Порядок подбора и расчета подшипников
При подборе типа подшипника должны быть прежде всего учтены конструктивно-эксплуатационные требования: необходимость восприятия осевых сил, самоустановка, возможность монтажа подшипника в сборе или отдельными кольцами, регулирования осевого натяга или зазора и т.п. Очень существенным для рационального подбора подшипников является правильное назначение срока их службы. Для машин со сроком службы менее 2500 часов срок службы подшипников назначается равным сроку службы машины. Для машин с большими сроками службы срок службы подшипников назначается в два, три и т.д. раз меньше срока службы машины так, чтобы он не превышал 50000 часов.
При известных нагрузках на подшипник по вычисленной приведенной нагрузке Р и расчетному ресурсу L определяют требуемую динамическую грузоподъемность С = PL1/m. По динамической грузоподъёмности, пользуясь каталогом или справочником, выбирают подшипник.
Однако подбор подшипников таким способом возможен не всегда, так как от типа и размера подшипника зависят положения точек приложения к валу радиальных реакций подшипников и, следовательно, величина нагрузок на них. Кроме того, в шариковых радиальных однорядных и радиально-упорных подшипниках с углом контакта α ≤ 18° положение точки радиальной реакции и величина коэффициента Y осевой нагрузки зависят от отношения Fa/ C0. Поэтому значительно чаще подшипники выбирают предварительно по конструктивным соображениям, исходя из диаметра вала в месте посадки.
|
|
При выборе радиально-упорных шарикоподшипников угол контакта рекомендуется назначать в зависимости от соотношения осевой и радиальной нагрузок:
Отношение до 0,35 0,35…0,80 0,8…1,2 свыше 1,2
Угол контакта 0о 12о 26о 36о
Затем определяют точки приложения и величины радиальных реакций подшипников, вычисляют приведенные динамические нагрузки Р и проверяют расчетом их ресурс Lh.
СОЕДИНЕНИЯ ВАЛОВ С УСТАНОВЛЕННЫМИ НА НИХ ДЕТАЛЯМИ
Соединения вал – ступица предназначены для закрепления деталей на валах и передачи крутящего момента. Основными типами соединений являются: шпоночное соединение; шлицевое (зубчатое) соединение; штифтовое соединение; соединение с гарантированным натягом (прессовое соединение).
Выбор типа соединения определяется требованиями конструкции, величиной передаваемого момента и требованиями прочности вала.
Расчет шпоночного соединения
В авиационных конструкциях находят применение преимущественно соединения с призматической, сегментной и круглой шпонками.
Основные размеры соединения с призматической шпонкой определяются по ГОСТ 23360 – 78 и показаны на рис. 19.
|
|
Размеры сечений определяются по табл. 24 в зависимости от диаметра вала.
Рис.19
Таблица 24
Основные размеры соединения с призматической шпонкой ( по ГОСТ 23360 – 78 )
Диаметр вала, мм | Сечение шпонки, ![]() | Глубина паза вала, ![]() |
Свыше 10 до 12 | 4×4 | 2,5 |
Свыше 12 до 17 » 17 » 22 » 22 » 30 | 5×5 6×6 8×7 | 3,0 3,5 4,0 |
Свыше 30 до 38 » 38 » 44 » 44 » 50 » 50 » 58 » 58 » 65 | 10×8 12×8 14×9 16×10 18×11 | 5,0 5,0 5,5 6,0 7,0 |
Свыше 65 до 75 » 75 » 85 » 85 » 95 » 95 » 110 » 110 » 130 | 20×12 22×14 25×14 28×16 32×18 | 7,5 9,0 9,0 10,0 11,0 |
Длина шпонки назначается по длине ступицы, установленной на валу детали, округляется до ближайшего из ряда длин шпонок: 6, 8, 10, 12, 14, 16, 18, 20, 25, 28, 32, 36, 40, 45, 50, 56, 63, 70, 80, 90, 100.
Проверка прочности соединения производится по напряжениям смятия боковых граней:
.
Здесь - расчетная длина с учетом типа исполнения шпонки (см. рис.19). При этом исполнение 1 является предпочтительным.
Допускаемое напряжение смятия определяется по формуле . При этом в качестве предела текучести
принимается меньшее из трех значений – для материала вала, материала ступицы детали и материала шпонки. Допускаемый запас прочности принимается равным:
|
|
- при малоизменяющейся нагрузке;
- при ударной нагрузке и работе с частыми пусками и остановками.
Для реверсивного нагружения допускаемый запас прочности увеличивается на 30%.
Если условия прочности не обеспечиваются, возможно изменение материалов деталей соединения или замена шпоночного соединения шлицевым.
Основные размеры соединения с сегментной шпонкой определяются по ГОСТ24071 – 80 и показаны на рис. 20.
Рис.20
Соединение с сегментной шпонкой применяется преимущественно для установки на концевых участках валов деталей типа маховики, рукоятки и т.п. Концевые участки валов могут быть цилиндрическими или коническими.
Размеры шпонки выбираются в зависимости от диаметра вала по табл. 25.
Проверка прочности соединения производится на смятие боковых граней и срез шпонки:
и
.
При этом допускаемое напряжение смятия определяется, как показано выше, а допускаемое напряжение среза по формуле
, где
- предел текучести на сдвиг для материала шпонки.
|
|
Расчетная длина соединения может быть принята равной
.
Таблица 25
Основные размеры соединения с сегментной шпонкой ( по ГОСТ 24071 – 80 )
Диаметр вала ![]() | Размеры шпонки ![]() | Глубина паза ![]() |
Свыше 10 до 12 | 3×6,5×16 | 5,3 |
Свыше 12 до 14 » 14 » 16 » 16 » 18 » 18 » 20 » 20 » 22 » 22 » 25 » 25 » 28 | 4×6,5×16 4×7,5×19 5×6,5×16 5×7,5×19 5×9×22 6×9×22 6×10×25 | 5,0 6,0 4,5 5,0 7,0 6,5 7,5 |
Свыше 28 до 32 » 32 » 38 | 8×11×28 10×13×32 | 8,0 10,0 |
Соединение с цилиндрическими шпонками не стандартизовано и применяется в конструкциях с общим торцом у ступицы детали и вала, допускающим изготовление отверстий в собранном виде, как показано на рис. 21.
Рис.21
Диаметр шпонки и ее длину рекомендуется принимать из нормализованных рядов диаметров и длин. При этом диаметр шпонки должен удовлетворять условию . Так как шпонка устанавливается в отверстие с натягом, распределение нагрузки по ее длине, а также между шпонками, если их несколько, более равномерное, чем для других типов шпонок. В этой связи допускаемые напряжения смятия увеличиваются на 25%. Расчет соединения сводится к определению требуемого числа шпонок по формуле
.
Если требуемое число шпонок превышает шесть, целесообразно заменить соединение на шлицевое.
Расчет шлицевого соединения
В авиационных конструкциях применяются соединения с прямобочными, эвольвентными и треугольными шлицами. Соединения с треугольными шлицами применяются только для весьма тонкостенных деталей и в настоящем пособии не рассматриваются.
Основные размеры соединений с прямобочными и эвольвентными шлицами показаны на рис. 22 и 23 и приведены в табл. 26 и 27.
При выборе размеров соединения для ступенчатых валов необходимо обеспечить, чтобы диаметр по впадинам шлицев был больше, чем диаметр соседнего участка вала. Разность диаметров определяется технологическими требованиями.
Таблица 26
Основные размеры соединения с прямобочными шлицами (по ГОСТ 1139 – 80 )
![]() | | ![]() | ![]() | | ![]() | ||||
Легкая серия | |||||||||
6×23×26 6×26×30 6×28×32 8×32×36 8×36×40 8×42×46 8×46×50 | 6 6 7 6 7 8 9 | 0,3 0,3 0,3 0,4 0,4 0,4 0,4 | 8×52×58 8×56×62 10×62×68 10×72×78 10×82×88 10×92×98 10×102×108 | 10 10 12 12 12 14 16 |
0,5 | ||||
Средняя серия | |||||||||
6×13×16 6×16×20 6×18×22 6×21×25 6×23×28 6×26×32 6×28×34 8×32×38 8×36×42 | 3,5 4 5 5 6 6 7 6 7 | 0,3 0,3 0,3 0,3 0,3 0,4 0,4 0,4 0,4 | 8×42×48 8×46×54 8×52×56 8×56×65 8×62×72 10×72×82 10×82×92 10×92×102 10×102×112 | 8 9 10 10 12 12 12 14 16 | 0,4 0,5 0,5 0,5 0,5 0,5 0,5 0,5 0,5 | ||||
Рис.22
Рис.23
Для эвольвентных шлицев диаметр окружности впадин зубьев определяется по формулам:
- при плоской впадине;
- при закругленной впадине.
Таблица 27
Наружные диаметры D, модули m и числа зубьев z эвольвентного шлицевого соединения (по ГОСТ 6033 – 80)
D, мм | Модуль m | ||||||||||||||
Ряд | 1 | 1,25 | 2 | 3 |
|
| 5 | ||||||||
Ряд | 2 | 1 | 1,5 | 2,5 |
| 3,5 | 4 |
| |||||||
1 | 2 | Число зубьев | |||||||||||||
20 - 25 - 30 - 35 - 40 - 45 - 50 - 55 - 60 - 65 70 75 80 85 90 95 100 110 120 140 | 22 28 32 38 42 48 52 58 62 130 150 | 18 20 24 26 28 30 34 36 38 40 44 45 48 50 54 56 58 | 14 16 18 21 22 24 26 29 30 32 34 37 38 40 42 45 46 48 50 54 58 62 | 12 13 15 17 18 20 22 24 25 26 28 30 32 33 35 37 38 40 42 45 48 52 55 58 62 64 72 | 8 9 11 12 13 14 16 18 18 20 21 22 24 24 26 28 28 30 31 34 36 38 41 44 46 48 54 58 64 68 74 | 6 7 8 10 10 11 12 14 14 15 16 18 18 19 20 22 22 23 24 26 28 30 32 34 36 38 42 46 50 54 58 |
6 7 8 8 9 10 11 12 12 13 14 15 16 17 18 18 19 20 22 24 25 27 28 30 32 35 38 42 45 48 |
12 12 12 12 14 14 16 16 18 18 20 22 24 24 26 28 30 34 36 38 42 |
6 7 8 8 9 10 10 11 11 12 13 13 14 15 16 17 18 20 21 22 24 26 28 31 34 36 | 6 7 7 8 8 9 9 10 10 11 11 12 13 14 15 16 18 18 20 22 24 26 28 | |||||
Проверка прочности соединения производится на смятие боковых поверхностей шлицев:
.
Здесь - число шлицев.
Средний диаметр соединения определяется по формулам:
- для соединения с прямобочными шлицами;
- для соединения с эвольвентными шлицами.
Рабочая высота боковой грани определяется по формулам:
- для соединения с прямобочными шлицами;
- для соединения с эвольвентными шлицами.
Расчетная длина соединения определяется длиной
ступицы установленной детали. Если в соединении имеются дополнительные цилиндрические центрирующие пояски (см. рис.23), расчетную длину соединения следует принять равной
.
Допускаемое напряжение смятия определяется по формуле
.
При этом принимается минимальное значение предела текучести из двух значений – для вала и для ступицы установленной детали.
Запас прочности принимается равным .
Коэффициент, учитывающий неравномерность распределения напряжений смятия, определяется по формуле
.
Коэффициент, учитывающий точность изготовления, принимается равным:
- при высокой точности изготовления;
- при невысокой точности изготовления.
Коэффициент, учитывающий неравномерность распределения нагрузки между зубьями (шлицами), определяется по эмпирическим формулам:
- при
;
- при
>0,6.
Здесь - коэффициент, зависящий от радиальной нагрузки
в соединении.
Если в соединении имеются дополнительные центрирующие пояски (см. рис.23), следует принять .
Коэффициент неравномерности распределения нагрузки по длине шлицевого соединения определяется в зависимости от схемы нагружения соединения, как показано на рис. 24 .
Если радиальная нагрузка смещена от середины ступицы в сторону места подвода крутящего момента, то
.
Если радиальная нагрузка смещена в сторону, противоположную месту подвода крутящего момента, то
- при
>
;
- при
<
.
Значение коэффициента , учитывающего влияние опрокидывающего момента, определяется по графику, приведенному на рис. 25.
Рис. 24 Рис.25
При этом параметр определяется по формуле
,
где опрокидывающий момент определяется выражением
.
Здесь и
- смещения от центра соединения соответственно радиальной F и осевой
нагрузок, определяемые по чертежу конструкции (см. рис.24). Значения F, Fa, e и r определяются с учетом их знаков в системе координат, приведенной на рис. 24.
Если радиальная нагрузка в соединении равна нулю или мала ( <0,2), значение коэффициента
следует определять по формуле:
.
Если в соединении имеются дополнительные центрирующие пояски, следует принять .
Коэффициент , учитывающий деформации вала и ступицы на длине соединения, для прямобочных шлицев определяется по табл. 28.
Таблица 28
Серия | Наружный диаметр, | Величина | |||
0,75 | 1,00 | 1,25 | 1,70 | ||
Легкая | До 26 30…50 50…120 | 1,20 1,30 1,50 | 1,30 1,50 1,80 | 1,50 1,70 2,20 | 1,70 2,00 2,60 |
Средняя | До 19 20…30 32…50 54…112 свыше 112 | 1,34 1,40 1,60 1,80 2,05 | 1,60 1,70 1,90 2,40 2,80 | 1,85 2,00 2,40 2,90 3,40 | 2,10 2,30 2,80 3,50 4,10 |
Для эвольвентных соединений значение коэффициента определяется по табл. 29 в зависимости от безразмерного параметра
.
Таблица 29
![]() | 1,5 | 2,0 | 3,0 | 4,0 | 5,0 | 6,0 | 7,0 |
![]() | 1,36 | 1,60 | 2,20 | 2,84 | 3,60 | 4,26 | 5,00 |
Условная длина шлицевого соединения выбирается в зависимости от соотношения диаметра ступицы и среднего диаметра шлицев:
- при
;
- при
;
- при
< 1,4.
Расчет на изнашивание выполняется для подвижных шлицевых соединений. Условие износостойкости имеет вид:
.
Допускаемое напряжение изнашивания рекомендуется определять по формуле
.
Базовое значение допускаемого напряжения изнашивания определяется по табл. 30 в зависимости от твердости поверхности шлицев и параметров
и
. Значение базового напряжения увеличивается или уменьшается в зависимости от условий работы соединения. Так при реверсивной работе
, иначе
.
Таблица 30
Параметры нагружения | Термообработка и твердость | ||||||
|
| без термообр. 20HRC | улуч-шение 28HRC | закалка
| цемент. или азотир. | ||
40HRC | 45HRC | 52HRC | |||||
0,59 | 0 0,25 0,50 | 38 21 18 | 42 23 21 | 55 29 25 | 69 36 32 | 75 39 35 | 83 44 39 |
0,50 | 0 0,25 0,50 | 47 32 22 | 55 37 26 | 67 47 34 | 85 60 42 | 92 66 45 | 100 72 50 |
0,42 | 0 0,25 0,50 | 65 42 35 | 76 49 41 | 92 60 50 | 116 75 63 | 127 82 68 | 141 91 76 |
0,35 | 0 0,25 0,50 | 73 52 38 | 85 60 45 | 105 77 60 | 130 97 75 | 142 105 80 | 158 117 90 |
При центрировании детали по наружному или внутреннему диаметру шлицев допускаемое напряжение может быть увеличено на . При центрировании по боковым граням шлицев
. Однако, при наличии дополнительных цилиндрических центрирующих поверхностей (см. рис.23)
.
Коэффициент долговечности при расчете шлицевых соединений определяется по формуле
.
При этом эквивалентное число циклов перемены напряжений определяется по формуле
.
При невыполнении условий прочности на смятие или износостойкость шлицев необходимо ввести изменения:
- уменьшение неравномерности распределения нагрузки;
- изменение материалов или термообработки;
- увеличение размеров соединения и переработка конструкции вала.
Расчет штифтового соединения
Штифтовое соединение, схема которого приведена на рис. 26, обеспечивает не только передачу крутящего момента, но и фиксацию детали на валу в осевом направлении.
Соединение не стандартизовано. Диаметр штифта рекомендуется принимать равным и выбирать из нормального ряда диаметров. В ряде случаев применяются конические штифты с малым углом конусности (обычно 1:50).
Рис.26
Длина штифта определяется конструктивно по диаметру ступицы детали с учетом условий сборки – разборки.
Проверка прочности соединения выполняется по напряжениям среза:
.
При этом допускаемое напряжение среза определяется по формуле
,
где - предел текучести на сдвиг материала штифта.
Запас прочности принимается не менее .
В связи с малой конусностью соединения с коническими штифтами рассчитываются так же, как с цилиндрическими. При этом под понимают среднее значение диаметра штифта.
При невыполнении условий прочности возможна установка двух штифтов во взаимно перпендикулярных плоскостях или замена вида соединения.
Расчет прессового соединения
Наибольшее распространение получили соединения по цилиндрическим поверхностям. Они относятся к неразъемным и обеспечивают минимальный вес соединения.
Передача крутящего момента и осевой силы в соединении обеспечивается силами трения. Необходимое давление посадки может быть определено по формуле
.
Здесь - коэффициент запаса по сцеплению;
- крутящий момент,
- осевая сила в соединении;
- диаметр вала в месте посадки;
- длина соединения;
- коэффициент трения.
Если для восприятия осевой силы на валу имеется упорный буртик, следует принять коэффициент =0. При отсутствии упорного буртика
=1.
Требуемая величина посадочного натяга определяется по формуле
.
Здесь и
- геометрические характеристики вала и установленной детали, определяемые по зависимостям:
,
.
Кроме того, и
- модули упругости и коэффициенты Пуассона материалов вала и установленной детали соответственно; d1 - диаметр отверстия вала;
- расчетное значение наружного диаметра ступицы установленной детали.
Минимальное значение посадочного натяга определяется с учетом способа сборки по формуле
,
где - характеристики шероховатости посадочных поверхностей вала и установленной детали.
При обычном (холодном) прессовании принимают =1,2, при сборке с нагревом детали или охлаждении вала -
=0.
Проверка прочности соединения выполняется по условиям:
и
.
Здесь и
- значения пределов текучести материалов вала и детали;
и
- приведенные нормальные напряжения на посадочных поверхностях вала и детали, определяемые по формулам:
,
.
При этом максимальное давление посадки определяется при максимальном значении посадочного натяга
по формуле
.
При невыполнении условий прочности необходимо увеличение размеров соединения или замена материалов.
Пример расчета вала
Рассчитать промежуточный вал (рис. 27) двухступенчатого зубчатого редуктора вертолета.
Рис. 27
Номинальный крутящий момент на промежуточном валу при установившемся режиме работы двигателя Т = 400 Н·м. Переменный крутящий момент от крутильных колебаний в системе составляет 25% (α = 0,25). Частота вращения вала . Требуемая долговечность подшипников 2000 часов.
Диаметр начальной окружности установленного на валу зубчатого колеса 1 =231мм. Шестерня 2 изготавливается заодно с валом и имеет параметры: модуль
=3мм, число зубьев
=30, диаметр начальной окружности
= 91мм.
Материал шестерни – вала - сталь 20Х2Н4А, предел прочности σв = 1250 МПа, пределы текучести σТ = 1070 МПа, τТ = 750 МПа, пределы выносливости σ-1 = 630 МПа, τ-1 = 320 МПа (см. табл. 1).
Оба косозубых колеса для уменьшения осевого усилия на опоры имеют одинаковое направление винтовой линии. Угол наклона зубьев по делительному цилиндру β = 8°30'07".
Определим номинальные значения усилий в зацеплениях зубьев.
Окружные усилия:
;
.
Радиальные усилия:
;
.
Осевые усилия:
;
.
Внешняя осевая нагрузка на опоры:
.
В связи с небольшой величиной осевой силы, действующей на подшипники, в опоре установлен зафиксированный по наружному и внутреннему диаметрам радиальный подшипник.
В этом случае опора должна быть "плавающей". В этой опоре устанавливаем радиальный роликоподшипник.
Проектировочный расчет
Ориентировочное значение диаметра вала определим из условия прочности по касательным напряжениям. По табл. 4 для промежуточного вала при несимметричном расположении опор и зубчатых колес условное значение запаса прочности примем равным . Тогда значение допускаемых напряжений кручения будет равно:
.
Коэффициент динамичности примем равным . Тогда расчетное значение крутящего момента будет равно:
.
Зададимся коэффициентом пустотелости . Тогда ориентировочное значение диаметра вала будет равно:
.
Разработка конструкции вала
При разработке конструкции вала пользуемся размерами, полученными при его предварительном расчете.
Выбираем подшипники:
- в опоре устанавливаем радиальный шариковый подшипник №209 повышенного класса точности с размерами 45×85×19;
- в опоре устанавливаем радиальный роликовый подшипник №32209 с размерами 45×85×19.
Диаметр вала d0 (см. рис. 27) принимаем равным внутреннему диаметру шарикоподшипника (d0 = 45 мм). Для того чтобы ступица зубчатого колеса во время сборки прошла этот участок свободно, без натяга, диаметр вала между шарикоподшипником и посадочным местом принимаем равным также 45 мм с постановкой при этом распорной втулки.
Шлицы для установки зубчатого колеса принимаются эвольвентными с модулем m = 2 мм. По технологическим требованиям наружный диаметр шлицев должен быть .
По табл. 27 принимаем шлицы с наружным диаметром и числом зубьев
.
Диаметр делительной окружности , диаметр окружности впадин
.
Длину ступицы колеса с учетом центрирующей втулки принимаем по соотношению . Длины центрирующей втулки и центрирующего участка вала равными примем соответственно 10мм и 12мм. Тогда расчетная длина шлицевого соединения будет равна
.
Диаметр посадочного места вала под ступицу зубчатого колеса с учетом технологических требований принимаем равным . Радиус закругления галтели берем по нормали свободных поверхностей круглых деталей
(см. табл. П3). Длина посадочного места выбирается в соответствии с длиной ступицы колеса с учетом способа нарезания шлицев.
При переходе посадочного места к большому диаметру имеется галтель. Радиус галтели выбираем по нормали для деталей при неподвижном соединении
(см. табл. П2). Диаметр буртика принимаем равным
.
Диаметр вала принимаем равным диаметру окружности впадин шестерни
.
Диаметр вала принимаем равным внутреннему диаметру роликоподшипника
.
Заплечик на валу выбираем по табл. П5 для роликоподшипника средней серии . Тогда
.
Радиус галтели в сечении 4 берем по нормали для свободных поверхностей круглых деталей (см. табл. П3).
Дата добавления: 2019-03-09; просмотров: 542; Мы поможем в написании вашей работы! |
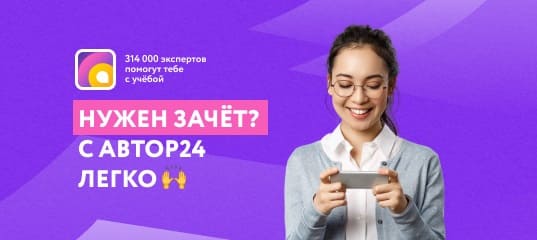
Мы поможем в написании ваших работ!