, парообразном или смешанном виде подают в середину колонны (рис. 2) между концентрационной, или укрепляющей и отгонной, или исчерпывающей частью колонны. Верхнюю тарелку отгонной части колонны называют питающей тарелкой. Колонна, имеющая концентрационную и отгонную части, называется полной ректификационной колонной (рис. 2а). В такой колонне создаются наиболее благоприятные условия для получения в практически чистом виде обоих компонентов бинарной смеси, однако возможно и самостоятельное действие отгонной и концентрационной колонны. Такие колонны именуют неполными.
Рис. 2 Схемы ректификационных колон
1 – дефлегматор; 2 – колонна; А – разделяемая смесь; В – вода; Д – дистиллят; П – пар; О – остаток.
Из нижней части неполной отгонной колонны (рис. 2б) в жидком виде отводится практически чистый т.л.к., над верхней тарелкой получается пар, несколько обогащенный л.л.к. В неполную концентрационную колонну, (рис. 2в) разделяемую смесь вводят в парообразном виде под ее нижнюю тарелку. Из верхней части концентрационной колонны отводят в парообразном, виде практически чистый л.л.к., а с нижней тарелки получается флегма, несколько обогащенная т.л.к. В отличие от полной ректификационной колонны в неполных колоннах для дальнейшего обогащения дистиллята отгонной колонны л.л.к. или остатка концентрационной колонны т.л.к. нужна их дополнительная ректификация.
Орошение флегмой, необходимое для осуществления процесса ректификации, в отгонных колоннах достигается подачей питания в жидком виде на верхнюю тарелку. В полных и укрепляющих колоннах орошение проводят за счет части конденсата пара, выходящего из верхней части колонны. Остальной пар образует дистиллят — верхний продукт колонны, поэтому орошение и отбор дистиллята количественно связаны между собой.
Отношение количества горячего (при температуре конденсации) орошения или флегмы (L) к количеству дистиллята (D) называется флегмовым числом (R):
R=L/D = (G — D)/D, (1)
где G — количество пара, выходящего из колонны.
Флегмовое число может изменяться от 0 до ∞. При R=0 не будет массообмена и обогащения пара л.л.к. При R =∞ весь конденсат паров, выходящий из колонны, полностью поступает на орошение; в этом случае отбор дистиллята равен нулю, колонна работает «на себя» (при установившемся процессе нижний продукт колонны будет иметь тот же состав, что и исходное питание). Практически колонна должна работать при 0<R<∞.
Отбирать дистиллят можно после частичной или полной конденсации пара (рис. 3). В 1 варианте обеспечивается дополнительное обогащение дистиллята л.л.к. вследствие частичной конденсации пара и массообмена между флегмой и паром при противоточном движении их в дефлегматоре. Во 2варианте пар, выходящий из колонны, дистиллят и флегма имеют одинаковый состав, и дефлегматор не дает никакого укрепляющего эффекта. В спиртовой промышленности обычно используют первый вариант.
Открытый обогрев колонн применим в том случае, когда греющий пар не оказывает отрицательного влияния на качество конечных продуктов, не взаимодействует с продуктами ректификации и не образует новых, трудноразделимых систем в колонне. При открытом обогреве конденсат греющего пара смешивается с конечным продуктом разделения (остатком). Закрытый обогрев требует наличия пара более высоких параметров.
Процесс массообмена между паровым и жидкостным потоками на контактных устройствах определяется величиной поверхности контакта фаз (F m2), средней разностью концентраций, или средней движущей силой процесса (∆С кг/кг), и коэффициентом массопередачи, отнесенным к 1 м2 поверхности фазового контакта [К кг/(м2*ч)]. Коэффициент массопередачи зависит от природы вещества и гидродинамического режима контакта фаз. Количество вещества, перешедшего из одной фазы в другую (в кг/ч), определяется равенством
М=К*F*∆C (2)
Конструкция контактного устройства должна обеспечивать возможно большую величину массообмена на нем. Это достигается в первую очередь созданием развитой поверхности контакта фаз. Тарелки ректификационных колонн могут быть колпачковые, решетчатые, чешуйчатые, клапанные и др. (рис. 4). Насадочная колонна представляет собой цилиндр, наполненный насадкой — телами с развитой поверхностью (кольца, шары, седла, сетки, блоки, пакеты, рейки и т. д.). Пар и жидкость контактируют на поверхности насадки при противоточном движении.
Работа контактных устройств оценивается пропускной способностью по пару и жидкости, способностью разделять рабочую смесь, диапазоном устойчивой работы, гидравлическим сопротивлением и др.
Пропускная способность по пару и жидкости определяет производительность колонн, или удельный съем конечного продукта с единицы поперечного сечения колонн.
Способность разделять перегоняемую смесь называют эффективностью контактного устройства или колонны в целом и обычно оценивают числом теоретических тарелок (ступеней изменения концентраций), или числом единиц переноса. Эффективность тарельчатых колонн, как правило, оценивают числом теоретических тарелок (т.т.).
Допустим, поступающая на тарелку жидкость (рис. 5, а) содержит Xi+1л.л.к., а покидающая ее — X*i; проходящий через тарелку пар соответственно содержит Yi и у*i+1 того же компонента. Если тарелка обеспечивает контакт пара и жидкости, в результате которого покидающие тарелку пар Y*.i+1 и жидкость Х*i будут равновесны, то такая тарелка имеет эффективность, равную одной теоретической тарелке.
Движущая сила массообменных процессов определяется степенью отклонения от равновесия или «расстоянием» от равновесия. Последнее определяется разностью между рабочей и равновесной концентрациями или равновесной и рабочей, в зависимости от того, какие из них больше. Движущую силу можно выражать либо через концентрации распределяемого вещества в фазе , то есть через
, либо через концентрации его в фазе
, то есть через
.
Во всех случаях, движущей силой процесса будет разность между рабочей и равновесной концентрациями, взятая с положительным знаком.
Из изложенного следует, что основное уравнение массопередачи можно записать двояко:
(11.13)
и
(11.14)
Движущая сила меняется с изменением рабочих концентраций, поэтому для всего процесса массообмена, протекающего в пределах изменения концентраций от начальных до конечных, должна быть определена величина средней движущей силы.
При определении величины средней движущей силы могут встретиться два случая:
1. зависимость между равновесными концентрациями не линейна; для этого случая равновесная концентрация определяется общей функциональной зависимостью ;
Величина средней движущей силы для случая .
,
Подобная структура уравнений сохранится и в тех случаях, когда вместо концентраций используют другие параметры, характеризующие систему: энтальпию, химический потенциал.
2. зависимость между равновесными концентрациями линейна, то есть (где
- постоянная величина).
В случае когда между равновесными и рабочими концентрациями существует прямолинейная зависимость, для определения средней движущей силы и числа единиц переноса могут быть выведены более простые соотношения.
,
где - движущая сила в начале поверхности фазового контакта;
- движущая сила в конце поверхности фазового контакта.
где - движущая сила в начале поверхности фазового контакта;
- движущая сила в конце поверхности фазового контакта.
Следовательно, для прямолинейной равновесной зависимости средняя движущая сила процесса определяется как средняя логарифмическая между движущими силами в начале и в конце поверхности фазового контакта.
7 Вопрос
Ректификационные колонны применяются в процессах дистилляции, экстрактивной ректификации, экстракции жидкостей, теплообмена между паром и жидкостью и в других процессах[1]. Один и тот же принцип действия ректификационной колонны используется как в относительно простых лабораторных приборах, так и в сложных промышленных установках нефтеперерабатывающей, нефтехимической, химической, газовой, пивоваренной и других отраслей. Диаметр промышленных ректификационных колонн может достигать 16 метров, а высота — 90 метров и более.
Исходная смесь, нагретая до температуры питания tf в паровой, парожидкостной или жидкой фазе, поступает в колонну в качестве питания (Gf). Зону, в которую подаётся питание, называют эвапорационной, так как там происходит процесс эвапорации — однократного отделения пара от жидкости.
Пары поднимаются в верхнюю часть колонны, охлаждаются, конденсируются в холодильнике-конденсаторе и подаются обратно на верхнюю тарелку колонны в качестве орошения (флегма). Таким образом, в верхней части колонны (укрепляющей) противотоком движутся пары (снизу вверх) и стекает жидкость (сверху вниз). Стекая вниз по тарелкам, жидкость обогащается тяжелокипящими компонентами, а пары чем выше поднимаются в верх колонны, тем более обогащаются легкокипящими компонентами. Таким образом, отводимый с верха колонны продукт обогащен легкокипящим компонентом. Продукт, отводимый с верха колонны, называют дистиллятом. Часть дистиллята, сконденсированного в холодильнике и возвращённого обратно в колонну, называют орошением или флегмой. Отношение количества возвращаемой в колонну флегмы и количества отводимого дистиллята называется флегмовым числом.
Для создания восходящего потока паров в кубовой (нижней, отгонной) части ректификационной колонны часть кубовой жидкости направляют в теплообменник, образовавшиеся пары подают обратно под нижнюю тарелку колонны.
Таким образом, в кубе колонны создается 2 потока:
· 1 поток — жидкость, стекающая с верха (из зоны питания+орошение)
· 2 поток — пары, поднимающиеся с низа колонны.
Кубовая жидкость, стекая сверху вниз по тарелкам, обогащается высококипящим компонентом, а пары обогащаются легкокипящим компонентом[2].
В случае, если разгоняемый продукт состоит из двух компонентов, конечными продуктами являются дистиллят, выходящий из верхней части колонны, и кубовый остаток (менее летучий компонент в жидком виде, вытекающий из нижней части колонны). Ситуация усложняется, если необходимо разделить смесь, состоящую из большого количества фракций. В этом случае используются аппараты, подобные изображённому на картинке.
Упрощенная технологическая схема непрерывной ректификации
Исходная смесь, нагретая до температуры питания tf в паровой, парожидкостной или жидкой фазе, поступает в колонну в качестве
8 вопрос
Сложная ректификационная колонна (схема)
Рис. IV-31. Схема сложной колонны для ректификации четырехкомпонентной смеси:
В такой сложной колонне процесс протекает следующим образом. Флегма, образованная при конденсации паров на верху колонны, последовательно перетекает с тарелки на тарелку . достигнув нижней тарелки этой колонны, флегма делится на два потока. Один поток отводится в отпарную секцию колонны III, где получается продукт Wm. Второй поток флегмы перетекает на верхнюю тарелку колонны II, являясь орошением для этой колонны.
Пары G'm из отгонной секции колонны III возвращаются под нижнюю тарелку концентрационной части этой колонны. Аналогично протекает процесс и в других колоннах II и /.
Дата добавления: 2019-07-15; просмотров: 446; Мы поможем в написании вашей работы! |
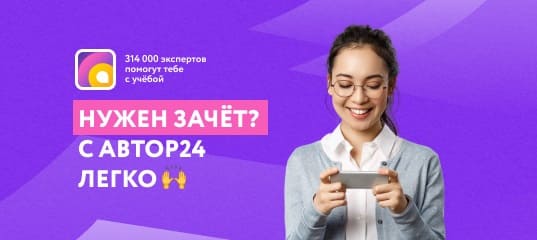
Мы поможем в написании ваших работ!